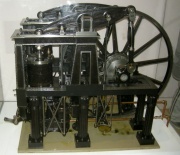
of Bolton-le-Moors (Bolton)
1833 Company founded by Benjamin Hick with his two sons John and Benjamin.
1833 Having left Rothwell, Hick and Rothwell, Hick set up a factory as Benjamin Hick and Sons.
1833 Patented Locomotive No. 6689.
1836 Supplied a 10 HP stationary engine to the Carrollton Railroad Co in Jefferson Parish, Louisiana, for ironworking purposes. It was damaged by fire in 1838[1]
1837 Delivered their first locomotives, seven four-wheel passenger type for the London and Birmingham Railway. The first were delivered in July 1837, and the remainder in 1838.
1840 'Large Casting.— On Thursday morning, an immense iron casting, about six yards long by three yards wide, and of a considerable thickness, passed through this town [Manchester?] on a waggon with eight wheels, drawn by no less than twenty horses and excited, as may be readily supposed, a good deal of curiosity. We understand it was on its way to the plate glass works, at Smethwick, near Birmingham, from the establishment of Messrs Hick and Son, of Bolton, where it had been cast and planed. We believe the weight was about nineteen tons. So great a number of horses in one team, at this period of railway travelling, would, no doubt, appear extraordinary ; but, we suppose the great weight and width of the casting had prevented it being conveyed by that mode.— Manchester Paper.'[2]
1842 Benjamin Hick died 9 September; the firm continued under the management of his son, John Hick
1845 John Hick took into partnership William Hargreaves, his brother-in-law and Benjamin Hick and Sons was renamed Hick, Hargreaves and Co
1851 Award at the 1851 Great Exhibition. See details at 1851 Great Exhibition: Reports of the Juries: Class VI.
1863 Engine for Hindley Twist Co [3]
1865 Article 'The Soho Works of Benjamin Hick & Son, Bolton' in 'The Engineer' [4]. This was reprinted in the Bolton Chronicle shortly afterwards[5]. An extract:-
' ..... in another part the town are forge and steel works, adjoining each other. In the first of these are a number of puddling furnaces and hammers, and it is here where the heavy forgings for the Soho Works are made. In the Bolton Steel Works, adjoining the forge, are two 5-ton Bessemer converters, which we saw in full work at the time of our visit. Powerful hammers and rolling mills are now being erected for working up the steel. From five to six hundred men are employed these two establishments, in which Mr. Hick, of the Soho Works, is we understand, one of the partners; the managing partner being a son of the late Mr. John Sharp, of the well-known Atlas Works, Manchester. Here are also rolled the Bessemer steel boiler plates, largely and successfully used at the Soho Works. Each plate has its edges cut in large shearing machine, one of the resulting crop ends being always bent double in order to test the quality of the material of each plate. The ductility of the material was remarkable, and it seemed the very stuff for boiler making. Apropos of boilers, we noticed a curious looking one placed in the usual way above a furnace. On inquiry we found that its appearance was due to a thick coating of a peculiar mortar-kind of material, made by a Bolton inventor. The boiler had worked for some time; its steam-producing powers were found to be improved by the retention of the heat by means of the non-conducting coating, and any extraneous corrosion was apparently also prevented. The other arrangements of the works were of the usual character adopted for puddling, forging, and rolling.
'In the good old days when there were comparatively few engineering shops in the world, before mechanical engineering had thrown off many separate off shoots, and before these causes, added to the present severe competition, had divided the trade into determinate special branches, the late Mr. Hick seems to have taken pride in turning out the most varied work. Locomotives, marine engines, machine tools, and many different kinds of manufacturing machinery, used to be made here. But marine engines are now almost solely, and at any rate most profitably made close to where the hulls they will drive are being built: while the fact that locomotive orders are generally given for a number at a time permits the adoption of special arrangements and tools, of, in fact, special factories, such as, for instance, the Gorton Works, which do not permit the competition of establishments like these, which are more suited for the manufacture of heavy stationary prime movers and their millwright gear.
