1960 Institution of Mechanical Engineers: Visits to Works
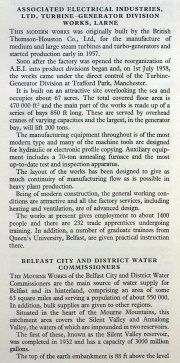
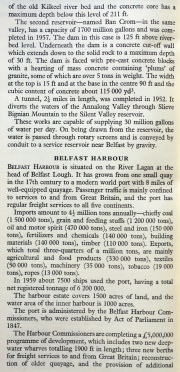
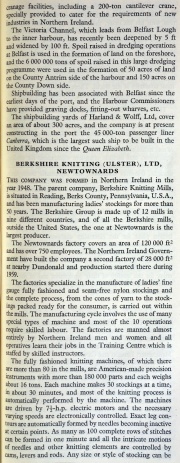
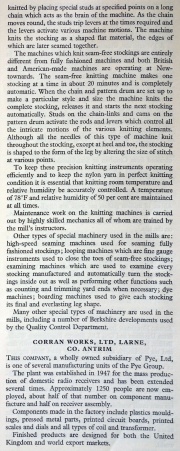
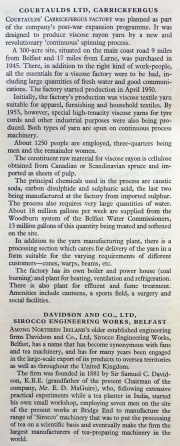

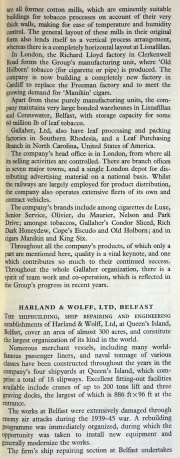
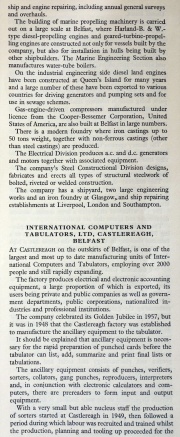
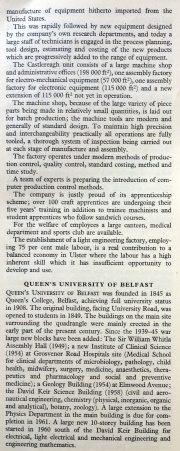
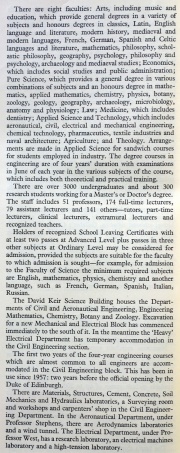
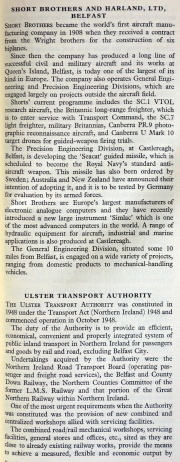
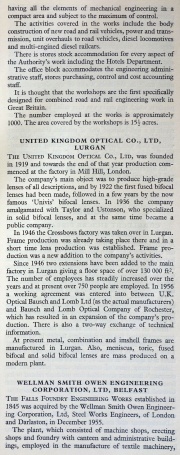
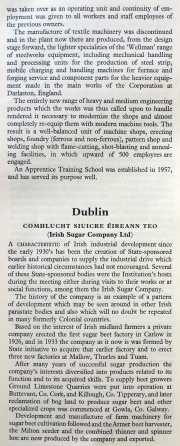
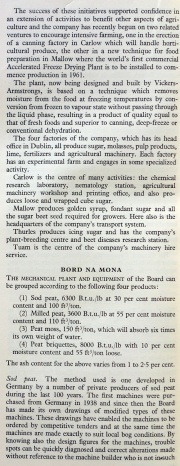
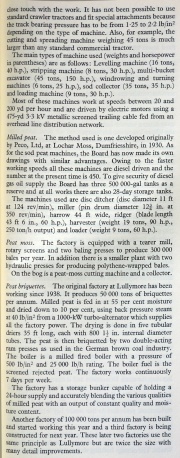
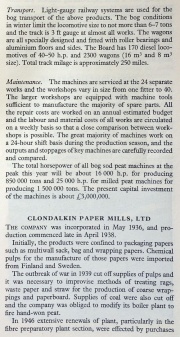
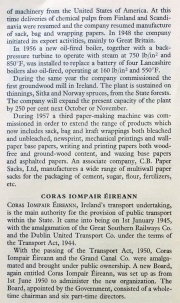
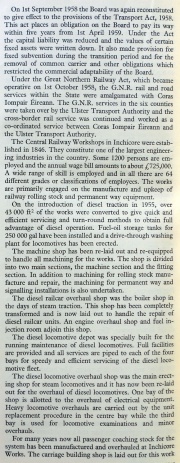
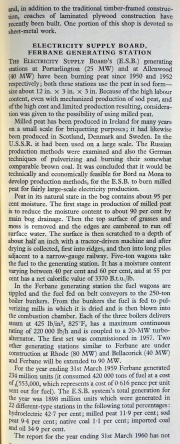
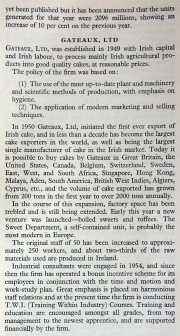
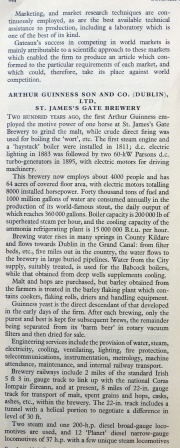
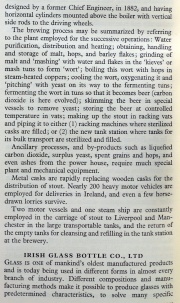
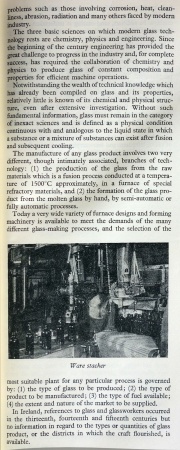
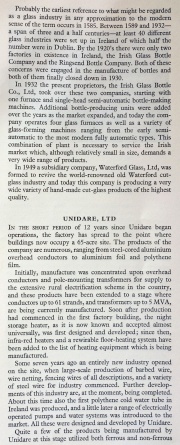

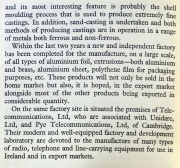
Note: This is a sub-section of 1960 Institution of Mechanical Engineers
ASSOCIATED ELECTRICAL INDUSTRIES, LTD, TURBINE-GENERATOR DIVISION WORKS, LARNE
AEI Ltd
This modern works was originally built by the British Thomson-Houston Co., Ltd, for the manufacture of medium and large steam turbines and turbo-generators and started production early in 1957.
Soon after the factory was opened the reorganization of A.E.I. into product divisions began and, on 1st July 1958, the works came under the direct control of the Turbine-Generator Division at Trafford Park, Manchester.
It is built on an attractive site overlooking the sea and occupies about 67 acres. The total covered floor area is 470,000 sq ft, and the main part of the works is made up of a series of bays 850 ft long. These are served by overhead cranes of varying capacities and the largest, in the generator bay, will lift 200 tons.
The manufacturing equipment throughout is of the most modern type and many of the machine tools are designed for hydraulic or electronic profile copying. Auxiliary equipment includes a 70-ton annealing furnace and the most up-to-date test and inspection apparatus.
