1909 Institution of Mechanical Engineers: Visits to Works
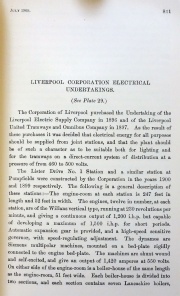
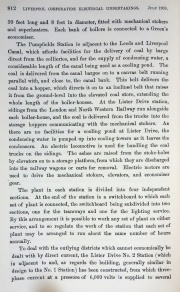
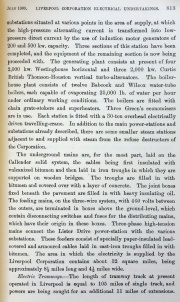
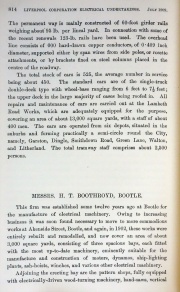
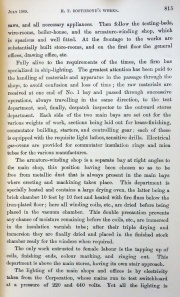
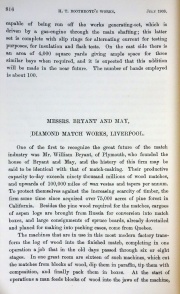
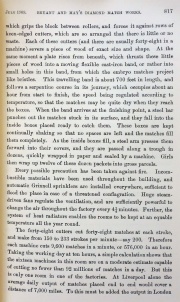
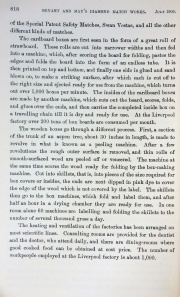
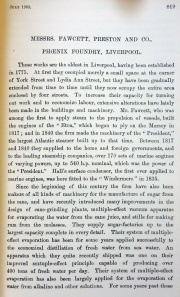
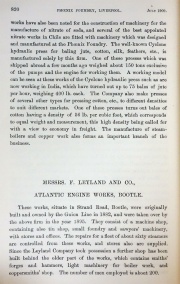
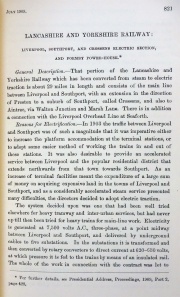
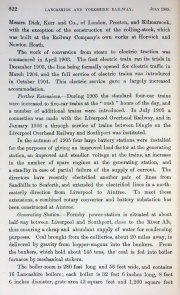
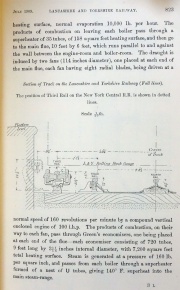
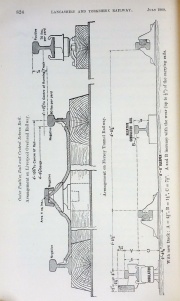
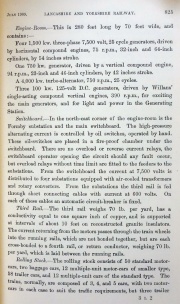
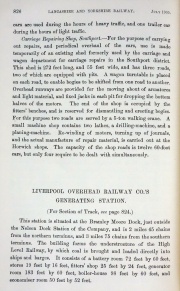
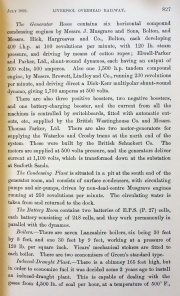
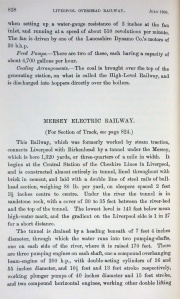
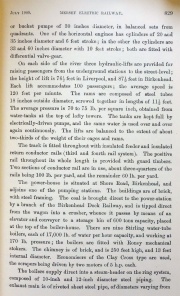
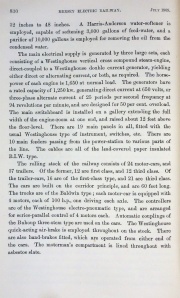
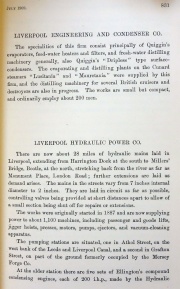
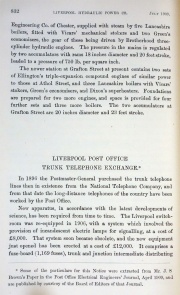
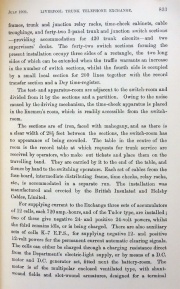

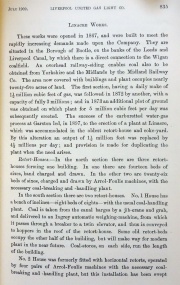
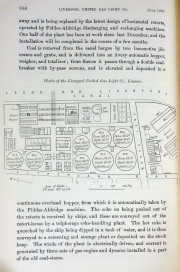
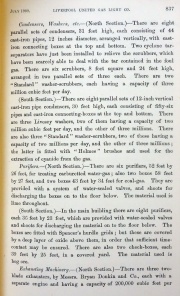
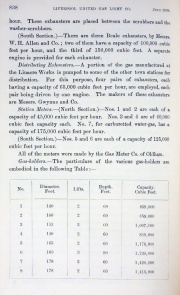
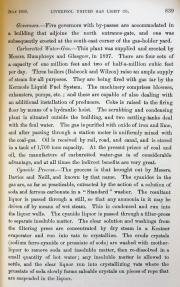
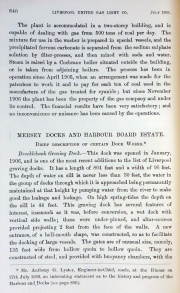
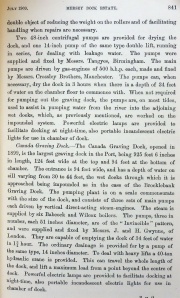
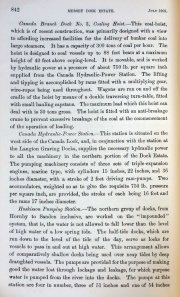
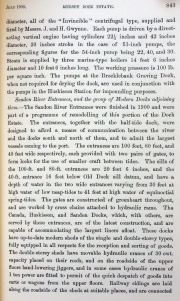
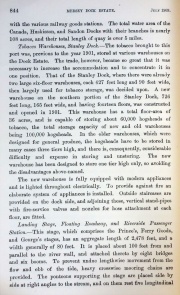

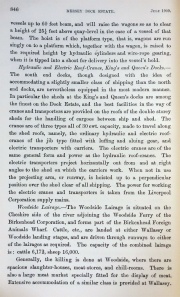
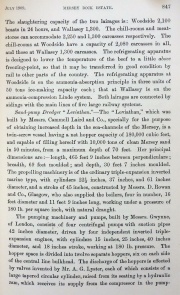
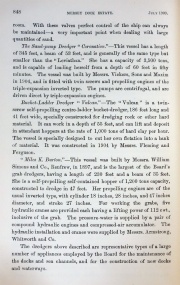
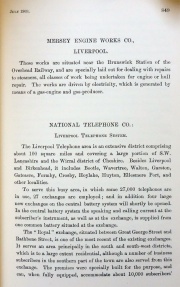
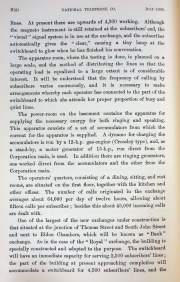
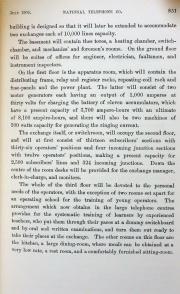
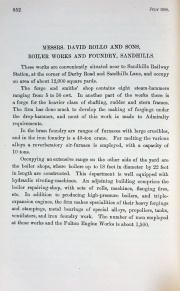
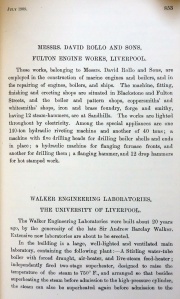
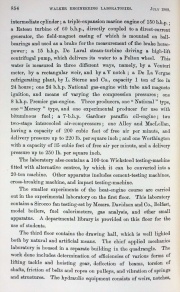
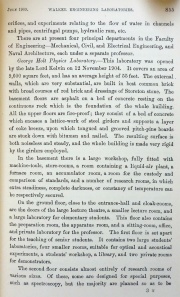
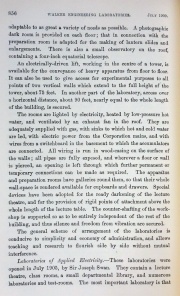
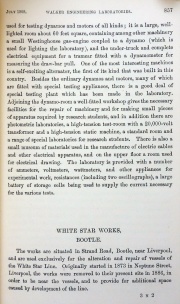
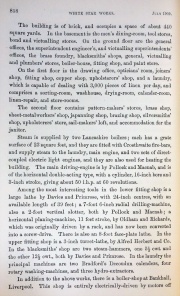
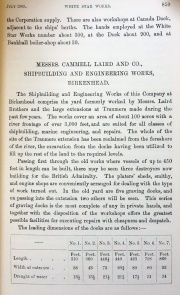
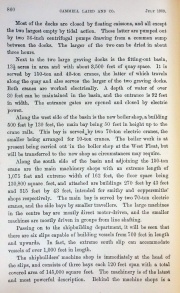
