1929 Institution of Mechanical Engineers: Visits to Works
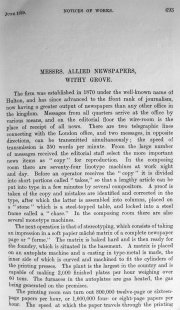
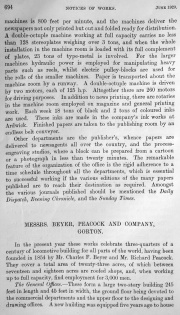
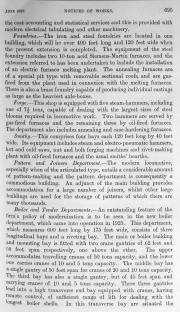
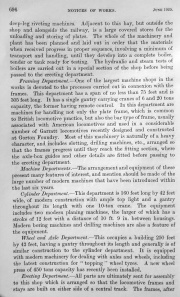
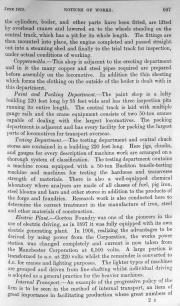
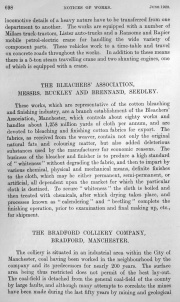
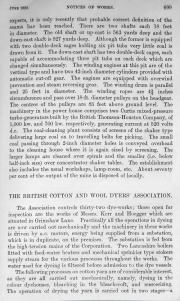
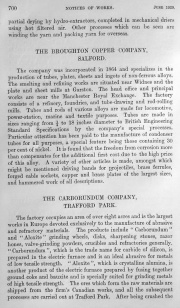
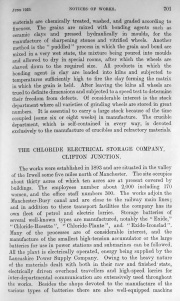
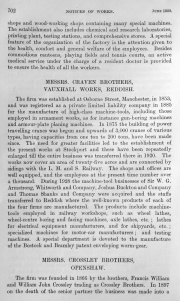
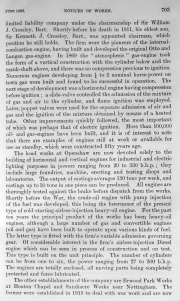
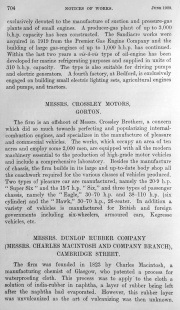
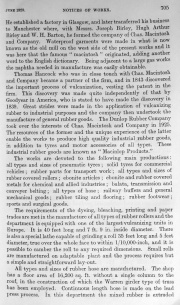
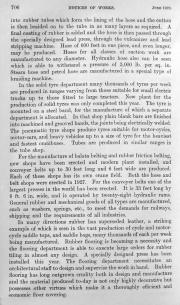
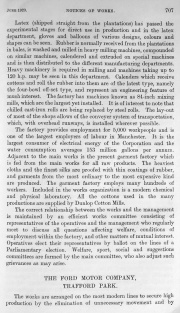
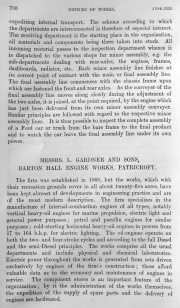
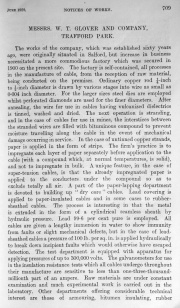
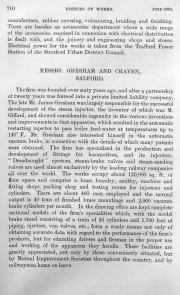
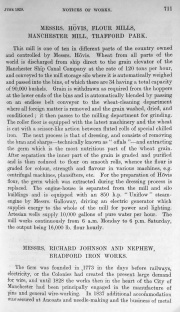
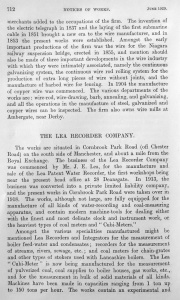
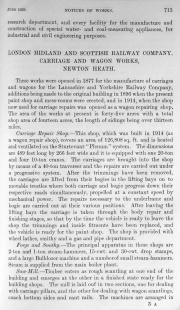
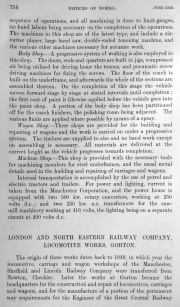
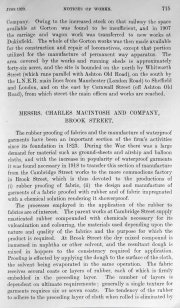
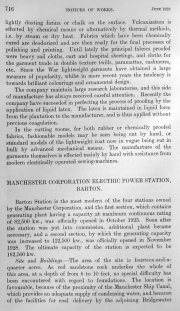
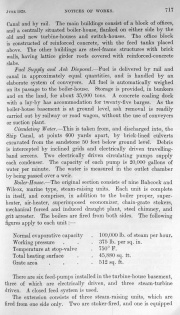
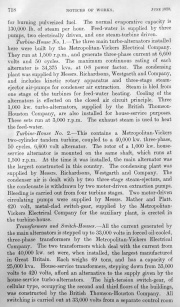
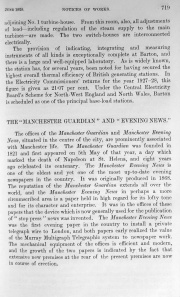
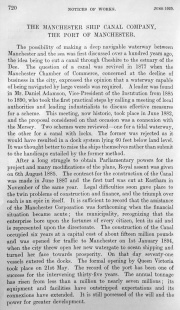
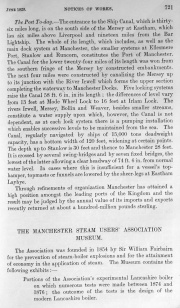
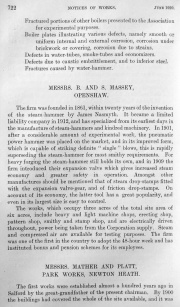
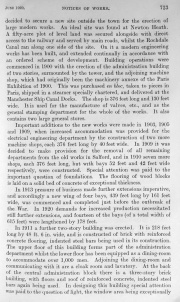
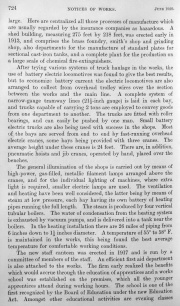
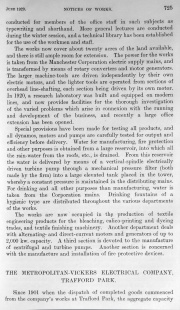

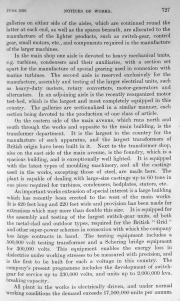
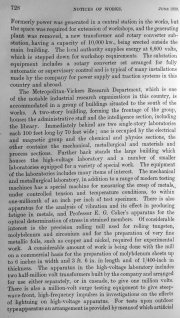
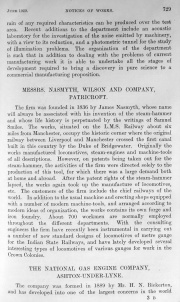
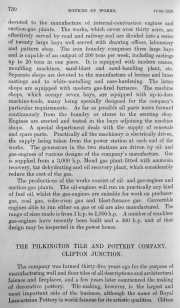
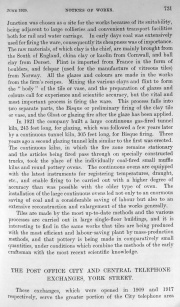
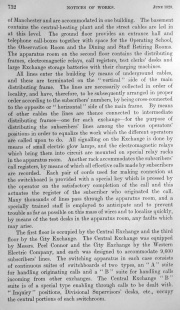
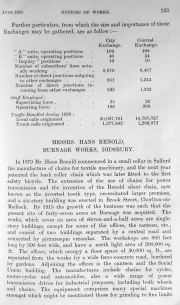
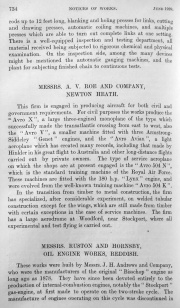
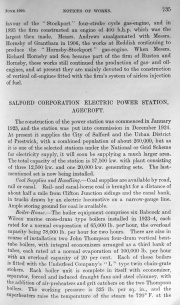
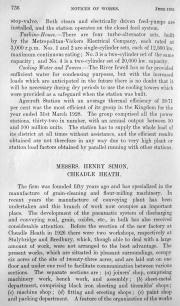
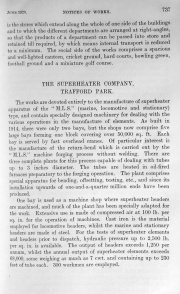
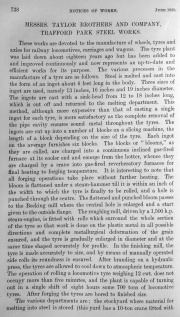
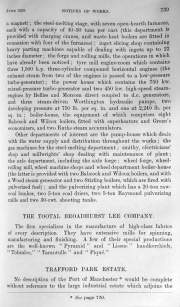
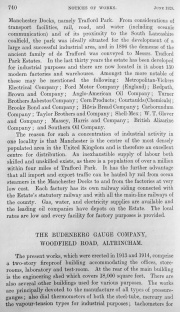
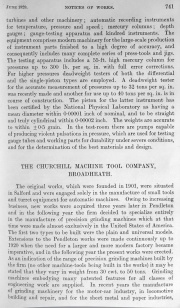
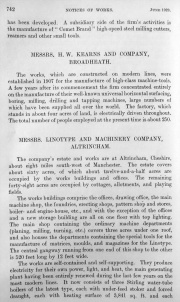
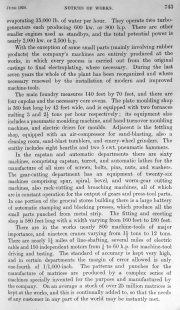
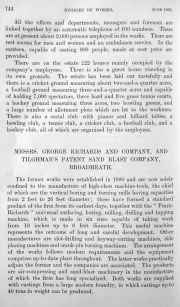
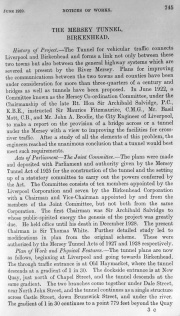

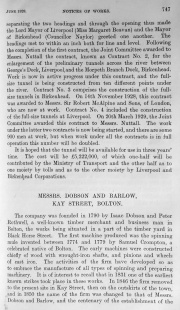
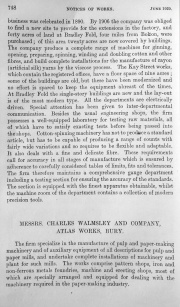
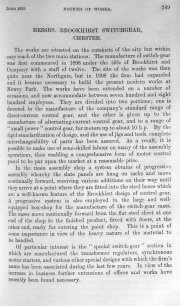

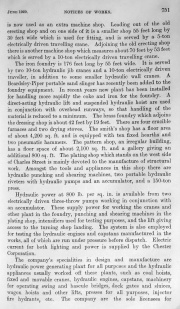
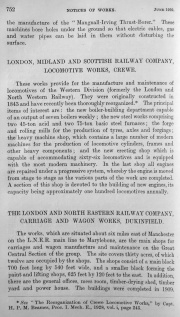
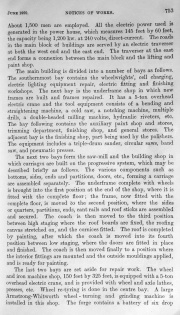
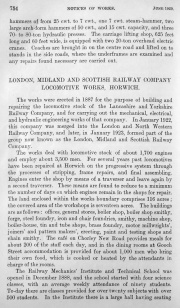
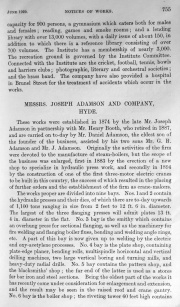
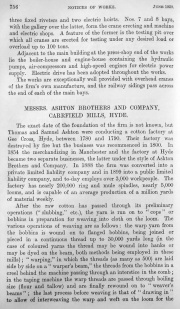
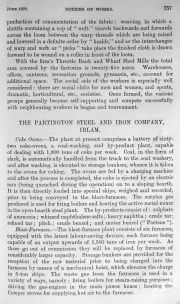
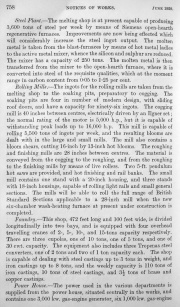
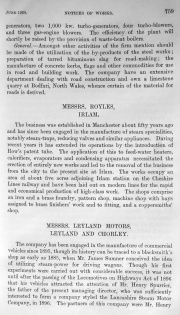
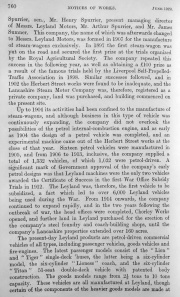
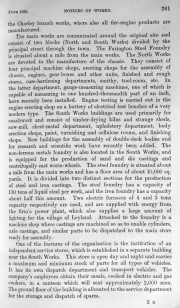

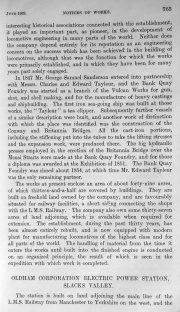
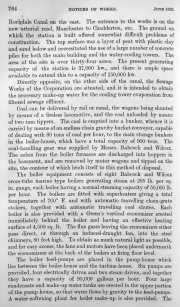
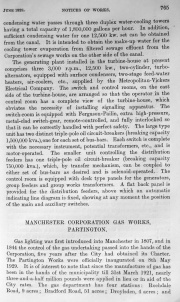
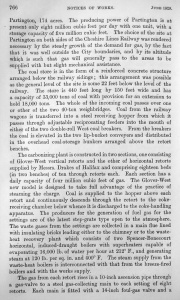
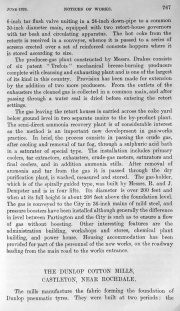
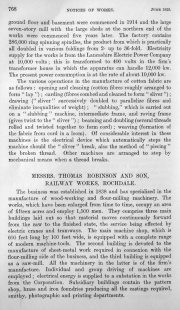
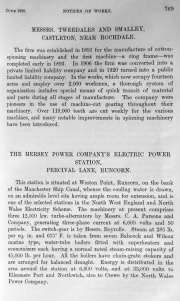
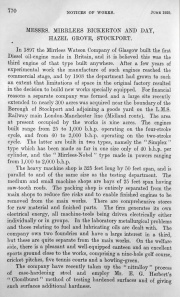
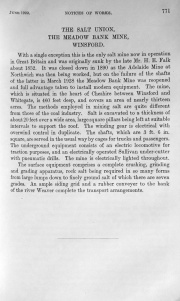
Note: This is a sub-section of 1929 Institution of Mechanical Engineers
Visits to Works (Excursions) in the Manchester area
Allied Newspapers
MESSRS. ALLIED NEWSPAPERS, WITHY GROVE.
The firm was established in 1870 under the well-known name of Hulton, and has since advanced to the front rank of journalism, now having a greater output of newspapers than any other office in the kingdom. Messages from all quarters arrive at the office by various means, and on the editorial floor the wire-room is the place of receipt of all news. There are two telegraphic lines connecting with the London office, and two messages, in opposite directions, can be transmitted simultaneously; the speed of transmission is 350 words per minute. From the large number of messages received the editorial staff select the more important news items as "copy" for reproduction. In the composing room there are seventy-four linotype machines at work night and day. Before an operator receives the "copy" it is divided into short portions called "takes," so that a lengthy article can he put into type in a few minutes by several compositors. A proof is taken of the copy and mistakes are identified and corrected in the type, after which the latter is assembled into columns, placed on a "stone" which is a steel-topped table, and locked into a steel frame called a "chase." In the composing room there are also several monotype machines.
The next operation is that of stereotyping, which consists of taking an impression in a soft papier mache matrix of a complete newspaper page or "forme." The matrix is baked hard and is then ready for the foundry, which is situated in the basement. A matrix is placed on an autoplate machine and a casting in type-metal is made, the inner side of which is curved and machined to fit the cylinders of the printing presses. The plant is the largest in the country and is capable of making 2,000 finished plates per hour weighing over 60 tons. The furnaces in the autoplates are gas heated, the gas being generated on the premises.
The printing room can turn out 800,000 twelve-page or sixteen-page papers per hour, or 1,600,000 four- or eight-page papers per hour. The speed at which the paper travels through the printing machines is 800 feet per minute, and the machines deliver the newspapers not only printed but cut and folded ready for distribution. A double-octuple machine working at full capacity carries no less than 128 stereoplates weighing over 3 tons, and when the whole installation in the machine room is loaded with its full complement of plates, 23 tons of type-metal is involved. For the larger machines hydraulic power is employed for manipulating heavy parts such as reels, whilst electric pulley-blocks are used for the rolls of the smaller machines. Paper is transported about the machine room by a runway. A double-octuple machine is driven by two motors, each of 125 h.p. Altogether there are 260 motors for driving purposes. In addition to news printing, there are rotaries in the machine room employed on magazine and general printing work. Each week 18 tons of black and 2 tons of coloured inks are used. These inks are made in the company's ink works at Ardwick. Finished papers are taken to the publishing room by an endless belt conveyer.
Other departments are the publisher's, whence papers are delivered to newsagents all over the country, and the process-engraving studios, where a block can be prepared from a cartoon or a photograph in less than twenty minutes. The remarkable feature of the organization of the office is the rigid adherence to a time schedule throughout all the departments, which is essential to successful working if the various editions of the many papers published are to reach their destination as required. Amongst the various journals published should be mentioned the Daily Dispatch, Evening Chronicle, and the Sunday Times.
Beyer, Peacock and Company, Gorton
MESSRS. BEYER, PEACOCK AND COMPANY, GORTON.
Beyer, Peacock and Company
In the present year these works celebrate three-quarters of a century of locomotive building for all parts of the world, having been founded in 1854 by Mr. Charles F. Beyer and Mr. Richard Peacock. They cover a total area of twenty-three acres, of which between seventeen and eighteen acres are roofed shops, and, when working up to full capacity, find employment for 3,000 men.
The General Offices. - These form a large two-story building 245 feet in length and 45 feet in width, the ground floor being devoted to the commercial departments and the upper floor to the designing and drawing offices. A new building was equipped five years ago to house the cost accounting and statistical services and this is provided with modern electrical tabulating and other machinery.
Foundries. — The iron and steel foundries are located in one building, which will be over 400 feet long and 120 feet wide when the present extension is completed. The equipment of the steel foundry includes two 10-ton acid Siemens-Martin furnaces, and the extension referred to has been undertaken to include the installation of an electric furnace melting plant. The annealing furnaces are of a special pit type with removable sectional roofs, and are gas-fired from the plant used in connexion with the melting furnaces. There is also a brass foundry capable of producing individual castings as large as the heaviest axle-boxes.
Forge. — This shop is equipped with five steam-hammers, including one of 7½ tons, capable of dealing with the largest sizes of steel blooms required in locomotive work. Two hammers are served by gas-fired furnaces and the remaining three by oil-fired furnaces. The department also includes annealing and case-hardening furnaces.
Smithy. — This comprises four bays each 120 feet long by 40 feet wide. Its equipment includes steam and electro-pneumatic hammers, hot and cold saws, nut and bolt forging machines and rivet-making plant with oil-fired furnaces and the usual smiths' hearths.
Pattern and Joiners Department. — The modern locomotive, especially when of the articulated type, entails a considerable amount of pattern-making and the pattern department is consequently a commodious building. An adjunct of the main building provides accommodation for a large number of joiners, whilst other large buildings are used for the storage of patterns of which there are many thousands.
Boiler and Tender Departments. — An outstanding feature of the firm's policy of modernization is to be seen in the new boiler department, which came into operation in 1925. This department, which measures 600 feet long by 175 feet wide, consists of three longitudinal bays and a riveting bay. The main or boiler building and mounting bay is fitted with two crane gantries of 62 feet and 59 feet span respectively, one above the other. The upper accommodates travelling cranes of 50 tons capacity, and the lower one carries cranes of 10 and 5 tons capacity. The middle bay has a single gantry of 50 feet span for cranes of 20 and 10 tons capacity. The third bay has also a single gantry, but of 45 feet span and carrying cranes of 10 and 5 tons capacity. These three gantries lead into a high transverse end bay equipped with cranes, having remote control, of sufficient range of lift for dealing with the longest boiler shells. In this transverse bay are situated the deep-leg riveting machines. Adjacent to this bay, but outside the shop and alongside the railway, is a large covered stores for the unloading and storing of plates. The whole of the machinery and plant has been planned and laid out in order that the materials when received progress in proper sequence, involving a minimum of transport and handling, until they develop into a complete boiler, tender or tank ready for testing. The hydraulic and steam tests of boilers are carried out in a special section of the shop before being passed to the erecting department.
Framing Department. — One of the largest machine shops in the works is devoted to the processes carried out in connexion with the frames. This department has a span of no less than 75 feet and is 305 feet long. It has a single gantry carrying cranes of 6 and 20 tons capacity, the former having remote control. In this department are machines for handling not only the plate frame, which is common to British locomotive practice, but also the bar type of frame, usually associated with American locomotives and used in a considerable number of Garratt locomotives recently designed and constructed at Gorton Foundry. Most of this machinery is naturally of a heavy character, and includes slotting, drilling machines, etc., arranged so that the frames progress until they reach the fitting section, where the axle-box guides and other details are fitted before passing to the erecting department.