The layout of the works has been designed to give as much continuity of manufacturing flow as is possible in heavy plant production.
Being of modern construction, the general working conditions are attractive and all the factory services, including heating and ventilation, are of advanced design.
The works at present gives employment to about 1400 people and there are 232 trade apprentices undergoing training. In addition, a number of graduate trainees from Queen's University, Belfast, are given practical instruction there.
BELFAST CITY AND DISTRICT WATER COMMISSIONERS
The Mourne Works of the Belfast City and District Water Commissioners are the main source of water supply for Belfast and its hinterland, comprising an area of some 63 square miles and serving a population of about 550,000. In addition, bulk supplies are given to other regions.
Situated in the heart of the Mourne Mountains, this catchment area covers the Silent Valley and Annalong Valley, the waters of which are impounded in two reservoirs.
The first of these, known as the Silent Valley reservoir, was completed in 1932 and has a capacity of 3,000 million gallons.
The top of the earth embankment is 88 ft above the level of the old Kilkeel river bed and the concrete core has a maximum depth below this level of 211 ft.
The second reservoir - named Ban Crom - in the same valley, has a capacity of 1700 million gallons and was completed in 1957. The dam in this case is 125 ft above riverbed level. Underneath the dam is a concrete cut-off wall which extends down to the solid rock to a maximum depth of 30 ft. The dam is faced with pre-cast concrete blocks with a hearting of mass concrete containing 'plums' of granite, some of which are over 5 tons in weight. The width at the top is 15 ft and at the base in the centre 90 ft and the cubic content of concrete about 115,000 cu yd.
A tunnel, 2.5 miles in length, was completed in 1952. It diverts the waters of the Annalong Valley through Slieve Bignian Mountain to the Silent Valley reservoir.
These works are capable of supplying 30 million gallons of water per day. On being drawn from the reservoir, the water is passed through rotary screens and is conveyed by conduit to a service reservoir near Belfast by gravity.
BELFAST HARBOUR
Belfast Harbour is situated on the River Lagan at the head of Belfast Lough. It has grown from one small quay in the 17th century to a modern world port with 8 miles of well-equipped quayage. Passenger traffic is mainly confined to services to and from Great Britain, and the port has regular freight services to all five continents.
Imports amount to 44 million tons annually - chiefly coal (1,500,000 tons), grain and feeding stuffs (1,200,000 tons), oil and motor spirit (470,000 tons), steel and iron (150,000 tons), fertilizers and chemicals (140,000 tons), building materials (140,000 tons), timber (110,000 tons). Exports, which total three-quarters of a million tons, are mainly agricultural and food products (330,000 tons), textiles (50,000 tons), machinery (35,000 tons), tobacco (19,000 tons), ropes (13,000 tons).
In 1959 about 7500 ships used the port, having a total net registered tonnage of 6,200,000.
The harbour estate covers 1,500 acres of land, and the water area of the inner harbour is 1,000 acres.
The port is administered by the Belfast Harbour Commissioners, who were established by Act of Parliament in 1847.
The Harbour Commissioners are completing a £5,000,000 programme of development, which includes two new deep-water wharves totalling 1900 ft in length; three new berths for freight services to and from Great Britain; reconstruction of older quayage, and the provision of additional cranage facilities, including a 200-ton cantilever crane, specially provided to cater for the requirements of new industries in Northern Ireland.
The Victoria Channel, which leads from Belfast Lough to the inner harbour, has recently been deepened by 5 ft and widened by 100 ft. Spoil raised in dredging operations at Belfast is used in the formation of land on the foreshore, and the 6,000,000 tons of spoil raised in this large dredging programme were used in the formation of 50 acres of land on the County Antrim side of the harbour and 150 acres on the County Down side.
Shipbuilding has been associated with Belfast since the earliest days of the port, and the Harbour Commissioners have provided graving docks, fitting-out wharves, etc.
The shipbuilding yards of Harland & Wolff, Ltd, cover an area of about 300 acres, and the company is at present constructing in the port the 45,000-ton passenger liner Canberra, which is the largest such ship to be built in the United Kingdom since the Queen Elizabeth.
BERKSHIRE KNITTING (ULSTER), LTD, NEWTOWNARDS
Berkshire Knitting (Ulster) Ltd
This company was formed in Northern Ireland in the year 1948. The parent company, Berkshire Knitting Mills, is situated in Reading, Berks County, Pennsylvania, U.S.A., and has been manufacturing ladies' stockings for more than 50 years. The Berkshire Group is made up of 12 mills in nine different countries, and of all the Berkshire mills, outside the United States, the one at Newtownards is the largest producer.
The Newtownards factory covers an area of 120,000 sq ft and has over 750 employees. The Northern Ireland Government have built the company a second factory of 28,000 sq ft at nearby Dundonald and production started there during 1959.
The factories specialize in the manufacture of ladies' fine gauge fully fashioned and seam-free nylon stockings and the complete process, from the cones of yarn to the stockings packed ready for the consumer, is carried out within the mills. The manufacturing cycle involves the use of many special types of machine and most of the 10 operations require skilled labour. The factories are manned almost entirely by Northern Ireland men and women and all operatives learn their jobs in the Training Centre which is staffed by skilled instructors.
The fully fashioned knitting machines, of which there are more than 80 in the mills, are American-made precision instruments with more than 180,000 parts and each weighs about 16 tons. Each machine makes 30 stockings at a time, in about 30 minutes, and most of the knitting process is automatically performed by the machine. The machines are driven by 7.5-h.p. electric motors and the necessary varying speeds are electronically controlled. Exact leg contours are automatically formed by needles becoming inactive at certain points. As many as 100 complete rows of stitches can be formed in one minute and all the intricate motions of needles and other knitting elements are controlled by cams, levers and rods. Any size or style of stocking can be knitted by placing special studs at specified points on a long chain which acts as the brain of the machine. As the chain moves round, the studs trip levers at the times required and the levers activate various machine motions. The machine knits the stocking as a shaped flat material, the edges of which are later seamed together.
The machines which knit seam-free stockings are entirely different from fully fashioned machines and both British. and American-made machines are operating at Newtownards. The seam-free knitting machine makes one stocking at a time in about 20 minutes and is completely automatic. When the chain and pattern drum are set up to make a particular style and size the machine knits the complete stocking, releases it and starts the next stocking automatically. Studs on the chain-links and cams on the pattern drum activate the rods and levers which control all the intricate motions of the various knitting elements. Although all the needles of this type of machine knit throughout the stocking, except at heel and toe, the stocking is shaped to the form of the leg by altering the size of stitch at various points.
To keep these precision knitting instruments operating efficiently and to keep the nylon yarn in perfect knitting condition it is essential that knitting room temperature and relative humidity be accurately controlled. A temperature of 78°F and relative humidity of 50 per cent are maintained at all times.
Maintenance work on the knitting machines is carried out by highly skilled mechanics all of whom are trained by the mill's instructors.
Other types of special machinery used in the mills are: high-speed seaming machines used for seaming fully fashioned stockings; looping machines which are fine gauge instruments used to close the toes of seam-free stockings; examining machines which are used to examine every stocking manufactured and automatically turn the stockings inside out as well as performing other functions such as counting and trimming yard ends when necessary; dye machines; boarding machines used to give each stocking its final and everlasting leg shape.
Many other special types of machinery are used in the mills, including a number of Berkshire developments used by the Quality Control Department.
CORRAN WORKS, LTD, LARNE, CO. ANTRIM
Pye Ltd
This company, a wholly owned subsidiary of Pye, Ltd, is one of several manufacturing units of the Pye Group.
