1862 London Exhibition: Catalogue: Class 7.: Platt Brothers and Co
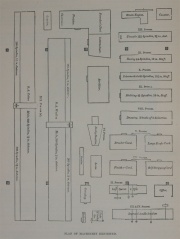
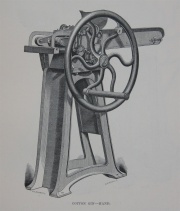
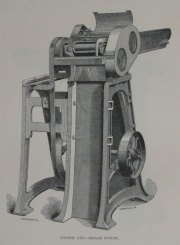
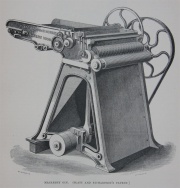
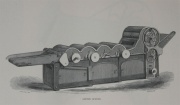
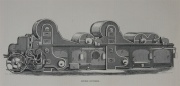
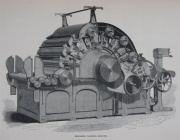
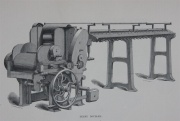
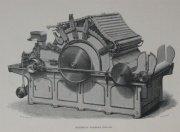
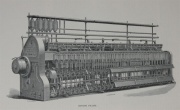
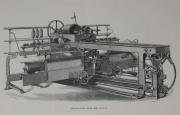
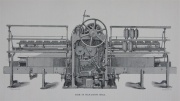
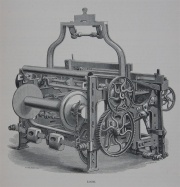
1528. PLATT, BROTHERS, and CO., Hartford Iron Works, Oldham
Machinery for preparing and spinning cotton and wool.
THE CHURKA GIN.
This machine is composed of two rollers, the lower of which is covered with hard wood, and is 1.5 in. diameter in its working part; the upper one is of steel, 0.5 in. diameter, with a finely fluted surface. They work in contact, and are coupled by gearing, so that their two circumferences travel at the same rate. It will clean all kinds of staple from hard seeds, one of its rollers being so small that the smallest seed cannot be taken in by the rollers.
When the fibre is separated from the seeds it is passed through the rollers and delivered, whilst the seeds as they are released drop through the grid in front of the rollers.
PLATT and RICHARDSON'S PATENT CHURKA GIN (exhibited)
The novelties and improvements introduced, consist in holding the rollers in contact, supplying them with seed cotton by a self feeder, and in preventing them from lapping. They operate as follows—The cotton containing the seed is spread on an endless travelling lattice, which conveys it to a series of three spiked rollers, the first of which revolving over the lattice and its circumference travelling at the same speed, holds the cotton; the second which travels much faster fills the spikes with cotton; whilst the third moves at an intermediate speed to the other two, its object being to prevent the second roller from carrying pieces of cotton on its surface.
The next operation is to strip the second roller and convey the cotton to the Churka rollers. This is done by a comb having a circular vibratory motion, given to it through an elastic connecting rod to prevent breakage in case of obstruction. After this operation of the rollers and comb, the fibres are loosened from the seeds, and are in the most favourable condition for being passed through the wood and steel Churka rollers. The steel roller is held in contact with the wooden roller by a weight and levers bearing upon its journals. A knife is fixed in a frame over the top of the steel roller to keep it clear. This frame also carries a roller covered with leather, which runs in contact with the wooden roller: this knife and the roller prevent the steel roller from being wrapped with cotton, and can be lifted out of the way together.
The bottom or wooden roller is kept from wrapping by a fluted roller revolving under it on the delivering side, and driven by one or the other rollers.
This gin will separate from hard seed about 600 lbs. of clean cotton weekly.
THE MACARTHY GIN.
This is a machine for separating cotton fibre from its seed.
The original Macarthy gin consists of a roller covered. with leather about 5 in. diameter, having a number of small grooves cut in spirals in its surface, making about one hundred and ten revolutions per minute. On the face of this roller is a thin steel plate acting against it with a slight pressure it is also furnished with a wire grid, upon which the seed with its fibre attached is pushed by hand against the face of the roller, which, by means of the spiral grooves, and the adhesive nature of the leather surface, draws the fibre under the steel plate until the seeds come in contact with its edge. Whilst the fibres are thus held the seeds are pushed off by the edge of a bar which has a vertical vibratory motion, so as to pass the edge of the plate where the seed is held, and thus separate it from the fibre, which is carried forward and delivered by a fluted roller placed in front, and which revolves in the same direction as the Macarthy roller.
It is important to make the spaces of the grid to the size of the seed the machine is cleaning, for if too coarse the seeds will pass through before they are cleaned, and if too fine they will accumulate.
ONE DOUBLE-ACTING MACARTHY GIN.
Platt and Richardson's patent (exhibited).
The novelties and improvements introduced are, in feeding the machine with seed cotton, which is placed on an endless travelling lattice, and conveyed by it to a series of rollers, the last of which is furnished with spikes, and travels at an increased speed, so as to separate the tufts in detail from the sheet spread on the lattice. From this spiked roller, the tufts are transmitted to the Macarthy roller by a comb having a circular vibratory motion given to it, through an elastic connecting rod, by which breakage from obstruction is prevented also in the introduction of two bars with vertical vibratory motion, moving alternately from a double crank (Platt and Richardson's patent balance), for the purpose of pushing the seeds from the fibre whilst held by the steel plate.
These improvements cause an immense saving of labour, as hitherto each machine required an attendant, and now one attendant can superintend several machines, whilst each machine will clean more than double the quantity.
This machine will clean all kinds of cotton, but it is especially adapted to such as contain soft and woolly seeds.
A machine 24 in. wide will separate from hard seed about 1000 lbs. of clean cotton weekly.
MIXING (FIRST PROCESS).— Selecting the bales and mixing the cotton is the first process in the cotton manufacture. It is done as follows—
A selection of bales of cotton suitable to the class of yarn required is made, and their contents spread out in layers of each so as to form a stack called a "mixing," from the sides of which the cotton is taken vertically to supply the opener.