Machine Departments. — The arrangement and equipment of these present many features of interest, and mention should be made of the large number of modern machines that have been introduced within the last six years.
Cylinder Department. — This department is 160 feet long by 42 feet wide, of modern construction with ample top light and a gantry throughout its length with one 10-ton crane. The equipment includes two modern planing machines, the larger of which has a stroke of 12 feet with a distance of 10 ft. 9 in. between housings. Modern boring machines and drilling machines are also a feature of the equipment.
Wheel and Axle Department. — This occupies a building 250 feet by 42 feet, having a gantry throughout its length and generally is of similar construction to the cylinder department. It is equipped with modern machinery for dealing with axles and wheels, including the latest construction for "topping" wheel tyres. A new wheel press of 450 tons capacity has recently been installed.
Erecting Department. — All parts are ultimately sent for assembly to this shop which is arranged so that the locomotive frames and stays are built on either side of a central track. The frames, after the cylinders, boiler, and other parts have been fitted, are lifted by overhead cranes and lowered on to the wheels standing on the central track, which has a pit for its whole length. The fittings are then mounted into place, the engine completed and passed straight out into a steaming shed and finally to the trial track for inspection, under actual conditions of working.
Coppersmiths. — This shop is adjacent to the erecting department and in it the many copper and steel pipes required are prepared before assembly on the locomotive. In addition the thin sheeting which forms the clothing on the outside of the boiler is dealt with in this departthent.
Paint and Packing Department. — The paint shop is a lofty building 220 feet long by 55 feet wide and has three inspection pits running its entire length. The central track is laid with multiple gauge rails and the crane equipment consists of two 50-ton cranes capable of dealing with the largest locomotives. The packing department is adjacent and has every facility for packing the largest parts of locomotives for transport overseas.
Testing Department. — The testing department and central chuck stores are contained in a building 220 feet long. Here jigs, chucks, and gauges for every description of machine work are arranged on a thorough system of classification. The testing department contains a machine room equipped with a 50-ton Buckton tensile-testing machine and machines for testing the hardness and transverse strength of materials. There is also a well-equipped chemical laboratory where analyses are made of all classes of fuel, pig iron, steel blooms and bars and other stores in addition to the products of the forge and foundries. Research work is also conducted here to determine the correct treatment in the manufacture of iron, steel and other materials of construction.
Electric Plant. — Gorton Foundry was one of the pioneers in the use of electric driving, as in 1897 it was fully equipped with its own electric generating plant. In 1906, realizing the advantages to be derived by using power from the Corporation, the works power station was changed completely and current is now taken from the Manchester Corporation at 6,500 volts. A large portion is transformed to a.c. at 220 volts whilst the remainder is converted to d.c. for cranes and lighting purposes. The lighter types of machines are grouped and driven from line-shafting whilst individual driving is adopted as a general practice for the heavier machines.
Internal Transport. — An example of the progressive policy of the firm is to be seen in the method of internal transport, an item of great importance in facilitating production where great numbers of locomotive details of a heavy nature have to be transferred from one department to another. The works are equipped with a number of Millars truck-tractors, Lister auto-trucks and a Ransome and Rapier mobile petrol-electric crane for handling the wide variety of component parts. These vehicles work to a time-table and travel on concrete roads throughout the works. In addition to these means there is a 5-ton steam travelling crane and two shunting engines, one of which is equipped with a crane.
Bleachers Association, Seedley
THE BLEACHERS' ASSOCIATION, MESSRS. BUCKLEY AND BRENNAND, SEEDLEY.
Buckley and Brennand, Bleachers Association
These works, which are representative of the cotton bleaching and finishing industry, are a branch establishment of the Bleachers' Association,. Manchester, which controls about eighty works and handles about 1,258 million yards of cloth per annum, and are devoted to bleaching and finishing cotton fabrics for export. The fabrics, as received from the weaver, contain not only the original natural fats and colouring matter, but also added deleterious substances used by the manufacturer for economic reasons. The business of the bleacher and finisher is to produce a high standard of "whiteness" without degrading the fabric, and then to impart by various chemical, physical and mechanical means, definite finishes to the cloth, which may be either permanent, semi-permanent, or artificial, all dependent upon the market for which the particular cloth is destined. To secure "whiteness" the cloth is boiled and then treated with chemicals, after which drying takes place, and processes known as "calendering" and "beetling" complete the finishing operation, prior to examination and final making up, etc., for shipment.
Bradford Colliery Company, Manchester
THE BRADFORD COLLIERY COMPANY, BRADFORD, MANCHESTER.
Bradford Colliery Co
The colliery is situated in an industrial area within the City of Manchester, coal having been worked in the neighbourhood by the company and its predecessors for nearly 200 years. The surface area being thus restricted does not permit of the best lay-out. The coal-field is detached from the general coal-field of the county by large faults, and although many attempts to correlate the mines have been made during the last fifty years by mining and geological experts, it is only recently that probable correct definition of the seams has been reached. There are two shafts each 18 feet in diameter. The old shaft or up-cast is 563 yards deep and the down-cast shaft is 927 yards deep. Although the former is equipped with two double-deck cages holding six pit tubs very little coal is drawn from it. The down-cast shaft has two double-deck cages, each capable of accommodating three pit tubs on each deck which are changed simultaneously. The winding engines at this pit are of the vertical type and have two 42-inch diameter cylinders provided with automatic cut-off gear. The engines are equipped with overwind prevention and steam reversing gear. The winding drum is parallel and 25 feet in diameter. The winding ropes are 4¾ inches circumference and pass over 18-ft. diameter pulleys on the headgear. The centres of the pulleys are 85 feet above ground level. The machinery in the power house comprises two Curtis mixed-pressure turbo-generators built by the British Thomson-Houston Company, of 1,000 kw. and 700 kw. respectively, generating current at 520 volts d.c. The coal-cleaning plant consists of screens of the shaker type delivering large coal on to travelling belts for picking. The small coal passing through 2-inch diameter holes is conveyed overhead to the cleaning house where it is again sized by screening. The larger lumps are cleaned over spirals and the smaller (i.e. below half-inch size) over concentrator shaker tables. The establishment also includes the usual workshops, lamp-room, etc. About seventy per cent of the output of the mine is disposed of locally.
British Cotton and Wool Dyers' Association
THE BRITISH COTTON AND WOOL DYERS' ASSOCIATION.
British Cotton and Wool Dyers Association
The Association controls thirty-two dye-works; those open for inspection are the works of Messrs. Kerr and Hoegger which are situated in Grimshaw Lane. Practically all the operations in dyeing are now carried out mechanically and the machinery in these works is driven by a.c. motors, energy being supplied from a substation, which is in duplicate, on the premises. The substation is fed from the high-tension mains of the Corporation. Two Lancashire boilers fitted with feed-water heaters and mechanical sprinkler type stokers supply steam for the various processes throughout the works. The water used for dyeing is filtered before admission to the dye vessels.
The following processes on cotton yarn are of considerable interest, as they are all carried out mechanically, namely, dyeing in the colour dyehouses, bleaching in the bleachcroft, and mercerizing. The operation of drying the yarn is carried out in two stages — a partial drying by hydro-extractors, completed in mechanical driers using hot filtered air. Other processes which can be seen are winding the yarn and packing yarn for overseas.
Broughton Copper Company, Salford
THE BROUGHTON COPPER COMPANY, SALFORD.
Broughton Copper Co
The company was incorporated in 1864 and specializes in the production of tubes, plates, sheets and ingots of non-ferrous alloys. The smelting and refining works are situated near Widnes and the plate and sheet mills at Garston. The head office and principal works are near the Manchester Royal Exchange. The factory consists of a refinery, foundries, and tube-drawing and rod-rolling mills. Tubes and rods of various alloys are made for locomotive, power-station, marine and textile purposes. Tubes are made in sizes ranging from ¼ to 18 inches diameter to British Engineering Standard Specifications by the company's special processes. Particular attention has been paid to the manufacture of condenser tubes for all purposes, a special feature being those containing 30 per cent of nickel. It is found that the freedom from corrosion more than compensates for the additional first cost due to the high price of this alloy. A variety of other articles is made, amongst which might be mentioned driving bands for projectiles, brass ferrules, forged cable sockets, copper and brass plates of the largest sizes, and hammered work of all descriptions.
Carborundum Company
THE CARBORUNDUM COMPANY, TRAFFORD PARK.
Carborundum Co
The factory occupies an area of over eight acres and is the largest works in Europe devoted exclusively to the manufacture of abrasive and refractory materials. The products include "Carborundum" and "Aloxite" grinding wheels, disks, sharpening stones, razor hones, valve-grinding powders, crucibles and refractories generally. "Carborundum", which is the trade name for carbide of silicon, is prepared in the electric furnace and is an ideal abrasive for metals of low tensile strength. "Aloxite", which is crystalline alumina, is another product of the electric furnace prepared by fusing together ground coke and bauxite and is specially suited for grinding metals of high tensile strength. The ores which form the raw materials are shipped from the firm's Canadian works, and all the subsequent processes are carried out at Trafford Park. After being crushed the materials are chemically treated, washed, and graded according to fineness. The grains are mixed with bonding agents such as ceramic clays and pressed hydraulically in moulds, for the manufacture of sharpening stones and vitrified wheels. Another method is the "puddled" process in which the grain and bond are mixed in a very wet state, the mixture being poured into moulds and allowed to dry in special rooms, after which the wheels are shaved down to the required size. All products in which the bonding agent is clay are loaded into kilns and subjected to temperatures sufficiently high to fire the clay forming the matrix in which the grain is held. After leaving the kilns all wheels are trued to definite dimensions and subjected to a speed test to determine their freedom from defects. Of considerable interest is the stock department where all varieties of grinding wheels are stored in great numbers. It is essential to carry a large stock because of the time occupied (some six or eight weeks) in manufacture. The crucible department, which is self-contained in every way, is devoted exclusively to the manufacture of crucibles and refractory materials.
Chloride Electrical Storage Co
THE CHLORIDE ELECTRICAL STORAGE COMPANY, CLIFTON JUNCTION.
Chloride Electrical Storage Co
The works were established in 1893 and are situated in the valley of the Irwell some five miles north of Manchester. The site occupies about thirty acres of which ten acres are at present covered by buildings. The employees number about 2,000 including 170 women, and the office staff numbers 300. The works adjoin the Manchester-Bury canal and are close to the railway main lines; and in addition to these transport facilities the company has its own fleet of petrol and electric lorries. Storage batteries of several well-known types are manufactured, notably the "Exide," "Chloride-Rosette", "Chloride-Plante", and "Exide-Ironclad". Many of the processes are of considerable interest, and the manufacture of the smallest high-tension accumulator or the large batteries for use in power stations and submarines can be followed. All the plant is electrically operated, energy being supplied by the Lancashire Power Supply Company. Owing to the heavy nature of the materials dealt with both in their raw and finished state, electrically driven overhead travellers and high-speed lorries for inter-departmental communication are extensively used throughout the works. Besides the shops devoted to the manufacture of the various types of batteries there are also well-equipped machine shops and wood-working shops containing many special machines. The establishment also includes chemical and research laboratories, printing plant, testing stations, and comprehensive stores. A special feature of the organization of the factory is the attention given to the health, comfort and general welfare of the employees. Besides commodious canteens, playing fields and tennis courts, an active medical service under the charge of a resident doctor is provided to ensure the health of all the workers.
Craven Brothers, Reddish
MESSRS. CRAVEN BROTHERS, VAUXHALL WORKS, REDDISH.
Craven Brothers
The firm was established at Osborne Street, Manchester, in 1853, and was registered as a private limited liability company in 1885 for the manufacture of high-class machine-tools, including those employed in armament works, as for instance gun-boring machines and armour-plate planing machines. In 1875 the building of power travelling cranes was begun and upwards of 3,000 cranes of various types, having capacities from one ton to 200 tons, have been made since. The need for greater facilities led to the establishment of the present works at Stockport and these have been repeatedly enlarged till the entire business was transferred there in 1920. The works now cover an area of twenty-five acres and are connected by sidings with the L. M. and S. Railway. The shops and offices are well equipped, and the employees at the present time number over a thousand. During 1928 the machine-tool businesses of Sir W. G. Armstrong, Whitworth and Co, Joshua Buckton and Co and Thomas Shanks and Co were acquired and the staffs transferred to Reddish where the well-known products of each of the four firms are manufactured. The products include machine-tools employed in railway workshops, such as wheel lathes, wheel-centre boring and facing machines, axle lathes, etc.; lathes for electrical equipment manufacturers, and for shipyards, etc.; specialized machines for motor-car manufacturers; and testing machines. A special department is devoted to the manufacture of the Bostock and Bramley patent enveloping worm-gear.
Crossley Brothers
MESSRS. CROSSLEY BROTHERS, OPENSHAW.
Crossley Brothers
The firm was founded in 1866 by the brothers, Francis William and William John Crossley trading as Crossley Brothers. In 1897 on the death of the senior partner the business was made into a limited liability company under the chairmanship of Sir William J. Crossley, Bart. Shortly before his death in 1911, his eldest son, Sir Kenneth J. Crossley, Bart., was appointed chairman, which position he still holds. The firm were the pioneers of the internal- combustion engine, having built and developed the original Otto and Langen gas-engine. In 1869 the "atmospheric" gas-engine took the form of a vertical construction with the cylinder below and the crank-shaft above, and there was no compression previous to ignition. Numerous engines developing from ¼ to 2 nominal horse-power on town gas were built and found to be successful in operation. The next stage of development was a horizontal engine having compression before ignition; a slide-valve controlled the admission of the mixture of gas and air to the cylinder, and flame ignition was employed. Later, poppet valves were used for the separate admission of air and gas and the ignition of the mixture obtained by means of a heated tube. Other improvements quickly followed, the most important of which was perhaps that of electric ignition. More than 100,000 oil- and gas-engines have been built, and it is of interest to note that there are examples of engines still at work or available for use as standby, which were constructed fifty years ago.
The head works at Openshaw are now devoted solely to the building of horizontal and vertical engines for industrial and electric lighting purposes in powers ranging from 20 to 330 b.h.p.; they include large foundries, machine, erecting and testing shops and laboratories. The output of castings averages 130 tons per week, and castings up to 30 tons in one piece can be produced. All engines are thoroughly tested against the brake before dispatch from the works. Shortly before the War, the crude-oil engine with pump injection of the fuel was developed, this being the forerunner of the present type of cold-starting airless-injection heavy-oil engine. For the past ten years the principal product of the works has been heavy-oil engines, although a large number of gas and convertible engines (oil and gas) have been built to operate upon various kinds of fuel. The latter type is fitted with the firm's variable admission governing gear. Of considerable interest is the firm's airless-injection Diesel engine which can be seen in process of construction and on test. This type is built on the unit principle. The number of cylinders can be from one to six, the power ranging from 27 to 300 b.h.p. The engines are totally enclosed, all moving parts being completely protected and force lubricated.
The other establishments of the company are Erwood Park Works at Heaton Chapel and Sandiacre Works near Nottingham. The former were established in 1915 to deal with war work and are now exclusively devoted to the manufacture of suction and pressure-gas plants and of small engines. A producer-gas plant of up to 3,000 b.h.p. capacity has been constructed. The Sandiacre works were acquired in 1919 from the Premier Gas Engine Company and the building of large gas-engines of up to 1,000 b.h.p. has continued. Within the last two years a vis-a-vis type of oil-engine has been developed for marine refrigerating purposes and supplied in units of 310 b.h.p. capacity. The type is also suitable for driving pumps and electric generators. A fourth factory, at Bedford, is exclusively engaged on building small electric lighting sets, agricultural engines and pumps, and tractors.
Crossley Motors, Gorton
MESSRS. CROSSLEY MOTORS, GORTON.
Crossley Motors
The firm is an offshoot of Messrs. Crossley Brothers, a concern which did so much towards perfecting and popularizing internal-combustion engines, and specializes in the manufacture of pleasure and commercial vehicles. The works, which occupy an area of ten acres and employ some 2,000 men, are equipped with all the modern machinery essential to the production of high-grade motor vehicles and include a comprehensive laboratory. Besides the manufacture of chassis, the firm builds in its large and up-to-date body shop all the coachwork required for the various classes of vehicles produced. Two types of pleasure car are manufactured, namely the 20.9 h.p. "Super Six" and the 15.7 h.p. "Six," and three types of passenger chassis, namely the "Eagle," 30-70 h.p. and 38-110 h.p. (six cylinder) and the "Hawk," 30-70 h.p., 26-seater. In addition a variety of vehicles is manufactured for British and foreign governments including six-wheelers, armoured cars, Kegresse vehicles, etc.
Dunlop Rubber Company
MESSRS. DUNLOP RUBBER COMPANY (MESSRS. CHARLES MACINTOSH AND COMPANY BRANCH), CAMBRIDGE STREET.
Dunlop Rubber Co, Charles Macintosh and Co
The firm was founded in 1823 by Charles Macintosh, a manufacturing chemist of Glasgow, who patented a process for waterproofing cloth. This process was to apply to the cloth a solution of india-rubber in naphtha, a layer of rubber being left after the naphtha had evaporated. However, this rubber layer was unvulcanized as the art of vulcanizing was then unknown.
He established a factory in Glasgow, and later transferred his business to Manchester where, with Messrs. Joseph Birley, Hugh Arthur Birley and W. H. Barton, he formed the company of Chas. Macintosh and Company. Waterproof garments were made in what is now known as the old mill on the west side of the present works and it was here that the famous "macintosh" originated, adding another word to the English dictionary. Being adjacent to a large gas works the naphtha needed in manufacture was easily obtainable.
Thomas Hancock who was in close touch with Chas. Macintosh and Company became a partner of the firm, and in 1843 discovered the important process of vulcanization, vesting the patent in the firm. This discovery was made quite independently of that by Goodyear in America, who is stated to have made the discovery in 1839. Great strides were made in the application of vulcanizing rubber to industrial purposes and the company then undertook the manufacture of general rubber goods. The Dunlop Rubber Company took over the interests of Chas. Macintosh and Company in 1925. The resources of the former and the unique experience of the latter enable the works to produce high quality industrial rubber goods, in addition to tyres and motor accessories of all types. These industrial rubber goods are known as "Macinlop Products."
The works are devoted to the following main productions: all types and sizes of pneumatic tyres; solid tyres for commercial vehicles; rubber parts for transport work; all types and sizes of rubber covered rollers; ebonite articles; ebonite and rubber covered metals for chemical and allied industries; balata, transmission and conveyer belting; all types of hose; railway buffers and general mechanical goods; rubber tiling and flooring; rubber footwear; sports and surgical goods.
The requirements of the dyeing, bleaching, printing and paper trades are met in the manufacture of all types of rubber rollers and the department is equipped with one of the largest vulcanizing units in Europe. It is 40 feet long and 7 ft. 9 in. inside diameter. There is also a special lathe capable of grinding a roll 35 feet long and 5 feet diameter, true over the whole face to within 1/10,000-inch, and it is possible to camber the roll to any required dimensions. Small rolls are manufactured on adaptable plant and the process requires but a simple and straightforward lay-out.
All types and sizes of rubber hose are manufactured. The shop has a floor area of 16,200 sq. ft. without a single column to the roof, in the construction of which the Warren girder type of truss has been employed. Continuous length hose is made on the lead press process. In this department the mixed rubber is extruded into rubber tubes which form the lining of the loose and the cotton is then braided on to the tube in as many layers as required. A final coating of rubber is added and the hose is then passed through the specially designed lead press, through the vulcanizer and lead stripping machine. Hose of 600 feet in one piece, and even longer, may be produced. Hoses for all classes of suction, work are manufactured to any diameter. Hydraulic hose also can be seen which is able to withstand a pressure of 3,000 lb. per sq. in. Steam hose and petrol hose are manufactured in a special type of braiding machine.
In the solid tyre department many thousands of tyres per week are produced in ranges varying from those suitable for small electric trucks up to those fitted to large tractors. New plant for the production of solid tyres was only completed this year. The tyre is mounted on a steel band, for the manufacture of which a separate department is allocated. In that shop plain blank bars are finished into machined and grooved bands, the joints being electrically welded. The pneumatic tyre shops produce tyres suitable for motor-cycles, motor-cars, and heavy vehicles up to a size of tyre for the heaviest and fastest omnibuses. Tubes are produced in similar ranges in the tube shop.
For the manufacture of balata belting and rubber friction belting, new shops have been erected and modern plant installed, and conveyer belts up to 30 feet long and 6 feet wide are produced. Each of these shops has its own crane field. Both the hose and belt shops were erected in 1927. For the conveyer belts one of the largest presses in the world has been erected. It is 33 feet long by 6 ft. 6 in. wide, and is operated by twenty-eight hydraulic rams. General rubber and mechanical goods of all types are manufactured, such as washers, springs, etc., to meet the demands for railways, shipping and the requirements of all industries.
In many directions rubber has superseded leather, a striking example of which is seen in the vast production of cycle and motorcycle saddle tops, and saddle bags, many thousands of each per week being manufactured. Rubber flooring is becoming a necessity and the flooring department is able to execute large orders for rubber tiling in almost any design. A specially designed press has been installed this year. The flooring department necessitates an architectural staff to design and supervise the work in hand. Rubber flooring has long outgrown crudity both in design and manufacture and the material produced to-day is not only highly decorative but possesses other virtues which make it a thoroughly efficient and economic floor covering.