'Walking through the works this is, in fact, what we see — very complete arrangements for making the large details heavy stationary steam and hydraulic prime movers. Amongst the machine tools is thus the large vertical boring machine which, when first constructed some years ago, attracted much attention. It consists, in reality, of three distinct machines, for boring, drilling, and face-grinding, respectively. Four columns support an entablature carrying the upper parts of these three different machines. In the centre is the machine for boring cylinders up to 95in. in diameter and about 10ft. high. They are fixed on movable supports in the usual way by clamps, and are also steadied by a circular frame able to slide up and down. The smaller boring machine used to be employed for boring out such work as cranks’ centres, but it is now found more convenient to do this kind of work in rather more accessible and independent machine. The smaller tool on the other side of the large boring machine illustrates the progress of different modes of work, and the introduction of scraping instead of grinding. It was designed for grinding the faces of piston rings and of similar work, which was fixed on the table as if being bored, while a vertical bar drove the grinding plate. At present, it need scarcely be said, such work is first faced in the lathe and then scraped up, a very slight grinding by hand, with emery and oil, being resorted to at the end of the process.
'Of a somewhat similar character in its way is the large planing machine, first designed many years ago by the late Mr. Hick, for planing large cast iron plates for glass casting. Old as it is, however, it was only few weeks ago that an American engineer, in the course of a visit to these works stated that he had re-invented and patented a planing machine after the very same plan — a coincidence which he only accidentally discovered after having sacrificed much time and money. The peculiarity of Mr. Hick's machine, once a wonder in its way, consists in making the tool move while the work remained stationary. It will take in a plate 30ft. by 12ft., and is also able to receive a cylinder of 400-horse power in order to plane the valve-box flanges and the other surfaces. The framework is formed of two longitudinal side pieces, on which rest the cross slide pedestals carrying the cutter box. We understand that the cross-slide consisted first of a round bar, able to slightly oscillate the cutter box holding two tools cutting each way, and alternately raised at each return stroke by the oscillation of the bar on the axis. To the cross bar carrying the tool are attached levers, one on each aide, to which were connected endless steel belts passing over pulleys at each end of the machine. One set were the drivers, the other set the carriers ; the friction upon the first being sufficient for the heaviest cut. As the belts moved the cross bar backwards and forwards at the return of each stroke, the oscillating motion was given to it, limited by two set pins. The machine is now fitted with one of Mr. Whitworth’s revolving tool boxes.
'Near the heavy vertical boring machine we spoke of at first, is a lathe, with a 10ft. face-plate, capable of boring up 16ft. diameter. A convenient plan, requiring only one setting, is adopted for boring out the eyes of engine beams. The beam is simply fixed on a table sliding in V slides, similar, in fact, to a planing machine table, the boring tool being worked in an ordinary vertical boring machine. This machine is also found very convenient for other work. A tool of, to us, rather novel form is used for facing up such work as the valve chests of large cylinders. It was designed by Mr. John Hick, C.B.. the present senior partner of the firm, and it may be styled a sort of composite tool between a slotting and a planing machine. The tool box is fed down vertically, being worked to and fro on a planing machine bed, while the work is set on a fixed table, the longitudinal axis of which is at right angles to that of the pair of slides which the tool box is worked. On the millwrights’ side of the establishment, where all other but engine work is done, the separate arms of the large fly wheels are fitted together ever pits, within which one-half of the wheels can turn. A lathe can thus be easily extemporised, so to speak, and fixed up at any diameter, and against the tool of which the wheels may be turned up. In the smaller pit, in use at the time of our visit, was being put together a spur flywheel 26ft. in diameter. The teeth of these wheels are never, in this establishment, cast solid on the iron rim. Such wheels, with the teeth on a separate outside rim, are found to wear much better, being free from the effects of unequal contraction, produced when the teeth are cast together with the main rim. Wooden packings, into which thin iron wedges are afterwards driven, are placed between the ends of the segments. All the boilers made there are, of course, systematically tested by hydraulic pressure, for which purpose set up a pair of force pumps which can be driven from the shop engine by means of a belt. The smaller machine tools are placed in a storey upon the ground floor on which are the heavier machines. In order to be able to clear away the columns which would otherwise have to support a floor eighteen yards wide, and to thereby afford room for the heavy cranes on the ground floor, the flooring of the first storey is suspended from number of slender tie-rods, attached to cross beams in the masonry. These smaller lathes and machines are of the usual descriptions.