The plant was established in 1947 for the mass production of domestic radio receivers and has been extended several times. Approximately 1250 people are now employed, about half of that number on component manufacture and half on receiver assembly.
Components made in the factory include plastics mouldings, pressed metal parts, printed circuit boards, printed scales and dials and all types of coil and transformer.
Finished products are designed for both the United Kingdom and world export markets.
COURTAULDS LTD, CARRICKFERGUS
Courtaulds Ltd
Courtauld’s Carrickfergus factory was planned as part of the company's post-war expansion programme. It was designed to produce viscose rayon yarn by a new and revolutionary 'continuous' spinning process.
A 300-acre site, situated on the main coast road 9 miles from Belfast and 17 miles from Larne, was purchased in 1945. There, in addition to the right kind of work-people, all the essentials for a viscose factory were to be had, including large quantities of fresh water and good communications. The factory started production in April 1950.
Initially, the factory's production was viscose textile yarn suitable for apparel, furnishing and household textiles. By 1953, however, special high-tenacity viscose yarns for tyre cords and other industrial purposes were also being produced. Both types of yarn are spun on continuous process machinery.
About 1,250 people are employed, three-quarters being men and the remainder women.
The constituent raw material for viscose rayon is cellulose obtained from Canadian or Scandinavian spruce and imported as sheets of pulp.
The principal chemicals used in the process are caustic soda, carbon disulphide and sulphuric acid, the last two being manufactured at the factory from imported sulphur. The process also requires very large quantities of water. About 18 million gallons per week are supplied from the Woodburn system of the Belfast Water Commissioners, 13 million gallons of this quantity being treated and softened on the site.
In addition to the yarn manufacturing plant, there is a processing section which caters for delivery of the yarn in a form suitable for the varying requirements of different customers — cones, warps, beams, etc.
The factory has its own boiler and power house (coal burning) and plant for heating, ventilation and refrigeration. There is also plant for effluent and fume treatment. Amenities include canteens, a sports field, a surgery and social facilities.
DAVIDSON AND CO., LTD, SIROCCO ENGINEERING WORKS, BELFAST
Davidson and Co Ltd
Among Northern Ireland’s older established engineering firms Davidson and Co., Ltd, Sirocco Engineering Works, Belfast, has a name that has become synonymous with fans and tea machinery, and has for many years been engaged in the large-scale export of its products to overseas territories as well as throughout the United Kingdom.
The firm was founded in 1881 by Sir Samuel C. Davidson, K.B.E. (grandfather of the present Chairman of the company, Mr. E. D. MaGuire), who, following extensive practical experiments while a tea planter in India, started his own small workshop, employing seven men on the site of the present works at Bridge End to manufacture the range of 'Sirocco' machinery that was to put the processing of tea on a scientific basis and eventually make the firm the largest manufacturers of tea-preparing machinery in the world.
From his subsequent invention of the 'Sirocco' centrifugal fan, which he initially developed to work in conjunction with his tea drier, there grew up another important side of the firm's activities embracing fans for mines, power stations, ships, and industrial requirements generally.
The company has grown steadily in importance, and its Belfast works now cover 12 acres and give employment to 1200 men. Abroad, there are subsidiary companies in South Africa, India and Australia, a large depot in Ceylon, and numerous agents representing 'Sirocco' interests in most countries of the world. There are fully staffed Branch Offices in London, Manchester, Birmingham, Newcastle, Leeds, and Glasgow.
The company not only makes machines for every stage in the preparation of the tea leaf, but also undertakes the design, manufacture and supply of tea factory buildings, while on the fan engineering side 'Sirocco' products find application in every field of industry, from the ventilating of coal mines to the installation of full-scale air-conditioning equipment, and include complete equipment for cooling, drying, dust collecting, heating and ventilating, mechanical draught, flue-dust collection, and pneumatic conveyance. A recent extension of the company's activities has been the establishment of a Nuclear Power Department, largely specializing in the design and manufacture of sealed gas blowers.
The company has for many years been among the main providers of mine ventilating fans for the British coal industry and of mechanical draught fans and flue dust collection plant for the electricity authorities. Many large overseas contracts for such equipment have also been secured in the face of strong competition.
Founded on a pioneering tradition, Davidson and Co., Ltd, are rightly proud of the world-wide reputation they enjoy for the quality of their equipment and of the consistently important part they have played for many years in Northern Ireland's economy.
GALLAHER, LTD
Gallaher Ltd
In 1857 Thomas Gallaher started making and selling twist tobacco in Londonderry, and from that small beginning has grown the present company with over 12,000 employees in the Group, and factories in Northern Ireland, Manchester, London and Cardiff.
In 1959 the company opened at Lisnafillan in Northern Ireland a factory which is one of the biggest and most up to date of its kind in the world. There are two main buildings, the larger being 900 ft long and 105 ft wide, there being no interior roof supports or pillars to interfere with the layout of machinery or processes. The roof beams, which were precast in sections on site, are used to carry ventilation ducts and other services.
As the processes used in the manufacture of cigarettes and tobacco require very strict humidity control within the factory, air conditioning is used in this and the company's other factories. In the Manchester area, the company's three factories - at Ashton, Middleton and Hyde - are all former cotton mills, which are eminently suitable buildings for tobacco processes on account of their very thick walls, making for ease of temperature and humidity control. The general layout of these mills in their original form also lends itself to a vertical process arrangement, whereas there is a completely horizontal layout at Lisnafillan. In London, the Richard Lloyd factory in Clerkenwell Road forms the Group's manufacturing unit, where 'Old Holborn' tobacco (for cigarette or pipe) is produced. The company is now building a completely new factory in Cardiff to replace the Freeman factory and to meet the growing demand for 'Manikin' cigars.
Apart from these purely manufacturing units, the company maintains very large bonded warehouses in Lisnafillan and Connswater, Belfast, with storage capacity for some 60 million lb of leaf tobacco.
Gallaher, Ltd, also have leaf processing and packing factories in Southern Rhodesia, and a Leaf Purchasing Branch in North Carolina, United States of America.
The company's head office is in London, from where all its selling activities are controlled. There are branch offices in seven major towns, and a single London depot for distributing advertising material on a national basis. Whilst the railways are largely employed for product distribution, the company also operates extensive fleets of its own and contract vehicles.
The company's brands include among cigarettes de Luxe, Senior Service, Olivier, du Maurier, Nelson and Park Drive; amongst tobaccos, Gallaher's Condor Sliced, Rich Dark Honeydew, Cope's Escudo and Old Holborn; and in cigars Manikin and King Six.
Throughout all the company's products, of which only a part are mentioned here, quality is a vital keynote, and one which contributes so much to their continued success. Throughout the whole Gallaher organization, there is a spirit of team work and co-operation, which is reflected in the Group's progress in recent years.
HARLAND & WOLFF, LTD, BELFAST
The shipbuilding, ship repairing and engineering establishments of Harland & Wolff, Ltd, at Queen's Island, Belfast, cover an area of almost 300 acres, and constitute the largest organization of its kind in the world.
Numerous merchant vessels, including many world-famous passenger liners, and naval tonnage of various classes have been constructed throughout the years in the company's four shipyards at Queen's Island, which comprise a total of 18 slipways. Excellent fitting-out facilities available include cranes of up to 200 tons lift and three graving docks, the largest of which is 886 ft x 96 ft at the entrance.
The works at Belfast were extensively damaged through enemy air attacks during the 1939-45 war. A rebuilding programme was immediately organized, during which the opportunity was taken to install new equipment and generally modernize the works.
The firm's ship repairing section at Belfast undertakes ship and engine repairing, including annual general surveys and overhauls.