THE COTTON OPENING (SECOND PROCESS). – This process is to open out the fibres of the cotton after it has been pressed in bales, and to extract the sand, dried leaf and other impurities imported with it, and it is important to do this without entangling or injuring the fibre. The machines used for this purpose are of various kinds, to suit the requirements of the trade.
NEW OPENING AND COTTON-CLEANING MACHINE.
The machine illustrated is recommended and used for cottons of short and middling staple. It comprises an endless lattice, upon which cotton is spread, and an iron roller with ribs on its surface, which together convey the cotton to a pair of fluted feed rollers, and is delivered by them to the first of a series of four cylinders which is furnished with twelve rows of teeth, the second, third, and fourth having only four rows of teeth. These cylinders revolve in the same direction, in journals or bearings supported by a horizontal framing, at a speed of about 1,000 revolutions per minute. These cylinders are all cased on the upper side with sheet iron, the first part of the under side of each is cased by angular bars with spaces betwixt them, forming a circular grid, which allows the dirt disengaged by the action of the cylinders to pass through to the floor.
The remaining part of the under casing is made from a perforated sheet of metal, which allows the dust to escape through whilst the cotton is passing over it.
The first of these cylinders strikes the cotton from the cylinders, and passes it on to the third and fourth cylinders, feed rollers, passes it over the circular grid and perforated so that this action is repeated three times with the four plate, and delivers it to the second cylinder, whence it cylinders, each making a deposit through its respective receives a blow equal to the combined velocity of the two grid and perforated plate, and as the light fibre only offers any resistance to the quick blows of these cylinders, it is impossible it should receive any injury in this operation.
The last or fourth cylinder drives the cotton over a straight grid to the back of two wire cylinders, when it is collected and afterwards stripped by two iron rollers, which carry it to a delivery lattice in front of the machine, so that throughout the whole passage of the cotton from the feed rollers to the wire cylinders, there is a continual deposit of impurities.
The two wire cylinders are exhausted by a fan which collects the dust within the casing of the machine and forces it into any place provided for its reception, by this means keeping the rooms where these machines are in operation perfectly free from dust.
These machines are also constructed with one or two cylinders, and with lap machines attached, so as to prepare laps to be afterwards fed up the scutcher.
ONE OPENING MACHINE, with two cylinders and lap attached (exhibited).
REMARKS. —The machinery previously used for opening and cleaning cotton having been found incapable of taking out the dried leaves and other impurities contained in the cotton imported to this country during the last few years, without materially damaging the cotton fibre, has called for the introduction of this machine to the trade, and it is found to be admirably suited to the purpose.
SCUTCHING AND LAPPING (THIRD PROCESS). —The machines are supplied with cotton from the opener in a uniform fleece by two methods; one by dividing a feeding lattice into a number of equal parts, and spreading uniformly upon each part a given weight of cotton to present to the feed rollers. The other is by driving the lattice and feed rollers of the scutcher at varying speeds in proportion to the thickness of cotton supplied, which speed is regulated by the rise and fall of the top feed roller multiplied by levers, so as to guide a strap communicating motion to the lattice and feed rollers, from a cone pulley revolving at a uniform rate to a second cone pulley. These pulleys are on parallel vertical axes attached to the sides of the feeder; thus when the feed roller rises, its speed is diminished, when it falls it is increased, and an almost uniform supply of cotton is presented to the first cleaning cylinder, which is furnished with twelve rows of teeth, that in revolving strike the cotton and pass it over a circular grid to a revolving beater with three blades, which then passes it over a second circular grid and a straight grid to a pair of wire dust cylinders that are exhausted by a fan. The cotton is then stripped from these dust cylinders by a pair of iron rollers, and passed through a second set of two pairs of feed rollers which revolve more quickly than the first, thereby delivering a thinner fleece to the second beater, which again passes it over a circular and straight grid to two other wire dust cylinders which are stripped by rollers as before. This latter pair of cylinders and rollers travel at three times the speed of the feeder, so that they deliver a fleece one-third the thickness first supplied to the machine.
The next operation is to form the cotton into a large roll or lap. This is done by the lap machine attached to the scutcher, forming together one machine.
The rollers which strip the last dust cylinder, deliver the fleece to a set of four callender rollers placed over each other, so that the cotton in passing through them receives three compressions, which form the fleece into a kind of felt; three of these callenders have their surfaces kept clean by bars of iron covered with flannel which are pressed in contact with them. The cotton then passes over one of two large fluted rollers which revolves in the same direction, and under a smaller plain roller which is above the fluted roller, and receives its motion from it by contact through the fleece; this small roller also cleans the second callender roller, by running against it in a contrary direction with a slight pressure (it also breaks the fleece when the lap is formed).
The fleece is now wound upon an iron tube slightly taper, that is placed in the channel between the two fluted rollers, and driven by contact with them, having gudgeons at each end, on which it receives pressure from two friction pulleys revolving in racks placed vertically and gearing into pinions upon a shaft across the machine. This shaft again communicates by gearing to a break pulley which has a slight pressure given to it by a lever that can be released by the foot of the attendant; by this means as each successive layer is wound upon the rollers, the break slips and allows it to rise. One of these fluted rollers has a worm on its axis geared into a wheel with such a number of teeth, that one revolution of it will indicate the length of fleece to form the lap required. On the same axis as this wheel is a tappet which stops the feeding motion and callenders, by pulling the support from under the hand levers that carry the end of the driving shaft. When the wheel drops out of gear, the two fluted rollers carrying the lap continue to revolve and break the fleece, the foot lever releases the break, the racks are lifted by a hand wheel, and the lap is taken out and stripped by dropping the small end of the tube upon a block of caoutchouc placed conveniently on the floor, and which, by its elasticity, causes the tube to rebound from the lap, when the attendant seizes it, lifts it out of the lap and again places it upon the machine, lowers the rack and friction pulleys by the hand wheel, lifts up the gear levers, and the process again commences.