Latex (shipped straight from the plantations) has passed the experimental stages for direct use in production and in the latex department, gloves and balloons of various designs, colours and shapes can be seen. Rubber is normally received from the plantations in bales, is washed and milled in heavy milling machines, compounded on similar machines, calendered and extruded on special machines and is then distributed to the different manufacturing departments. Heavy machinery is required in milling and machines taking up to 120 h.p. may be seen in this department. Calenders which receive cottons and roll the rubber into them are of the latest type, namely the four-bowl off-set type, and represent an engineering feature of much interest. The factory has machines known as 84-inch mixing mills, which are the largest yet installed. It is of interest to note that chilled cast-iron rolls are being replaced by steel rolls. The lay-out of most of the shops allows of the conveyer system of transportation, which, with overhead runways, is installed wherever possible.
The factory provides employment for 5,000 workpeople and is one of the largest employers of labour in Manchester. It is the largest consumer of electrical energy of the Corporation and the water consumption averages 153 million gallons per annum. Adjacent to the main works is the present garment factory which is fed from the main works for all raw products. The heaviest cloths and the finest silks are proofed with thin coatings of rubber, and garments from the most ordinary to the most expensive kind are produced. The garment factory employs many hundreds of workers. Included in the works organization is a modern chemical and physical laboratory. All the cottons used in the many productions are supplied by Dunlop Cotton Mills.
The correct relationship between the works and the management is maintained by an efficient works committee consisting of representatives of the operatives and the management who regularly meet to discuss all questions affecting welfare, conditions of employment within the factory, and other matters of mutual interest. Operatives elect their representatives by ballot on the lines of a Parliamentary election. Welfare, sport, social and suggestions committees are formed by the main committee, who also adjust such grievances as may arise.
Ford Motor Company, Trafford Park
THE FORD MOTOR COMPANY, TRAFFORD PARK.
Ford
The works are arranged on the most modern lines to secure high production by the elimination of unnecessary movement and by expediting internal transport. The scheme according to which the departments are interconnected is therefore of especial interest. The receiving department is the starting place in the organization, all materials and components being there taken into stock. All incoming material passes to the inspection department whence it is dispatched to the various shops for minor assembly, e.g. the sub-departments dealing with rear-axles, the engines, frames, dashboards, radiator, etc. Each minor assembly line finishes at its correct point of contact with the main or final assembly line. The final assembly line commences with the chassis frame upon which are fastened the front and rear axles. As the conveyer of the final assembly line moves along slowly during the adjustment of the two axles, it is joined, at the point required, by the engine which has just been delivered from its own minor assembly conveyer. Similar principles are followed with regard to the respective minor assembly lines. It is thus possible to inspect the complete assembly of a Ford car or truck from the bare frame to the final product and to watch the car leave the final assembly line under its own power.
L. Gardner and Sons, Patricroft
MESSRS. L. GARDNER AND SONS, BARTON HALL ENGINE WORKS, PATRICROFT.
L. Gardner and Sons
The firm was established in 1868, but the works, which with their recreation grounds cover in all about twenty-five acres, have been kept abreast of developments in engineering practice and are of the most modern description. The firm specializes in the manufacture of internal-combustion engines of all types, notably vertical heavy-oil engines for marine propulsion, electric light and general power purposes; petrol and paraffin engines for similar purposes; cold-starting horizontal heavy-oil engines in powers from 17 to 164 b.h.p. for electric lighting. The oil-engines operate on both the two- and four-stroke cycles and according to the full Diesel and the semi-Diesel principles. The works comprise all the usual departments and include physical and chemical laboratories. Electric power throughout the works is generated from sets driven exclusively by engines of the firm's construction; these afford valuable data as to the economy and maintenance of engines in service. The component stores is an important feature of the organization; by it the administration of the works themselves, the expedition of the supply of spare parts and the delivery of engines are facilitated.
W. T. Glover and Company
MESSRS. W. T. GLOVER AND COMPANY, TRAFFORD PARK.
W. T. Glover and Co
The works of the company, which was established sixty years ago, were originally situated in Salford, but increase in business necessitated a more commodious factory which was secured in 1900 on the present site. The factory is self-contained, all processes in the manufacture of cable, from the reception of raw material, being conducted on the premises. Ordinary copper rod ¼-inch to ½-inch diameter is drawn by various stages into wire as small as 0.004 inch diameter. For the larger sizes steel dies are employed whilst perforated diamonds are used for the finer diameters. After annealing, the wire for use in cables having vulcanized dielectrics is tinned, washed and dried. The next operation is stranding, and in the case of cables for use in mines, the interstices between the stranded wires are filled with bituminous compound to prevent moisture travelling along the cable in the event of mechanical damage occurring in service. In the case of untinned copper strands, paper is applied in the form of strips. The firm's practice is to impregnate each layer of paper separately before application to the cable (with a compound which, at normal temperatures, is solid), and not to impregnate in bulk. A unique feature, in the case of super-tension cables, is that the already impregnated paper is applied to the conductors under the compound so as to exclude totally all air. A part of the paper-lapping department is devoted to building up "dry core" cables. Lead covering is applied to paper-insulated cables and in some cases to rubber-sheathed cables. The process is interesting in that the metal is extruded in the form of a cylindrical seamless sheath by hydraulic pressure. Lead 99.6 per cent pure is employed. All cables are given a lengthy immersion in water to show immunity from faults or slight mechanical defects, but in the case of lead-sheathed cables a pressure of 100 lb. per sq. in. is applied hydraulically to break down incipient faults which would otherwise have escaped detection. The test department is equipped with apparatus for applying pressures of up to 300,000 volts. The galvanometers for use in the insulation resistance tests which all cables undergo throughout their manufacture are sensitive to less than one-three-thousand millionth part of an ampere. Raw materials are under constant examination and much experimental work is carried out in the laboratory. Other departments offering considerable technical interest are those of armouring, bitumen insulating, rubber manufacture, rubber covering, vulcanizing, braiding and finishing. There are besides an accessories department where a wide range of the accessories required in connexion with electrical distribution is dealt with, and the joinery and engineering shops and stores. Electrical power for the works is taken from the Trafford Power Station of the Stretford Urban District Council.
Gresham and Craven, Salford
MESSRS. GRESHAM AND CRAVEN, SALFORD.
Gresham and Craven
The firm was founded over sixty years ago, and after a partnership of twenty years was formed into a private limited liability company. The late Mr. James Gresham was largely responsible for the successful development of the steam injector, the inventor of which was M. Giffard, and showed considerable ingenuity in the various inventions and improvements in that apparatus, which resulted in the automatic restarting injector to pass boiler feed-water at temperatures up to 140° F. Mr. Gresham also interested himself in the automatic vacuum brake, in connexion with the details of which many patents were obtained. The firm has specialized in the production and development of fittings for locomotives, and its injectors, "Dreadnought" ejectors, steam-brake valves and steam-sanding valves are used almost exclusively by the leading railway companies all over the world. The works occupy about 120,000 sq. ft. of floor space and comprise a brass foundry, smithy, machine and fitting shops, packing shop and testing rooms for injectors and cylinders. There are about 460 men employed and the normal output is 40 tons of finished brass mountings and 2,000 vacuum brake cylinders per month. In the drawing office are kept complete sectional models of the firm's specialities which, with the model brake stand consisting of a train of 50 cylinders and 1,700 feet of piping, ejectors, van valves, etc., form a ready means not only of obtaining accurate data with regard to the performance of the firm's products, but for educating drivers and firemen in the proper use and working of the apparatus they handle. These facilities are greatly appreciated, not only by those conveniently situated, but by Mutual Improvement Societies throughout the country, and by railwaymen home on leave.
Hovis, Trafford Park Flour Mills
MESSRS. HOVIS, FLOUR MILLS, MANCHESTER MILL, TRAFFORD PARK.
Hovis
This mill is one of ten in different parts of the country owned and controlled by Messrs. Hovis. Wheat from all parts of the world is discharged from ship direct to the grain elevator of the Manchester Ship Canal Company at the rate of 120 tons per hour, and conveyed to the mill storage silo where it is automatically weighed and passed into the bins, of which there are 34 having a total capacity of 90,000 bushels. Grain is withdrawn as required from the hoppers at the lower ends of the bins and is automatically blended by passing on an endless belt conveyer to the wheat-cleaning department where all foreign matter is removed and the grain washed, dried, and conditioned; it then passes to the milling department for grinding. The roller floor is equipped with the latest machinery and the wheat is cut with a scissor-like action between fluted rolls of special chilled iron. The next process is that of dressing, and consists of removing the bran and sharps—technically known as "offals" — and extracting the germ which is the most nutritious part of the wheat grain. After separation the inner part of the grain is graded and purified and is then reduced to flour on smooth rolls, whence the flour is graded for colour, strength and flavour in various machines, e.g. centrifugal machines, plansifters, etc. For the preparation of Hovis flour, the germ which was extracted during the dressing process is replaced. The engine-house is separated from the mill and silo buildings and is equipped with an 850 h.p. "Uniflow" steam-engine by Messrs. Galloway, driving an electric generator which supplies energy to the whole of the mill for power and lighting. Artesian wells supply 10,000 gallons of pure water per hour. The mill works continuously from 6 a.m. Monday to 6 p.m. Saturday, the output being 16,000 lb. flour hourly.
Richard Johnson and Nephew
MESSRS. RICHARD JOHNSON AND NEPHEW, BRADFORD IRON WORKS.
Richard Johnson and Nephew
The firm was founded in 1773 in the days before railways, electricity, or the Colonies had created the present large demand for wire, and until 1828 the works then in the heart of the City of Manchester had been principally engaged in the manufacture of pins and general wire-working. In 1837 additional accommodation was sectored at Ancoats and needle-making and the business of metal merchants added to the occupations of the firm. The invention of the electric telegraph in 1837 and the laying of the first submarine cable in 1851 brought a new era to the wire manufacturer, and in 1853 the present works were established. Amongst the early important productions of the firm was the wire for the Niagara railway suspension bridge, erected in 1855, and mention should also be made of three important developments in the wire industry with which they were intimately associated, namely the continuous galvanizing system, the continuous wire rod rolling system for the production of extra long pieces of wire without joints, and the manufacture of barbed wire for fencing. In 1904 the manufacture of copper wire was commenced. The various departments of the works are: wire-rod, wire-drawing, barb, annealing, and galvanizing, and all the operations in the manufacture of steel, galvanized and copper wires can be inspected. The firm also owns wire mills at Ambergate, near Derby.
Lea Recorder Company
THE LEA RECORDER COMPANY.
Lea Recorder Co
The works are situated in Cornbrook Park Road (off Chester Road) on the south side of Manchester, and about a mile from the Royal Exchange. The business of the Lea Recorder Company was commenced by Mr. J. E. Lea, for the manufacture and sale of the Lea Patent Water Recorder, the first workshops being near the present head office at 28 Deansgate. In 1913, the business was converted into a private limited liability company, and the present works in Cornbrook Park Road were taken over in 1918. The works, although not large, are fully equipped for the manufacture of all kinds of water-recording and coal-measuring apparatus, and contain modern machine-tools for dealing either with the finest and most delicate clock and instrument work, or the heaviest types of coal meters and "Cubi-Meters."
Amongst the various specialities manufactured might be mentioned Lea Recorders and Integrators for the measurement of boiler feed-water and condensates; recorders for the measurement of streams, rivers, sewage, etc.; and coal meters for chain-grates and other types of stokers used with Lancashire boilers. The Lea "Cubi-Meter" is now being manufactured for the measurement of pulverized coal, coal supplies to boiler houses, gas works, etc., and for the measurement in bulk of solid materials of all kinds. Machines have been made in capacities ranging from 1 ton up to 150 tons per hour. The works contain an experimental and research department, and every facility for the manufacture and construction of special water- and coal-measuring appliances, for industrial and civil engineering purposes.
LMSR Carriage and Wagon Works, Newton Heath
LONDON MIDLAND AND SCOTTISH RAILWAY COMPANY. CARRIAGE AND WAGON WORKS, NEWTON HEATH.
Newton Heath Works
These works were opened in 1877 for the manufacture of carriages and wagons for the Lancashire and Yorkshire Railway Company, additions being made to the original building in 1896 when the present paint shop and mess-rooms were erected, and in 1914, when the shop now used for carriage repairs was opened as a wagon repairing shop. The area of the works at present is forty-five acres with a total shop area of fourteen acres, the length of sidings being over thirteen miles.
Carriage Repair Shop. — This shop, which was built in 1914 (as a wagon repair shop), covers an area of 126,808 sq. ft. and is heated and ventilated on the Sturtevant "Plenum" system. The dimensions are 489 feet long by 266 feet wide and it is equipped with one 20-ton and four 10-ton cranes. The carriages are brought into the shop by means of a 40-ton traverser and the repairs are carried out under a progressive system. After the trimmings have been removed, the carriages are lifted from their bogies in the lifting bays on to movable trestles where both carriage and bogie progress down their respective roads simultaneously, propelled at a constant speed by mechanical power. The repairs necessary to the underframe and bogie are carried out at their various positions. After leaving the lifting bays the carriage is taken through the body repair and finishing stages, so that by the time the vehicle is ready to leave the shop the trimmings and inside fitments have been replaced, and the vehicle is ready for the paint shop. The shop is provided with wheel lathes, smithy and a gas and pipe department.
Forge and Smithy. — The principal apparatus in these shops are 2-ton and 1-ton steam-hammers, 15-cwt. and 30-cwt. drop stamps, and a large Bulldozer machine and a number of small steam-hammers. Steam is supplied from the main boiler plant.
Saw-Mill. — Timber enters as rough scantling at one end of the building and emerges at the other in a finished state ready for the building shops. The mill is laid out in two sections, one for dealing with carriage pillars, and the other for dealing with wagon scantlings, coach bottom sides and cant rails. The machines are arranged in Sequence of operations, and all machining is done to limit-gauges, no hand labour being necessary on the completion of the operations. The machines in this shop are of the latest type, and include a six-cutter planer, large band saw, double-ended tenoning machine, and the various other machines necessary for accurate work.
Body Shop. — A progressive system of working is also employed in this shop. The doors, ends and quarters are built in jigs, compressed air being utilized for driving home the tenons, and pneumatic screw driving machines for fixing the screws. The floor of the coach is built on the underframe, and afterwards the whole of the sections are assembled thereon. On the completion of this stage the vehicle moves forward stage by stage at stated intervals until completion; the first coat of paint is likewise applied before the vehicle goes into the paint shop. A portion of the body shop has been partitioned off for the coach finishers, the polishing room being adjacent. The various fluids are applied where possible by means of a spray.
Wagon Shop. — Three shops are provided for the building and repairing of wagons and the work is carried on under a progressive system. The timbers are supplied to size and no hand work except on assembling is necessary. All materials are delivered at the correct height as the vehicle progresses towards completion.
Machine Shop. — This shop is provided with the necessary tools for machining members for steel underframes, and the usual metal details used in the building and repairing of carriages and wagons.
Internal transportation is accomplished by the use of petrol and electric tractors and trailers. For power and lighting, current is taken from the Manchester Corporation, and the power house is equipped with two 500 kw. rotary converters, working at 250 volts d.c.; and two 250 kw. a.c. transformers for the sawmill machinery working at 416 volts, the lighting being on a separate circuit at 200 volts d.c.
LNER Locomotive Works, Gorton
LONDON AND NORTH EASTERN RAILWAY COMPANY, LOCOMOTIVE WORKS, GORTON.
Gorton Works
The origin of these works dates back to 1849, in which year the locomotive, carriage and wagon workshops of the Manchester, Sheffield and Lincoln Railway Company were transferred from Newton, Cheshire. Later the works at Gorton became the headquarters for the construction and repair of locomotives, carriages and wagons, and for the manufacture of a portion of the permanent way requirements for the Engineer of the Great Central Railway Company. Owing to the increased stock on that railway the space available at Gorton was found to be insufficient, and in 1907 the carriage and wagon work was transferred to new works at Dukinfield. The whole of the Gorton works was then made available for the construction and repair of locomotives, except that portion utilized for the manufacture of permanent way apparatus. The area covered by the works and running sheds is approximately forty-six acres, and the site is bounded on the north by Whitworth Street (which runs parallel with Ashton Old Road), on the south by the L.N.E.R. main lines from Manchester (London Road) to Sheffield and London, and on the east by Cornwall Street (off Ashton Old Road), from which street the main offices and works are reached.
Charles Macintosh and Company
MESSRS. CHARLES MACINTOSH AND COMPANY, BROOK STREET.
Charles Macintosh and Co
The rubber proofing of fabrics and the manufacture of waterproof garments have been an important section of the firm's activities since its foundation in 1823. During the War there was a large demand for material such as ground-sheets and airship and balloon cloths, and with the increase in popularity of waterproof garments it was found necessary in 1918 to transfer this section of manufacture from the Cambridge Street works to the more commodious factory in Brook Street, which is thus devoted to the productions of (i) rubber proofing of fabric, (ii) the design and manufacture of garments of a fabric proofed with rubber and of fabric impregnated with a chemical solution rendering it shower-proof.
The processes employed in the application of the rubber to fabrics are of interest. The parent works at Cambridge Street supply masticated rubber compounded with chemicals necessary for its vulcanization and colouring, the materials used depending upon the nature and quality of the fabrics and the purpose for which the product is required. At Brook Street the dry mixed compound is immersed in naphtha or other solvent, and the resultant dough is mixed in hoppers to the consistency required for application. Proofing is effected by applying the dough to the surface of the cloth, the solvent being evaporated in the same operation. The fabric receives several coats or layers of rubber, each of which is firmly embedded in the preceding layer. The number of layers is dependent on ultimate requirements; generally a single texture for garments requires six or seven coats. The tendency of the rubber to adhere to the preceding layer of cloth when rolled is eliminated by lightly dusting farina or chalk on the surface. Vulcanization is effected by chemical means or alternatively by thermal methods, i.e. by steam or dry heat. Fabrics which have been chemically cured are deodorized and are then ready for the final processes of polishing and printing. Until lately the principal fabrics proofed were heavy sail cloths, cart and hospital sheetings, and cloths for the garment trade in double texture twills, paramattas, cashmeres, etc. Since the War lightweight garments have obtained a large measure of popularity, whilst in more recent years the tendency is towards brilliant colourings and ornamental design.
The company maintain large research laboratories, and this side of manufacture has always received careful attention. Recently the company have succeeded in perfecting the process of proofing by the application of liquid latex. The latex is maintained in liquid form from the plantation to the manufacturer, and is thus applied without previous coagulation.
In the cutting rooms, for both rubber or chemically proofed fabrics, fashionable models may be seen being cut by hand, or standard models of the lightweight coat now in vogue being cut in bulk by advanced mechanical means. The manufacture of the garments themselves is effected mainly by hand with assistance from modern electrically operated sewing-machines.
Barton Power Station, Manchester
MANCHESTER CORPORATION ELECTRIC POWER STATION, BARTON.
Barton Power Station, Manchester
Barton Station is the most modern of the four stations owned by the Manchester Corporation, and the first section, which contains generating plant having a capacity at maximum continuous rating of 82,500 kw., was officially opened in October 1923. Soon after the station was put into commission, additional plant became necessary, and a second section, by which the generating capacity was increased to 122,500 kw., was officially opened in November 1928. The ultimate capacity of the station is expected to be 162,500 kw.
Site and Buildings. — The area of the site is fourteen-and-a quarter acres. As red sandstone rock underlies the whole of this area, at a depth of from 6 to 10 feet, no special difficulty has been encountered with regard to foundations. The location is favourable, because of the proximity of the Manchester Ship Canal, which provides an adequate supply of condensing water, and because of the facilities for coal delivery by the adjoining Bridgewater Canal and by rail. The main buildings consist of a block of offices, and a centrally situated boiler-house, flanked on either side by the old and new turbine-houses and switch-houses. The office block is constructed of reinforced concrete, with the feed tanks placed above. The other buildings are steel-frame structures with brick walls, having lattice girder roofs covered with reinforced-concrete slabs.
Fuel Supply and Ash Disposal. — Fuel is delivered by rail and canal in approximately equal quantities, and is handled by an elaborate system of conveyers. All fuel is automatically weighed on its passage to the boiler-house. Storage is provided, in bunkers and on the land, for about 35,000 tons. A concrete coaling dock with a lay-by has accommodation for twenty-five barges. As the boiler-house basement is at ground level, ash removal is readily carried out by railway or road wagon, without the use of conveyers or suction plant.
Circulating Water. — This is taken from, and discharged into, the Ship Canal, at points 600 yards apart, by brick-lined culverts excavated from the sandstone 50 feet below ground level. Debris is intercepted by inclined grids and electrically driven travelling-band screens. Two electrically driven circulating pumps supply each condenser. The capacity of each pump is 20,000 gallons of water per minute. The water is measured in the outlet chamber by being passed over a weir.
Boiler-House. — The original section consists of nine Babcock and Wilcox, marine type, steam-raising units. Each unit is complete in itself, and comprises, in addition to the boiler proper, superheater, air-heater, superimposed economizer, chain-grate stokers, mechanical forced and induced draught plant, steel chimney, and grit arrester. The boilers are fired from both sides. The following figures apply to each unit:-
Normal evaporative capacity . 100,000 lb. of steam per hour.
Working pressure . . . 375 lb. per sq. in.
Temperature at stop-valve . 750° F.
Total heating surface . . 45,880 sq. ft.
Grate area . . . . 512 sq. ft.
There are six feed-pumps installed in the turbine-house basement, three of which are electrically driven, and three steam-turbine driven. A closed feed system is used.
The extension consists of three steam-raising units, which are fired from one side only. Two are stoker-fired, and one is equipped for burning pulverized fuel. The normal evaporative capacity is 130,000 lb. of steam per hour. Feed-water is supplied by three pumps, two electrically driven, and one steam-turbine driven.