The building of marine propelling machinery is carried out on a large scale at Belfast, where Harland-B. & W.type diesel-propelling engines and geared-turbine-propelling engines are constructed not only for vessels built by the company, but also for installation in hulls being built by other shipbuilders. The Marine Engineering Section also manufactures water-tube boilers.
On the industrial engineering side diesel land engines have been constructed at Queen's Island for many years and a large number of these have been exported to various countries for driving generators and pumping sets and for use in sewage schemes.
Gas-engine-driven compressors manufactured under licence from the Cooper-Bessemer Corporation, United States of America, are also built at Belfast in large numbers.
There is a modern foundry where iron castings up to 50 tons weight, together with non-ferrous castings (other than steel castings) are produced.
The Electrical Division produces a.c. and d.c. generators and motors together with associated equipment.
The company's Steel Constructional Division designs, fabricates and erects all types of structural steelwork of bolted, riveted or welded construction.
The company has a shipyard, two large engineering works and an iron foundry at Glasgow, and ship repairing establishments at Liverpool, London and Southampton.
INTERNATIONAL COMPUTERS AND TABULATORS, LTD, CASTLEREAGH, BELFAST
International Computers and Tabulators Ltd
At Castlereagh on the outskirts of Belfast, is one of the largest and most up to date manufacturing units of International Computers and Tabulators, employing over 2,000 people and still rapidly expanding.
The factory produces electrical and electronic accounting equipment, a large proportion of which is exported, its users being private and public companies as well as government departments, public corporations, nationalized industries and professional institutions.
The company celebrated its Golden Jubilee in 1957, but it was in 1948 that the Castlereagh factory was established to manufacture the ancillary equipment to the tabulator.
It should be explained that ancillary equipment is necessary for the rapid preparation of punched cards before the tabulator can list, add, summarize and print final lists or tabulations.
The ancillary equipment consists of punches, verifiers, sorters, collators, gang punches, reproducers, interpreters and, in conjunction with electronic calculators and computers, there are prereaders to form input and output equipment.
With a very small but able nucleus staff the production of sorters started at Castlereagh in 1949, then followed a period during which labour was recruited and trained whilst the production, planning and tooling up proceeded for the manufacture of equipment hitherto imported from the United States.
This was rapidly followed by new equipment designed by the company's own research departments, and today a large staff of technicians is engaged in the process planning, tool design, estimating and costing of the new products which are progressively added to the range of equipment.
The Castlereagh unit consists of a large machine shop and administrative offices (198,000 sq ft), one assembly factory for electro-mechanical equipment (57,000 sq ft), one assembly factory for electronic equipment (115,000 sq ft) and a new extension of 115,000 sq ft not yet in operation.
The machine shop, because of the large variety of piece parts being made in relatively small quantities, is laid out for batch production; the machine tools are modern and generally of standard design. To maintain high precision and interchangeability practically all operations are fully tooled, a thorough system of inspection being carried out at each stage of manufacture and assembly.
The factory operates under modern methods of production control, quality control, standard costing, method and time study.
A team of experts is preparing the introduction of computer production control methods.
The company is justly proud of its apprenticeship scheme; over 100 craft apprentices are undergoing their five years' training in addition to trainee machinists and student apprentices who follow sandwich courses.
For the welfare of employees a large canteen, medical department and sports dub are available.
The establishment of a light engineering factory, employing 75 per cent male labour, is a real contribution to a balanced economy in Ulster where the labour has a high inherent skill which it has insufficient opportunity to develop and use.
QUEEN'S UNIVERSITY OF BELFAST
Queen’s University of Belfast was founded in 1845 as Queen's College, Belfast, achieving full university status in 1908. The original building, facing University Road, was opened to students in 1849. The buildings on the main site surrounding the quadrangle were mainly erected in the early part of the present century. Since the 1939-45 war large new blocks have been added: The Sir William Whitla Assembly Hall (1949); a new Institute of Clinical Science (1954) at Grosvenor Road Hospitals site (Medical School for clinical departments of microbiology, pathology, child health, midwifery, surgery, medicine, anaesthetics, therapeutics and pharmacology and social and preventive medicine); a Geology Building (1954) at Elmwood Avenue; the David Keir Science Building (1958) (civil and aeronautical engineering, chemistry (physical, inorganic, organic and analytical), botany, zoology). A large extension to the Physics Department in the main building is due for completion in 1961. A large new 10-storey building has been started in 1960 south of the David Keir Building for electrical, light electrical and mechanical engineering and engineering mathematics.
There are eight faculties: Arts, including music and education, which provide general degrees in a variety of subjects and honours degrees in classics, Latin, English language and literature, modern history, mediaeval and modern languages, French, German, Spanish and Celtic languages and literature, mathematics, philosophy, scholastic philosophy, geography, psychology, philosophy and psychology, archaeology and mediaeval studies; Economics, which includes social studies and public administration; Pure Science, which provides a general degree in various combinations of subjects and an honours degree in mathematics, applied mathematics, chemistry, physics, botany, zoology, geology, geography, archaeology, microbiology, anatomy and physiology; Law; Medicine, which includes dentistry; Applied Science and Technology, which includes aeronautical, civil, electrical and mechanical engineering, chemical technology, pharmaceutics, textile industries and naval architecture; Agriculture; and Theology. Arrangements are made in Applied Science for sandwich courses for students employed in industry. The degree courses in engineering are of four years' duration with examinations in June of each year in the various subjects of the course, which includes both theoretical and practical training.
There are over 3,000 undergraduates and about 300 research students working for a Master's or Doctor's degree. The staff includes 51 professors, 174 full-time lecturers, 79 assistant lecturers and 141 others — tutors, part-time lecturers, clinical lecturers, extramural lecturers and recognized teachers.
Holders of recognized School Leaving Certificates with at least two passes at Advanced Level plus passes in three other subjects at Ordinary Level may be considered for admission, provided the subjects are suitable for the faculty to which admission is sought — for example, for admission to the Faculty of Science the minimum required subjects are English, mathematics, physics, chemistry and another language, such as French, German, Spanish, Italian, Russian.
The David Keir Science Building houses the Departments of Civil and Aeronautical Engineering, Engineering Mathematics, Chemistry, Botany and Zoology. Excavation for a new Mechanical and Electrical Block has commenced immediately to the south of it. In the meantime the 'Heavy' Electrical Department has temporary accommodation in the Civil Engineering section.
The first two years of the four-year engineering courses which are almost common to all engineers are accommodated in the Civil Engineering block. This has been in use since 1957: two years before the official opening by the Duke of Edinburgh.
There are Materials, Structures, Cement, Concrete, Soil Mechanics and Hydraulics laboratories, a Surveying room and workshops and carpenters' shop in the Civil Engineering Department. In the Aeronautical Department, under Professor Stephens, there are Aerodynamics laboratories and a wind tunnel. The Electrical Department, under Professor West, has a research laboratory, an electrical machines laboratory and a high-tension laboratory.
SHORT BROTHERS AND HARLAND, LTD, BELFAST
Short Brothers and Harland Ltd
Short Brothers became the world's first aircraft manufacturing company in 1908 when they received a contract from the Wright brothers for the construction of six biplanes.
Since then the company has produced a long line of successful civil and military aircraft and its works at Queen's Island, Belfast, is today one of the largest of its kind in Europe. The company also operates General Engineering and Precision Engineering Divisions, which are engaged largely on projects outside the aircraft field. Shorts' current programme includes the SC.1 VTOL research aircraft, the Britannic long-range freighter, which is to enter service with Transport Command, the SC7 light freighter, military Britannias, Canberra PR.9 photographic reconnaissance aircraft, and Canberra U Mark 10 target drones for guided-weapon firing trials.