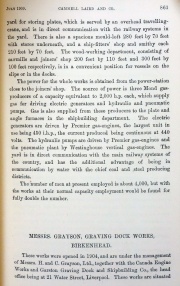
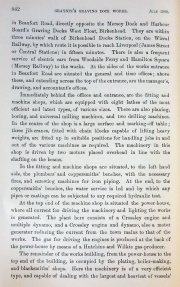
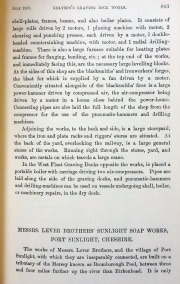
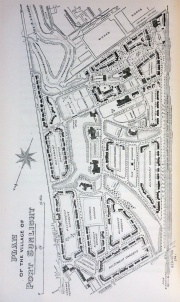
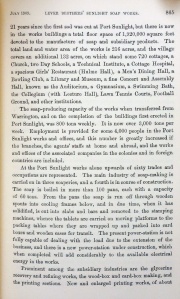
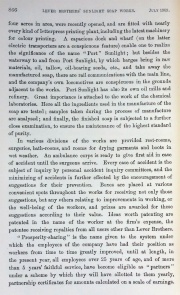
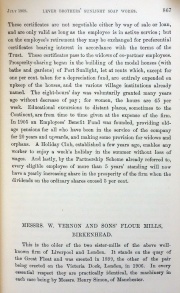
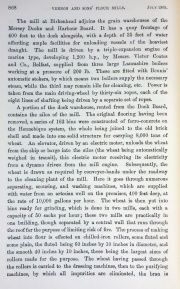
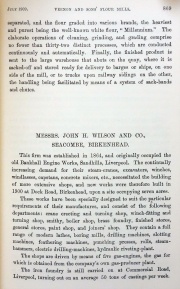
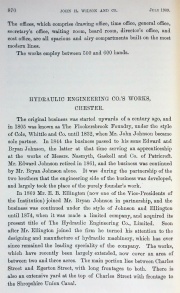
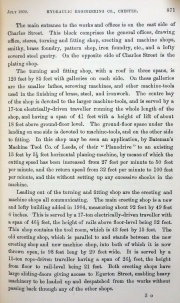
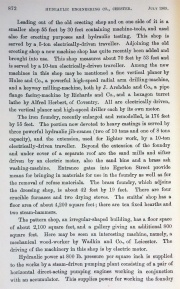
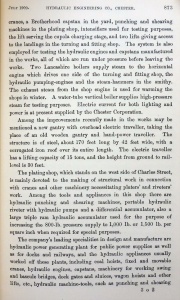
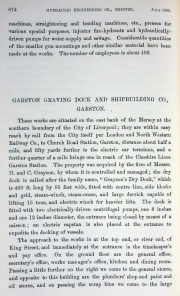

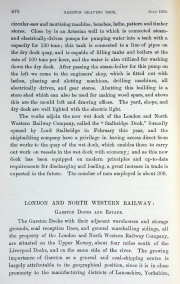
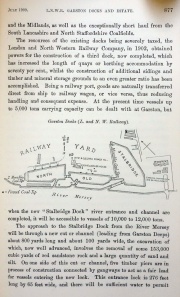
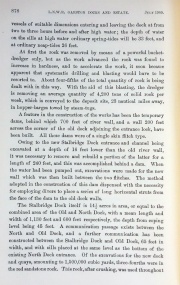
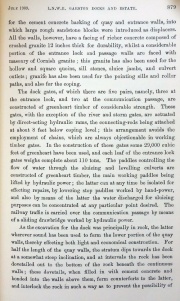
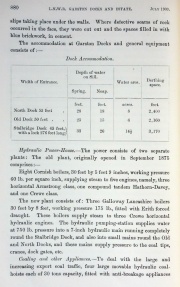
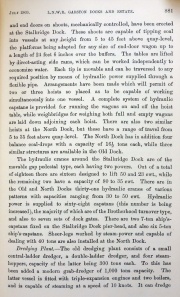
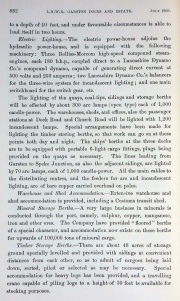
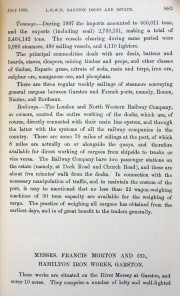
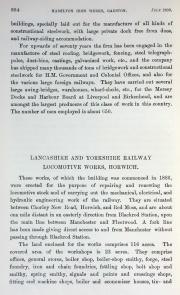
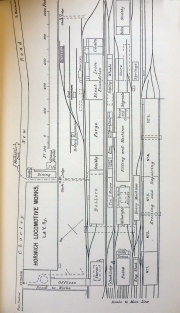
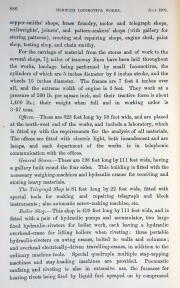
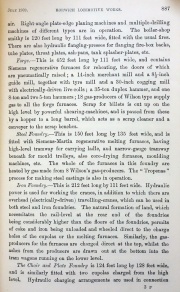
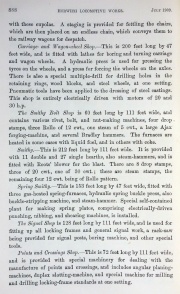
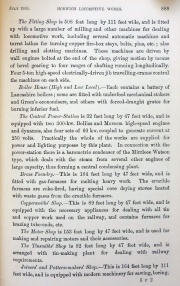
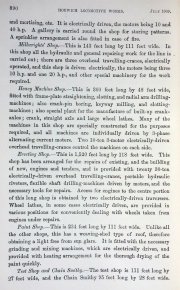
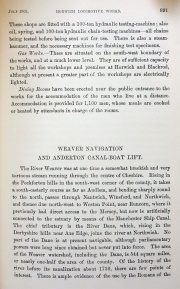
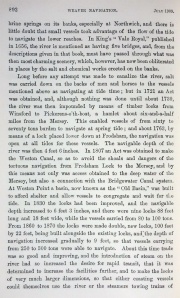
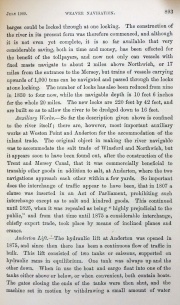
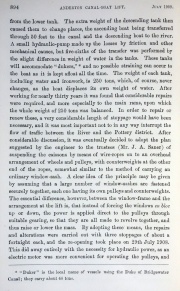
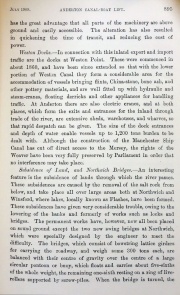
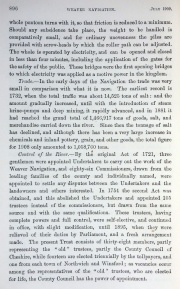
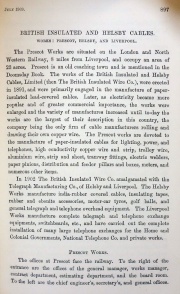
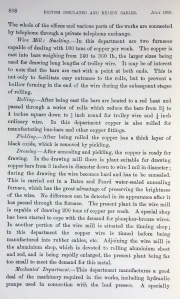
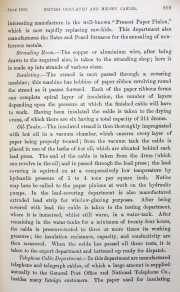
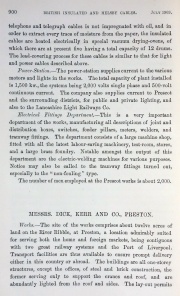
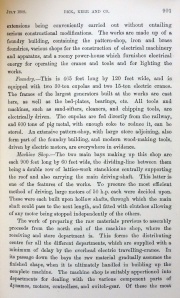
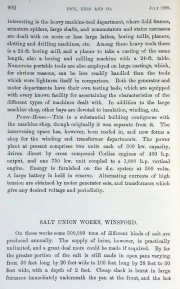

Note: This is a sub-section of 1909 Institution of Mechanical Engineers
Visits to Works (Excursions) in the Liverpool area
Liverpool Corporation Electrical Undertakings
LIVERPOOL CORPORATION ELECTRICAL UNDERTAKINGS. (See Plate 29.)