'To an unprofessional visitor everything is new and astonishing in a large and mechanical workshop; but an engineer rather directs his gaze to more or less exceptional things. We must thus confess that we were previously unaware that such large pistons as 3ft. in diameter, and even more, could be made with the narrow piston rings first introduced into this country Mr. Ramsbottom, of Crewe. The large horizontal blowing cylinders for Mr. Bessemer’s converters are made with such pistons. We notice that the cast-iron rings of the ordinary V-piston have additional elasticity given them hollowing out the inside with a V-groove, and then drilling a series of holes round the circumference, which are afterwards opened with many radial saw cuts. Messrs. Hick and Son, with Messrs. Galloway, Manchester, are, we believe, the sole English engine-makers licensed by Messrs. Bessemer to manufacture his blowing engines, converters, hydraulic cranes, and the general apparatus used in his process. A number of Bessemer converters and other work of the kind were being made here, amongst which we noticed a small one, 4ft 4in. in diameter, ordered Mr. Ramsbottom, of Crewe, for carrying out experiments in the conversion of Bessemer steel. A good deal of work is here turned out for the Royal Arsenals, amongst which observed some small surface condensers, on Spencer's principle, intended for stationary engines. Close by was being fitted up an engine upon Corliss’ patent. With a somewhat complicated appearance, and arrangement of gearing which could not be made clear without diagrams, we feel, as the result of our examination, no doubt that the success of these engines in America and some parts of Germany, where fuel is much dearer than with ourselves, has been well deserved. At these works was, we believe, first introduced some years ago, a very simple and efficient mode of strengthening the internal flues of boilers. T-iron rings are used, on which the plates are rivetted thus ? — a space being left between them for access for caulking, while the T-iron ring itself can caulked in the usual way. We noticed a great number flues made upon this principle; and the rings and plates were in addition welded together at the longitudinal joint, thus forming almost as strong a flue against collapse as could possibly be made. Those works are noted for the use of a particular mixture of very hard brass. As an instance of what can be done in this way, we may state that, while in Preston a short time ago, we paid a visit to Messrs. Horrocks’ large mill, which has been at work for nearly seventy years. Exactly twenty-five years ago, the late Mr. Benjamin Hick erected there a pair of very handsomely-designed beam engines, each of 100-horse power nominal, but together now working up to some 670 indicated horse-power. The cylinders are 45in. in diameter, with an eight foot stroke, and were probably designed to work about ten revolutions per minute, though now driven at double the speed. We were informed by the managers of the mill that these engines had been working without the least repairs for the last quarter of century, and that the crank brasses had during that long period only worn down one-sixteenth of inch.
'Amongst ether comparative novelties in enginework to be seen here is an engine upon Mr. E. E. Allen’s principle - a plan now very generally known to the engineering public, more especially in the shape of a portable engine. It has been indicated to 60-horse power, and is now driving two fans, sand mixing machines, and other work for the large foundry of the establishment.
'An interesting peculiarity of the Soho Works is the number of novel schemes for various purposes in stationary work, which are being tried or are being actually manufactured to meet a demand. Experiments of this kind may often directly unremunerative, but they are attended with indirect advantages of various kinds, amongst , which may be reckoned the acquirement of reputation for keeping abreast with the times, well as a resulting general stimulus to the powers of invention of the draughtsmen and foremen in the works. Amongst the novel apparatus of this category is a very ingenious hydraulic press for packing cotton, the invention of Mr. Luthy, a gentleman in the employ of the firm. We described this useful press some time ago. To those who have studied the history of the hydraulic press it is well known that the late Mr. Hick gave it the finishing touch after its leaving Bramah’s hands, having, can be proved by irrefragable evidence, first indented and adopted the self-expanding collar as at present used. Large numbers of hydraulic presses, and, at one time, the largest presses made in the trade, have been turned out of these works. As Mr. Luthy's very ingenious press is the one recommended by the firm for packing cotton — for machines of which kind there is now a large demand in that now reviving trade — we may briefly describe it again, as it is mainly designed to economise in time and labour in pressing cotton, also render the press itself more portable. At the same time, it must be remarked, that only a set of diagrams would do justice to its arrangements. The first portion of the stroke in packing the cotton bale - during which, as in packing hay, there is necessarily but little pressure required — is rapidly performed by means of a ram of small diameter, into the cylinder of which the water is, of course, quickly pumped. This small ram is either placed inside or outside the large cylinder. When its work is done, and more pressure and less speed is required, the force pump is made to act on the large ram, which completes the stroke. An ingenious, self-acting apparatus is used for alternately admitting the supply to the rams. It consists of a suction valve, for the supply of the large cylinder during the first part of the stroke, and of a valve weighted according to the pressure of the pumps or accumulator, besides the ordinary arrangements for letting off the water. It opens and gives the pressure to the large cylinder, when the small ram meets with resistance to the pressure on its useful area. There are several other noteworthy points about Mr. Luthy’s press.