The Precision Engineering Division, at Castlereagh, Belfast, is developing the 'Seacat' guided missile, which is scheduled to become the Royal Navy's standard antiaircraft weapon. This missile has also been ordered by Sweden; Australia and New Zealand have announced their intention of adopting it, and it is to be tested by Germany for evaluation by its armed forces.
Short Brothers are Europe's largest manufacturers of electronic analogue computers and they have recently introduced a new large instrument 'Simlac' which is one of the most advanced computers in the world. A range of hydraulic equipment for aircraft, industrial and marine applications is also produced at Castlereagh.
The General Engineering Division, situated some 10 miles from Belfast, is engaged on a wide variety of projects, ranging from domestic products to mechanical-handling vehicles.
ULSTER TRANSPORT AUTHORITY
The Ulster Transport Authority was constituted in 1948 under the Transport Act (Northern Ireland) 1948 and commenced operation in October 1948.
The duty of the Authority is to provide an efficient, economical, convenient and properly integrated system of public inland transport in Northern Ireland for passengers and goods by rail and road, excluding Belfast City. Undertakings acquired by the Authority were the Northern Ireland Road Transport Board (operating passenger and freight road services), the Belfast and County Down Railway, the Northern Counties Committee of the former L.M.S. Railway and that portion of the Great Northern Railway within Northern Ireland.
One of the most urgent requirements when the Authority was constituted was the provision of new combined and centralized workshops allied with servicing facilities.
The combined road/rail mechanical workshops, servicing facilities, general stores and offices, etc., sited as they are close to already existing railway works, provide the means to achieve a measured, flexible and economic output by having all the elements of mechanical engineering in a compact area and subject to the maximum of control.
The activities covered in the works include the body construction of new road and rail vehicles, power and transmission, unit overhauls to road vehicles, diesel locomotives and multi-engined diesel railcars.
There is stores stock accommodation for every aspect of the Authority's work including the Hotels Department.
The office block accommodates the engineering administrative staff, stores purchasing, control and cost accounting staff.
It is thought that the workshops are the first specifically designed for combined road and rail engineering work in Great Britain.
The number employed at the works is approximately 1,000. The area covered by the workshops is 15.5 acres.
UNITED KINGDOM OPTICAL CO., LTD, LURGAN
The United Kingdom Optical Co., Ltd, was founded. in 1919 and towards the end of that year production commenced at the factory in Mill Hill, London.
The company's main object was to produce high-grade lenses of all descriptions, and by 1922 the first fused bifocal lenses had been made, followed in a few years by the now famous 'Univis' bifocal lenses. In 1936 the company amalgamated with Taylor and Ustonson, who specialized in solid bifocal lenses, and at the same time became a public company.
In 1946 the Crossbows factory was taken over in Lurgan. Frame production was already taking place there and in a short time lens production was established. Frame production was a new addition to the company's activities.
Since 1946 two extensions have been added to the main factory in Lurgan giving a floor space of over 130,000 sq ft. The number of employees has steadily increased over the years and at present over 750 people are employed. In 1956 a working agreement was entered into between U.K. Optical Bausch and Lomb Ltd (as the actual manufacturers) and Bausch and Lomb Optical Company of Rochester, which has resulted in an expansion of the company's production. There is also a two-way exchange of technical information.
At present metal, combination and imshell frames are manufactured in Lurgan. Also, meniscus, toric, fused bifocal and solid bifocal lenses are mass produced on a modern plant.
WELLMAN SMITH OWEN ENGINEERING CORPORATION, LTD, BELFAST
Wellman, Smith, Owen Engineering Corporation Ltd
The Falls Foundry Engineering Works established in 1845 was acquired by the Wellman Smith Owen Engineering Corporation, Ltd, Steel Works Engineers, of London and Darlaston, in December 1955.
The plant, which consisted of machine shops, erecting shops and foundry with canteen and administrative buildings, employed in the manufacture of textile machinery, was taken over as an operating unit and continuity of employment was given to all workers and staff employees of the previous owners.
The manufacture of textile machinery was discontinued and in the plant now there are produced, from the design stage forward, the lighter specialities of the 'Wellman' range of steelworks equipment, including mechanical handling and processing units for the production of steel strip, mobile charging and handling machines for furnace and forging service and component parts for the heavier equipment made in the main works of the Corporation at Darlaston, England.
The entirely new range of heavy and medium engineering products which the works was thus called upon to handle rendered it necessary to modernize the shops and almost completely re-equip them with modern machine tools. The result is a well-balanced unit of machine shops, erecting shops, foundry (ferrous and non-ferrous), pattern shop and welding shop with flame-cutting, shot-blasting and annealing facilities, in which upward of 500 employees are engaged.
An Apprentice Training School was established in 1957, and has served its purpose well.
DUBLIN
COMHLUCHT SIUICRE EIREANN TEO (Irish Sugar Company Ltd)
Irish Sugar Co Ltd
A Characteristic of Irish industrial development since the early 1930's has been the creation of State-sponsored boards and companies to supply the industrial drive which earlier historical circumstances had not encouraged. Several of these State-sponsored bodies were the Institution's hosts during the meeting either during visits to their works or at social functions, among them the Irish Sugar Company.
The history of the company is an example of a pattern of development which may be seen around in other Irish parastate bodies and also which will no doubt be repeated in many formerly Colonial countries.
Based on the interest of Irish midland farmers a private company erected the first sugar beet factory in Carlow in 1926, and in 1933 the company as it now is was formed by State initiative to acquire that earlier factory and to erect three new factories at Mallow, Thurles and Tuam.
After many years of successful sugar production the company's interests diversified into products related to its function and to its acquired skills. To supply beet growers Ground Limestone Quarries were put into operation at Buttevant, Co. Cork, and Killough, Co. Tipperary, and later reclamation of bog land to produce sugar beet and other specialized crops was commenced at Gowla, Co. Galway.
Development and manufacture of farm machinery for sugar beet cultivation followed and the Armer beet harvester, the Milton seeder and the combined thinner and spinner hoe are now produced by the company and exported.
The success of these initiatives supported confidence in an extension of activities to benefit other aspects of agriculture and the company has recently begun on two related ventures to encourage intensive farming, one in the erection of a canning factory in Carlow which will handle horticultural produce, the other in a new technique for food preparation in Mallow where the world's first commercial Accelerated Freeze Drying Plant is to be installed to commence production in 1961.
The plant, now being designed and built by Vickers-Armstrongs, is based on a technique which removes moisture from the food at freezing temperatures by conversion from frozen to vapour state without passing through the liquid phase, resulting in a product of quality equal to that of fresh foods and superior to canning, deep-freeze or conventional dehydration.
The four factories of the company, which has its head office in Dublin, all produce sugar, molasses, pulp products, lime, fertilizers and agricultural machinery. Each factory has an experimental farm and engages in some specialized activity.
Carlow is the centre of many activities: the chemical research laboratory, nematology station, agricultural machinery workshop and printing office, and also produces loose and wrapped cube sugar.
Mallow produces golden syrup, fondant sugar and all the sugar beet seed required for growers. Here also is the headquarters of the company's transport system.
Thurles produces icing sugar and has the company's plant-breeding centre and beet diseases research station.
Tuam is the centre of the company's machinery hire service.
BORD NA MONA
The mechanical plant and equipment of the Board can be grouped according to the following four products:
(1) Sod peat, 6300 B.t.u./lb at 30 per cent moisture content and 100 cu ft/ton.