THE SECOND SCUTCHING AND LAPPING (FOURTH PROCESS).— The machine used in this process is similar to the one previously described except in its feeder part, which is so arranged that three of the laps made by the first machine can be placed upon it so as to be uncoiled by the traverse of the lattice, and which is done as follows — Through the centre of the laps rods are inserted, the laps are then placed upon the lattice with the rods in slits or guides made in the framing to receive them, and thus keep them parallel; the laps are then uncoiled and spread upon the surface of the lattice in three layers on the top of each other, so as to present to the feed rollers a uniform fleece equal in thickness to that fed upon the first scutcher.
The machine is then set in motion, the cotton is passed through the feed rollers, and the remainder of the operation is precisely the same as in the machine previously described. By thus doubling the laps the fibres are more thoroughly mixed, and the fleece is made more uniform in thickness; and as the fleece must be uniform in its length and breadth as well, it is absolutely necessary that the beater should produce one uniform current of air, and thus waft the fibre over the straight grid direct to the wire cylinder. It is whilst the cotton is thus floating that the heavier impurities, loosened by the beaters, drop out and fall through the grids into the dust boxes. The laps formed by this machine are then taken to the breaker carding engines.
ONE NEW SCUTCHING AND LAPPING MACHINE (exhibited).
Novelties consist of an improved section of machine, by which more uniform currents are obtained, and better felted laps produced; in cylinders with teeth in combination with a beater with knives instead of having a beater only; in producing a uniform fleece by varying the speed of the feed roller; and lastly, in the covering and casing them with steel made by the Bessemer process, and in the application of Lord's patent feeder.
REMARKS. —By successive stages through a long series of years to the present time, the difficulties which originally presented themselves to the adoption of this class of machinery for cotton cleaning have been overcome, and the cotton can now be perfectly cleaned without injury to the staple or fibre, laps produced with fleeces uniform in length, breadth, and thickness, and so felted that they uncoil at the carding engine without any derangement of the felted fleece.
THE FIRST CARDING ENGINE (FIFTH PROCESS) continues the operation from the lap machine to the drawing frame by a kind of combing process. For low coarse yarns one only is used (single carding) to change the lap fleece into a sliver, but for finer yarns, and for coarse yarns made from the best description of cotton, two cards are used, one acting as a "breaker "and the other as a "finisher," the laps to supply the latter being formed from slivers delivered by the breaker on a machine called the Lap Doubler. By this process the felted fleece delivered by the lap machine, with its fibres crossed in all directions, is combed and straightened, and the light impurities still adhering to it, such as short fibre and the moss-like covering of the seeds, are taken out, for if allowed to pass this operation they would give a roughness to the yarn. To straighten and clean each fibre in the fleece, it requires to be combed many times, and this is done in its passage through these machines as follows —
The breaker card illustrated (may also be used for single carding for coarse yarns) has a taker-in, three self-stripping dirt rollers (Adshead's patent), and the remainder of its upper surface covered with rollers and clearers. This card is supplied or fed by a lap of the fleece from the lap machine, which is placed on a roller at its feeding end, guided by plates at each side which have slots in them to receive the ends of the rods passing through the laps' centre. The unlapping of this fleece is governed by the motion of this roller; it is now passed over the plate to the feed roller which delivers it to the taker-in roller; at this point the combing or carding commences, whilst the fleece is held by the feed rollers travelling at a slow speed, the taker-in running much faster and having its surface covered with cards (see CARDS), a kind of wire brush covered with crooked teeth so fixed that the points of the teeth strike down into the fleece held by the feed rollers. As these fibres are combed the impurities separated fall to the floor; the taker-in passes the fibrous tufts of cotton as they are released by the feed roller on its under surface to the large cylinder which is also covered with cards and which revolves in an opposite direction to the taker-in. The points of its teeth incline in the direction of motion, and its surface travels much faster than that of the taker-in from which in passing it takes the fibrous tufts and carries them to the self-stripping dirt rollers, the cards on which have their hook point to face those of the cylinder, so as to hold in the interstices of their wires such impurities as they may receive, which are carried forward by their motion and stripped by a vibratory comb so as to form a roll on their upper surfaces, to be taken away at intervals.
These dirt rollers revolve with a very slow motion, so that they assist in stretching the fibres as well as in collecting the dirt. From the dirt rollers it passes under the first clearer to the first carding roller, whose hooks also face those of the cylinder, so as to straighten the fibres and divide any tuft remaining; this roller passes the fibres fixed in its teeth (by their antagonism with the cylinder) back to be stripped by the clearer, this again delivers them to the cylinder to be again divided by the same roller. This operation is repeated by each of the five rollers and clearers, till the tufts are all reduced to straight fibres, which pass on to the doffer (another cylinder about half the size of the main cylinder); the hooks of the doffer face the cylinder, its motion also recedes with it and travels at a much slower speed, the fibres are again stretched whilst they are left on its surface, they now pass on its under side to be stripped by the doffing comb, which is formed of thin plates of steel having fine straight teeth on their lower edge, which are hardened to prevent wearing; these plates are fixed to a channel-bar which is connected at each end to a crank running at a high speed, and which gives to it a vertical vibratory motion, so as to strip a portion of fleece from the face of the doffer by its downward motion and clear itself by its rising, the fleece is then contracted through a funnel and taken forward by the drawing rollers which deliver it in the form of a sliver or riband to the coiler and can.
COILER AND REVOLVING CAN MOTION.
This is a small machine for receiving the slivers from the breaker cards, and coiling it into a tin can for the purpose of taking it to the lap doubler. It works as follows—The sliver from the draw-box of the carding engine is passed through a funnel in the top cover of the machine, to a small pair of revolving rollers underneath, by which it is taken in and delivered through a tube and revolving plate to the can over which it is placed: the top end of the tube is concentric and the lower end eccentric to its motion, i. e. the tube is placed at an angle. The can is situated below in a revolving dish, whose position is eccentric to that of the top plate; by means of these two motions, and the top plate running a number of revolutions for the bottom plate one, the can receives a number of coils each revolution. The outside of these coils are laid so as to touch the inside of the cans, where they form circles of coils continually crossing each other, until the can is full up to the top plate, which, still continuing to deliver, presses more sliver in the can, and thus causes them to come out without adhering to each other.