Turbine-House No. 1. — The three main turbo-alternators installed here were built by the Metropolitan-Vickers Electrical Company. They run at 1,500 r.p.m., and generate three-phase current at 6,600 volts and 50 cycles. The maximum continuous rating of each alternator is 34,375 kva. at 0.8 power factor. The condensing plant was supplied by Messrs. Richardsons, Westgarth and Company, and includes kinetic rotary apparatus and three-stage steam-ejector air-pumps for condenser air extraction. Steam is bled from one stage of the turbines for feed-water heating. Cooling of the alternators is effected on the closed air circuit principle. Three 1,000 kw. turbo-alternators, supplied by the British Thomson-Houston Company, are also installed for house-service purposes. These sets run at 3,000 r.p.m. The exhaust steam is used to heat the feed-water.
Turbine-House No. 2. — This contains a Metropolitan-Vickers two-cylinder tandem turbine, coupled to a 40,000 kw. three-phase, 50 cycles, 6,600 volt alternator. The rotor of a 1,000 kw. house-service alternator is mounted on the same shaft, which runs at 1,500 r.p.m. At the time it was installed, the main alternator was the largest constructed in this country. The condensing plant was supplied by Messrs. Richardsons, Westgarth and Company. The condenser air is dealt with by two three-stage steam-ejectors, and the condensate is withdrawn by two motor-driven extraction pumps. Bleeding is carried out from four turbine stages. Two motor-driven circulating pumps were supplied by Messrs. Mather and Platt 420 volt, metal-clad switch-gear, supplied by the Metropolitan-Vickers Electrical Company for the auxiliary plant, is erected in the turbine-house.
Transformers and Switch-Houses. — All the current generated by the main alternators is stepped up to 33,000 volts in forced oil-cooled, three-phase transformers by the Metropolitan-Vickers Electrical Company. The two transformers which deal with the current from the 40,000 kw. set were, when installed, the largest manufactured in Great Britain. Each weighs 69 tons, and has a capacity of 25,000 kva. House-service transformers, stepping down from 33,000 volts to 420 volts, afford an alternative to the supply given by the house-service turbo-alternators. The high-tension switch-gear, of cellular type, occupying the second and third floors of the buildings, was constructed by the British Thomson-Houston Company. All switching is carried out at 33,000 volts from a separate control room adjoining No. 1 turbine-house. From this room, also, all adjustments of load—including regulation of the steam supply to the main turbines—are made. The two switch-houses are interconnected electrically.
The provision of indicating, integrating and measuring instruments of all kinds is exceptionally complete at Barton, and there is a large and well-equipped laboratory. As is widely known, the station has, for several years, been noted for having secured the highest overall thermal efficiency of British generating stations. In the Electricity Commissioners' returns for the year 1927-28, this figure is given as 21.07 per cent. Under the Central Electricity Board's Scheme for North-West England and North Wales, Barton is scheduled as one of the principal base-load stations.
Manchester Guardian and Evening News
THE "MANCHESTER GUARDIAN " AND " EVENING NEWS."
The offices of the Manchester Guardian and Manchester Evening News, situated in the centre of the city, are prominently associated with Manchester life. The Manchester Guardian was founded in 1821 and first appeared on 5th May of that year, a day which marked the death of Napoleon at St. Helena, and eight years ago celebrated its centenary. The Manchester Evening News is one of the oldest and yet one of the most up-to-date evening newspapers in the country. It was originally produced in 1868. The reputation of the Manchester Guardian extends all over the world, and the Manchester Evening News in perhaps a more circumscribed area is a paper held in high regard for its lofty tone and for its character and enterprise. It was in the offices of these papers that the device which is now generally used for the publication of "stop press" news was invented. The Manchester Evening News was the first evening paper in the country to install a private telegraph wire to London, and both papers early realized the value of the Murray Multigraph Telegraphic system to newspaper work. The mechanical equipment of the offices is efficient and modern, and the growth of the two papers is indicated by the fact that extensive new premises at the rear of the present premises are now is course of erection.
Manchester Ship Canal Company
THE MANCHESTER SHIP CANAL COMPANY, THE PORT OF MANCHESTER.
Manchester Ship Canal
The possibility of making a deep navigable waterway between Manchester and the sea was first discussed over a hundred years ago, the idea being to cut a canal through Cheshire to the estuary of the Dee. The question of a canal was revived in 1877 when the Manchester Chamber of Commerce, concerned at the decline of business in the city, expressed the opinion that a waterway capable of being navigated by large vessels was required. A leader was found in Mr. Daniel Adamson, Vice-President of the Institution from 1885 to 1890, who took the first practical steps by calling a meeting of local authorities and leading industrialists to discuss effective measures for a scheme. This meeting, now historic, took place in June 1882, and the proposal considered on that occasion was a connexion with the Mersey. Two schemes were reviewed - one for a tidal waterway, the other for a canal with locks. The former was rejected as it would have resulted in a dock system lying 60 feet below land level. It was thought better to raise the ships themselves rather than submit to the handicaps entailed by the former method.
After a long struggle to obtain Parliamentary powers for the project and many modifications of the plans, Royal assent was given on 6th August 1885. The contract for the construction of the Canal was made in June 1887 and the first turf was cut at Eastham in November of the same year. Legal difficulties soon gave place to the twin problems of construction and finance, and the triumph over each is an epic in itself. It is sufficient to record that the assistance of the Manchester Corporation was forthcoming when the financial situation became acute; the municipality, recognizing that the enterprise bore upon the fortunes of every citizen, lent its aid and is represented upon the directorate. The construction of the Canal occupied six years at a capital cost of about fifteen million pounds and was opened for traffic to Manchester on 1st January 1894, when the city threw open her new watergate to ocean shipping and turned her face towards prosperity. On that day seventy-one vessels entered the docks. The formal opening by Queen Victoria took place on 21st May. The record of the port has been one of success for the intervening thirty-five years. The annual tonnage has risen from less than a million to nearly seven millions; its equipment and facilities have outstripped expectations and its connexions have extended. It is still possessed of the will and the power for greater development.
The Port To-day. - The entrance to the Ship Canal, which is thirty-six miles long, is on the south side of the Mersey at Eastham, which lies six miles above Liverpool and nineteen miles from the Bar Lightship. The whole of its length, which includes, as well as the main dock system at Manchester, the smaller systems at Ellesmere Port, Stanlow and Runcorn, constitutes the Port of Manchester. The Canal for the lower twenty-four miles of its length was won from the southern fringe of the Mersey by constructed embankments. The next four miles were constructed by canalizing the Mersey up to its junction with the River Irwell which forms the upper section completing the waterway to Manchester Docks. Five locking systems raise the Canal 58 ft. 6 in. in its length; the differences of level vary from 13 feet at Mode Wheel Lock to 16 feet at Irlam Lock. The rivers Irwell, Mersey, Bollin and Weaver, besides smaller streams, constitute a water supply upon which, however, the Canal is not dependent, as at each lock system there is a pumping installation which enables successive levels to be maintained from the sea. The Canal, regularly navigated by ships of 15,000 tons deadweight capacity, has a bottom width of 120 feet, widening at certain points. The depth up to Stanlow is 30 feet and thence to Manchester 28 feet. It is crossed by several swing-bridges and by seven fixed bridges, the lowest of the latter allowing a clear headway of 74 ft. 6 in. from normal water level. In cases where this is insufficient for a vessel's top-hamper, topmasts or funnels are lowered by the sheer-legs at Eastham Laybye.
Through refinements of organization Manchester has attained a high position amongst the leading ports of the Kingdom and the result may be judged by the annual value of its imports and exports recently returned at about a hundred-million pounds sterling.
Manchester Steam Users' Association Museum
THE MANCHESTER STEAM USERS' ASSOCIATION MUSEUM.
Manchester Steam Users Association
The Association was founded in 1854 by Sir William Fairbairn for the prevention of steam-boiler explosions and for the attainment of economy in the application of steam. The Museum contains the following exhibits:-
Portions of the Association's experimental Lancashire boiler on which numerous tests were made between 1874 and 1876; the outcome of the tests is the design of the modern Lancashire boiler.
Fractured portions of other boilers presented to the Association for experimental purposes.
Boiler plates illustrating various defects, namely smooth or uniform internal and external corrosion, corrosion under brickwork or covering, corrosion due to strains.
Defects in water-tubes, smoke-tubes and economizers.
Defects due to caustic embrittlement, and to inferior steel.
Fractures caused by water-hammer.
B and S Massey, Openshaw
MESSRS. B. AND S. MASSEY, OPENSHAW.
B. and S. Massey
The firm was founded in 1861, within twenty years of the invention of the steam-hammer by James Nasmyth. It became a limited liability company in 1912, and has specialized from its earliest days in the manufacture of steam-hammers and kindred machinery. In 1901, after a considerable amount of experimental work, the pneumatic power hammer was placed on the market, and in its improved form, which is capable of striking definite "single" blows, this is rapidly superseding the steam-hammer for most smithy requirements. For heavy forging the steam-hammer still holds its own, and in 1909 the firm introduced their expansion valve which gives increased steam economy and greater safety in operation. Amongst other manufactures should be mentioned that of steam drop-stamps fitted with the expansion valve-gear, and of friction drop-stamps. On account of its economy, the latter tool has a great popularity, and even in its largest size is easy to control.
The works, which occupy three acres of the total site area of six acres, include heavy and light machine shops, erecting shop, pattern shop, smithy and stamp shop, and are electrically driven throughout, power being taken from the Corporation supply. Steam and compressed air are available for testing purposes. The firm was one of the first in the country to adopt the 48-hour week and has instituted bonus and pension schemes for its employees.
Mather and Platt
MESSRS. MATHER AND PLATT, PARK WORKS, NEWTON HEATH.
Mather and Platt
The first works were established almost a hundred years ago in Salford by the great-grandfather of the present chairman. By 1900 the buildings had covered the whole of the site available, and it was decided to secure a new site outside the town for the erection of large modern works. An ideal site was found at Newton Heath. A fifty-acre plot of level land was secured alongside with direct access to the railway and served by main roads, whilst the Rochdale Canal ran along one side of the site. On it a modern engineering works has been built, and extended continually in accordance with an ordered scheme of development. Building operations were commenced in 1900 with the erection of the administration building of two stories, surmounted by the tower, and the adjoining machine shop, which had originally been the machinery annexe of the Paris Exhibition of 1900. This was purchased en bloc, taken to pieces in Paris, shipped in a steamer specially chartered, and delivered at the Manchester Ship Canal Docks. The shop is 376 feet long and 130 feet wide. It is used for the manufacture of valves, etc., and as the general stamping department for the whole of the works. It also contains two large general stores.
Important additions to the new works were made in 1903, 1905 and 1909, when increased accommodation was provided for the electrical engineering department by the construction of two more machine shops, each 376 feet long by 40 feet wide. In 1909 it was decided to make provision for the removal of all remaining departments from the old works in Salford, and in 1910 seven more shops, each 376 feet long, but with bays 52 feet and 42 feet wide respectively, were constructed. Special attention was paid to the important question of foundations. The flooring of wood blocks is laid on a solid bed of concrete of exceptional thickness.
In 1913 pressure of business made further extensions imperative, and accordingly a new wing of four bays, 439 feet long by 161 feet wide, was commenced and completed just before the outbreak of the War. In 1920 demands for increased production necessitated still further extensions, and fourteen of the bays (of a total width of 615 feet) were lengthened by 178 feet.
In 1911 a further two-story building was erected. It is 218 feet long by 48 ft. 6 in. wide, and is constructed of brick with reinforced concrete flooring, indented steel bars being used in its construction. The upper floor of this building forms part of the administration department whilst the lower floor has been equipped as a dining-room to accommodate over 1,000 men. Adjoining the dining-room and communicating with it are a cloak room and lavatory. At the back of the central administration block there is a three-story brick building, with floors and roof of reinforced concrete, indented steel bars again being used. In designing this building special attention was paid to the questions of light, the window area being exceptionally large. Here are centralized all those processes of manufacture which are usually regarded by the insurance companies as hazardous. A shed building, measuring 275 feet by 218 feet, was erected early in 1913, and comprises the brass foundry, smith's shop and grinding shop, also departments for the manufacture of standard plates for sectional cast-iron tanks, and a complete plant for the production on a large scale of chemical fire-extinguishers.
After trying various systems of truck haulage in the works, the use of battery electric locomotives was found to give the best results, but to economize battery current the electric locomotives are also arranged to collect from overhead trolley wires over the section between the works and the main line. A complete system of narrow-gauge tramway lines (21½-inch gauge) is laid in each bay, and trucks capable of carrying 2 tons are employed to convey goods from one department to another. The trucks are fitted with roller bearings, and can easily be pushed by one man. Small battery electric trucks are also being used with success in the shops. Most of the bays are served from end to end by fast-running overhead electric cranes, some bays being provided with three cranes. The average height under these cranes is 24 feet. There are, in addition, pneumatic hoists and jib cranes, operated by hand, placed over the benches.
The general illumination of the shops is carried out by means of high-power, gas-filled, metallic filament lamps arranged above the cranes, and for the individual lighting of machines, where extra light is required, smaller electric lamps are used. The ventilation and heating have been well considered, the latter being by means of steam at low pressure, each bay having its own battery of heating pipes running the full length. The steam is produced by four vertical tubular boilers. The water of condensation from the heating system is exhausted by vacuum pumps, and is delivered into a tank near the boilers. In the heating installation there are 26 miles of piping from 6 inches down to 1¼ inches diameter. A temperature of 55° to 58° F. is maintained in the works, this being found the best average temperature for comfortable working conditions.
The new staff canteen was erected in 1917 and is run by a committee of members of the staff. An efficient first aid department is also attached to the works. The firm early realized the benefits which would accrue through the education of apprentices and a works school was established on the premises, which all the younger apprentices attend during working hours. The school is one of the first recognized by the Board of Education under the new Education Act. Amongst other educational activities are evening classes conducted for members of the office staff in such subjects as typewriting and shorthand. More general lectures are conducted during the winter session, and a technical library has been established for the use of the workmen and staff.
The works now cover about twenty acres of the land available, and there is still ample room for extension. The power for the works is taken from the Manchester Corporation electric supply mains, and is transformed by means of rotary converters and motor generators. The larger machine-tools are driven independently by their own electric motors, and the lighter tools are operated from sections of overhead line-shafting, each section being driven by its own motor. In 1920, a research laboratory was built and equipped on modern lines, and now provides facilities for the thorough investigation of the varied problems which arise in connexion with the running and development of the business, and recently a large office extension has been opened.
Special provisions have been made for testing all products, and all dynamos, motors and pumps are carefully tested for output and efficiency before delivery. Water for manufacturing, fire protection and other purposes is obtained from a large reservoir, into which all the rain-water from the roofs, etc., is drained. From this reservoir the water is delivered by means of a vertical-spindle electrically driven turbine pump through a mechanical pressure filter (both made by the firm) into a large elevated tank placed in the tower, whereby a constant pressure is maintained in the distributing mains. For drinking and all other purposes than manufacturing, water is taken from the Corporation mains. Drinking fountains of a hygienic type are distributed throughout the various departments of the works.
The works are now occupied in the production of textile engineering products for the bleaching, calico-printing and dyeing trades, and textile finishing machinery. Another department deals with alternating- and direct-current motors and generators of up to 2,000 kw. capacity. A third section is devoted to the manufacture of centrifugal and turbine pumps. Another section is concerned with the manufacture and installation of fire protective devices.
Metropolitan-Vickers
THE METROPOLITAN-VICKERS ELECTRICAL COMPANY, TRAFFORD PARK.
Metropolitan-Vickers
Since 1901 when the dispatch of completed goods commenced from the company's works at Trafford Park, the aggregate capacity of apparatus manufactured has totalled well over thirty million horsepower. This total includes turbines and generators up to 67,000 kw. individual capacity, motors up to 25,000 h.p., and every form of electrical apparatus for steam and water power generating and distribution systems, for railway and tramway traction and for service in every kind of industrial application. The company has also a factory at Sheffield and subsidiary companies manufacturing insulating materials, lamps, fittings and domestic appliances. The wide range of the company's products enables it to undertake comprehensive electrification schemes, which is of considerable benefit to the purchaser. The main works at Trafford Park are one of the largest and best equipped in the world, having a floor area which recent extensions have increased to 11 million square feet. The number of workpeople and staff in this factory at the present time is over 10,000 and the total number of the firm's employees is over 15,000.
The buildings run north and south. The northern end constitutes the frontage and provides accommodation for the administration, technical, selling and other staffs. The southern end borders on the Bridgewater Canal. Within easy reach are the docks of the port of Manchester and the Ship Canal. Materials are delivered to the southern end of the workshops over the railway tracks which intersect each building. The finished products are picked up at the northern end by the service railway for dispatch to their destination. The total weight of incoming material and outgoing finished products exceeds 500 tons per day.
The factory buildings are designed to give continuous central aisles with flanking galleries. In the main shops the aisles are of considerable size, each being 900 feet in length, by 90 feet wide, the total overall width of the shop being 440 feet and the height 80 feet to ridge of roof. The railway tracks pass down the centres of the aisles to feed or draw from either side. If desired, the work can be picked up at the point of assembly to be loaded directly into the railway wagon or truck. Each of the main aisles is spanned by three or four 50-ton electric cranes having full command of both the width and length of the shop. The overhead handling equipment is supplemented by a number of jib cranes disposed in a row along either side of the aisle, to swing the material to and from the machines and in and out of the detail assembly bays or stores under the side galleries. This arrangement leaves the whole of the central space of the well free for manufacture and assembly of the largest units. One advantage of the lay-out is the flood of natural illumination from the glass roof over the whole area of the main floor. The galleries on either side of the aisles, which are continued round the latter at each end, as well as the spaces beneath, are allocated to the manufacture of the lighter products, such as switch-gear, control gear, small motors, etc., and components required in the manufacture of the larger machines.
In the main shop one aisle is devoted to heavy mechanical units, e.g. turbines, condensers and their auxiliaries, with a section set apart for the manufacture of special gearing used in connexion with marine turbines. The second aisle is reserved exclusively for the manufacture, assembly and testing of the larger electrical units, such as heavy-duty motors, rotary converters, motor-generators and alternators. In an adjoining aisle is the recently reorganized motor test-bed, which is the largest and most completely equipped in this country. The galleries are sectionalized in a similar manner, each section being devoted to the production of one class of article.
On the eastern side of the main avenue, which runs north and south through the works and opposite to the main building, is the transformer department. It is the largest in the country for the manufacture of such apparatus, and the largest transformers of British origin have been built in it. Next to the transformer shop, also on the east side of the main avenue, is the foundry, which is a spacious building, and is exceptionally well lighted. It is equipped with the latest types of moulding machinery, and all the castings used in the works, excepting those of steel, are made here. The plant is capable of dealing with large-size castings up to 60 tons in one piece required for turbines, condensers, bedplates, stators, etc.
An important works extension of special interest is a large building which has recently been erected to the west of the main works. It is 420 feet long and 220 feet wide and provision has been made for extensions which may more than double this size. It is equipped for the assembly and testing of the largest switch-gear units, of both the metal-clad and outdoor types, required for the British "Grid" and other super-power schemes in connexion with which the company has large contracts in hand. The testing equipment includes a 500,000 volt testing transformer and a Schering bridge equipment for 300,000 volts. This equipment enables the energy loss in dielectrics under working stresses to be measured with precision, and is the first to be built for such a voltage in this country. The company's present programme includes the development of switch-gear for service up to 230,000 volts, and units up to 2,000,000 kva. breaking capacity.
All plant in the works is electrically driven, and under normal working conditions the demand exceeds 17,500,000 units per annum.
Formerly power was generated in a central station in the works, but the space was required for extension of workshops, and the generating plant was removed, a new transformer and rotary converter substation, having a capacity of 10,000 kw., being erected outside the main building. The local authority supplies energy at 6,600 volts, which is stepped down for workshop requirements. The substation equipment includes a rotary converter set arranged for fully automatic or supervisory control and is typical of many installations made by the company for power supply and traction systems in this country and abroad.
The Metropolitan-Vickers Research Department, which is one of the notable industrial research organizations in this country, is accommodated in a group of buildings situated to the south of the works. A two-story building, forming the frontage of the group, houses the administrative staff and the intelligence section, including the library. Immediately behind are two single-story laboratories each 100 feet long by 70 feet wide; one is occupied by the electrical and magnetic group and the chemical and physics sections, the other contains the mechanical, metallurgical and materials and process sections. Further back stands the large building which houses the high-voltage laboratory and a number of smaller laboratories equipped for a variety of special work. The equipment of the laboratories includes many items of interest. The mechanical and metallurgical laboratory, in addition to a range of modern testing machines has a special machine for measuring the creep of metals, under controlled tension and temperature conditions, to within one-millionth of an inch per inch of test specimen. There is also apparatus for the analysis of vibration and its effect in producing fatigue in metals, and Professor E. G. Coker's apparatus for the optical determination of stress in strained members. Of considerable interest is the precision rolling mill used for rolling tungsten, molybdenum and zirconium and for the preparation of very fine metallic foils, such as copper and nickel, required for experimental work. A considerable amount of work is being done with the mill on a commercial basis for the preparation of molybdenum sheets up to 6 inches in width and 3 ft. 6 in. in length and of 1/400-inch in thickness. The apparatus in the high-voltage laboratory includes two half-million volt transformers built by the company and arranged for use either separately, or in cascade, to give one million volts. There is also a million-volt surge testing equipment to give steepwave-front, high-frequency impulses in investigations on the effects of lightning on high-voltage apparatus. For tests upon outdoor type apparatus an arrangement is provided by means of which artificial rain of any required characteristics can be produced over the test area. Recent additions to the department include an acoustic laboratory for the investigation of the noise emitted by machinery, with a view to its reduction, and a photometric tunnel for the study of illumination problems. The organization of the department is such that in addition to dealing with the problems of current manufacturing work it is able to undertake all the stages of development required to bring a discovery in pure science to a commercial manufacturing proposition.