(2) Milled peat, 3600 B.t.u./lb at 55 per cent moisture content and 110 cu ft/ton.
(3) Peat moss, 150 cu ft/ton, which will absorb six times its own weight of water.
(4) Peat briquettes, 8000 B.t.u./lb with 10 per cent moisture content and 55 cu ft/ton loose.
The ash content for the above varies from 1 to 2.5 per cent.
Sod peat. The method used is one developed in Germany by a number of private producers of sod peat during the last 100 years. The first machines were purchased from Germany in 1938 and since then the Board has made its own drawings of modified types of these machines. These drawings have enabled the machines to be ordered by competitive tenders and at the same time the machines are made exactly to suit local bog conditions. By knowing also the design figures for the machines, trouble spots can be quickly diagnosed and correct alterations made without reference to the machine builder who is not in such close touch with the work. It has not been possible to use standard crawler tractors and fit special attachments because the track bearing pressure has to be from 1.25 to 2.2 lb/sq in depending on the type of machine. Also, for example, the cutting and spreading machine weighing 45 tons is much larger than any standard commercial tractor.
The main types of machine used (weights and horsepower in parentheses) are as follows: Levelling machine (16 tons, 40 h.p.), stripping machine (8 tons, 30 h.p.), multi-bucket excavator (45 tons, 150 h.p.), windrowing and turning machines (6 tons, 25 h.p.), sod collector (35 tons, 35 h.p.) and loading machine (9 tons, 30 h.p.).
Most of these machines work at speeds between 20 and 200 yd per hour and are driven by electric motors using a 475-yd 3.3 kV metallic screened trailing cable fed from an overhead line distribution network.
Milled peat. The method used is one developed originally by Peco, Ltd, at Lochar Moss, Dumfriesshire, in 1930. As for the sod peat machines, the Board has now made its own drawings with similar advantages. Owing to the faster working speeds all these machines are diesel driven and the number at the present time is 450. To give security of diesel gas oil supply the Board has three 500,000-gal tanks as a reserve and at all works there are also 28-day storage tanks.
The machines used are disc ditcher (disc diameter 11 ft at 124 rev/min), miller (pin drum diameter 12.75 in. at 350 rev/min), harrow 44 ft wide, ridger (blade length 43 ft 6 in., 60 h.p.), harvester (weight 19 tons, 90 h.p., 250 ton/h output) and loader (weight 9 tons, 60 h.p.).
Peat moss. The factory is equipped with a tearer mill, rotary screens and two baling presses to produce 300,000 bales per year. In addition there is a smaller plant with two hydraulic presses for producing polythene-wrapped bales.
On the bog is a peat-moss cutting machine and a collector.
Peat briquettes. The original factory at Lullymore has been working since 1938. It produces 50,000 tons of briquettes per annum. Milled peat is fed in at 55 per cent moisture and dried down to 10 per cent, using back pressure steam at 40 lb/sq in from a 1000-kW turbo-alternator which supplies all the factory power. The drying is done in five tubular driers 35 ft long, each with 800 1.5 in. internal diameter tubes. The peat is then briquetted by two double-acting ram presses as used in the German brown coal industry. The boiler is a milled fired boiler with a pressure of 500 lb/sq in and 25,000 lb/h rating. The boiler fuel is the screened rejected peat. The factory works continuously 7 days per week.
The factory has a storage bunker capable of holding a 24-hour supply and accurately blending the various qualities of milled peat with an output of constant quality and moisture content.
Another factory of 100,000 tons per annum has been built and started working this year and a third factory is being constructed for next year. These later two factories use the same principle as Lullymore but are twice the size with many detail improvements.
Transport. Light-gauge railway systems are used for the bog transport of the above products. The bog conditions in winter limit the locomotive size to not more than 6-7 tons and the track is 3 ft gauge at almost all works. The wagons are all specially designed and fitted with roller bearings and aluminium floors and sides. The Board has 170 diesel locomotives of 40-50 h.p. and 2300 wagons (16 cu m and 8 cu m size). Total track mileage is approximately 250 miles.
Maintenance. The machines are serviced at the 24 separate works and the workshops vary in size from one fitter to 40. The larger workshops are equipped with machine tools sufficient to manufacture the majority of spare parts. All the repair costs are worked on an annual estimated budget and the labour and material costs of all works are circulated on a weekly basis so that a close comparison between workshops is possible. The great majority of machines work on a 24-hour shift basis during the production season, and the outputs and stoppages of key machines are carefully recorded and compared.
The total horsepower of all bog sod peat machines at the peak this year will be about 16,000 h.p. for producing 850,000 tons and 25,000 h.p. for milled peat machines for producing 1 500,000 tons. The present capital investment of the machines is about £3,000,000.
CLONDALKIN PAPER MILLS, LTD
The company was incorporated in May 1936, and production commenced late in April 1938.
Initially, the products were confined to packaging papers such as multiwall sack, bag and wrapping papers. Chemical pulps for the manufacture of those papers were imported from Finland and Sweden.
The outbreak of war in 1939 cut off supplies of pulps and it was necessary to improvise methods of treating rags, waste paper and straw for the production of coarse wrappings and paperboard. Supplies of coal were also cut off and the company was obliged to modify its boiler plant to fire hand-won peat.
In 1946 extensive renewals of plant, particularly in the fibre preparatory plant section, were effected by purchases of machinery from the United States of America. At this time deliveries of chemical pulps from Finland and Scandinavia were resumed and the company resumed manufacture of sack, bag and wrapping papers. In 1948 the company initiated its export activities, mainly to Great Britain.
In 1956 a new oil-fired boiler, together with a backpressure turbine to operate with steam at 750 lb/sq in and 850°F, was installed to replace a battery of four Lancashire boilers also oil-fired, operating at 160 lb/sq in, and 550°F.
During the same year the company commissioned the first ground-wood mill in Ireland. The plant is sustained on thinnings, Sitka and Norway spruces, from the State forests. The company will expand the present capacity of the plant by 250 per cent next October or November.
During 1957 a third paper-making machine was commissioned in order to extend the range of products which now includes sack, bag and kraft wrappings both bleached and unbleached, newsprint, mechanical printings and wallpaper base papers, writing and printing papers both wood-free and ground-wood content, and waxing base papers and asphalted papers. An associate company, C. B. Paper Sacks, Ltd, manufactures a wide range of multiwall paper sacks for the packaging of cement, sugar, flour, fertilizers, etc.
CORAS IOMPAIR EIREANN
Coras Iompair Eireann, Ireland's transport undertaking, is the main authority for the provision of public transport within the State. It came into being on 1st January 1945, with the amalgamation of the Great Southern Railways Co. and the Dublin United Transport Co. under the terms of the Transport Act, 1944.
With the passing of the Transport Act, 1950, Coras Iompair Eireann and the Grand Canal Co. were amalgamated and brought under public ownership. A new Board, again entitled Coras Iompair Eireann, was set up as from 1st June 1950 to administer the new organization. The Board, appointed by the Government, consisted of a whole-time chairman and six part-time directors.
On 1st September 1958 the Board was again reconstituted to give effect to the provisions of the Transport Act, 1958. This act places an obligation on the Board to pay its way within five years from 1st April 1959. Under the Act the capital liability was reduced and the values of certain fixed assets were written down. It also made provision for fixed subvention during the transition period and for the removal of common carrier and other obligations which restricted the commercial adaptability of the Board.
Under the Great Northern Railway Act, which became operative on 1st October 1958, the G.N.R. rail and road services within the State were amalgamated with Coras Iompair Eireann. The G.N.R. services in the six counties were taken over by the Ulster Transport Authority and the cross-border rail service was continued and worked as a co-ordinated service between Coras Iompair Eireann and the Ulster Transport Authority.