The Corporation of Liverpool purchased the Undertaking of the Liverpool Electric Supply Company in 1896 and of the Liverpool United Tramways and Omnibus Company in 1897. As the result of these purchases it was decided that electrical energy for all purposes should be supplied from joint stations, and that the plant should be of such a character as to be suitable both for lighting and for the tramways on a direct-current system of distribution at a pressure of from 460 to 500 volts.
The Lister Drive No. 1 Station and a similar station at Pumpfields were constructed by the Corporation in the years 1900 and 1899 respectively. The following is a general description of these stations:—The engine-room at each station is 247 feet in length and 52 feet in width. The engines, twelve in number, at each station, are of the Willans vertical type, running at 230 revolutions per minute, and giving a continuous output of 1,200 i.h.p. but capable of developing a maximum of 1,500 i.h.p. for short periods. Automatic expansion gear is provided, and a high-speed sensitive governor, with speed-regulating adjustment.
The dynamos are Siemens multipolar machines, mounted on a bed-plate rigidly connected to the engine bed-plate. The machines are shunt wound and self-excited, and give an output of 1,420 amperes at 550 volts. On either side of the engine-room is a boiler-house of the same length as the engine-room, 51 feet wide. Each boiler-house is divided into two sections, and each section contains seven Lancashire boilers, 30 feet long and 8 feet in diameter, fitted with mechanical stokers and superheaters. Each bank of boilers is connected to a Green's economiser.
The Pumpfields Station is adjacent to the Leeds and Liverpool Canal, which affords facilities for the delivery of coal by barge direct from the collieries, and for the supply of condensing water, a considerable length of the canal being used as a cooling pond. The coal is delivered from the canal barges on to a canvas bolt running parallel with, and close to, the canal bank. This belt delivers the coal into a hopper, which directs it on to an inclined belt that raises it from the ground-level into the elevated coal store, extending the whole length of the boiler-houses.