Nasmyth, Wilson and Company
MESSRS. NASMYTH, WILSON AND COMPANY, PATRICROFT.
Nasmyth, Wilson and Co
The firm was founded in 1836 by James Nasmyth, whose name will always be associated with his invention of the steam-hammer and whose life history is perpetuated by the writings of Samuel Smiles. The works, situated on the L.M.S. Railway about six miles from Manchester, occupy the historic corner where the original railway between Liverpool and Manchester crossed the first canal built in this country by the Duke of Bridgewater. Originally the works manufactured locomotives, steam-engines and machine-tools of all descriptions. However, on patents being taken out for the steam-hammer, the activities of the firm were directed solely to the production of this tool, for which there was a large demand both at home and abroad. After the patent rights of the steam-hammer lapsed, the works again took up the manufacture of locomotives, etc. The customers of the firm include the chief railways of the world. In addition to the usual machine and erecting shops equipped with a number of modern machine-tools, and arranged according to modern ideas of organization, the works contains its own forge and iron foundry. About 700 workmen are normally employed throughout the different departments. With the consulting engineers the firm have recently been instrumental in carrying out a number of new standard designs of locomotives of metre gauge for the Indian State Railways, and have lately developed several interesting types of locomotives of various. gauges for work in the Crown Colonies.
National Gas Engine Company
THE NATIONAL GAS ENGINE COMPANY, ASHTON-UNDER-LYNE.
National Gas Engine Co
The company was formed in 1889 by Mr. H. N. Bickerton, and has developed into one of the largest concerns in the world devoted to the manufacture of internal-combustion engines and suction-gas plants. The works, which cover over thirty acres, are effectively served by road and railway and are divided into a series of twenty large bays well served with drawing offices, laboratory and pattern shop. The iron foundry comprises three large bays and is capable of an output of 200 tons per week, including castings up to 20 tons in one piece. It is equipped with modern cranes, moulding machines, sand-blast and sand-handling plant, etc. Separate shops are devoted to the manufacture of bronze and brass castings and to white-metalling and case-hardening. The latter shops are equipped with modern gas-fired furnaces. The machine shops, which occupy seven bays, are equipped with up-to-date machine-tools, many being specially designed for the company's particular requirements. As far as possible all parts move forward continuously from the foundry or stores to the erecting shop. Engines are erected and tested in the bays adjoining the machine shops. A special department deals with the supply of renewals and spare parts. Practically all the machinery is electrically driven, the supply being taken from the power station at each end of the works. The generators in the two stations are driven by oil- and gas-engines of various designs of the company's manufacture. Gas is supplied from a 3,000 h.p. Mond gas plant fitted with ammonia recovery, tar dehydrating and oil recovery plant, which considerably reduce the cost of the gas.
The productions of the works consist of oil- and gas-engines and suction-gas plants. The oil-engines will run on practically any kind of fuel oil, whilst the gas-engines are suitable for work on producer- gas, coal gas, coke-oven gas and blast-furnace gas. Convertible engines able to run either on gas or oil are also manufactured. The range of sizes made is from 1 h.p. to 1,500 h.p. A number of crankless gas-engines have recently been built and a 300 h.p. unit of that design may be inspected in the power house.
Pilkington Tile and Pottery Company
THE PILKINGTON TILE AND POTTERY COMPANY, CLIFTON JUNCTION.
Pilkington Tile and Pottery Co
The company was formed thirty-five years ago for the purpose of manufacturing wall and floor tiles of all descriptions and architectural faience and fireplaces, and a few years later commenced the making of decorative pottery. Tile-making, however, is the largest and most important side of the business, although the name of Royal Lancastrian Pottery is world famous for its artistic qualities. Clifton Junction was chosen as a site for the works because of its suitability, being adjacent to large collieries and convenient transport facilities both for rail and water carriage. In early days coal was extensively used for firing the ware, consequently its cheapness was of importance. The raw materials, of which clay is the chief, are mainly brought from the South of England, china clay or kaolin from Cornwall, and ball clay from Dorset. Flint is imported from France in the form of boulders, and felspar (used for the manufacture of vitreous tiles) from Norway. All the glazes and colours are made in the works from the firm's recipes. Mixing the various clays and flint to form the "body" of the tile or vase, and the preparation of glazes and colours call for experience and scientific accuracy, but the vital and most important process is firing the ware. This process falls into two separate parts, the Bisque or preliminary firing of the clay tile or vase, and the Glost or glazing fire after the glaze has been applied.
In 1921 the company built a large continuous gas-fired tunnel kiln, 243 feet long, for glazing, which was followed a few years later by a continuous tunnel kiln, 305 feet long, for Bisque firing. Three years ago a second glazing tunnel kiln similar to the first was erected. The continuous kilns, in which the fire zone remains stationary and the articles being fired pass through on specially constructed trucks, took the place of the individually coal-fired small muffle kilns and round pottery ovens. The continuous ovens are equipped with the latest instruments for registering temperatures, draught, etc., and enable firing to be carried out with a higher degree of accuracy than was possible with the older type of oven. The installation of the large continuous ovens led not only to an enormous saving of coal and a considerable saving of labour but also to an extensive reconstruction and enlargement of the works generally.
Tiles are made by the most up-to-date methods and the various processes are carried out in large single-floor buildings, and it is interesting to find in the same works that tiles are being produced with the most efficient and labour-saving plant by mass-production methods, and that pottery is being made in comparatively small quantities, under conditions which combine the methods of the early craftsman with the most recent scientific knowledge.
Post Office Telephone Exchanges, Manchester
THE POST OFFICE CITY AND CENTRAL TELEPHONE EXCHANGES, YORK STREET.
These exchanges, which were opened in 1909 and 1917 respectively, serve the greater portion of the City telephone area of Manchester and are accommodated in one building. The basement contains the central-heating plant and the street cables are led in at this level. The ground floor provides an entrance hall and telephone call-boxes together with space for the Operating School, the Observation Room and the Dining and Staff Retiring Rooms. The apparatus room on the second floor contains the distributing frames, electromagnetic relays, call registers, test clerks' desks and large Exchange storage batteries with their charging machines.
All lines enter the building by means of underground cables, and these are terminated on the "vertical" side of the main distributing frame. The lines are necessarily collected in order of locality, and have, therefore, to be subsequently arranged in proper order according to the subscribers' numbers, by being cross-connected to the opposite or "horizontal" side of the main frame. By means of other cables the lines are thence connected to intermediate distributing frames — one for each exchange — for the purpose of distributing the subscribers' lines among the various operators' positions in order to equalize the work which the different operators are called upon to do. All signalling on the Exchange is done by means of small electric glow lamps, and the electromagnetic relays which bring them into circuit are mounted on special relay racks in the apparatus room. Another rack accommodates the subscribers' call registers, by means of which all effective calls made by subscribers are recorded. Each pair of cords used for making connexion at the switchboard is provided with a special key which is pressed by the operator on the satisfactory completion of the call and this actuates the register of the subscriber who originated the call. Many thousands of lines pass through the apparatus room, and a specially trained staff is employed to anticipate and to prevent trouble as far as possible on this mass of wires and to localize quickly, by means of the test desks in the apparatus room, any faults which may arise.
The first floor is occupied by the Central Exchange and the third floor by the City Exchange. The Central Exchange was equipped by Messrs. Peel Connor and the City Exchange by the Western Electric Company, and each was designed to accommodate 9,600 subscribers' lines. The switching apparatus in each case consists of continuous suites of switchboards of two types, an "A" suite for handling originating calls and a "B" suite for handling calls incoming from other exchanges. The Central Exchange "B" suite is of a special type enabling through calls to be dealt with. "Inquiry" positions, Divisional Supervisors' desks, etc., occupy the central portions of each switchroom.
Further particulars, from which the size and importance of these Exchanges may be gathered, are as follow:-
City Exchange | Central Exchange | |
"A" suite operating positions | 109 | 108 |
"B" suite operating positions | 40 | 54 |
"Inquiry" positions | 10 | 10 |
No. of subscribers' lines actually working | 8,878 | 8,497 |
No. of direct junctions outgoing to other exchanges | 851 | 1,243 |
No. of direct junctions incoming from other exchanges | 933 | 1,392 |
Staff Employed: | ||
Supervising force | 25 | 26 |
Operating force | 198 | 208 |
Traffic Handled during 1928: | ||
Local calls originated . . | 20,027,701 | 16,797,037 |
Trunk calls originated . . | 1,577,862 | 1,268,072 |
Hans Renold, Didsbury
MESSRS. HANS RENOLD, BURNAGE WORKS, DIDSBURY.
Hans Renold Ltd
In 1879 Mr. Hans Renold commenced in a small cellar in Salford the manufacture of chains for textile machinery, and the next year patented the bush roller chain which was later fitted to the first safety bicycle. The extension of the use of chains for power transmission and the invention of the Renold silent chain, now known as the inverted tooth type, necessitated larger premises, and a six-story building was erected in Brook Street, Chorlton-on-Medlock. By 1915 the growth of the business was such that the present site of forty-seven acres at Burnage was acquired. The works, which cover an area of eleven-and-a-half acres are single-story buildings, except for some of the offices, the canteen, etc., and consist of two buildings separated by a central road and connected by picturesque verandas. The workshops are 860 feet long by 500 feet wide, and have a north light area of 200,000 sq. ft. The offices, which occupy a floor space of 30,000 sq. ft., are separated from the works by a wide ferro-concrete road, bordered by gardens. Adjoining the offices is the canteen and the Social Unions building. The manufactures include chains for cycles, motor-cycles and automobiles, also a wide gauge of power transmission drives for industrial purposes, including both wheels and chains. The equipment comprises many special machines amongst which might be mentioned those for grinding to fine limits rods up to 12 feet long, blanking and holing presses for links, cutting and drawing presses, automatic coiling machines, and multiple presses which are able to turn out complete links at one setting. There is a well-equipped inspection and testing department, all material received being subjected to rigorous chemical and physical examination. On the inspection side, among the many devices might be mentioned the automatic gauging machines, and the plant for subjecting finished chain to continuous tests.
A. V. Roe and Company
MESSRS. A. V. ROE AND COMPANY, NEWTON HEATH.
A. V. Roe and Co
This firm is engaged in producing aircraft for both civil and government requirements. For civil purposes the works produce the "Avro X", a large three-engined monoplane of the type which successfully made the transatlantic crossing from east to west, also the "Avro V", a smaller machine fitted with three ArmstrongSiddeley "Genet" engines, and the "Avro Avian", a light aeroplane which has created many records, including that made by Hinkler in his great flight to Australia and other long-distance flights carried out by private owners. The type of service aeroplane on which the shops are at present engaged is the "Avro 504 N", which is the standard training machine of the Royal Air Force. These machines are fitted with the 180 h.p. "Lynx" engine, and were evolved from the well-known training machine "Avro 504 K".
In the transition from timber to metal construction, the firm has specialized, after considerable experiment, on welded tubular construction except for the wings, which are still made from timber with certain exceptions in the case of service machines. The firm has a large aerodrome at Woodford, near Stockport, where all experimental and test flying is carried out.
Ruston and Hornsby, Reddish
MESSRS. RUSTON AND HORNSBY, OIL ENGINE WORKS, REDDISH.
Ruston and Hornsby
These works were built by Messrs. J. H. Andrews and Company, who were the manufacturers of the original "Bisschop" engine as long ago as 1878. They have since been devoted entirely to the production of internal-combustion engines, notably the "Stockport" gas-engine, at first made to operate on the two-stroke cycle. The manufacture of engines operating on this cycle was discontinued in favour of the "Stockport" four-stroke cycle gas-engine, and in 1893 the firm constructed an engine of 400 b.h.p. which was the largest then made. Messrs. Andrews amalgamated with Messrs. Hornsby of Grantham in 1906, the works at Reddish continuing to produce the "Hornsby-Stockport" gas-engine. When Messrs. Richard Hornsby and Son became part of the firm of Ruston and Hornsby, these works still continued the production of gas- and oil- engines, and at present they are mainly devoted to the construction of vertical oil-engines fitted with the firm's system of airless injection of fuel.
Agecroft Power Station, Salford Corporation
SALFORD CORPORATION ELECTRIC POWER STATION, AGECROFT.
Agecroft Power Station
The construction of the power station was commenced in January 1923, and the station was put into commission in December 1924. At present it supplies the City of Salford and the Urban District of Prestwich, with a combined population of about 260,000, but as it is one of the selected stations under the National or Grid Scheme for electricity supply, it will soon be supplying a much larger area. The total capacity of the station is 57,500 kw. with plant consisting of three 12,500 kw. and one 20,000 kw. generating sets. The last-mentioned set is now being installed.
Coal Supplies and Handling. — Coal supplies are available by road, rail or canal. Rail- and canal-borne coal is brought for a distance of about half a mile from Clifton Junction sidings and the canal bank, in trucks drawn by an electric locomotive on a narrow-gauge line. Ample storing ground for coal is available.
Boiler-House. - The boiler equipment comprises six Babcock and Wilcox marine cross-drum type boilers installed in 1923-4, each rated for a normal evaporation of 65,000 lb. per hour, the overload capacity being 78,000 lb. per hour for two hours. There are also in course of installation two John Thompson four-drum vertical bent-tube boilers, with integral economizers arranged as a third bank of tubes, each rated at a normal evaporation of 100,000 lb. per hour with an overload capacity of 20 per cent. Each of these boilers is fitted with the Underfeed Company's "L" type twin chain-grate stokers. Each boiler unit is complete in itself with economizer, separator, forced and induced draught fans and steel chimney, with the addition of air-preheaters and grit catchers on the two Thompson boilers. The working pressure is 325 lb. per sq. in., and the superheaters raise the temperature of the steam to 720° F. at the stop-valve. Both steam and electrically driven feed-pumps are installed, and the station operates on the closed feed system.
Turbine-House. — There are four turbo-alternator sets, built by the Metropolitan-Vickers Electrical Company, each rated at 3,000 r.p.m. Nos. 1 and 2 are single-cylinder sets, each of 12,500 kw. maximum continuous rating; No. 3 is a two-cylinder set of the same capacity; and No. 4 is a two-cylinder set of 20,000 kw. capacity.
Cooling Water and Towers. — The River Irwell has so for provided sufficient water for condensing purposes, but with the increased loads which are anticipated in the future there is no doubt that it will be necessary during dry periods to use the cooling towers which were provided as a safeguard when the station was built.
Agecroft Station with an average thermal efficiency of 18.71 per cent was the most efficient of its group in the Kingdom for the year ended 31st March 1928. The group comprised all the power stations, thirty-two in number, with an annual output between 50 and 100 million units. The station has to supply the whole load of its district at all times without assistance, and the efficient results obtained are not therefore in any way due to very high plant or station load factors obtained by parallel running with other stations.
Henry Simon, Cheadle Heath
MESSRS. HENRY SIMON, CHEADLE HEATH.
Henry Simon
The firm was founded fifty years ago and has specialized in the manufacture of grain-cleaning and flour-milling machinery. In recent years the manufacture of conveying plant has been undertaken and this branch of work now occupies an important place. The development of the pneumatic system of discharging and conveying coal, grain, oxides, etc., in bulk has also received considerable attention. Before the erection of the new factory at Cheadle Heath in 1926 there were two workshops, respectively at Stalybridge and Bredbury, which, though able to deal with a large amount of work, were not arranged to the best advantage. The present works, which are situated in pleasant surroundings, occupy six acres of the site of twenty-three acres, and are laid out on one floor and under one roof to facilitate communication between various sections. The separate sections are: (a) joiners' shop, comprising machinery work, bench work, and assembly; (b) sheet-metal department, comprising black iron sheeting and tinsmiths' shops; (c) machine shop; (4) fitting and erecting shops; (e) paint shop and packing department. A feature of the organization of the works is the stores which extend along the whole of one side of the buildings and to which the different departments are arranged at right-angles, so that the products of a department can be passed into store and retained till required, by which means internal transport is reduced to a minimum. The social side of the works comprises a spacious and well-lighted canteen, cricket ground, hard courts, bowling green, football ground and a miniature golf course.
The Superheater Company, Trafford Park
THE SUPERHEATER COMPANY, TRAFFORD PARK.
Superheater Co
The works are devoted entirely to the manufacture of superheater apparatus of the "M.L.S." (marine, locomotive and stationary) type, and contain specially designed machinery for dealing with the various operations in the manufacture of elements. As built in 1914, there were only two bays, but the shops now comprise five large bays forming one block covering over 50,000 sq. ft. Each bay is served by fast overhead cranes. Of particular interest is the manufacture of the return-bend which is carried out by the "M.L.S." machine forging process without welding. There are three complete plants for this process capable of dealing with tubes up to 3 inches diameter. The tubes are heated in oil-fired furnaces preparatory to the forging operation. The plant comprises special apparatus for bending, offsetting, testing, etc., and since its installation upwards of one-and-a-quarter million ends have been produced.
One bay is used as a machine shop where superheater headers are machined, and much of the plant has been specially adapted for the work. Extensive use is made of compressed air at 100 lb. per sq. in. for the operation of machines. Cast iron is the material employed for locomotive headers, whilst the marine and stationary headers are made of steel. For the tests of superheater elements and headers prior to dispatch, hydraulic pressure up to 2,500 lb. per sq. in. is available. The output of headers exceeds 1,250 per annum, whilst the annual output of superheater elements exceeds 68,000, some weighing as much as 7 cwt. and containing up to 230 feet of tube each. 300 workmen are employed.
Taylor Brothers and Company
MESSRS. TAYLOR BROTHERS AND COMPANY, TRAFFORD PARK STEEL WORKS.
Taylor Brothers and Co
These works are devoted to the manufacture of wheels, tyres and axles for railway locomotives, carriages and wagons. The tyre plant was laid down about eighteen years ago but has been added to and improved continuously and now represents an up-to-date and efficient works for its purpose. The various processes in the manufacture of a tyre are as follows. Steel is melted and cast into the form of an ingot about 6 feet long in the body. Three sizes of ingot are used, namely 13 inches, 16 inches and 19 inches diameter. The ingots are cast with a sink-head from 12 to 18 inches long, which is cut off and returned to the melting department. This method, although more expensive than that of casting a single ingot for each tyre, is more satisfactory as the complete removal of the pipe cavity ensures sound metal throughout the tyres. The ingots are cut up into a number of blocks on a slicing machine, the length of a block depending on the size of the tyre. Each ingot on the average furnishes six blocks. The blocks or "blooms," as they are called, are charged into a continuous inclined gas-fired furnace at its cooler end and emerge from the hotter, whence they are charged by a crane into gas-fired reverberatory furnaces for final heating to forging temperature. It is interesting to note that all forging operations take place without further heating. The bloom is flattened under a steam-hammer till it is within an inch of the width to which the tyre is finally to be rolled, and a hole is punched through the centre. The flattened and punched bloom passes to the Becking mill where the central hole is enlarged and a start given to the outside flange. The roughing mill, driven by a 1,500 h.p. steam-engine, is fitted with rolls which surround the whole section of the tyre so that work is done on the plastic metal in all possible directions and complete metallurgical deformation of the grain ensured, and the tyre is gradually enlarged in diameter and at the same time shaped accurately for profile. In the finishing mill, the tyre is made accurately to size, and by means of manually operated side rolls its roundness is ensured. After branding on a hydraulic press, the tyres are allowed to cool down to atmospheric temperature. The operation of rolling a locomotive tyre weighing 12 cwt. does not occupy more than five minutes, and the plant is capable of turning out in a single shift of eight hours some 700 tons of locomotive tyres. After forging the tyres are bored to finished size. The various departments are: the stockyard where material for melting into steel is stored (this yard has a 10-ton crane fitted with a magnet); the steel-melting stage, with seven open-hearth furnaces, each with a capacity of 40-50 tons per cast (this department is provided with charging cranes, and waste-heat boilers are fitted in connexion with four of the furnaces); ingot slicing shop containing heavy parting machines capable of dealing with ingots up to 22 inches diameter; the forge and rolling mills, the operations in which have already been noticed; tyre mill engine-room which contains three 1,500 11.p. three-cylinder compound horizontal engines (the exhaust steam from two of the engines is passed to a low-pressure turbo-generator); the power house which contains the 750 kw. mixed-pressure turbo-generator and two 450 kw. high-speed steam-engines by Belliss and Morcom direct coupled to d.c. generators, and three steam-driven Worthington hydraulic pumps, two developing pressure at 750 lb. per sq. in. and one at 2,240 lb. per sq. in.; boiler-house, the equipment of which comprises eight Babcock and Wilcox boilers, fitted with superheaters and Green's economizers, and two Ruths steam accumulators.
Other departments of interest are the pump-house which deals with the water supply and distribution throughout the works; the gas machines for the steel-melting department; smithy, electricians' shop and millwrights' shop dealing with maintenance of plant; the axle department, including the axle forge; wheel forge, wheel-rolling mill, wheel machine shops and wheel department boiler-house (the latter is provided with two Babcock and Wilcox boilers, and with a Wood steam generator and two Stirling boilers, which are fired with pulverized fuel); and the pulverizing plant which has a 20-ton raw-coal bunker, two 5-ton coal driers, two 5-ton Raymond pulverizing mills and two 30-cwt. shooting tanks.
Tootal Broadhurst Lee Company
THE TOOTAL BROADHURST LEE COMPANY.
Tootal Broadhurst Lee Co
The firm specializes in the manufacture of high-class fabrics of every description. They have extensive mills for spinning, manufacturing and finishing. A few of their special productions are the well-known "Pyramid" and "Lissue" handkerchiefs, "Tobralco," "Tarantulle" and "Pique."