The Central Railway Workshops in Inchicore were established in 1846. They constitute one of the largest engineering industries in the country. Some 1200 persons are employed and the annual wage bill amounts to about £725,000. A wide range of skill is employed and in all there are 64 different grades or classifications of employees. The works are primarily engaged on the manufacture and upkeep of railway rolling stock and permanent way equipment.
On the introduction of diesel traction in 1955, over 43,000 sq ft of the works were converted to give quick and efficient servicing and turn-round methods to obtain full advantage of diesel operation. Fuel-oil storage tanks for 250,000 gal have been installed and a drive-through washing plant for locomotives has been erected.
The machine shop has been re-laid out and re-equipped to handle all machining for the works. The shop is divided into two main sections, the machine section and the fitting section. In addition to machining for rolling stock manufacture and repair, the machining for permanent way and signalling installations is also undertaken.
The diesel railcar overhaul shop was the boiler shop in the days of steam traction. This shop has been completely transformed and is now laid out to handle the repair of diesel railcar units. An engine overhaul shop and fuel injection room adjoin this shop.
The diesel locomotive depot was specially built for the running maintenance of diesel locomotives. Full facilities are provided and all services are piped to each of the four bays for speedy and efficient servicing of the diesel locomotive fleet.
The diesel locomotive overhaul shop was the main erecting shop for steam locomotives and it has now been re-laid out for the overhaul of diesel locomotives. One bay of the shop is allotted to the overhaul of electrical equipment. Heavy locomotive overhauls are carried out by the unit replacement procedure in the centre bay while the third bay is used for locomotive examinations and minor overhauls.
For many years now all passenger coaching stock for the system has been manufactured and overhauled at Inchicore Works. The carriage building shop is laid out for this work and, in addition to the traditional timber-framed construction, coaches of laminated plywood construction have recently been built. One portion of this shop is devoted to sheet-metal work.
ELECTRICITY SUPPLY BOARD, FERBANE GENERATING STATION
The Electricity Supply Board’s (E.S.B.) generating stations at Portarlington (25 MW) and at Allenwood (40 MW) have been burning peat since 1950 and 1952 respectively; both these stations use the peat in sod form - size about 12 in. x 3 in. x 3 in. Because of the high labour content, even with mechanized production of sod peat, and of the high cost and limited production resulting, consideration was given to the possibility of using milled peat.
Milled peat has been produced in Ireland for many years on a small scale for briquetting purposes; it had likewise been produced in Scotland, Denmark and Sweden. In the U.S.S.R. it had been used on a large scale. The Russian production methods were examined and also the German techniques of pulverizing and burning their somewhat comparable brown coal. It was concluded that it would be technically and economically feasible for Bord na Mona to develop production methods, for the E.S.B. to burn milled peat for fairly large-scale electricity production.
Peat in its natural state in the bog contains about 95 per cent moisture. The first stage in production of milled peat is to reduce the moisture content to about 90 per cent by main bog drainage. Then the top surface of grasses and moss is removed and the edges are cambered to run off surface water. The surface is then scratched to a depth of about half an inch with a tractor-driven machine and after drying is collected, first into ridges, and then into long piles adjacent to a narrow-gauge railway. Five-ton wagons take the fuel to the generating station. It has a moisture content varying between 40 per cent and 60 per cent, and at 55 per cent has a net calorific value of 3370 B.t.u./lb.
In the Ferbane generating station the fuel wagons are tippled and the fuel fed on belt conveyors to the 250-ton boiler bunkers. From the bunkers the fuel is fed to pulverizing mills in which it is dried and is then blown into the combustion chamber. Each of the three boilers delivers steam at 425 lb/sq in, 825°F, has a maximum continuous rating of 220,000 lb/h and is coupled to a 20-MW turbo-alternator. The first set was commissioned in 1957. Two other generating stations similar to Ferbane are under construction at Rhode (80 MW) and Bellacorick (40 MW) and Ferbane will be extended to 90 MW.
For the year ending 31st March 1959 Ferbane generated 234 million units (it consumed 420,000 tons of fuel at a cost of £553,000, which represents a cost of 0.616 pence per unit sent out for fuel). The E.S.B. system's total generation for the year was 1898 million units which were generated in 22 different-type stations in the following total percentages: hydroelectric 42.7 per cent; milled peat 11.9 per cent; sod peat 9.4 per cent; native coal 1.1 per cent; imported coal and oil 34.9 per cent.
The report for the year ending 31st March 1960 has not yet been published but it has been announced that the units generated for that year were 2096 millions, showing an increase of 10 per cent on the previous year.
GATEAUX, LTD
Gateaux Ltd
Gateaux, Ltd, was established in 1949 with Irish capital and Irish labour, to process mainly Irish agricultural products into good quality cakes, at reasonable prices.
The policy of the firm was based on:
(1) The use of the most up-to-date plant and machinery and scientific methods of production, with emphasis on hygiene.
(2) The application of modern marketing and selling techniques.
In 1950 Gateaux, Ltd, initiated the first ever export of Irish cake, and in less than a decade has become the largest cake exporters in the world, as well as being the largest single manufacturer of cake in the Irish market. Today it is possible to buy cakes by Gateaux in Great Britain, the United States, Canada, Belgium, Switzerland, Sweden, East, West, and South Africa, Singapore, Hong Kong, Malaya, Aden, South America, British West Indies, Algiers, Cyprus, etc., and the volume of cake exported has grown from 200 tons in the first year to over 2,000 tons annually.
In the course of this expansion, factory space has been trebled and is still being extended. Early this year a new venture was launched — boiled sweets and toffees. The Sweet Department, a self-contained unit, is probably the most modern in Europe.
The original staff of 50 has been increased to approximately 250 workers, and about two-thirds of the raw materials used are produced in Ireland.
Industrial consultants were engaged in 1954, and since then the firm has operated a bonus incentive scheme for its employees in conjunction with the time and motion and work-study plan. Great emphasis is placed on harmonious staff relations and at the present time the firm is conducting T.W.I. (Training Within Industry) Courses. Training and education are encouraged amongst all grades, from top management to the newest apprentice, and are supported financially by the firm.
Marketing, and market research techniques are continuously employed, as are the best available technical assistance to production, including a laboratory which is one of the best of its kind.
Gateaux's success in competing in world markets is mainly attributable to a scientific approach to these markets which enabled the firm to produce an article which conformed to the particular requirements of each market, and which could, therefore, take its place against world competition.
ARTHUR GUINNESS SON AND CO. (DUBLIN), LTD, ST. JAMES'S GATE BREWERY
Arthur Guinness, Son and Co (Dublin) Ltd
Two hundred years ago, the first Arthur Guinness employed the motive power of one horse at St. James's Gate Brewery to grind the malt, while crude direct firing was used for boiling the 'wort', etc. The first steam engine and a 'haystack' boiler were installed in 1811; d.c. electric lighting in 1883 was followed by two 60-kW Parsons d.c. turbo-generators in 1895, with electric motors for driving machinery.
This brewery now employs about 4,000 people and has 64 acres of covered floor area, with electric motors totalling 8000 installed horsepower. Forty thousand tons of fuel and 1000 million gallons of water are consumed annually in the production of its world-famous stout, the daily output of which reaches 360,000 gallons. Boiler capacity is 200,000 lb of superheated steam per hour, and the cooling capacity of the ammonia refrigerating plant is 15,000,000 B.t.u. per hour.