At the Lister Drive station, sidings from the London and North Western Railway run alongside each boiler-house, and the coal is delivered from the trucks into the storage hoppers communicating with the mechanical stokers. As there are no facilities for a cooling pond at Lister Drive, the condensing water is pumped up into cooling towers as it leaves the condensers. An electric locomotive is used for handling the coal trucks on the sidings. The ashes are raised from the stoke-holes by elevators on to a storage platform, from which they are discharged into the railway wagons or carts for removal. Electric motors are used to drive the mechanical stokers, elevators, and economiser gear.
The plant in each station is divided into four independent sections. At the end of the station is a switchboard to which each set of plant is connected, the switchboard being subdivided into two sections, one for the tramways and one for the lighting service. By this arrangement it is possible to work any set of plant on either service, and to so regulate the work of the station that each set of plant may be arranged to run about the same number of hours annually.
To deal with the outlying districts which cannot economically be dealt with by direct current, the Lister Drive No. 2 Station (which is adjacent to and, as regards the building, generally similar in design to the No. 1 Station) has been constructed, from which three-phase current at a pressure of 6,000 volts is supplied to several substations situated at various points in the area of supply, at which the high-pressure alternating current is transformed into low-pressure direct current by the use of induction motor generators of 200 and 500 kw. capacity. Three sections of this station have been completed, and the equipment of the remaining section is now being proceeded with.