Trafford Park Estate
TRAFFORD PARK ESTATE.
Trafford Park
No description of the Port of Manchester would be complete without reference to the large industrial estate which adjoins the Manchester Docks, namely Trafford Park. From considerations of transport facilities, rail, road, and water (including oceanic communication) and of its proximity to the South Lancashire coalfield, the park was ideally situated for the development of a large and successful industrial area, and in 1896 the demesne of the ancient family of de Trafford was conveyed to Messrs. Trafford Park Estates. In the last thirty years the estate has been developed for industrial purposes and there are now located in it about 130 modern factories and warehouses. Amongst the more notable of these may be mentioned the following: Metropolitan-Vickers Electrical Company; Ford Motor Company (England); Redpath, Brown and Company; Anglo-American Oil Company; Turner Brothers Asbestos Company; Corn Products; Courtaulds (Chemicals); Brooke Bond and Company; Hovis Bread Company; Carborundum Company; Taylor Brothers and Company; Shell-Mex; W. T. Glover and Company; Massey, Harris and Company; British Alizarine Company; and Southern Oil Company.
The reason for such a concentration of industrial activity in one locality is that Manchester is the centre of the most densely populated area in the United Kingdom and is therefore an excellent centre for distribution. An inexhaustible supply of labour both skilled and unskilled exists, as there is a population of over a million within four miles of Trafford Park. It has the further advantage that all import and export traffic can be hauled by rail from ocean steamers in the Manchester Docks to and from the factories at very low cost. Each factory has its own railway siding connected with the Estate's statutory railway and with all the main-line railways of the county. Gas, water, and electricity supplies are available and the leading oil companies have depots on the Estate. The local rates are low and every facility for factory purposes is provided.
Budenberg Gauge Company. Altrincham
THE BUDENBERG GAUGE COMPANY, WOODFIELD ROAD, ALTRINCHAM.
Budenberg Gauge Co
The present works, which were erected in 1913 and 1914, comprise a two-story fireproof building accommodating the offices, storerooms, laboratory and test-room. At the rear of the main building is the engineering shed which covers 18,000 square feet. There are also several other buildings used for various purposes. The works are principally devoted to the manufacture of all types of pressure-gauges; also dial thermometers of both the steel-tube, mercury and the vapour-tension types for industrial purposes; tachometers for turbines and other machinery; automatic recording instruments for temperature, pressure and speed; mercury columns; depth gauges; gauge-testing apparatus and kindred instruments. The equipment comprises modern machinery for the large-scale production of instrument parts finished to a high degree of accuracy, and consequently includes many complete series of press-tools and jigs. The testing apparatus includes a 55-ft. high mercury column for pressures up to 300 lb. per sq. in. with full error corrections. For higher pressures deadweight testers of both the differential and the single-piston types are employed. A deadweight tester for the accurate measurement of pressures up to 32 tons per sq. in. was recently made and another for use up to 40 tons per sq. in. is in course of construction. The piston for the latter instrument has been certified by the National Physical Laboratory as having a mean diameter within 0.00001 inch of nominal, and to be straight and truly cylindrical within 0.00002 inch. The weights are accurate to within +/- 0.5 grain. In the test-room there are pumps capable of producing violent pulsations in pressure, which are used for testing gauge tubes and working parts for durability under severe conditions, and for the determination of the best materials and design.
Churchill Machine Tool Company, Broadheath
THE CHURCHILL MACHINE TOOL COMPANY, BROADHEATH.
Churchill Machine Tool Co
The original works, which were founded in 1901, were situated in Salford and were engaged solely in the manufacture of small tools and turret equipment for automatic machines. Owing to increasing business, new works were acquired three years later in Pendleton and in the following year the firm decided to specialize entirely in the manufacture of precision grinding machines which at that time were made almost exclusively in the United States of America. The first two types to be built were the plain and universal models. Extensions to the Pendleton works were made continuously up to 1920 when the need for a larger and more modern factory became imperative, and in the following year the present works were erected. As an indication of the range of precision grinding machines built by the firm (no other machine-tools being built in the works) it may be stated that they vary in weight from 30 cwt. to 50 tons. Grinding machines embodying many patented features for all classes of engineering work are supplied. In recent years the manufacture of grinding machinery for the motor-car industry, in locomotive building and repair, and for the sheet metal and paper industries, has been developed. A subsidiary side of the firm's activities is the manufacture of "Comet Brand" high-speed steel milling cutters, reamers and other small tools.
H. W. Kearns and Company
MESSRS. H. W. KEARNS AND COMPANY, BROADHEATH.
H. W. Kearns and Co
The works, which are constructed on modern lines, were established in 1907 for the manufacture of high-class machine-tools. A few years after its commencement the firm concentrated entirely on the manufacture of their well-known universal horizontal surfacing, boring, milling, drilling and tapping machines, large numbers of which have been supplied all over the world. The factory, which stands in about four acres of land, is electrically driven throughout. The total number of people employed at the present time is about 250.
Linotype and Machinery Company. Altrincham
MESSRS. LINOTYPE AND MACHINERY COMPANY, ALTRINCHAM.
Linotype and Machinery Co
The company's estate and works are at Altrincham, Cheshire, about eight miles south-west of Manchester. The estate covers about sixty acres, of which about twelve-and-a-half acres are occupied by the works buildings and offices. The remaining forty-eight acres are occupied by cottages, allotments, and playing fields.
The works buildings comprise the offices, drawing office, the main machine shop, the foundries, erecting shops, pattern shop and stores, boiler- and engine-house, etc., and with the exception of the offices and a new storage building are all on one floor with top lighting. The main shop containing the ordinary machine departments (planing, milling, turning, etc.) covers three acres under one roof, and also houses the departments containing the special tools for the manufacture of matrices, moulds, and magazines for the Linotype. The central gangway running from one end of this shop to the other is 520 feet long by 12 feet wide.
The works are self-contained and self-supporting. They produce electricity for their own power, light, and heat, the main generating plant having been entirely renewed during the last few years on the most modern lines. It now consists of three Stirling water-tube boilers of the latest type, each with under-feed stoker and forced draught, each with heating surface of 3,841 sq. ft. and each evaporating 15,000 lb. of water per hour. They operate two turbogenerators each producing 600 kw. or 800 h.p. There are other smaller engines used as standbys, and the total potential power is nearly 2,000 kw. or 2,500 h.p.
With the exception of some small parts (mainly involving rubber products) the company's machines are entirely produced at the works, in which every process is carried out from the original castings to final electroplating, where necessary. During the last seven years the whole of the plant has been reorganized and where necessary renewed by the installation of modern and improved machine-tools.
The main foundry measures 140 feet by 70 feet, and there are four cupolas and the necessary core ovens. The plate moulding shop is 360 feet long by 42 feet wide, and is equipped with two furnaces melting 3 and 2½ tons per hour respectively; its equipment also includes a pneumatic moulding machine, and hand turnover moulding machines, and electric driers for moulds. Adjacent is the fettling shop, equipped with an air-compressor for sand-blasting, also a cleaning room, sand-blast tumblers, and emery-wheel grinders. The smithy includes eight hearths and two 5 cwt. pneumatic hammers.
In the capstan and automatic departments there are sixty machines, comprising capstan, turret, and automatic lathes for the manufacture of all sizes of screws, bolts, pins, nuts, and washers. The gear-cutting department has an equipment of twenty-six machines comprising spur, spiral, bevel, and worm-gear cutting machines, also rack-cutting and broaching machines, all of which are in constant operation for the output of gears and press-tool parts. In one portion of the general stores building there is a large battery of automatic stamping and blocking presses, which produce all the small parts punched from metal strip. The fitting and erecting shop is 580 feet long with a width varying from 160 feet to 180 feet.
There are in the works nearly 800 machine-tools of major importance, and nineteen cranes varying from 1½ tons to 12 tons. There are nearly 1¼ miles of line-shafting, several miles of electric cable and 150 independent motors from ⅙ to 60 h.p. for machine-tool driving and testing. The standard of accuracy is kept very high, and in certain departments the margin of error allowed is only one-fourth of 1/1,000-inch. The patterns and punches for the manufacture of matrices are produced by a complex series of machines specially invented for the purpose and manufactured by the company. On an average a stock of over 25 million matrices is kept at the works, and this is continually added to, so that the needs of any customer in any part of the world may be instantly met.
All the offices and departments, managers and foremen are linked together by an automatic telephone of 100 numbers. There are at present about 2,000 persons employed in the works. There are rest rooms for men and women and an ambulance service. In the canteen, capable of seating 800 people, meals at cost price are provided.
There are on the estate 222 houses mainly occupied by the company's employees. There is also a guest house standing in its own grounds. The estate has been laid out tastefully and there is a cricket ground measuring about two-and-a-quarter acres, a football ground measuring three-and-a-quarter acres and capable of holding 7,000 spectators, three hard and five grass tennis courts, a hockey ground measuring three acres, two bowling greens, and a large number of allotment plots which are let to the workmen. There is also a social club with pianos and billiard tables, a bowling club, a tennis club, a cricket club, a football club, and a hockey club, all of which are organized by the employees.
George Richards and Company, and Tilghman's Patent Sand Blast Co
MESSRS. GEORGE RICHARDS AND COMPANY, & TILGHMAN'S PATENT SAND BLAST COMPANY, BROADHEATH.
George Richards and Co, Tilghman's Patent Sand Blast Co
The former works were established in 1880 and are now solely confined to the manufacture of high-class machine-tools, the chief of which are the vertical boring and turning mills having capacities from 2 feet to 26 feet diameter; these have formed a standard product of the firm from its earliest days, together with the "Pearn, Richards" universal surfacing, boring, milling, drilling and tapping machine, which is made in six sizes capable of taking work from 18 inches up to 6 feet diameter. This useful machine represents the outcome of long and careful development. Other manufactures are slot-drilling and keyway-cutting machines, side planing machines and crank-pin turning machines. The arrangement of the works follows modern requirements and the equipment comprises up-to-date plant throughout. The latter works practically adjoin the former and the companies are associated. The products are air-compressing and sand-blast machinery in the manufacture of which the firm has long specialized. Both works are supplied with castings from a large modern foundry, in which castings up to 40 tons in weight can be produced.
Mersey Tunnel
THE MERSEY TUNNEL, BIRKENHEAD.
Queensway Tunnel
History of Project. — The Tunnel for vehicular traffic connects Liverpool and Birkenhead and forms a link not only between these two towns but also between the general highway systems which are severed at present by the River Mersey. Plans for improving the communications between the two towns and counties have been under consideration for more than three-quarters of a century and bridges as well as tunnels have been proposed. In June 1922, a Committee known as the Mersey Co-ordination Committee, under the Chairmanship of the late Rt. Hon Sir Archibald Salvidge, P.C., K.B.E., instructed Sir Maurice Fitzmaurice, C.M.G., Mr. Basil Mott, C.B., and Mr. John A. Brodie, the City Engineer of Liverpool, to make a report on the provision of a bridge across or a tunnel under the Mersey with a view to improving the facilities for cross-river traffic. After a study of all the elements of this problem, the engineers reached the unanimous conclusion that a tunnel would best meet such requirements.
Acts of Parliament—The Joint Committee. — The plans were made and deposited with Parliament and authority given by the Mersey Tunnel Act of 1925 for the construction of the tunnel and the setting up of a statutory committee to carry out the powers conferred by the Act. The Committee consists of ten members appointed by the Liverpool Corporation and seven by the Birkenhead Corporation with a Chairman and Vice-Chairman appointed by and from the members of the Joint Committee, but not both from the same Corporation. The first Chairman was Sir Archibald Salvidge to whose public-spirited energy the genesis of the project was greatly due. He held office until his death in December 1928. The present Chairman is Sir Thomas White. Further detailed study led to modifications in plan from the original scheme. These were authorized by the Mersey Tunnel Acts of 1927 and 1928 respectively.
Plan of Work and Physical Features. — The tunnel plans are now as follows, beginning at Liverpool and going towards Birkenhead. The through traffic entrance is at Old Haymarket, where the tunnel descends at a gradient of 1 in 30. The dockside entrance is at New Quay, just north of Chapel Street, and the tunnel descends at the same gradient. The two branches come together under Dale Street, near North John Street, and the tunnel continues as a single structure across Castle Street, down Brunswick Street, and under the river. The gradient of 1 in 30 continues to a point 779 feet beyond the Quay wall of George's Parade, Liverpool. The tunnel then rises slowly for 1,670 feet to a point 1,299 feet from the Birkenhead Quay wall, where the gradient again becomes 1 in 30 and the tunnel continues as a single structure to a point in Birkenhead in the block bounded by Canning Street, Bridge Street, and Argyle Street. From this point the two approach tunnels diverge. The through traffic line curves under Hamilton Square, Hamilton Street, and comes to the surface at the junction of Chester Street and Market Place South. The gradient of this approach is 1 in 30, and the entrance is close to the main highway, Chester Street, and at a focal point for the convergence and divergence of the through traffic.
The dockside branch has a ruling gradient of 1 in 30, with 1 in 40 for part of its length, and passes parallel to Cleveland Street to an entrance at Rendel Street, near Corporation Road. The width of the roadway between kerbs, from the Old Haymarket, Liverpool, to Market Place South, Birkenhead, will be 36 feet and enough for four lines of traffic abreast. The width of the roadway on each of the dockside branches will be 19 feet, sufficient for two lines of traffic. The total length from end to end of the through traffic line will be 2.16 miles and of the dockside line 2.08 miles.
The under-river portion of the tunnel, 46 feet 3 inches external diameter and 44 feet internal diameter, will be the largest sub-aqueous tunnel yet constructed. The total length of tunnel will be 2.9 miles. The quantity of excavation will amount to more than one million tons of rock. The tunnel will be lined with cast-iron plates bolted together, to support the ground and to afford a lining which is perfectly watertight. The total weight of iron thus used will be over 75,000 tons. The iron lining will be protected from corrosion by an outside and inside covering of cement grout and concrete.
Contracts for Construction. — The first contract for the work was known as Contract No. 1, and was awarded by the Joint Committee on 8th December 1925, to Messrs. Edmund Nuttall, Sons and Company, of Trafford Park, Manchester. The work was formally inaugurated in December 1925, when H.R.H. Princess Mary turned compressed air into the drills at the working shaft at George's Dock, Liverpool. This contract was for the purpose of driving preliminary tunnels along the line of the future main tunnel in order to explore and prepare the ground prior to the execution of the full-size tunnel work.
On 3rd April 1928, the heading from Liverpool met that from Birkenhead almost exactly under the middle of the river, and the occasion was marked by a ceremony, in which the Chairman of the Mersey Tunnel Joint Committee broke through the wall of rock separating the two headings and through the opening thus made the Lord Mayor of Liverpool (Miss Margaret Beavan) and the Mayor of Birkenhead (Councillor Naylor) greeted one another. The headings met to within an inch both for line and level. Following the completion of the first contract, the Joint Committee awarded to Messrs. Nuttall the contract, known as Contract No. 2, for the enlargement of the preliminary tunnels across the river between George's Dock, Liverpool,and the Morpeth Branch Dock, Birkenhead. Work is now in active progress under this contract, and the full-size tunnel is being constructed from ten different points under the river. Contract No. 3 comprises the construction of the full-size tunnels in Birkenhead. On 14th November 1928, this contract was awarded to Messrs. Sir Robert McAlpine and Sons, of London, who are now at work. Contract No. 4 included the construction of the full-size tunnels at Liverpool. On 20th March 1929, the Joint Committee awarded this contract to Messrs. Nuttall. The work under the latter two contracts is now being started, and there are some 900 men at work, but when work under all the contracts is in full operation this number will be doubled.
It is hoped that the tunnel will be available for use in three years' time. The cost will be £5,222,000, of which one-half will be contributed by the Ministry of Transport and the other half as to one moiety by tolls and as to the other moiety by Liverpool and Birkenhead Corporations.
Dobson and Barlow, Bolton
MESSRS. DOBSON AND BARLOW, KAY STREET, BOLTON.
Dobson and Barlow
The company was founded in 1790 by Isaac Dobson. and Peter Rothwell, a well-known timber merchant and business man in Bolton, the works being situated in a part of the timber yard in Black Horse Street. The first machine produced was the spinning mule invented between 1774 and 1779 by Samuel Crompton, a celebrated native of Bolton. The early machines were constructed chiefly of wood with wrought-iron shafts, and pillions and wheels of cast iron. The activities of the firm have developed no as to embrace the manufacture of all types of spinning and preparing machinery. It is of interest to recall that in 1831 one of the earliest known strikes took place in these works. In 1846 the firm removed to the present site in Kay Street, then on the outskirts of the town, and in 1850 the name of the firm was changed to that of Messrs. Dobson and Barlow, and the centenary of the establishment of the business was celebrated in 1890. By 1906 the company was obliged to find a new site to provide for the extensions in the factory, and forty acres of land at Bradley Fold, four miles from Bolton, were purchased; of this area twenty acres are now covered by buildings. The company produce a complete range of machines for ginning, opening, preparing, spinning, winding and doubling cotton and other fibres, and build complete installations for the manufacture of rayon (artificial silk) yarns by the viscose process. The Kay Street works, which contain the registered offices, have a floor space of nine acres; some of the buildings are old, but these have been modernized and no effort is spared to keep the equipment abreast of the times. At Bradley Fold the single-story buildings are new and the lay-out is of the most modern type. All the departments are electrically driven. Special attention has been given to inter-departmental communication. Besides the usual engineering shops, the firm possesses a well-equipped laboratory for testing raw materials, all of which have to satisfy exacting tests before being passed into the shops. Cotton-spinning machinery has not to prodaace a standard article, but has to be capable of producing a range of counts with fairly wide variations and so requires to be flexible and adaptable. It also deals with a fine and delicate fibre. These requirements call for accuracy in all stages of manufacture which is ensured by adherence to carefully considered tables of limits, fits and tolerances. The firm therefore maintains a comprehensive gauge department including a testing section for ensuring the accuracy of the standards. The section is equipped with the finest apparatus obtainable, whilst the machine room of the department contains a collection of modern precision tools.
Charles Walmsley and Company, Bury
MESSRS. CHARLES WALMSLEY AND COMPANY, ATLAS WORKS, BURY.
Charles Walmsley and Co
The firm specialize in the manufacture of pulp and paper-making machinery and of auxiliary equipment of all descriptions for pulp and paper mills, and undertake complete installations of machinery and plant for such mills. The works comprise pattern shops, iron and non-ferrous metals foundries, machine and erecting shops, most of which are specially arranged and equipped for dealing with the machinery required in the paper-making industry.
Brookhirst Switchgear, Chester
MESSRS. BROOKHIRST SWITCHGEAR, CHESTER.
Brookhirst Switchgear
The works are situated on the outskirts of the city but within easy reach of the two main stations. The manufacture of switch-gear was first commenced in 1898 under the title of Brookhirst and Company with a staff of twelve. The site of the works was then quite near the Northgate, but in 1908 the firm had expanded and it became necessary to build the present modern works at Newry Park. The works have been extended on a number of occasions, and now accommodate between seven hundred and eight hundred employees. They are divided into two portions; one is devoted to the manufacture of the company's standard range of direct-current control gear, and the other is given up to the manufacture of alternating-current control gear, and to a range of "small power" control gear, for motors up to about 10 h.p. By the rigid standardization of design, and the use of jigs and tools, complete interchangeability of parts has been assured. As a result, it is possible to make use of semi-skilled labour on many of the assembly operations, thus enabling a comprehensive form of motor control panel to be put upon the market at a reasonable price.
In the main assembly shop a system obtains of progressive assembly whereby the slate panels are hung on racks and move continually forward, receiving various additions on their way until they arrive at a point where they are fitted into the steel boxes which are a well-known feature of the Brookhirst design of control gear. A progressive system is also employed in the large and well-equipped box-shop for the manufacture of the switch-gear cases. The cases move continually forward from the flat steel sheet at one end of the shop to the finished product, fitted with doors, at the other end, ready for entering the paint shop. This is a point of some importance in view of the heavy nature of the material to be handled.
Of particular interest is the "special switch-gear" section in which are manufactured the transformer regulators, synchronous motor starters, and various other special designs with which the firm's name has been associated during the last few years. In view of the increase in business further extensions of offices and works have recently been found necessary.
Hydraulic Engineering Co
THE HYDRAULIC ENGINEERING COMPANY, CHESTER.
Hydraulic Engineering Co
The original business was started over a century ago, and in 1805 was known as the Flookersbrook Foundry, under the style of Cole, Whittle and Company, until 1832, when Mr. John Johnson became sole partner. In 1844 the business passed to his sons Edward and Bryan Johnson, and during the partnership of the two brothers the engineering side of the business was developed, and largely took the place of the purely founder's work.
In 1869, Edward Johnson having retired, the late Mr. E. B. Ellington (President of the Institution, 1911-12) joined Mr. Bryan Johnson in partnership, and the business was continued under the style of Johnson and Ellington until 1874, when it was made a limited liability company and acquired its present title.
The works cover an area of between two and three acres. The main portion lies between Charles Street and Egerton Street, with long frontages to both. There is also an extensive yard at the top of Charles Street with frontage to the Shropshire Union Canal. The main entrance to the works and offices is on the east side of Charles Street. This block comprises the general offices, drawing office, stores, turning and fitting shop, erecting and machine shops, smithy, brass foundry, pattern shop, iron foundry, etc., and a lofty covered steel gantry. On the opposite side of Charles Street is the plating shop.
The turning shop, with a roof in three spans, is 120 feet long by 85 feet wide with galleries on each side. On the galleries are the smaller lathes, screwing machines and other machine-tools used in the finishing of brass, steel and ironwork. The centre bay of the shop is devoted to the larger machine-tools, and is served by a 17-ton electrically driven traveller running the whole lengths of the shop, and having a span of 41 feet with a height of lift of about 18 feet above ground-floor level. The ground-floor space under the landing on one side is devoted to machine-tools.