A BREAKER CARDING ENGINE 40 in. on wire, 401 in. diameter of cylinder, patent feeder, taker-in 9 in. diameter, three self-stripping rollers, four rollers and four clearers, 20-in. doffer, coiler and revolving can motions, and Platt and Richardson's patent balanced cranks (exhibited).
A BREAKER CARDING ENGINE 40 in. on wire, cylinder 40.5 in. diameter, patent feeder, taker-in 9 in. diameter, two self-stripping rollers (Adshead's patent), five rollers and four clearers, 20-in. doffer, coiler and revolving can motions, and Platt and Richardson's patent balanced cranks (exhibited).
CARDS.
These cards are made by fixing staples about in. long, and in wide, made of very fine wires, with a side bend in the middle of their length, into a strip of elastic cloth composed of caoutchouc, united to a number of layers of cloth, made from either linen, cotton, and wool, or a combination of these materials; these strips are about 11 in. wide, and in lengths that will cover the cylinder by being wound spirally on its surface. These staples or teeth are made of varying strengths of wire, and set in the cloth at pitches to suit the parts of the machine, as well as the kinds of work they are intended for; they were formerly all set in leather, which is still used to a limited extent for cotton, but still more generally for wool. When the card is wound tight on the cylinders the crossed end of the staples is pressed to its surface, so that they can neither rise nor fall, but have an elastic firmness which keeps them to the work.
A portion of the wire used in making the cards exhibited is from steel made by Bessemer's process.
THE LAP DOUBLER (SIXTH PROCESS) exhibited. — By this machine the slivers from the breaker card are formed into a fleece and coiled into a lap to supply the finisher card; it operates as follows—
Two rows of tin cans containing slivers are placed on each side of the feeding table, which forms the section of a cone; this table is furnished with two pairs of plain rollers of the entire length of, and parallel to, each side; these rollers take the slivers from the cans filled by the toilers, and deliver them upon the surface of the table. In their course from the cans to the table the slivers pass through holes in a bar of iron to guide them over a curved plate, under which is a revolving shaft that carries a boss with three wings opposite each sliver. On the top edge of the curved plate is a fulcrum, which carries a small two-ended lever; the lower end hangs under it, and is heavier, to give it a vertical direction, so as to cause it to fall in contact with one of the wings in the revolving shaft. The top ends of these levers project above the plate, and are pressed down by the slivers passing over them, when the shaft is free to revolve, till one of the slivers either breaks or runs out, when its lever falls, and stops its motion. The stopping of this shaft puts in motion a cam that moves the strap upon the loose pulley, and stops the machine; the end of the sliver is again supplied, and the machine proceeds as before. By this means missing slivers, or "singles," is entirely prevented, and the fleece is uniform.
Two slivers, one from each side, pass up the centre of the table, close to each other, from the apex of the cone, the others are supplied in equal divisions on each side, so as to fill the whole surface.
The lap machine is connected to the wide end of the table, and the first of its callenders that receives the sliver, travels at the same surface speed as the smaller rollers that supply the table from the cans, so that the slivers move in straight lines from one to the other, and are drawn over the table by mutual assistance, as the long ones up the centre would break if not assisted by those at the sides.
The machine that winds the lap is similar to that described for the scutcher, but the laps are wound upon wooden bobbins that are taken with them to the cards. These bobbins are weighted by Knowles' patent motion, consisting of an iron roller which presses on them whilst their ends are formed against revolving washers, guided in their centres, without gudgeons, which facilitates the removal of the laps.
These machines are constructed to form laps, either one-third, one-half, or the full width of the lap required, as may be desired.
The novelties introduced are — improved stop motions (Knowles' patent), revolving plates to lap ends, feeding table, and improved general construction of machine.
THE SECOND, OR FINISHER CARD (SEVENTH PROCESS). —The finisher card continues the operation of combing and cleaning commenced by the breaker.
In some cases for carding middling qualities, cards similar to the breaker cards before described, are used as finishers also; so that if desirable both may be used for single carding.
For fine qualities those of the construction illustrated and exhibited are most generally used; for fine qualities of still higher counts, this construction of carding engine is used for both breaker and finisher; and for the finest qualities, it is used as a breaker card for cotton to be afterwards combed by the combing machine.
The finisher is supplied with laps formed by the lap doubler (before described) of 96 slivers from the breaker card, in order that the mixing of the cotton may be more thoroughly effected, and to ensure more perfect uniformity of the sliver.
These laps are placed between two rollers at the feeding end of the card which unlap the fleece and deliver it to the feeding roller; they are guided at each side by a plate to keep the fleece central with the cards. The taker-in roller combs it from the feed rollers, and carries it to the main cylinder, which is covered on a portion of its surface with a train of iron flats, covered with cards, and united at each end by links, so as to form an endless travelling lattice. This lattice is carried on shafts, having a slow motion, and supported by bearings in the general framing. Those flats in operation slide upon a curve that is adjustable to the cylinder.
The sliding portion of the flat is formed with a slight angle to the face, upon which the card is fixed, so that the point of contact with the cylinder will be near to the front or leading side of the card. Those flats not in operation slide on plain slips on each side of the cylinder to support them whilst the faces of the cards on their surface are ground true and sharp by a short disc of metal covered with emery, and running at a quick speed and at the same time traversing over the lengths of the strips of card on the flats, so as to form the points of wire to a true surface. The hooks of these cards face those of the cylinder, so that each flat combs the fibres as it passes on the face of the cylinder. The main cylinder and doffer are also made true by this method of grinding. The impurities separated are carried forward by the motion of this train, and are stripped off by a vibratory comb in front, when they fall into a box.
After passing the flats, the fleece is again combed and delivered as before described in the breaker carding engine.
TWO FINISHER CARDING ENGINES, 40 in. on wire, cylinder 40.5 in. diameter, with patent feeder, taker-in 9 in. diameter, fifty revolving flats (Leigh's patent), eighteen of which are in action, and doffers 18 in. diameter, coilers and revolving can motions, guards to wheels, etc. , and Platt and Richardson's patent balanced cranks (exhibited).
The novelties consist in the arrangement of the machine, so that the flats can be accurately ground whilst the card is working, and the other portions of the machine can be stripped and ground without being moved from their place, and in the application of a motion to stop the doffer when breakage of sliver or any other obstruction occurs.