The generating plant consists at present of four 2,000 kw. Westinghouse horizontal and three 2,000 kw. Curtis British Thomson-Houston vertical turbo-alternators. The boiler- house plant consists of twelve Babcock and Wilcox water-tube boilers, each capable of evaporating 25,000 lb. of water per hour under ordinary working conditions. The boilers are fitted with chain grate-stokers and superheaters. Three Green's economisers are in use. Each station is fitted with a 30-ton overhead electrically driven travelling-crane. In addition to the main power-stations and substations already described, there are some smaller steam stations adjacent to and supplied with steam from the refuse destructors of the Corporation.
The underground mains are, for the most part, laid on the Callender solid system, the cables being first insulated with vulcanized bitumen and then laid in iron troughs in which they are supported on wooden bridges. The troughs are filled in with bitumen and covered over with a layer of concrete. The joint boxes fixed beneath the pavement are filled in with heavy insulating oil. The feeding mains, on the three-wire system, with 460 volts between the outers, are terminated in boxes above the ground-level, which contain disconnecting switches and fuses for the distributing mains, which have their origin in these boxes. Three-phase high-tension mains connect the Lister Drive power-station with the various substations. These feeders consist of specially paper-insulated lead- covered and armoured cables laid in cast-iron troughs filled in with bitumen. The area in which the electricity is supplied by the Liverpool Corporation contains about 32 square miles, being approximately 81 miles long and 4i miles wide.
Electric Tramways. — The length of tramway track at present operated in Liverpool is equal to 105 miles of single track, and powers are being sought for an additional 11 miles of extensions.
The permanent way is mainly constructed of 60-foot girder rails weighing about 95 lb. per lineal yard. In connection with some of the recent renewals 123-1b. rails have been used. The overhead line consists of 000 hard-drawn copper conductors, of 0.409 inch diameter, supported either by span wires from side poles, or rosette attachments, or by brackets fixed on steel columns placed in the centre of the roadway.
The total stock of cars is 525, the average number in service being about 450. The standard cars are of the single-truck double-deck typo with wheel-base ranging from 6 feet to 71 feet; the upper deck in the large majority of cases being roofed in. All repairs and maintenance of cars are carried out at the Lambeth Road Works, which are adequately equipped for the purpose, covering an area of about 13,000 square yards, with a staff of about 400 men. The cars are operated from six depots, situated in the suburbs and forming practically a semi-circle round the City, namely, Garston, Dingle, Smithdown Road, Green Lane, Walton, and Litherland. The total tram way staff comprises about 2,500 persons.
H. T. Boothroyd
MESSRS. H. T. BOOTHROYD, BOOTLE.
H. T. Boothroyd
This firm was established some twelve years ago at Bootle for the manufacture of electrical machinery. Owing to increasing business it was soon found necessary to move to more commodious works at Akenside Street, Bootle, and again, in 1902, these works were entirely rebuilt and remodelled, and now cover an area of about 3,000 square yards, consisting of three spacious bays, each fitted with the most up-to-date machinery, eminently suitable for the manufacture and construction of motors, dynamos, ship-lighting plants, ash-hoists, winches, and various other electrical machinery. Adjoining the erecting bay are the pattern shops, fully equipped with electrically-driven wood-turning machinery, band-saws, vertical saws, and all necessary appliances. Then follow the testing-beds, wire-rooms, boiler-house, and the armature-winding shop, which is spacious and well fitted. At the frontage to the works are substantially built store-rooms, and on the first floor the general offices, drawing office, etc.
Fully alive to the requirements of the times, the firm has specialized in ship-lighting. The greatest attention has been paid to the handling of materials and apparatus in the passage through the shops, to avoid confusion and loss of time; the raw materials are received at one end of No. 1 bay and passed through successive operations, always travelling in the same direction, to the test department, and, finally, despatch inspector to the outward stores department. Each side of the two main bays are set out for the various weights of work, sections being laid out for brass-finishing, commutator building, starters, and controlling gear: each of these is equipped with the requisite light lathes, sensitive drills. Electrical gas-ovens are provided for commutator insulation rings and mica tubes for the various manufactures.
The armature-winding shop is a separate bay at right angles to the main shop, this position having been chosen so as to be free from metallic dust that is always present in the main bays where erecting and machining takes place. This department is specially heated and contains a large drying oven, the latter being a brick chamber 10 feet by 10 feet and heated with fire flues below the iron-plated floor; here all winding coils, etc., are dried before being placed in the vacuum chamber. This double precaution prevents any chance of moisture remaining before the coils, etc., are immersed in the insulation varnish tubs; after their triple drying and immersion they are finally dried and placed in the finished stock chamber ready for the winders when required.
The only work entrusted to female labour is the tapping up of coils, finishing ends, colour marking, and ringing out. This department is above the main stores, having its own stair approach. The lighting of the main shops and offices is by electricity taken from the Corporation, whose mains run to test switchboard at a pressure of 220 and 440 volts. Yet all the lighting is capable of being run off the works generating-set, which is driven by a gas-engine through the main shafting; this latter set is complete with slip rings for alternating current for testing purposes, for insulation and flash tests. On the east side there is an area of 4,000 square yards giving ample space for three similar bays when required, and it is expected that this addition will be made in the near future.