'Mr. Hick has also tried that curious scheme for raising steam — Grimaldi’s rotary boiler. The inventor is an Italian, Dr. Grimaldi, and a specimen of his boiler was seen in the Italian Department of the 1862 Exhibition. Such is the progress of science and the changes of time. In the last century Italy sent us Grimaldi the clown famous for his summersaults; in this century she exports the Grimaldi rotating boiler. We understand that the apparatus which is now showing worked very fairly, but that neither an increased evaporation nor diminished deposit showed itself as a set off for the necessarily additional complication and expense. We also doubt whether the plan is even a valid patent, for a similar scheme is to be found described in a very old back volume of our contemporary the Scientific American. A very different mechanical invention is the arrangement, the invention of Mr. R. Harwood, a gentleman in the employ of Messrs Hick and Son, adopted by the firm for easily regulating the speed of turbines and water-wheels. Applied to a turbine the clow for regulating the inlet of the water is connected to a piston. This piston is worked means of water, let in on either side valve, which valve is opened or shut by a ball governor, driven by the prime mover. The motion of the clow is thus directly regulated by means of the governor, which has only to overcome the resistance of the valve itself. When the turbine is running at the proper speed the valve occupies a central position, covering the ports, thereby preventing ingress or egress of water to the cylinder, and the throttle valve is thus kept stationary. But should the speed be increased the governor balls fly out, and lowering the valve at the end of the rod, allow the pressure of water to come on the top side of piston, which moves downward and closes the throttle valve until the right speed is attained, when the valve again occupies central position, and locks the throttle valve as before. If, on the other hand, the speed becomes reduced, the valve at the end of the rod is raised, the water pressure is brought bear the on underside of the piston, and the throttle valve is proportionately closed until the right speed be again attained. This simple plan has been successfully in use for some time.
'Among the inventions of Mr. Bell, the principal millwright of these works, is a simple lubricating apparatus, largely made here. In the course of our visit saw many hundreds of the above very ingenious form of self-lubricating bearing for mill shafting, and as many thousands are use in Lancashire mills, a goodly number of different self-lubricating apparatus for shafting have been tried at various periods, but lubrication by hand is still in very general use. We remember a noted case where, in some large works in Manchester, each bearing was provided with apparatus, worked by gearing, and causing the oil flow drop by drop from a glass cup. The greater number worked very well, but one or two out of the lot got each day out of order. The result was that the man usually employed to perambulate the works and lubricate the shafting had to continue at least supervision over the bearings, that little or nothing was gained by the numerous lubricating apparatus. They were afterwards removed, with a return the old system of hand lubrication, with its attendant objection, amongst others, of much waste of lubricating matter. Tho sine qua non of an apparatus of the kind is thus simplicity, which seems to be attained in Mr. Bell's plan. We understand that a grooved bearing oiled by this means can be left to itself for more than a quarter of a year.
'Thousands of men and boys are being every day let up and down the colliery pits of this country means of wire ropes. It is only a long habit that can quite overcome the rather uncomfortable feeling that one’s life is literally dependent on a thread —of iron or steel though it may be. In some mining countries, such those of Germany and Austria, it is forbidden by law to use mining cages unprovided with safety apparatus for raising and lowering the miners. Much damage and loss of life are annually caused in this country from the mining cages being but seldom provided with one or other of the several forms of safety apparatus which have proved themselves be more or less efficient. A rather large number of contrivances of the kind were to be seen South Kensington in 1862 ; some of them very ingenious, and constructed on sound principles ; others scarcely deserving such praise. We remember a very eccentric cage of the kind. It was so designed as to bring catches against the pit guides means of the action of common - ball governor ; and it was expected by the inventor that (supposing the instrument kept its efficiency in the midst of the pit dirt and coal dust) too high speed of the balls would be sufficient cause the catchers to act and stop the descending cage. Unfortunately, however, the cage came to grief in the very exhibition itself, as the governor balls refused to act when the cage (which was arranged in guides of some altitude) was allowed to drop by tho exhibitor. An evidently much more efficient apparatus the kind is that of Mr. Owen, made these works, and several specimens of which have been in efficient action for some years in the Lancashire mining districts. The safety apparatus has also been applied to some of the large hoists so much into use in the great hotels and other establishments ; and Messrs. Hick have set one or two in the metropolis. The plan is simple enough, and bears on the face of it a stamp of satisfactory efficiency. The broad principle upon which the safety cage relies for its action when the rope breaks may be said to consist in employing the weight of the tackle used to attach the rope to the cage to bring the safety catches into operation. Upon each side of the guide rods are two levers, turning on hinges upon forks fixed in the hoist or cage. The longer ends of the levers are jointed in connecting links, attached to link to which is secured the winding rope. The whole weight of the cage is carried in the pins of the levers, the longer ends of which are also drawn up the rope, while the shorter ends are also necessarily at the same time kept away from the guide rods. Should the rope break the links and other parts also fall down, causing the short ends of the levers to catch against the guides, and this action is also quickened by means of springs placed in the long ends of the levers. These springs also in a great measure carry out the important functions of drawsprings between the rope and the cage, preventing those injurious jerks which quickly wear away the rope, more especially at the portion immediately adjacent to the cage. held that both safety and economy—generally convertible terms—should always lead to the addition of an elastic attachment between the cage and wire rope—more especially pits worked quick speed. The engravings show the invention as applied by Messrs. Hick and Son to a hoist for mill or similar building.