REMARKS.- Until recently, the finisher cards were constructed without taker-in rollers, the main cylinder taking the fleece direct from the feeding roller, causing the fibres to fill the cards, and any impurities passing the feed rollers damaged the cards on this large surface. By using taker-in rollers, these evils are prevented, the fibres being delivered to the cylinder without pressure.
The original difficulties with the carding engine were to maintain true surfaces, on which the cards were fixed; (these being generally constructed of timber varying with every change of the atmosphere, had to be made true each time by grinding the full parts from the ends of the wires.) The cylinders and rollers were not carefully constructed so as to run with a steady motion.
The fixings for carrying the different journals were not capable of a fine adjustment, neither were they steady after being set. These defects prevented the cards working sufficiently near to each other without occasionally coming in contact, which destroyed the carding point. The above defects are now overcome by using iron instead of wood, and by the aid of machinery in the construction. The moving parts are capable of fine adjustment, and are as firm as the fixed ones when set. These improvements in construction cause less grinding and stripping to be required, as the finer and truer the points of the wire can be maintained, the clearer will be the card.
THE DRAWING FRAME (EIGHTH PROCESS).—By this process, the cotton already cleaned, carded, straightened, partially drawn and formed into ribands or slivers, is doubled and further drawn by passing a number of those ends or slivers—say about six—over guides depressed by the weight of the sliver, through a series of four pairs of rollers, each pair travelling at a different speed; the difference in this case between the first and the fourth pair being about as one is to six, that is to say, that the circumference of the fourth roller travels through a space six times greater than the circumference of the first pair, and by so doing elongates or draws the sliver thus passed to six times the original length, and forming a single web, which is passed through a funnel to a pair of callender rollers, through which it passes to a coiling motion which deposits it in a revolving can, as described in the carding engine.
The sliver thus deposited being doubled six times and drawn six times is the same weight or thickness per yard as each of the slivers received by the back roller, and the object sought by this is to equalize the quality of the cotton and to make the slivers of uniform strength and texture by the combination. This process is repeated three times in this machine, and the amount of doubling and draft is equal in each case, say 216.
The guides depressed by the sliver in passing to the back rollers act as stop motions when the sliver breaks or runs out, by being thus released and coming in contact with a spider having a circular vibratory motion communicating to it through a catch box connected with a strap fork.
ONE DRAWING FRAME, with three heads of three deliveries each, four rows of rollers, the front row of steel made by the Bessemer process, and the back row fluted with coarse flutes, Leigh's top rollers to the front row, and coarse fluted top rollers to the back row, fitted with stop motions, coilers, and revolving can motions, and improved flats with endless traversing cloth, for cans 36 x 9 in. (exhibited).
The novelties introduced are in the use of rollers made from Bessemer's steel, Leigh's top rollers with revolving bosses, for front row; in an improved top clearer or flat which hangs upon hinges, and is provided with an endless cloth which clears the top rollers by travelling over them; its advantages are, a saving of power, labour, oil, and roller leather, it is much cleaner than the ordinary flat, there is less friction, and consequently less heat and electricity; the oil is less fluid, and the greasing of the pivots of the rollers is much better, facility of inspection is much greater, and the "flat waste " is never taken away by the sliver; in a stop motion for stopping the machine when the sliver breaks betwixt the front rollers and the callender, and which is driven from the same shaft and catch box as that used when the sliver breaks betwixt the can and the back roller.
THE SLURRING, INTERMEDIATE, AND ROVING FRAMES (NINTH, TENTH, AND ELEVENTH PROCESS).-The single slivers of cotton delivered in the last operation of the drawing frame are now conveyed in their cans to the back of the slubbing frame. This frame is furnished with guides similar to those described in the drawing frame, over which the ends pass to a series of three pairs of rollers revolving at varying speeds, the speed of the first pair being to the speed of the last in the proportion of one to five, so that the sliver is again increased in length five times in passing through them. In front of these rollers are two rows of spindles which are furnished with flyers having two hollow legs, and upon these spindles, bobbins about 11 in. long are threaded. These spindles and bobbins are both made to revolve, but at varying rates, and from distinct and separate movements.
The cotton, now called slubbing, delivered by these rollers is partially spun or twisted by the revolutions of the spindles, passes through the hollow legs of the flyers, and is wound upon bobbins; two of these bobbins are then filled into the creel of the intermediate frame; the slubbings are then doubled by passing the ends of two of them through another series of three pairs of rollers, and joining, drawing, twisting, and winding them upon bobbins about 9 in. long, which are revolving upon spindles in front of the delivery rollers as before; two of these bobbins are then doubled in the creel of the roving frame, the process of drawing, twisting, and winding is again repeated, and the cotton, now called roving, is wound upon bobbins about 8 in. long, ready for being spun in the mule and throstle. The twisting of the cotton, after being delivered by the rollers of these machines, is effected by the revolutions of the spindles, the slubbing or roving is passed through a hole on the top of, and down one of the legs of the flyer to its finger or presser, round which it is coiled, and delivered to the bobbin; this presser hangs loosely upon the flyer leg, but is parallel with and earned round by it at a uniform rate, causing a uniform pressure to be given to the bobbin through its weight and the resistance of the air in its circuit. As the bobbin is being wound, it is caused to traverse up and down the spindle against the finger, so as to equally distribute the roving. The winding of the roving upon the bobbin is regulated by increasing or diminishing its speed accordingly as the bobbin follows the flyer or the flyer follows the bobbin. Frames are made in both ways.
When the bobbin follows the flyer its speed must be increased as its diameter increases by winding, or the roving will be irregularly stretched or broken.
The speed of the front roller delivering the roving and the speed of the spindle which twists it is constant.
In these frames the bobbin follows the flyers, and the first motion communicating with the bobbin is at its greatest speed when the bobbin begins to wind, the speed gradually diminishing as the layers are wound on. This diminution of speed is effected by moving a strap upon two conical drums, one concave and the other convex, the speed of the concave drum is constant; these drums also communicate motion to a rail which, in its up and down motion, traverses the bobbin upon the spindle, and by this means regulates the speed of this traverse to suit the increased diameter of the bobbins.