The number of hands employed is about 100.
Bryant and May
MESSRS. BRYANT AND MAY, DIAMOND MATCH WORKS, LIVERPOOL.
Bryant and May, Diamond Match Works
One of the first to recognize the great future of the match industry was Mr. William Bryant, of Plymouth, who founded the house of Bryant and May, and the history of this firm may be said to be identical with that of match-making. Their productive capacity to-day exceeds ninety thousand millions of wood matches, and upwards of 100,000 miles of wax vestas and tapers per annum. To protect themselves against the increasing scarcity of timber, the firm some time since acquired over 75,000 acres of pine forest in California. Besides the pine wood required for the snatches, cargoes of aspen logs are brought from Russia for conversion into match boxes, and large consignments of spruce boards, already dovetailed and planed for making into packing cases, come from Quebec.
The machines that are in use in this most modern factory transform the log of wood into the finished match, completing in one operation a job that in the old days passed through six or eight stages. In one great room are sixteen of such machines, which cut the matches from blocks of wood, dip them in paraffin, tip them with composition, and finally pack them in boxes.
At the start of operations a man feeds blocks of wood into the jaws of the machine, which grips the block between rollers, and forces it against rows of keen-edged cutters, which are so arranged that there is little or no waste. Each of these cutters (and there are usually forty-eight in a machine) severs a piece of wood of exact size and shape. At the same moment a plate rises from beneath, which thrusts these little pieces of wood into a moving flexible cast-iron band, or rather into small holes in this baud, from which the embryo matches project like bristles. This travelling band is about 700 feet in length, and follows a serpentine course in its journey, which occupies about an hour from start to finish, the speed being regulated according to temperature, so that the matches may be quite dry when they reach the boxes. When the band arrives at the finishing point, a steel bar punches out the matches stuck in its surface, and they fall into the inside boxes placed ready to catch them. These boxes are kept continually shaking so that no spaces are left and the matches fill them completely. As the inside boxes fill, a steel arm presses them forward into their covers, and they are passed along a trough in dozens, quickly wrapped in paper and sealed by a machine. Girls then wrap up twelve of these dozen packets into gross parcels.
Every possible precaution has been taken against fire. Incombustible materials have been used throughout the building, and automatic Grinnell sprinklers are installed everywhere, sufficient to flood the place in case of a threatened conflagration. Huge steam-driven fans regulate the ventilation, and are sufficiently powerful to change the air throughout the factory every 4.25 minutes. Further, the system of heat radiators enables the rooms to be kept at an equable temperature all the year round.
The forty-eight cutters cut forty-eight matches at each stroke, and make from 150 to 233 strokes per minute — say 200. Therefore - each machine cuts 9,600 matches in a minute, or 576,000 in an hour. Taking the working day at ten hours, a simple calculation shows that the sixteen machines in this room are on a moderate estimate capable of cutting no fewer than 92 millions of matches in a day. But this is only one room in one of the factories. At Liverpool alone the average daily output of matches placed end to end would cover a distance of 7,000 miles. To this must be added the output in London of the Special Patent Safety Matches, Swan Vestas, and all the other different kinds of matches.
The cardboard boxes are first seen in the form of a great roll of strawboard. These rolls are cut into narrower widths and then fed into a machine, which, after scoring the board for folding, pastes the edges and folds the board into the form of an endless tube. It is then printed on top and bottom, and finally one side is glued and sand blown on, to make a striking surface, after which each is cut off to the right size and ejected ready for use from the machine, which turns out over 1,000 boxes per minute. The insides of the cardboard boxes are made by another machine, which cuts out the board, scores, folds, and glues over the ends, and then carries the completed inside box on a travelling chain till it is dry and ready for use. At the Liverpool factory over 200 tons of box boards are consumed per month.
The wooden boxes go through a different process. First, a section of the trunk of an aspen tree, about 30 inches in length, is made to revolve in what is known as a peeling machine. After a few revolutions the rough outer surface is removed, and thin rolls of smooth-surfaced wood are peeled off or veneered. The machine at the same time scores the wood ready for folding by the box-making machine. Cut into skillets, that is, into pieces of the size required for box covers or insides, the ends are next dipped in pink dye to cover the edge of the wood which is not covered by the label. The skillets then go to the box machines, which fold and label them, and after half an hour in a drying chamber they are ready for use. In one room alone 60 machines are labelling and folding the skillets to the number of several thousand gross a day.
The heating and ventilation of the factories has been arranged on most scientific lines. Consulting rooms are provided for the dentist and the doctor, who attend daily, and there are dining-rooms where good cooked food can be obtained at cost price.
The number of workpeople employed at the Liverpool factory is about 1,000.
Fawcett, Preston and Co
MESSRS. FAWCETT, PRESTON AND CO., PHOENIX FOUNDRY, LIVERPOOL.
Fawcett, Preston and Co
These works are the oldest in Liverpool, having been established in 1775. At first they occupied merely a small space at the corner of York Street and Lydia Ann Street, but they have been gradually extended from time to time until they now occupy the entire area enclosed by four streets. To increase their capacity for turning out work and to economize labour, extensive alterations have lately been made in the buildings and machinery.