Leading out of the turning and fitting shop are the erecting and machine shops. The erecting shop measures about 92 feet long by 49 feet wide, and is served by a 17-ton electrically driven travelling crane having a span of 46 feet, the height of rails above floor level being 32 feet. The original erecting shop was parallel to and stands between the erecting shop and machine shop, and is 98 feet long by 29 feet wide. It is served by a 15-ton rope-driven traveller having a span of 26 feet, the height from floor to rail level being 21 feet, and is now used as an extra machine shop. Leading out of the old erecting shop and on one side of it is a smaller shop 55 feet long by 30 feet wide which is used for fitting, and is served by a 5-ton electrically driven travelling crane. Adjoining the old erecting shop there is another machine shop which measures about 70 feet by 53 feet which is served by a 10-ton electrically driven travelling crane.
The iron foundry is 176 feet long by 55 feet wide. It is served by two 10-ton hydraulic jib cranes and a 10-ton electrically driven traveller, in addition to some smaller hydraulic wall cranes. A Beardsley-Piper portable sand slinger has recently been added to the foundry equipment. In recent years new plant has been installed for handling more rapidly the coke and iron for the foundry. A direct-acting hydraulic lift and suspended hydraulic hoist are used in conjunction with overhead runways, so that handling of the material is reduced to a minimum. The brass foundry which adjoins the dressing shop is about 42 feet by 19 feet. There are four crucible furnaces and two drying stoves. The smith's shop has a floor area of about 4,200 sq. ft. and is equipped with ten fixed hearths and two pneumatic hammers. The pattern shop, an irregular building, has a floor space of about 2,100 sq. ft. and a gallery giving an additional 800 sq. ft. The plating shop which stands on the west side of Charles Street is mainly devoted to the manufacture of structural work. Amongst the tools and appliances in this shop there are hydraulic punching and shearing machines, two portable hydraulic riveters with hydraulic pumps and an accumulator, and a 150-ton press.
Hydraulic power at 800 lb. per sq. in. is available from two electrically driven three-throw pumps working in conjunction with an accumulator. These supply power for working the cranes and other plant in the foundry, punching and shearing machines in the plating shop, intensifiers used for testing purposes, and the lift giving access to the turning shop landing. The system is also employed for testing the hydraulic engines and capstans manufactured in the works, all of which are run under pressure before dispatch. Electric current for both lighting and power is supplied by the Chester Corporation.
The company's specialities in design and manufacture are hydraulic power generating plant for all purposes and the hydraulic appliances usually worked off these plants, such as coal hoists, fixed and movable cranes, hydraulic engines, capstans, machinery for operating swing and bascule bridges, dock gates and sluices, wagon hoists and other lifts, presses for all purposes, injector fire hydrants, etc. The company are the sole licensees for the manufacture of the "Mangnall-Irving Thrust-Borer." These machines bore holes under the ground so that electric cables, gas and water pipes can be laid in them without disturbing the surface.
LMSR Works, Crewe
LONDON, MIDLAND AND SCOTTISH RAILWAY COMPANY, LOCOMOTIVE WORKS, CREWE.
Crewe Works
These works provide for the manufacture and maintenance of locomotives of the Western Division (formerly the London and North Western Railway). They were originally constructed in 1843 and have recently been thoroughly reorganized. The principal items of interest are: the new boiler-building department capable of an output of seven boilers weekly; the new steel works comprising two 45-ton acid and two 75-ton basic steel furnaces; the forge and rolling mills for the production of tyres, axles and forgings; the heavy machine shop, which contains a large number of modern machines for the production of locomotive cylinders, frames and other heavy components; and the new erecting shop which is capable of accommodating sixty-six locomotives and is equipped with the most modern machinery. In the last shop all engines are repaired under a progressive system, whereby the engine is moved from stage to stage as the various parts of the work are completed. A section of this shop is devoted to the building of new engines, its capacity being approximately one hundred locomotives annually.
LNER Dukinfield Carriage and Wagon Works
THE LONDON AND NORTH EASTERN RAILWAY COMPANY, CARRIAGE AND WAGON WORKS, DUKINFIELD.
Dukinfield Works
The works, which are situated about six miles east of Manchester on the L.N.E.R. main line to Marylebone, are the main shops for carriages and wagon manufacture and maintenance on the Great Central Section of the group. The site covers thirty acres, of which twelve are occupied by the shops. The shops consist of a main block 700 feet long by 540 feet wide, and a smaller block forming the paint and lifting shops, 625 feet by 120 feet to the east. In addition, there are the general offices, mess room, timber-drying shed, timber yard and power house. The buildings were completed in 1909.
About 1,500 men are employed. All the electric power used is generated in the power house, which measures 145 feet by 60 feet, the capacity being 1,200 kw. at 240 volts, direct-current. The roads in the main block of buildings are served by an electric traverser at both the west end and the east end. The traverser at the east end forms a connexion between the main block and the lifting and paint shop.
The main building is divided into a number of bays as follows. The southernmost bay contains the wheelwrights', cell charging, electric lighting equipment repair, electric fitting and finishing workshops. The next bay is the underframe shop in which new frames are built and frames repaired. It has a 5-ton overhead electric crane and the tool equipment consists of a bending and straightening machine, a cold saw, a notching machine, multiple drills, a double-headed milling machine, hydraulic riveters, etc. The bay following contains the auxiliary paint shop and stores, trimming department, finishing shop, and general stores. The adjacent bay is the finishing shop, part being used by the polishers. The equipment includes a triple-drum sander, circular saws, band saw, and pneumatic presses.
The next two bays form the saw-mill and the building shop in which carriages are built on the progressive system, which may be described briefly as follows. The various components such as bottoms, sides, ends and partitions, doors, etc., forming a carriage are assembled separately. The underframe complete with wheels is brought into the first position at the end of the shop, where it is fitted with the complete floor; the frame, now fitted with the complete floor, is moved to the second position, where the sides or quarters, partitions, ends, cant rails and roof sticks are assembled and secured. The coach is then moved to the third position between high staging where the roof boards are fixed, the roofing canvas stretched on, and the cornices fitted. The roof is completed by painting, after which the coach is moved into its fourth position between low staging, where the doors are fitted in place and finished. The coach is then moved finally to a position where the interior fittings are mounted and the outside mouldings applied, and is ready for painting.
The last two bays are set aside for repair work. The wheel and iron machine shop, 150 feet by 325 feet, is equipped with a 5-ton overhead electric crane, and is provided with wheel and axle lathes, presses, etc. Wheel re-tyring is done in the centre bay. A large Armstrong-Whitworth wheel-turning and grinding machine is installed in this shop. The forge contains a battery of six drop hammers of from 25 cwt. to 7 cwt., one 7 cwt. steam-hammer, two large arch-form hammers of 50 cwt., and 15 cwt. capacity, and three 70- to 80-ton hydraulic presses. The carriage lifting shop, 625 feet long and 60 feet wide, is equipped with two 20-ton overhead electric cranes. Coaches are brought in on the centre road and lifted on to stands in the side roads, where the underframes are examined and any repairs found necessary are carried out.
LMSR Horwich Works
LONDON, MIDLAND AND SCOTTISH RAILWAY COMPANY LOCOMOTIVE WORKS, NORWICH.
Horwich Works
The works were erected in 1887 for the purpose of building and repairing the locomotive stock of the Lancashire and Yorkshire Railway Company, and for carrying out the mechanical, electrical, and hydraulic engineering works of that company. In January 1922, this company was merged into the London and North Western Railway Company, and later, in January 1923, formed part of the group now known as the London, Midland and Scottish Railway Company.
The works deal with locomotive stock of about 1,700 engines and employ about 3,500 men. For several years past locomotives have been repaired at Horwich on the progressive system through the processes of stripping, frame repairs, and final assembling. Engines enter the shop by means of a traverser and leave again by a second traverser. These means are found to reduce to a minimum the number of days on which engines remain in the shops for repair. The land enclosed within the works boundary comprises 116 acres; the covered area of the workshops is seventeen acres. The buildings are as follows: offices, general stores, boiler shop, boiler shop smithy, forge, steel foundry, iron and chair foundries, smithy, machine shop, boiler-house, tin and tube shops, brass foundry, motor millwrights', joiners' and pattern makers', erecting, paint and testing shops and chain smithy. The cafe on Chorley New Road provides meals for about 200 of the staff each day, and in the dining rooms at Gooch Street accommodation is provided for about 1,000 men who bring their own food, which is cooked or heated by the attendants in charge of the rooms.
The Railway Mechanics' Institute and Technical School was opened in December 1888, and the school started with four science classes, with an average weekly attendance of ninety students. To-day there are classes provided for over twenty subjects with over 500 students. In the Institute there is a large hall having seating capacity for 900 persons, a gymnasium which caters both for males and females; reading, games and smoke rooms; and a lending library with over 13,000 volumes, with a daily issue of about 150, in addition to which there is a reference library consisting of over 700 volumes. The Institute has a membership of nearly 3,000. The recreation ground is governed by the Institute Committee. Connected with the Institute are the cricket, football, tennis, bowls and harriers clubs; photographic, literary and orchestral societies; and the brass band. The company have also provided a hospital in Brunel Street for the treatment of accidents which occur in the works.
Joseph Adamson and Company, Hyde
MESSRS. JOSEPH ADAMSON AND COMPANY, HYDE.
Joseph Adamson and Co
These works were established in 1874 by the late Mr. Joseph Adamson in partnership with Mr. Henry Booth, who retired in 1887, and are carried on to-day by Mr. Daniel Adamson, the eldest son of the founder of the business, assisted by his two sons Mr. G. R. Adamson and Mr. J. Adamson. Originally the activities of the firm were devoted to the manufacture of steam-boilers, but the scope of the business was enlarged, first in 1883 by the erection of a new shop to specialize in hydraulic press work, and secondly in 1894 by the construction of one of the first three-motor electric cranes to be built in this country, the success of which resulted in the placing of further orders and the establishment of the firm as crane-makers.
The works proper are divided into nine bays. Nos. 1 and 2 contain the hydraulic presses and their dies, of which there are to-day upwards of 1,100 tons ranging in size from 2 feet to 12 ft. 6 in. diameter. The largest of the three flanging presses will admit plates 13 ft. 4 in. diameter in the flat. No. 3 bay is the smithy which contains an overhung press for sectional flanging, as well as the machinery for fire welding and flanging boiler flues, bending and welding angle rings, etc. A part of this bay is now given up to welding by the electric and oxy-acetylene processes. No. 4 bay is the plate shop, containing plate-edge planer, bending rolls, multispindle horizontal and vertical drilling machines, two large vertical boring and turning mills, and heavy-duty radial drills. No. 5 bay contains the pattern shop, and the blacksmiths' shop; the far end of the latter is used as a stores for bar iron and steel sections. Being the oldest part of the works it has recently come under consideration for enlargement and extension, and the result may be seen in the raised roof and crane gantry. No. 6 bay is the boiler shop; the riveting tower 60 feet high contains three fixed riveters and two electric hoists. Nos. 7 and 8 bays, with the gallery over the latter, form the crane erecting and machine and electric shops. A feature of the former is the testing pit over which all cranes are erected for testing under any desired load or overload up to 100 tons.
Adjacent to the main building at the press-shop end of the works lie the boiler-house and engine-house containing the hydraulic pumps, air-compressors and high-speed engines for electric power supply. Electric drive has been adopted throughout the works.
The works are exceptionally well provided with overhead cranes of the firm's own manufacture, and the railway sidings pass across the end of each of the main bays.
Ashton Brothers and Company
MESSRS. ASHTON BROTHERS AND COMPANY, CARRFIELD MILLS, HYDE.
Ashton Brothers and Co
The exact date of the foundation of the firm is not known, but Thomas and Samuel Ashton were conducting a cotton factory at Gee Cross, Hyde, between 1780 and 1790. Their factory was destroyed by fire but the business was recommenced in 1800. In 1854 the merchandizing in Manchester and the factory at Hyde became two separate businesses, the latter under the style of Ashton Brothers and Company. In 1888 the firm was converted into a private limited liability company and in 1899 into a public limited liability company, and to-day employs over 3,000 workpeople. The factory has nearly 200,000 ring and mule spindles, nearly 5,000 looms, and is capable of an average production of a million yards of material weekly.
After the raw cotton has passed through its preliminary operations ("slubbing," etc.), the yarn is run on to "cops" or bobbins in preparation for weaving into cloth on the loom. The various operations of weaving are as follows: the warp yarn from the bobbins is wound on to flanged bobbins, being joined or pieced in a continuous thread up to 30,000 yards long (in the case of coloured yarns the thread may be wound into hanks or may be dyed on the beam, both methods being employed in these mills); "warping," in which the threads (as many as 500) are laid side by side on a "warper's beam," the threads from the bobbins in a creel behind the machine passing through an interstice in the comb; in the taping machine the warp threads are passed through boiling size (flour and tallow) and are finally rewound on to "weaver's beams "; the last process before weaving is that of "drawing in" to allow of interweaving the warp and weft on the loom for the production of ornamentation of the fabric; weaving, in which a shuttle containing a cop of "weft" travels backwards and forwards across the loom between the warp threads which are being raised and lowered in a definite order by "healds," and as the interchanges of warp and weft or "picks" take place the finished cloth is drawn forward to be wound on a roller in front of the loom.
With the firm's Throstle Bank and Wharf Shed Mills the total area covered by the factories is twenty-five acres. Warehouses, offices, canteens, recreation grounds, gymnasia, etc., account for additional space. The social side of the workers is especially well considered: there are social clubs for men and women, and sports, dramatic, horticultural, etc., societies. Once formed, the various groups generally become self-supporting and compete successfully with neighbouring workers in league and tournament.
Partington Steel and Iron Company, Irlam
THE PARTINGTON STEEL AND IRON COMPANY, IRLAM.
Partington Steel and Iron Co
Coke Ovens. — The plant at present comprises a battery of sixty two coke-ovens, a coal-washing, and by-product plant, capable of dealing with 1,900 tons of coke per week. Coal, in the form of slack, is automatically handled from the truck to the coal washery, and after washing, is elevated to storage bunkers, whence it is taken to the ovens for coking. The ovens are fed by a charging machine and after the process is completed, the coke is ejected by an electric ram (being quenched during the operation) on to a sloping hearth. It is then directly loaded into special skips, weighed and recorded, prior to being conveyed to the blast-furnaces. The surplus gas produced is used for firing boilers and heating the active metal mixer in the open-hearth steel plant. The by-products consist of sulphate of ammonia; whizzed naphthalene salts; heavy naphtha; crude tar; refined tar; pitch; crude benzol; and motor benzol ("Partene").
Blast-Furnaces. - The blast-furnace plant consists of six furnaces, equipped with the latest labour-saving devices, each furnace being capable of an output upwards of 1,500 tons of iron per week. As these go out of commission they will be replaced by furnaces of considerably larger capacity. Storage bunkers are provided for the reception of the raw material prior to being charged into the furnaces by means of a mechanical hoist, which elevates the charge in 5-ton skips. The waste gas from the furnaces is used in a variety of ways, namely firing boilers for steam-raising purposes; driving the gas-engines in the main power house; heating the Cowper stoves for supplying hot air to the furnaces.
Steel Plant. — The melting shop is at present capable of producing 3,600 tons of steel per week by means of Siemens open-hearth regenerative furnaces. Improvements are now being effected which will considerably increase the steel ingot output. The molten metal is taken from the blast-furnaces by means of hot metal ladles to the active metal mixer, whence the silicon and sulphur are reduced. The mixer has a capacity of 250 tons. The molten metal is then transferred from the mixer to the open-hearth furnace, where it is converted into steel of the requisite qualities, which at the moment range in carbon content from 0.05 to 1.25 per cent.
Rolling Mills. — The ingots for the rolling mills are taken from the melting shop to the soaking pits, preparatory to cogging. The soaking pits are four in number of modern design, with sliding roof doors, and have a capacity for ninety-six ingots. The cogging mill is 40 inches between centres, electrically driven by an Ilgner set; the normal rating of the motor is 5,000 h.p., but it is capable of withstanding peak loads up to 16,000 h.p. This mill is capable of rolling 5,500 tons of ingots per week, and the resulting blooms are dealt with in the large and small mills. The mill also contains a bloom shears, cutting 16-inch by 13-inch hot blooms. The roughing and finishing mills are 28 inches between centres. The material is conveyed from the cogging to the roughing, and from the roughing to the finishing mills by means of live rollers. Two 5-ft. pendulum hot saws are provided, and hot finishing and rail banks. The small mill contains one stand with a 20-inch housing, and three stands with 18-inch housings, capable of rolling light rails and small general sections. The mills will be able to roll the full range of British Standard Sections applicable to a 28-inch mill when the new six-chamber wash-heating furnace at present under construction is completed.
Foundry. — This shop, 472 feet long and 100 feet wide, is divided longitudinally into two bays, and is equipped with four overhead travelling cranes of 2-, 5-, 10-, and 15-tons capacity respectively. There are three cupolas, one of 10 tons, one of 5 tons, and one of 30 cwt. capacity. The equipment also includes three Tropenas steel converters, one of 2 tons and two of 1 ton capacity each. The shop is capable of dealing with steel castings up to 3 tons in weight, and iron castings up to 8 tons, and the weekly capacity is 110 tons of iron castings, 10 tons of steel castings, and 3½ tons of brass and copper castings.
Power House. — The power used in the various departments is supplied from the power house, situated centrally in the works, and contains one 3,000 kw. gas-engine generator, six 1,000 kw. gas-engine generators, two 1,000 kw. turbo-generators, four turbo-blowers, and three gas-engine blowers. The efficiency of the plant will shortly be raised by the provision of waste-heat boilers.
General. — Amongst other activities of the firm mention should be made of the utilization of the by-products of the steel works; preparation of tarred bituminous slag for road-making; the manufacture of concrete kerbs, flags and other commodities for use in road and building work. The company have an extensive department dealing with road construction and own a limestone quarry at Bodfari, North Wales, whence certain of the material for roads is derived.
Royles
MESSRS. ROYLES, IRLAM.
Royles
The business was established in Manchester about fifty years ago and has since been engaged in the manufacture of steam specialities, notably steam-traps, reducing valves and similar appliances. During recent years it has extended its operations by the introduction of Row's patent tube. The application of this to feed-water heaters, calorifiers, evaporators and condensing apparatus necessitated the erection of entirely new works and led to the removal of the business from the city to the present site at Irlam. The works occupy an area of about five acres adjoining Irlam station on the Cheshire Lines railway and have been laid out on modern lines for the rapid and economical production of high-class work. The shops comprise an iron and a brass foundry, pattern shop, machine shop with bays assigned to brass finishers' work and to fitting, and a coppersmiths' shop.
Leyland Motors, Leyland and Chorley
MESSRS. LEYLAND MOTORS, LEYLAND AND CHORLEY.
Leyland Motors
The company has been engaged in the manufacture of commercial vehicles since 1895, though its history can be traced to a blacksmith's shop as early as 1885, when Mr. James Sumner conceived the idea of utilizing steam-power for driving wagons. Though his first experiments were carried out with considerable success, it was not until after the passing of the Locomotives on Highways Act of 1896 that his vehicles attracted the attention of Mr. Henry Spurrier, the father of the present managing director, who was sufficiently interested to form a company styled the Lancashire Steam Motor Company, in 1896. The partners of this company were Mr. Henry Spurrier, sen., Mr. Henry Spurrier, present managing director of Messrs. Leyland Motors, Mr. Arthur Spurrier, and Mr. James Sumner. This company, the name of which was afterwards changed to Messrs. Leyland Motors, was formed in 1907 for the manufacture of steam-wagons exclusively. In 1897 the first steam-wagon was put on the road and secured the first prize at the trials organized by the Royal Agricultural Society. The company repeated this success in the following year, as well as obtaining a £100 prize as a result of the famous trials held by the Liverpool Self-Propelled-Traffic Association in 1898. Similar successes followed, and in 1902 the Herbert Street works were found to be inadequate, and the Lancashire Steam Motor Company was, therefore, registered as a private company, land was purchased, and building commenced on the present site.
Up to 1904 its activities had been confined to the manufacture of steam-wagons, and although business in this type of vehicle was continuously expanding, the company did not overlook the possibilities of the petrol internal-combustion engine, and as early as 1904 the design of a petrol vehicle was completed, and an experimental machine came out of the Herbert Street works at the close of that year. Sixteen petrol vehicles were manufactured in 1905, and from 1906 to 1913, inclusive, the company supplied a total of 1,332 vehicles, of which 1,032 were petrol-driven. A significant mark of Government approval of the company's early petrol designs was that Leyland machines were the only two vehicles awarded the Certificate of Success in the first War Office Subsidy Trials in 1912. The Leyland was, therefore, the first vehicle to be subsidized, a fact which led to over 6,000 Leyland vehicles being used during the War. From 1914 onwards, the company continued to expand rapidly, and in the two years following the outbreak of war, the head offices were completed, Chorley Works opened, and further land in Leyland purchased for the erection of the company's steel foundry and coach-building shops, until the company's Lancashire properties extended over 160 acres.
The present-day Leyland products are petrol-driven commercial vehicles of all types, including passenger vehicles, goods vehicles and fire-engines. The latest passenger models consist of the "Lion" and "Tiger" single-deck buses, the latter being a six-cylinder model, the six-cylinder "Lioness" coach, and the six-cylinder "Titan" 51-seat double-deck vehicle with patented body construction. The goods models range from 2½ tons to 10 tons capacity. These vehicles are all manufactured at Leyland, though certain of the components of the heavier goods models are made at the Chorley branch works, where also all fire-engine products are manufactured.