The length of these drums is arranged to suit the diameter of the bobbins to be filled, so that when the strap has been traversed across the drum, the bobbin has attained its full dimensions when the frame knocks off.
The bobbins being now filled, are taken off and exchanged for empty ones; the end of the convex drum is raised so as to release the strap, which is wound back to the opposite end of the drum by means of a rack and pinion, and the frame is ready for starting again.
ONE SLUBBING FRAME of 42 spindles, three rows of rollers, with Leigh's top rollers to the front row, back rows (top and bottom) fluted with coarse flutes. Double centrifugal pressure for bobbins 10 in. lift by 5 in. diameter, fitted with stop motions, indicator and improved flat with endless traversing cloth (exhibited).
ONE INTERMEDIATE FRAME of 60 spindles, three rows of rollers with Leigh's top rollers to the front row, back rows (top and bottom) fluted with coarse flutes. Double centrifugal pressers, for bobbins 9 in. lift by 4.25 in. diameter, with iron creels, indicator, and improved traversing top clearer or flat (exhibited).
ONE ROVING FRAME of 84 spindles, three rows of rollers with Leigh's top rollers to the front row, back rows (top and bottom) fluted with coarse flutes. Double centrifugal pressers for bobbins 7 in. lift by 34 in. diameter, with iron creels, indicator, and improved traversing top clearer or flat (exhibited)
The novelties introduced in these machines, are Leigh's front top rollers with revolving bosses and coarse fluted back rollers (top and bottom) for better holding the cotton; in an improved flat with its endless travelling cloth which hangs upon hinges as in the drawing frame; more complete casing-up of the working parts; more convenient arrangement of setting-on and knocking-off rods, and in more effective and economical lubricating arrangements.
THE THROSTLE (TWELFTH PROCESS). —These machines are generally used for spinning yarn, for making warps, and winding it upon small bobbins; they have also been sometimes arranged for spinning weft and winding it in the form of cops, but never with good practical results, and always at a cost of increased complication in the mechanism. They are used for spinning from 40s. downwards.
The creel for supporting the bobbins filled with rovings to be spun by the throstle, is placed on the top of the frame between two sets of three pairs of rollers, and which travel at varying rates, the variation in this instance between the first back roller, and the third or front, being about one into eight. Through one of these three pairs of rollers each roving is drawn and afterwards passed through an eylet or guide wire, which is fixed in a bar of wood (hinged to the beam for supporting the rollers), and whose position when at work is immediately over the centre of the revolving spindles which twist the yarn; one row of which is supported by rails, parallel with and perpendicular to the rollers on each side of the machine. The tops of these spindles are furnished with flyers, round one leg of which the thread is coiled and passed through another eylet at the bottom to a bobbin which is threaded upon the spindle, and upon which the yarn is wound. The lower rail or bar for supporting the spindles, is fixed, and the upper one is movable, and upon it the bobbin rests; this rail or bar has an up and down motion given to it by means of racks and pinions in communication with a heart cam; the bobbin is thus moved up and down the spindle past the eylet of the flyer, and the yarn is equally distributed upon it in winding.
The motion of the bobbin round the spindle is variable, and is obtained from the tension of the yarn whilst winding, and as the revolutions of the spindle and flyer cause the yarn to drag the bobbin after them, and the weight and friction of the Vobbin upon the movable rail acts as a break, the yarn is wound tight on its surface.
ONE THROSTLE of 152 spindles, 2 in. lift, three rows of rollers, Leigh's front top rollers, middle and back rollers self-weighted, lifting rails, top and bottom oiling plates (exhibited).
The novelties introduced are as follows — Oiling plates for both bottom and top spindle rails the whole length of the machine, which can be lifted by racks so as to allow the attendant to oil the whole of the spindles without interruption; also in an improved iron creel plate fitted with steel pegs for the tin tubes of the roving bobbins to revolve upon, and in an arrangement by which yarns of one count may be spun on one side of the machine, whilst those of another count are being spun on the opposite side.
SELF-ACTING MULE FOR SPINNING COTTON.
TWELFTH PROCESS (a).—These machines are used for drawing and twisting into yarn the rovings as prepared by the machinery before described, and coiling or winding it upon spindles in the form of cops by automatic means. Like the common hand mule jenny, this machine may be divided into two principal parts, one part fixed, and comprising the creels for supporting the bobbins, the rollers for drawing or elongating the fibres, the frame-work or headstock containing the movements for effecting the changes required in the operation, and for communicating motion to the movable portion of the machine called the carriage, which supports the spindles and the drum for imparting motion to them, and which is made to traverse in and out from the rollers upon iron rails or slips as the yarn is being drawn out or wound upon the spindles. The average length of this traverse or draw is about 63 in.
As the fibres of the roving are being drawn and. delivered by the rollers, the carriage is caused to move from the rollers until it arrives at the end of the stretch, when it stops; the rollers and drawing-out motions are disengaged, the twist motion is acting, the spindles continue to revolve, until the quantity of twist necessary to be put in the yarn has been given, the change is then made from the twist to the backing off, by causing the direction of motion of the spindles to be reversed, and the yarn to be uncoiled a little, so as not to break by the depression of the faller wire upon it. The winding-on and taking-in changes are then made, the carriage advances to the rollers, the yarn is wound upon spindles, and the operation is complete.
The different changes are effected by means of a cam shaft in connexion with the long lever, which is acted upon by the traversing in and out of the carriage, the locking of the faller, and the revolution of the twist motion.
ONE SELF-ACTING MULE Of 648 spindles 1.375 in. distance, 16.5 in. spindles, three rows of rollers for two threads to each boss, Leigh's front top rollers, spindles driven by tin rollers, plate footsteps and bolsters, iron creels for single roving, back-shafts, and driven direct from the main-shaft (exhibited).
The novelties in this machine as exhibited and illustrated are:-
1. The introduction of foundation plates for supporting the headstock or principal framing of the fixed portion of the machine, the iron rails or slips upon which the carriage traverses, and the copping and taking-in motions, thus entirely preventing derangement of the working parts from deflection or bad floors.