Mr. Fawcett, who was among the first to apply steam to the propulsion of vessels, built the engines of the "Etna," which began to ply on the Mersey in 1817; and in 1840 the firm made the machinery of the "President," the largest Atlantic steamer built up to that time. Between 1817 and 1840 they supplied to the home and foreign governments, and to the leading steamship companies, over 170 sets of marine engines of varying powers, up to 540 h.p. nominal, which was the power of the "President." Hall's surface condenser, the first ever applied to marine engines, was hero fitted to the "Windermere" in 1835.
Since the beginning of this century the firm have also been makers of all kinds of machinery for the manufacture of sugar from the cane, and have recently introduced many improvements in the design of cane-grinding plants, multiple-effect vacuum apparatus for evaporating the water from the cane juice, and stills for making rum from the molasses. They supply sugar-factories up to the largest capacity complete in every detail. Their system of multiple-effect evaporation has been for some years applied successfully to the economical distillation of fresh water from sea water. An apparatus which they quite recently shipped was one on their improved sextuple-effect principle capable of producing over 400 tons of fresh water per day. Their system of multiple-effect evaporation has also been largely applied for the evaporation of water from alkaline and other solutions.
For some years past these works have also been noted for the construction of machinery for the manufacture of nitrate of soda, and several of the best appointed nitrate works in Chile are fitted with machinery which was designed and manufactured at the Phoenix Foundry. The well-known Cyclone hydraulic press for baling jute, cotton, silk, feathers, etc., is manufactured solely by this firm. One of these presses which was shipped abroad a few months ago weighed about 150 tons exclusive of the pumps and the engine for working them. A working model can be seen at these works of the Cyclone hydraulic press such as are now working in India, which have turned out up to 75 bales of jute per hour, weighing 400 lb. each.
The Company also make presses of several other types for pressing cotton, etc., to different densities to suit different markets. One of these presses turns out bales of cotton having a density of 56 lb. per cubic foot, which corresponds to equal weight and measurement, this high density being called for with a view to economy in freight. The manufacture of steam-boilers and copper work also forms an important branch of the business.
Frederick Leyland and Co
MESSRS. F. LEYLAND AND CO., ATLANTIC ENGINE WORKS, BOOTLE.
Frederick Leyland and Co
These works, situate in Strand Road, Bootle, were originally built and owned by the Guion Line in 1882, and were taken over by the above firm in the year 1895. They consist of a machine shop, containing also tin shop, small foundry and sawyers' machinery, with stores and offices. The repairs for a fleet of about sixty steamers are controlled from these works, and stores also are supplied. Since the Leyland Company took possession a further shop has been built behind the older part of the works, which contains smiths' forges and hammers, light machinery for boiler work, and coppersmiths' shop.
The number of men employed is about 200.
Lancashire and Yorkshire Railway
LANCASHIRE AND YORKSHIRE RAILWAY: LIVERPOOL, SOUTHPORT, AND OROSSENS ELECTRIC SECTION, AND FORMBY POWER-HOUSE.
Lancashire and Yorkshire Railway
General Description. — That portion of the Lancashire and Yorkshire Railway which has been converted from steam to electric traction is about 29 miles in length and consists of the main line between Liverpool and Southport, with an extension in the direction of Preston to a suburb of Southport, called Crossens, and also to Aintree, via Walton Junction and Marsh Lane. There is in addition a connection with the Liverpool Overhead Line at Seaforth.
Reasons for Electrification. — In 1903 the traffic between Liverpool and Southport was of such a magnitude that it was imperative either to increase the platform accommodation at the terminal stations, or to adopt some easier method of working the trains in and out of these stations. It was also desirable to provide an accelerated service between Liverpool and the popular residential district that extends northwards from that town towards Southport. As an increase of terminal facilities meant the expenditure of a large sum of money on acquiring expensive laud in the towns of Liverpool and Southport, and as a considerably accelerated steam service presented many difficulties, the directors decided to adopt electric traction.
The system decided upon was one that had been well tried elsewhere for heavy tramway and inter-urban services, but had never up till then been tried for heavy trains for main-line work. Electricity is generated at 7,500 volts A.C., three-phase, at a point midway between Liverpool and Southport, and delivered by underground cables to five substations. In the substations it is transformed and then converted by rotary converters to direct current at 620-630 volts, at which pressure it is fed to the trains by means of an insulated rail. The whole of the work in connection with the contract was let to Messrs. Dick, Kerr and Co., of London, Preston, and Kilmarnock, with the exception of the construction of the rolling-stock, which was built at the Railway Company's own works at Horwich and Newton Heath.
The work of conversion from steam to electric traction was commenced in April 1903. The first electric train ran its trials in December 1903, the line being formally opened for electric traffic in March 1904, and the full service of electric trains was introduced in October 1904. This electric service gave a largely increased accommodation.
Further Extensions. — During 1905 the standard four-car trains were increased to five-car trains at the "rush" hours of the day, and a number of additional trains were introduced. In July 1905 a connection was made with the Liverpool Overhead Railway, and in January 1906 a through service of trains between Dingle on the Liverpool Overhead Railway and Southport was instituted.