Brewing water rises in many springs in County Kildare and flows towards Dublin in the Grand Canal: from filter beds, etc., five miles out in the country, the water flows to the brewery in large buried pipelines. Water from the City supply, suitably treated, is used for the Babcock boilers, while that obtained from deep wells supplements cooling.
Malt and hops are purchased, but barley obtained from the farmers is treated in the barley flaking plant which contains cookers, flaking rolls, driers and handling equipment.
Guinness yeast is the direct descendant of that developed in the early days of the firm. After each brewing, only the purest and best is kept for subsequent brews, the remainder being separated from its 'barm beer' in rotary vacuum filters and then dried for sale.
Engineering services include the provision of water, steam, electricity, cooling, ventilating, lighting, fire protection, telecommunications, instrumentation, metrology, machine attendance, maintenance, and internal railway transport.
Brewery railways include 2 miles of the standard Irish 5 ft 3 in. gauge track to link up with the national Coras Iompair Eireann, and at present, 8 miles of 22-in. gauge track for transport of malt, spent grains and hops, casks, ashes, etc., within the brewery. The 22-in. track includes a tunnel with a helical portion to negotiate a difference in level of 30 ft.
Two steam and one 200-h.p. diesel broad-gauge locomotives are used, and 12 'Planet' diesel narrow-gauge locomotives of 37 h.p. with a few unique steam locomotives designed by a former Chief Engineer, in 1882, and having horizontal cylinders mounted above the boiler with vertical side rods to the driving wheels.
The brewing process may be summarized by referring to the plant employed for the successive operations: Water purification, distribution and heating; obtaining, handling and storage of malt, hops, and barley flakes; grinding of malt and 'mashing' with water and flakes in the 'kieves' or mash tuns to form 'wort'; boiling this wort with hops in steam-heated coppers; cooling the wort, oxygenating it and 'pitching' with yeast on its way to the fermenting tuns; fermenting the wort in tuns so that it becomes beer (carbon dioxide is here evolved); skimming the beer in special vessels to remove yeast; storing the beer at controlled temperature in vats; making up the stout in racking vats and piping it to either (1) racking machines where sterilized casks are filled; or (2) the new tank station where tanks for its bulk transport are sterilized and filled.
Ancillary processes, and by-products such as liquefied carbon dioxide, surplus yeast, spent grains and hops, and even ashes from the power house, require much special plant and mechanical equipment.
Metal casks are rapidly replacing wooden casks for the distribution of stout. Nearly 200 heavy motor vehicles are employed for deliveries in Ireland, and even a few horse-drawn lorries survive.
Two motor vessels and one steam ship are constantly employed in the carriage of stout to Liverpool and Manchester in the large transportable tanks, and the return of the empty tanks for cleansing and refilling in the tank station at the brewery.
IRISH GLASS BOTTLE CO., LTD
Glass is one of mankind's oldest manufactured products and is today being used in different forms in almost every branch of industry. Different compositions and manufacturing methods make it possible to produce glasses with predetermined characteristics, to solve many specific problems such as those involving corrosion, heat, cleanliness, abrasion, radiation and many others faced by modern industry.
The three basic sciences on which modern glass technology rests are chemistry, physics and engineering. Since the beginning of the century engineering has provided the great challenge to progress in the industry and, for complete success, has required the collaboration of chemistry and physics to produce glass of constant composition and properties for efficient machine operations.
Notwithstanding the wealth of technical knowledge which has already been compiled on glass and its properties, relatively little is known of its chemical and physical structure, even after extensive investigation. Without such fundamental information, glass must remain in the category of inexact sciences and is defined as a physical condition continuous with and analogous to the liquid state in which a substance or a mixture of substances can exist after fusion and subsequent cooling.
The manufacture of any glass product involves two very different, though intimately associated, branches of technology: (1) the production of the glass from the raw materials which is a fusion process conducted at a temperature of 1500°C approximately, in a furnace of special refractory materials, and (2) the formation of the glass product from the molten glass by hand, by semi-automatic or fully automatic processes.
Today a very wide variety of furnace designs and forming machinery is available to meet the demands of the many different glass-making processes, and the selection of the most suitable plant for any particular process is governed by: (1) the type of glass to be produced; (2) the type of product to be manufactured; (3) the type of fuel available; (4) the extent and nature of the market to be supplied.
In Ireland, references to glass and glassworkers occurred in the thirteenth, fourteenth and fifteenth centuries but no information in regard to the types or quantities of glass product, or the districts in which the craft flourished, is available.
Probably the earliest reference to what might be regarded as a glass industry in any approximation to the modern sense of the term occurs in 1585. Between 1589 and 1932 - a span of three and a half centuries — at least 40 different glass industries were set up in Ireland of which half the number were in Dublin. By the 1920's there were only two factories in existence in Ireland, the Irish Glass Bottle Company and the Ringsend Bottle Company. Both of these concerns were engaged in the manufacture of bottles and both of them finally closed down in 1930.
In 1932 the present proprietors, the Irish Glass Bottle Co., Ltd, took over these two companies, starting with one furnace and single-head semi-automatic bottle-making machines. Additional bottle-producing units were added over the years as the market expanded, and today the company operates four glass furnaces as well as a variety of glass-forming machines ranging from the early semiautomatic to the most modern fully automatic types. This combination of plant is necessary to service the Irish market which, although relatively small in size, demands a very wide range of products.
In 1949 a subsidiary company, Waterford Glass, Ltd, was formed to revive the world-renowned old Waterford cut-glass industry and today this company is producing a very wide variety of hand-made cut-glass products of the highest quality.
UNIDARE, LTD
Unidare Ltd
In the short period of 12 years since Unidare began operations, the factory has spread to the point where buildings now occupy a 65-acre site. The products of the company are numerous, ranging from steel-cored aluminium overhead conductors to aluminium foil and polythene film.
Initially, manufacture was concentrated upon overhead conductors and pole-mounting transformers for supply to the extensive rural electrification scheme in the country, and these products have been extended to a stage where conductors up to 61 strands, and transformers up to 5 MVA, are being currently manufactured. Soon after production had commenced in the first factory building, the night storage heater, as it is now known and accepted almost universally, was first designed and developed; since then, infra-red heaters and a re-wirable floor-heating system have been added to the list of heating equipment which is being manufactured.
Some seven years ago an entirely new industry opened on the site, when large-scale production of barbed wire, wire netting, fencing wires of all descriptions, and a variety of steel wire for industry commenced. Further developments of this industry are, at the moment, being completed. About this time also the first polythene cold water tube in Ireland was produced, and a little later a range of electrically operated pumps and water systems was introduced to the market. All these were designed and developed by Unidare.
Quite a few of the products being manufactured by Unidare at this stage utilized both ferrous and non-ferrous castings in their make-up and the need arose for a foundry to supply this demand. This was installed four years ago and its most interesting feature is probably the shell moulding process that is used to produce extremely fine castings. In addition, sand-casting is undertaken and both methods of producing castings are in operation in a range of metals both ferrous and non-ferrous.
Within the last two years a new and independent factory has been completed for the manufacture, on a large scale, of all types of aluminium foil, extrusions—both aluminium and brass, aluminium sheet, polythene film for packaging purposes, etc. These products will not only be sold in the home market but also, it is hoped, in the export market alongside most of the other products being exported in considerable quantity.
On the same factory site is situated the premises of Telecommunications, Ltd, who are associated with Unidare, Ltd, and Pye Telecommunications, Ltd, of Cambridge. Their modern and well-equipped factory and development laboratory are devoted to the manufacture of many types of radio, telephone and line-carrying equipment for use in Ireland and in export markets.