The main works are concentrated around the original site and consist of two blocks (North and South Works) divided by the principal street through the town. The Farington Steel Foundry is situated about a mile from the main works. The North Works are devoted to the manufacture of the chassis. They consist of four principal machine shops, erecting shops for the assembly of chassis, engines, gear-boxes and other units, finished and rough stores, case-hardening departments, smithy, tool-room, etc. In the latter department, gauge-measuring machines, one of which is capable of measuring to one hundred-thousandth part of an inch, have recently been installed. Engine testing is carried out in the engine erecting shop on a battery of electrical test benches of a very modern type. The South Works buildings are used primarily for coachwork and consist of timber-drying kilns and storage sheds, saw-mill, sheet-metal department, upholstery department, body erection shops, paint, varnishing and cellulose rooms, and finishing shops. New buildings for the assembly of double-deck bodies and for research and scientific work have recently been added. The non-ferrous metals foundry is also located in the South Works, and is equipped for the production of sand and die castings and centrifugally cast worm-wheels. The steel foundry is situated about a mile from the main works and has a floor area of about 10,000 sq. yards. It is divided into two distinct sections for the production of steel and iron castings. The steel foundry has a capacity of 130 tons of liquid steel per week, and the iron foundry has a capacity about half this amount. Two electric furnaces of 4 and 3 tons capacity respectively are used, and are supplied with energy from the firm's power plant, which also supplies a large amount of lighting for the village of Leyland. Attached to the foundry is a machine shop where castings are machined so as to enable cylinders, axle castings, and similar parts to be dispatched to the main store ready for assembly.
One of the features of the organization is the institution of an independent service stores, which is established in a separate building near the South Works. This store is open day and night and carries a maximum and minimum stock of parts for all types of vehicles. It has its own dispatch department and transport vehicles. The company's employees obtain their meals, cooked in electric and gas cookers, in a canteen which will seat approximately 2,000 men. The ground floor of the building is allocated to the service department for the storage and dispatch of spares.
The facilities for recreation are numerous. Extensive grounds for cricket, football, hockey, tennis, and bowling have been laid out in close proximity to the works, the respective clubs being under control of the employees.
Vulcan Foundry Locomotive Works, Newton-le-Willows
THE VULCAN FOUNDRY LOCOMOTIVE WORKS, NEWTON-LE-WILLOWS.
Vulcan Foundry
The early associations of this establishment are linked with some of the most prominent names connected with the history of engineering in Great Britain, and Charles Tayleur, the founder of the works, had with him at one time or another, either as partners or occupants of responsible positions in the management of the concern, such men as Robert Stephenson, who withdrew from partnership on his appointment as engineer-in-chief of the London and Birmingham Railway, and William Kirtley, who subsequently became locomotive superintendent of the Midland Railway, whilst later H. Dubs, founder of the locomotive works of that name in Glasgow, acted as works manager. In 1864, when the concern was turned into a limited liability company, Mr. W. F. Gooch, brother of Sir Daniel Gooch, became general manager, being succeeded in 1892 by Mr. W. Collingwood — subsequently Sir William Collingwood, K.B.E., who was managing director until shortly before his death in November 1928. Mr. R. P. Richards, C.B.E., held the position of General Manager from 1917 to 1923, when he joined the Board of Directors and Mr. F. S. Whalley the present General Manager was appointed.
Operations connected with the building of Vulcan locomotives commenced in the year 1830; and Mr. Hargreaves, of Bolton, received delivery in 1833 of the first two engines built at the works, i.e., No. 1 "Tayleur" and No. 2 "Stephenson." These locomotives were four-wheeled engines with, inside cylinders 11 inches diameter by 16 inches stroke, and wheels 4 ft. 8 in. diameter. In the same year two of the earliest locomotives to be imported into America from this country were constructed at the works, Nos. 4 and 5 on the makers' list, and named "Fire Fly" and "Red Rover" respectively. These were bogie engines with single driving wheels, and they ran for many years on the Camden and Woodbury Railroad, U.S.A. Later, in 1852, the Vulcan Locomotive Company received orders for a number of passenger and goods locomotives for the East Indian Railway, and in 1872 they had the distinction of supplying the first locomotive engine to run in Japan. Apart, therefore, from other interesting historical associations connected with the establishment, it played an important part, as pioneer, in the development of locomotive engineering in many parts of the world. Neither does the company depend entirely for its reputation as an engineering concern on the success which has been achieved in the building of locomotives, although that was the function for which the works were primarily established, and in which they have been for many years past solely engaged.
In 1847 Mr. George Samuel Sanderson entered into partnership with Messrs. Charles and Edward Tayleur, and the Bank Quay Foundry was started as a branch of the Vulcan Works for gun, shot, and shell making, and for the manufacture of heavy castings and shipbuilding. The first iron sea-going ship was built at those works, the "Tayleur" a tea clipper. Subsequently further vessels of a similar description were built, and another work of distinction with which the place was identified was the construction of the Conway and Britannia Bridges. All the cast-iron portions, including the stiffening put into the tubes to take the lifting stresses and the expansion work, were produced there. The big hydraulic presses employed in the erection of the Britannia Bridge over the Menai Straits were made at the Bank Quay Foundry, and for those a diploma was awarded at the Exhibition of 1851. The Bank Quay Foundry was closed about 1854, at which time Mr. Edward Tayleur seas the only remaining partner.
The works at present enclose an area of about forty-nine acres, of which thirteen-and-a-half are covered by buildings. They are built on freehold land owned by the company, and are favourably situated for railway facilities, a short siding connecting the shops with the L.M.S. Railway. The company also own some thirty-seven acres of land adjoining, which is available when required for extension. The establishment, during the past thirty years, has been almost entirely rebuilt, and is now equipped with modern plant for manufacturing locomotives of the highest class and for all parts of the world. The handling of material from the time it enters the works until built into the finished engine is conducted on an organized principle, the result of which is seen in the expedition with which work is completed.
Oldham Power Station, Slacks Valley
OLDHAM CORPORATION ELECTRIC POWER STATION, SLACKS VALLEY.
Oldham Power Station
The station is built on land adjoining the main line of the L.M.S. Railway from Manchester to Yorkshire on the west, and the Rochdale Canal on the east. The entrance to the works is on the new arterial road, Manchester to Chadderton, etc. The ground on which the station is built offered somewhat difficult problems of construction. The top surface was a layer of peat with plastic clay and sand below and necessitated the use of a large number of concrete piles for both the main building and the water-cooling towers. The area of the site is over thirty-four acres. The present generating capacity of the station is 37,000 kw., and there is ample space available to extend this to a capacity of 150,000 kw.
Directly opposite, on the other side of the canal, the Sewage Works of the Corporation are situated, and it is intended to obtain the necessary make-up water for the cooling tower evaporation from filtered sewage effluent.
Coal can be delivered by rail or canal, the wagons being shunted by means of a fireless locomotive, and the coal unloaded by means of two ram tippers. The coal is emptied into a bunker, whence it is carried by means of an endless chain gravity bucket conveyer, capable of dealing with 80 tons of coal per hour, to the main storage bunkers in the boiler-house, which have a total capacity of 900 tons. The coal-handling gear was supplied by Messrs. Babcock and Wilcox. The ashes from the boiler furnaces are discharged into hoppers in the basement, and are removed by motor wagons and tipped on the site, the contour of which lends itself to this method of disposal.
The boiler equipment consists of eight Babcock and Wilcox cross-tube marine type boilers generating steam at 295 lb. per sq. in. gauge, each boiler having a normal steaming capacity of 50,000 lb. per hour. The boilers are fitted with superheaters giving a total temperature of 700° F. and with automatic travelling chain-grate stokers, together with automatic travelling coal chutes. Each boiler is also provided with a Green's vertical economizer erected immediately behind the boiler and having an effective heating surface of 4,500 sq. ft. The flue gases leaving the economizers either pass direct, or through an induced-draught fan, into the steel chimneys, 80 feet high. To obtain as much natural light as possible, and for easy access, the fans and motors have been placed underneath the economizers at the back of the boilers at firing floor level.
The boiler feed-pumps are placed in the pump-house which lies between the boiler-house and the turbine-house. Six pumps are provided, four electrically driven and two steam driven, and together they have a capacity of 95,000 gallons per hour. Four large condensate and make-up water tanks are erected in the upper portion of the pump-house, so that water flows by gravity to the feed-pumps. A water-softening plant for boiler make-up is also provided. The condensing water passes through three duplex water-cooling towers having a total capacity of 1,800,000 gallons per hour. In addition, sufficient condensing water for one 12,500 kw. set can be obtained from the canal. It is intended to obtain the make-up water for the cooling tower evaporation from filtered sewage effluent from the Corporation's sewage works on the other side of the canal.
The generating plant installed in the turbine-house at present comprises three 3,000 r.p.m., 12,500 kw., two-cylinder, turbo-alternators, equipped with surface condensers, two-stage feed-water heaters, air-coolers, etc., supplied by the Metropolitan-Vickers Electrical Company. The switch and control rooms, on the east side of the turbine-house, are arranged so that the operator in the control room has a complete view of the turbine-house, which obviates the necessity of installing signalling apparatus. The switch-room is equipped with Ferguson-Pailin, extra high-pressure, metal-clad switch-gear, remote-controlled, and fully interlocked so that it can be correctly handled with perfect safety. The large type unit has two distinct triple-pole oil circuit-breakers (breaking capacity 1,500,000 kva.), one for each set of bus-bars. Each switch is complete with the necessary instrument, potential transformers, etc., and is motor-operated. The smaller unit controlling the distribution feeders has one triple-pole oil circuit-breaker (breaking capacity 750,000 kva.), which, by transfer mechanism, can be coupled to either set of bus-bars as desired and is solenoid-operated. The control room is equipped with desk type panels for the generators, group feeders and group works transformers. A flat back panel is provided for the distribution feeders, above which an automatic indicating line diagram is fixed, showing at any moment the position of the main and auxiliary switches.
Manchester Gas Works, Partington
MANCHESTER CORPORATION GAS WORKS, PARTINGTON.
Manchester Gas Works
Gas lighting was first introduced into Manchester in 1807, and in 1844 the control of the gas undertaking passed into the hands of the Corporation, five years after the City had obtained its Charter. The Partington Works were officially inaugurated on 8th May 1929. It is of interest to note that since the manufacture of gas has been in the hands of the municipality till 31st March 1921, nearly three-and-a-half million pounds were applied in lieu or in aid of the City rates. The gas department has four stations: Rochdale Road, 9 acres; Bradford Road, 51 acres; Droylsden, 4 acres; and Partington, 174 acres. The producing power of Partington is at present only eight million cubic feet per day with one unit, with a storage capacity of five million cubic feet. The choice of the site at Partington on both sides of the Cheshire Lines Railway was rendered necessary by the steady growth of the demand for gas, by the fact that it was well outside the City boundaries, and by its altitude which is such that gas will generally pass to the areas to be supplied with but slight mechanical assistance.
The coal store is in the form of a reinforced concrete structure arranged below the railway sidings; this arrangement was possible as the general level of the site is some 22 feet below the level of the railway. The store is 440 feet long by 150 feet wide and has a capacity of 33,000 tons of coal with provision for an extension to hold 18,000 tons. The whole of the incoming coal passes over one or other of the two 40-ton weighbridges. Coal from the railway wagons is transferred into a steel receiving hopper from which it passes through adjustable reciprocating feeders into the mouth of either of the two double-roll West coal breakers. From the breakers the coal is elevated in the two lip-bucket conveyers and distributed in the overhead coal-storage bunkers arranged above the retort benches.
The carbonizing plant is constructed in two sections, one consisting of Glover-West vertical retorts and the other of horizontal retorts supplied by Messrs. Drakes of Halifax and comprising eighteen beds (in two benches) of ten through retorts each. Each section has a daily capacity of four million cubic feet of gas. The Glover-West new model is designed to take full advantage of the practice of steaming the charge. Coal is supplied to the hopper above each retort and continuously descends through the retort to the coke-receiving chamber below whence it is discharged to the coke-handling apparatus. The producers for the generation of fuel gas for the settings are of the latest step-grate type open to the atmosphere. The waste gases from the settings are collected in a main flue lined with insulating bricks leading either to the chimney or to the waste-heat recovery plant which consists of two Spencer-Bonecourt horizontal, induced-draught boilers with superheaters capable of evaporating 16,000 lb. of water per hour at 212° F., and generating steam at 120 lb. per sq. in. and 400° F. The steam supply from the waste-heat boilers is interconnected with that from the breeze-fired boilers and with the works supply.
The gas from each retort rises in a 10-inch ascension pipe through a gas-valve to a steel gas-collecting main to each setting of eight retorts. Each main is fitted with a 14-inch foul-gas valve and a 6-inch tar flush valve uniting in a 24-inch down-pipe to a common 30-inch diameter main, equipped with two retort-house governors with tar bosh and circulating apparatus. The hot coke from the retorts is received in a conveyer, whence it is passed to a series of screens erected over a set of reinforced concrete hoppers where it is stored according to size.
The producer-gas plant constructed by Messrs. Drakes consists of six patent "Trefois" mechanical breeze-burning producers complete with cleansing and exhausting plant and is one of the largest of its kind in this country. Provision has been made for extension by the addition of two more producers. From the outlets of the exhausters the cleaned gas is collected in a common main, and after passing through a water seal is dried before entering the retort settings.
The gas leaving the retort houses is carried across the coke yard below ground level in two separate mains to the by-product plant. The semi-direct ammonia recovery plant is of considerable interest as the method is an important new development in gas-works practice. In brief, the process consists in passing the crude gas, after cooling and removal of tar fog, through a sulphuric acid bath in a saturator of special type. The installation includes primary coolers, tar extractors, exhausters, crude-gas meters, saturators and final coolers, and in addition ammonia stills. After removal of ammonia and tar from the gas it is passed through the dry purification plant, is washed, measured and stored. The gas-holder, which is of the spirally guided type, was built by Messrs. R. and J. Dempster and is in four lifts. Its diameter is over 200 feet and when at its full height is about 208 feet above the foundation level. The gas is conveyed to the City in 36-inch mains of mild steel, and pressure boosters have been installed although generally the difference in level between Partington and the City is such as to ensure a flow of gas without boosting. Other interesting features are the administration building, workshops and stores, chemical plant building, and power house. Housing accommodation has been provided for part of the personnel of the new works, on the roadway leading from the main road to the works entrance.
Dunlop Cotton Mills, Castleton
THE DUNLOP COTTON MILLS, CASTLETON, NEAR ROCHDALE.
Dunlop Rubber Co
The mills manufacture the fabric forming the foundation of Dunlop pneumatic tyres. They were built at two periods: the ground floor and basement were commenced in 1914 and the large seven-story mill with the large sheds at the northern end of the works were commenced five years later. The factory contains 286,000 ring spinning spindles, the product from which is practically all doubled in various foldings from 2- up to 36-fold. Electricity supply for the works is from the Lancashire Electric Power Company at 10,000 volts; this is transformed to 400 volts in the firm's transformer house in which the apparatus can handle 12,000 kw. The present power consumption is at the rate of about 10,000 kw.
The various operations in the manufacture of cotton fabric are as follows: opening and cleaning (cotton fibres roughly arranged to form "lap"); carding (fibres combed and cleaned to form "sliver"); drawing ("sliver" successively doubled to parallelize fibres and eliminate inequalities of weight); "slubbing," which is carried out on a "slubbing" machine, intermediate frame, and roving frame (gives twist to the "sliver"); beaming and doubling (several threads rolled and twisted together to form cord); weaving (formation of the fabric from cord in a loom). Of considerable interest in these machines is the electrical device which automatically stops the machine should the "sliver" break, also the method of "piecing" the broken thread. Other machines are arranged to stop by mechanical means when a thread breaks.
Thomas Robinson and Son, Rochdale
MESSRS. THOMAS ROBINSON AND SON, RAILWAY WORKS, ROCHDALE.
Thomas Robinson and Son
The business was established in 1838 and has specialized in the manufacture of wood-working and flour-milling machinery. The works, which have been enlarged from time to time, occupy an area of fifteen acres and employ 1,500 men. They comprise three main buildings laid out so that material moves continuously forward from the raw to the finished state, the service being effected by electric cranes and tramways. The main machine shop, which is 600 feet long by 100 feet wide, is equipped with a complete range of modern machine-tools. The second building is devoted to the manufacture of sheet-metal work required in connexion with the flour-milling side of the business, and the third building is equipped as a saw-mill. All the machinery in the latter is of the firm's manufacture. Individual and group driving of machines are employed; electrical energy is supplied to a substation in the works from the Corporation. Subsidiary buildings contain the pattern shop, brass and iron foundries producing all the castings required, smithy, photographic and printing departments.
Tweedales and Smalley
MESSRS. TWEEDALES AND SMALLEY, CASTLETON, NEAR ROCHDALE.
Tweedales and Smalley
The firm was established in 1891 for the manufacture of cotton-spinning machinery and the first machine — a ring frame — was completed early in 1893. In 1906 the firm was converted into a private limited liability company and in 1920 turned into a public limited liability company. In the works, which now occupy fourteen acres and employ over 2,000 workmen, a thorough system of organization includes special means of quick transit of material and parts during all stages of manufacture. The company were pioneers in the use of machine-cut gearing throughout their machinery. Over 115,000 teeth are cut weekly for the various machines, and many notable improvements in spinning machinery have been introduced.
Mersey Power Company's Runcorn Station
THE MERSEY POWER COMPANY'S ELECTRIC POWER STATION, PERCIVAL LANE, RUNCORN.
Mersey Power Co
This station is situated at Weston Point, Runcorn, on the bank of the Manchester Ship Canal, whence the cooling water is drawn, on an admirable level site having ample room for extension, and is one of the selected stations in the North West England and North Wales Electricity Scheme. The machinery at present comprises three 12,500 kw. turbo-alternators by Messrs. C. A. Parsons and Company, generating three-phase current at 6,600 volts and 50 periods. The switch-gear is by Messrs. Reyrolle. Steam at 285 lb. per sq. in. and 675° F. is taken from seven Babcock and Wilcox marine type, water-tube boilers fitted with superheaters and economizers each having a normal rated steam-raising capacity of 45,000 lb. per hour. All the boilers have chain-grate stokers and are arranged for balanced draught. Energy is distributed in the area around the station at 6,600 volts, and at 33,000 volts to Ellesmere Port and Northwich, also to Crewe by the North Wales Power Company.
Mirrlees Bickerton and Day, Stockport
MESSRS. MIRRLEES BICKERTON AND DAY, HAZEL GROVE, STOCKPORT.
Mirrlees, Bickerton and Day
In 1897 the Mirrlees Watson Company of Glasgow built the first Diesel oil-engine made in Britain, and it is believed this was the third engine of that type built anywhere. After a few years of experimental work the manufacture of such engines reached the commercial stage, and by 1908 the department had grown to such an extent that limitations of space in the original factory resulted in the decision to build new works specially equipped. For financial reasons a separate company was formed and a large site recently extended to nearly 300 acres was acquired near the boundary of the Borough of Stockport and adjoining a goods yard on the L.M.S. Railway main London-Manchester line (Midland route). The area at present occupied by the works is nine acres. The engines built range from 25 to 1,000 b.h.p. operating on the four-stroke cycle, and from 40 to 2,000 b.h.p. operating on the two-stroke cycle. The latter are built in two types, namely the "Simplex" type which has been made so far in one size only of 40 b.h.p. per cylinder, and the "Mirrlees-Nobel" type made in powers ranging from 1,000 to 2,000 b.h.p.
The heavy machine shop is 325 feet long by 50 feet span, and is parallel to and of the same size as the testing department. The medium and small machine shops are bays of 25 feet span having saw-tooth roofs. The packing shop is entirely separated from the main shops to reduce fire risks and to enable finished engines to be removed from the main works. There are comprehensive stores for raw material and finished parts. The firm generates its own electrical energy, all machine-tools being driven electrically either individually or in groups. In the laboratory metallurgical problems and those relating to fuel and lubricating oils are dealt with. The company own two foundries and have a large interest in a third, but these are quite separate from the main works. On the welfare side, there is a pleasant and well-equipped canteen and an excellent sports ground close to the works, comprising a nine-hole golf course, cricket pitches, five tennis courts and a bowling-green.
The company have recently taken up the "nitralloy" process of case-hardening steel and employ Mr. E. G. Herbert's "Cloudburst" method of testing hardened surfaces and of giving such surfaces additional hardness.
Salt Union Meadow Bank Mine, Winsford
THE SALT UNION, THE MEADOW BANK MINE, WINSFORD.
Salt Union
With a single exception this is the only salt mine now in operation in Great Britain and was originally sunk by the late Mr. H. E. Falk about 1852. It was closed down in 1890 as the Adelaide Mine at Northwich was then being worked, but on the failure of the shafts of the latter in March 1928 the Meadow Bank Mine was reopened and full advantage taken to install modern equipment. The mine, which is situated in the heart of Cheshire between Winsford and Whitegate, is 460 feet deep, and covers an area of nearly thirteen acres. The methods employed in mining salt are quite different from those of the coal industry. Salt is excavated to a thickness of about 20 feet over a wide area, large square pillars being left at suitable intervals to support the roof. The winding gear is electrical with overwind control in duplicate. The shafts, which are 3 ft. 6 in. square, are served in the usual way by cages for trucks and passengers. The underground equipment consists of an electric locomotive for traction purposes, and an electrically operated Sullivan under-cutter with pneumatic drills. The mine is electrically lighted throughout.
The surface equipment comprises a complete crushing, grinding and grading apparatus, rock salt being required in so many forms from large lumps down to finely ground salt of which there are seven grades. An ample siding grid and a rubber conveyer to the bank of the river Weaver complete the transport arrangements.
See Also
Sources of Information