2. The improved arrangement for driving the cam shaft by gearing instead of by friction, making the motion positive, and causing a more certain and noiseless action of the changes.
3. Simple and direct arrangement of rim or twist band (called double banding), by passing the band twice round the rim and all other twist pullies for driving the spindles, by which means we can work with slacker bands, have less strain in the bearings, less wear and tear of band, and a greater regularity of twist in the yarn.
4. A new taking-in motion, which is differential without having an eccentric band pulley or scroll. The circumference of the concentric pulley now used being equal to the length of the draw, stretch, or traverse of the carriage, gives to the band one uniform tension, ensuring greater delicacy of action in working, much greater durability, and less breakage of taking-in bands.
This motion being firmly fixed upon the foundation plate, and being connected directly with the carriage, has no tendency to lift it from the rails during its traverse.
5. Simple construction and arrangement of copping and faller locking motions with double copping plates, by which the copping rail may be taken out in any stage of the cop's progress, without disturbance of its working position.
6. The application of a governor or cop regulator for adjusting the winding-on motion to the formation of the cop, which is perfectly automatic throughout.
7. Improved construction of carriage or movable portion of the machine, and in the manner of connecting the square and the carriage together, combining greater accuracy, strength, and neatness; and in the position and arrangement of the diagonal rods for strengthening the same; and
Lastly. In the general construction and adaptation of the framing to form a casing to the working parts of the machine, the facilities for making changes when required for spinning varied numbers, in the introduction of a friction coupling, through which motion is transmitted to the taking-in motion, and which may be so adjusted as to slip in cases of obstruction to the free traverse of the carriage, thereby preventing breakages in the machine and banding.
GRINDING MACHINE used for grinding and sharpening the teeth of the cards on the rollers and flats of the carding engines.
WRAP DRUM AND SCALES, for measuring and weighing rovings.
WRAP REEL AND SCALES, for measuring and weighing yarns.
SET OF TACKLE, for nailing on cards.
ROLLER ENDING MACHINE.
MACHINE for forcing leathers on top rollers.
CASES containing samples of bottom and top rollers, spindles, flyers, and bobbins.
CASE showing cotton in its various stages of manufacture.
CASE, showing wool in its various stages of manufacture.
SET OF PHOTOGRAPHS of the machinery exhibited.
ONE POWER Loom, 38 in. reed space, for weaving plain calicoes for skirtings, any kind of twills, fancy goods in cotton, or fine woollen, union cloth with cotton warp and woollen weft, fine linen goods or union cloths with ootton warp and linen weft (exhibited).
The novelties introduced are:-
An improved picking motion, which is worked from the first motion or crank shaft; the picking shaft is provided with loose tongues, which are acted upon by cams every alternate revolution of the crank shaft; this arrangement is exceedingly simple, is little liable to wear, and can easily be repaired in case of accident.
An improved surface taking-up roller, without glass or emery, and which is applicable for either light or strong goods.
An improved self-acting temple, and a new buffer or check-spring (instead of check-strap), to prevent breakage of cops or bobbins in the shuttles of the looms.
PREPARING WOOL.
Wool is prepared for the carding engine, first by shaking and having the dust extracted from it by a machine similar to that illustrated for opening cotton, and afterwards by oiling, for the purpose of softening it and preventing the short fibre from flying.
Dyed wool is also passed through a similar machine to be cleaned, and for the purpose of extracting the spent dye-wood from it, before being oiled.
CARDING WOOL.
Wool passes through a series of three machines in this process; viz. the "scribbler," the "intermediate," or second card, and the finisher card and "condenser," and is supplied to the first on an endless travelling lattice, which has its surface divided into a number of equal parts, and upon each of which a given weight of wool is spread. This lattice carries it to a pair of feeding rollers, which draw in and deliver it to a taker-in roller that carries it on its upper surface under a guard roller to the breast cylinder; this taker-in roller is formed of cast-iron, with a fine groove or thread cut on its surface, and into this groove is pressed the lower edge of a flat wire, whose upper edge is cut into teeth like those of a fine saw, so that it has the appearance of a roller with a number of fine saws placed at short intervals. The object of these teeth is to stretch the fibres until they are released by the feed rollers, when they pass forward in the spaces betwixt them, and any burrs or impurities that are carried on the surface of the wool are driven back by the guard roller which revolves at a quick speed, and has a number of ribs fixed longitudinally on its surface. This roller is so placed that its ribs clean from the points of the teeth any refuse, and deposit it in a box placed over the feed rollers to receive it. The taker-in roller is stripped by a clearer roller which passes the wool to a breast cylinder having two rollers and clearers revolving in suitable bearings over it to be broken up and prepared for the main cylinder. The breast cylinder is stripped by a clearer, which passes the wool to a large cylinder, over which revolve four rollers and four clearers for carrying on the carding process, and a large roller, called a "fancy," covered with long toothed cards, and whose surface travels faster than that of the cylinder, the object of which roller is to prevent the cards of the cylinders from being clogged with grease and wool, to raise the wool to the surface, and to deliver it to the surface of the doffing cylinder, from which it is stripped by a vibratory comb, as described in the cotton-carding process.
The fleece thus stripped from the doffer is formed into a sliver by being drawn through a revolving tube by means of a pair of rollers that are placed in front of the doffer, at one end of it, from which it falls upon an endless travelling cloth just over the floor, to be then conveyed to the second or intermediate card.
ONE SCRIBBLER ENGINE, 60 in. on wire, with common hand-spreading lattice feeder, one 12 in. patent burring roller, with guard and dirt box, working from patent feed rollers, with patent stripper, breast roller 27 in. diameter, with two rollers and two stripping rollers; cylinder 45.5 in. diameter, with four stripping rollers, four rollers and fancy; doffer 22 in. diameter; roping apparatus, and floor creeper (exhibited).
ONE INTERMEDIATE, OR SECOND CARDING ENGINE, 60 in. on wire, with Apperley and Co.'s patent diagonal feeding machine, patent taker-in 7 in. diameter, with stripper 7 in. diameter; cylinder 45.5 in. diameter, four stripping rollers, four clearers, and fancy; doffer 22 in. diameter (exhibited).