'After having been making so many large stationary engines for such a number of years, being in the centre of the cotton districts, where, especially for driving machines for spinning fine numbers, very regularly working engines are absolutely required, it was natural that the Bolton firm should direct all its skill to producing a better governor than the old centrifugal ball governor introduced by James Watt. Into the wide question of the best means of getting regular a number of turns out of an engine it would not suit our present purpose to enter; but mechanics need scarcely be reminded that Watt’s ball governor is defective in several respects. Many experiments have been made at the Bolton Soho Works with a view to introducing a better instrument, and the greater number of the mechanical schemes brought forward at different times have been successively tried. Some nine years ago, we remember that Siemens’ isochronous governor was tried here, but apparently without lasting success. A new form of engine governor is now being made by Mr. Hick, and one of which is very successfully regulating the large engine, which drives the tool and turning shops. It has been patented by Mr. Standfield, and though its general principle is scarcely novel, it doubtless embodies patentable practical details. The inventor also proposes to employ it for a marine engine governor, great numbers of which are now in demand, the necessity for and advantages of attaching a governor to a marine engine are now generally understood by shipowners. Its general principle — which, as we have said, it has been more than once previously attempted to practically apply — consists in employing the resistance afforded to the motion of fan or disc in a liquid, or even fluid, enclosed in case. The liquid may evidently be also revolved in the case against the blades. At a certain determinate speed this resistance is, of course, constant, and a variation may, by easy means, be once brought to act on the throttle valve. An advantage is doubtless the easy means of setting the instrument by moving the weight up the graduated lever. Any variation in speed either raises or depresses the weighted lever out of its normal position, which, in its turn, then alters the throttle valve to which it is connected by any of the ordinary means. The illustrative engravings accompanying the paper add much to its value, as the principle and action of the different machines are thus made clearly intelligible.'
A History of The Firm
From 'Short Histories of Famous Firms' by Ernest Leopold Ahrons The Engineer - 1920/07/30.
Locomotives Built by Messrs B. Hick and Son, Bolton
After leaving Messrs Rothwell, Hick and Rothwell, Mr B. Hick began to build locomotives at his new works. The earliest engines constructed by him appear to have been seven four-wheeled passenger engines for the London and Birmingham Railway, to the orders of Edward Bury. The first engine of this order was recorded by the railway company as having been delivered in July, 1837, and the remainder in 1838. Much of the earliest locomotive work of the firm was devoted to Bury’s type of engines, and most of them were built to Bury’s orders and designs, and had the standard dimensions then adopted by that engineer, with 5ft. 6in. “single” drivers and 12in. by 18 in. cylinders. Four of the type were delivered by Messrs Hick to the North Union Railway, in 1838-9, nine to the Midland Counties Railway, 1840-1, one to the Manchester and Leeds Railway, 1841, and three more to the London and Birmingham Railway in the same year.
Hick, Hargreaves and Co
The Period 1830-50 was one of singular importance for the engineering industry of this country, and in its history Lancashire engineers played a very great part. Situated as it is in the midst of coal mines and cotton mills, it is not surprising that the town of Bolton became a centre of mechanical engineering. The name of “Hick” was probably as famous in Bolton as “Whitworth” in Manchester, “Maudslay” in Lambeth, or “Tangye” in Birmingham. It was Benjamin Hick who started the Soho Ironworks at Bolton in 1832. He had previously been in partnership in the firm of Hick and Rothwell, who owned the Union Foundry in the same town – a firm which is no longer in existence, having been absorbed many years ago by the Bolton Iron and Steel Company, which in turn was taken over by Henry Bessemer and Co in 1906.
Benjamin Hick with his two sons John and Benjamin, began business as general engineers at the Soho Works with the title of B. Hick and Sons.