The sliver delivered by the scribbler card is formed into a fleece to supply this machine by an apparatus known as "Apperley's feeder," by taking the slivers from the travelling cloth, over the floor, and laying them in lines close to each other upon a number of endless travelling webs, which are driven by a shaft parallel to the feed rollers. These webs are of increased lengths, from side to side of the machine, so as to form an angle to the feed rollers. By this means, the slivers pass obliquely, and a number of them are presented at the same time to the feed rollers, insuring greater uniformity of fleece; which, after having passed the feed rollers, is acted upon by the first of 2 taker-in rollers, about 7 in. diameter. The first of these is covered with saw-like teeth (as described in the "scribbler"), and the second is covered with cards, and is by them passed to the main cylinder, which conveys it to the doffer, whilst the process of carding is going on with the rollers, clearers, and fancy, as before described in the "scribbler engine."
This doffer is also stripped by a comb, and delivered in a thin fleece to a travelling lattice supported on rollers, which are carried by levers in the form of a pair of compasses, and having one point fixed, and the other moving, with a small carriage on rails, which also carries two tin rollers. By this lattice and rollers the fleece is deposited in layers across the feeder lattice of the
FINISHER CARDING ENGINE,
which is placed at right angles to the intermediate, and which moves with a slow motion, so that each layer is placed a little behind the preceding one. This system of moving lattices is known as "Ferrabee's feeder," and its object is to lay the fibres so as to enter the feed rollers of the condenser card crosswise, to be again straightened and taken forward by two takers-in to the cylinder, rollers, and clearers, to be carded and passed to the doffer, upon the surface of which the fleece is now spread uniformly. The next operation is to strip it off in a number of small slivers or bands, and is called
CONDENSING.
There are a great variety of machines constructed for this purpose; the one exhibited is of recent contrivance, and is patented and known as "Fairbairn's condensor." Its novelty consists in having small grooves cut round the doffer in equal divisions, and placing in each a thin blade of steel level with the point of the cards, where they receive the fleece from the cylinder. This steel blade follows the face of the cylinder at a short distance, therefore projects above the cards of the doffer so as effectually to divide the fibres that lay across this line, when they are taken by the side which has the firmest hold; they now pass under the doffer and are stripped by a plain card roller placed in the front of the doffer, and which conveys them to two endless travelling sheets of leather. Each sheet is carried on two rollers and vibrates in contrary directions, so as to rub them into round felt slivers or bands, to be wound on to two bobbins by surface contact with two rollers, so that each bobbin contains one-half of the threads delivered.
These bobbins are then filled into the creel of the self-acting mule.
Note.— For some qualities of woollen yarn the fleece is stripped from the doffer in bands, which are afterwards joined together by the piecing machine, and wound upon bobbins to be filled into the creel of the self-acting slubbing mule, to be partially spun and wound upon bobbins to supply the creel of the self-acting mule.
FINISHER CARDING ENGINE AND CONDENSOR, 42 in. on wire, Ferrabee and Co.'s patent bat feeding machine up to patent feed rollers and strippers, patent taker-in 7 in. diameter, with stripper 7 in. diameter, cylinder 45.5 in. diameter, four stripping rollers, four rollers and fancy; doffer 22 in. diameter, with Fairbairn's patent condensor, to deliver forty good threads and two waste ends (exhibited).
SELF-ACTING MULE FOR WOOL, 380 spindles, 2 in. distance, 18 in. spindles, to spin either upon the bare spindle, or upon wooden or tin spools, and from condensor or slubbing bobbins, either warp or weft yarn (exhibited).
The improvements and novelties introduced in connexion with the self-acting mule for cotton-spinning, are also introduced into this machine, in addition to which we have also introduced:-
A "double speed" or fast and slow motion of the spindles with two rims, the change being obtained by a traverse of the strap and two rims without the aid of either counter shaft or gearing, the rim out of action in each case being converted into a carrier pulley, enabling us to retain the double banding arrangement.
In a motion for giving out the necessary length of slubbing to be spun, which is so connected with the camshaft, as to give a simultaneous action of the delivering rollers and the drawing-out motion.
In a simple arrangement of a receding motion of the carriage during the twisting of the yarn, and which may be regulated to recede quickly or slowly, as the fineness of the yarn and the amount of twist may require.
In a simple arrangement for regulating the length of draw or traverse of the carriage, in accordance with the running up of the yarn and the recedence of the carriage.
The cards in use in these machines are made by—
For Cotton, Messrs. Joseph Sykes and Brothers, Lindley, near Huddersfield, and Mr. William Horsfall, Great Bridgewater Street, Manchester.
For Woollen, Messrs. R. and C. Goldthorpe, Cleckheaton, near Leeds.
The bobbins and skewers are supplied by Messrs. Lawrence, Wilson, and Sons, Cornholm Mills, near Todmorden, and the banding by Mr. Samuel Green, King Street, Oldham.
Messrs. Samuel Radcliffe and Sons, of Rochdale, and Messrs. Radcliffe Brothers, of Lower House and Wallshaw Mills, Oldham, are working the cotton machinery.
Messrs. H. and L. Newall, of Littleborough, near Manchester, and Messrs. the Executors of George Lawton and Sons, of Micklehurst, near Mosley, are working the woollen machinery.
The engine driving the machinery is made by Messrs. B. Hick and Son, Bolton.
Prices may be had on application to—
Messrs. PLATT, BROTHERS, and Co., in the Exhibition; at their Works, in Oldham; and at their Offices, St. Ann's Square, Manchester.
And from their Agents—
- Russia: Messrs. DE JERSEY and Co., Manchester, St. Petersburg, and Moscow.
- France, Belgium, Holland, Prussia, Bavaria, Italy and Savoy, Sweden and Denmark: Messrs. E. NATHAN and SINGTON, Manchester.
- Saxony and Bohemia: Mr. W. W. DERHAM, Leipsig.
- Vienna and Switzerland: Mr F. E. SCHOCH, Vienna and Switzerland.
- Spain: Mr. JAMES SYKES, Barcelona.