In the autumn of 1905 four large battery stations were installed for the purposes of giving an improved load-factor at the generating station, an improved and steadier voltage at the trains, an increase in the number of spare engines at the generating station, and a standby in case of partial failure of the supply of current. The directors have recently electrified another pair of lines from Sandhills to Seaforth, and extended the electrified lines in a north-easterly direction from Liverpool to Aintree. To inset these extensions, a combined rotary converter and battery substation has been constructed at Aintree.
Generating Station. — Formby power-station is situated at about half-way between Liverpool and Southport, close to the River Alt, thus ensuring a cheap and abundant supply of water for condensing purposes. Coal brought from the collieries, about 20 miles away, is delivered by gravity from hopper-wagons into the bunkers. From the bunkers, which hold about 145 tons, the coal is fed into boiler furnaces by mechanical stokers.
[See diagram on attached image on page 823]
The boiler-room is 280 feet long and 56 feet wide, and contains 16 Lancashire boilers; each boiler is 32 feet 6 inches long, 8 feet 6 inches diameter, grate area 42 square feet and 1,200 square feet heating surface, normal evaporation 10,000 lb. per hour. The products of combustion on leaving each boiler pass through a superheater of 35 tubes, of 158 square feet heating surface, and than go to the main flue, 10 feet by 6 feet, which runs parallel to and against the wall between the engine-room and boiler-room. The draught is induced by two fans (114 inches diameter), one placed at each end of the main flue, each fan having eight radial blades, being driven at a normal speed of 160 revolutions per minute by a compound vertical enclosed engine of 100 i.h.p. The products of combustion, on their way to each fan, pass through Green's economisers, one being placed at each end of the flue — each economiser consisting of 720 tubes, 9 feet long by 3 11/16th inches internal diameter, with 7,200 square feet total heating surface. Steam is generated at a pressure of 160 lb. per square inch, and passes from each boiler through a superheater formed of a nest of U tubes, giving 140° F. superheat into the main steam-range.
Engine-Room. — This is 280 feet long by 70 feet wide, and contains:-
Four 1,500 kw. three-phase 7,500 volt, 25 cycle generators, driven by horizontal compound engines, 75 r.p.m., 32-inch and 64-inch cylinders, by 54 inches stroke.
One 750 kw. generator, driven by a vertical compound engine, 94 r.p.m., 23-inch and 46-inch cylinders, by 42 inches stroke.
A 4,000 kw. turbo-alternator, 750 r.p.m., 25 cycles.
Three 100 kw. 125-volt D.C. generators, driven by Willaus' single-acting compound vertical engines, 390 r.p.m., for exciting the main generators, and for light and power in the Generating Station.
Switchboard. — In the north-east corner of the engine-room is the Formby substation and the main switchboard. The high-pressure alternating current is controlled by oil switches, operated by hand. These oil-switches are placed in a fire-proof chamber under the switchboard. There are no overload or reverse current relays, the switchboard operator opening the circuit should any fault occur, but overload relays without time limit are fitted to the feeders to the substations. From the switchboard the current at 7,500 volts is distributed to four substations equipped with air-cooled transformers and rotary converters. From the substations the third rail is fed through short connecting cables with current at 600 volts. On each of these cables an automatic circuit-breaker is fixed.
Third Rail. — The third rail weighs 70 lb. per yard, has a conductivity equal to one square inch of copper, and is supported at intervals of about 10 feet on reconstructed granite insulators. The current returning from the motors passes through the train wheels into the running rails, which are not bonded together, but are each cross-bonded to a fourth rail, or return conductor, weighing 70 lb. per yard, which is laid between the running rails.
Rolling Stock — The rolling stock consists of 50 standard motorcars, two baggage cars, 12 multiple-unit motor-cars of smaller type, 58 trailer cars, and 12 multiple-unit cars of the standard type. The trains, normally, are composed of 3, 4, and 5 cars, with two motorcars in each case to suit the traffic requirements, but three trailer cars are used during the hours of heavy traffic, and one trailer car during the hours of light traffic.
Carriage Repairing Shop, Southport. — For the purpose of carrying out repairs, and periodical overhaul of the cars, use is made temporarily of an existing shed formerly used by the carriage and wagon department for carriage repairs in the Southport district. This shed is 272 feet long, and 55 feet wide, and has three roads, two of which are equipped with pits. A wagon turntable is placed on each road, to enable bogies to be shifted from one road to another. Overhead runways are provided for the moving about of armatures and light material, and fixed jacks in each pit for dropping the bottom halves of the motors. The end of the shop is occupied by the fitters' benches, and is reserved for dismantling and erecting bogies. For this purpose two roads are served by a 5-ton walking crane. A small machine shop contains two lathes, a drilling-machine, and a planing-machine. Re-winding of motors, turning up of journals, and the actual manufacture of repair material, is carried out at the Horwich shops. The capacity of the shop roads is twelve 60-foot cars, but only four require to be dealt with simultaneously.
Liverpool Overhead Railway
LIVERPOOL OVERHEAD RAILWAY CO.'S GENERATING STATION.
(For Section of Track, see diagram on attached image page 824)
Liverpool Overhead Railway
This station is situated at the Bramley Moore Dock, just outside the Nelson Dock Station of the Company, and is 2 miles 45 chains from the northern terminus, and 3 miles 75 chains from the southern terminus. The building forms the understructure of the High Level Railway, by which coal is brought and loaded directly into ships and barges. It consists of a battery room 72 feet by 60 feet, stores 19 feet by 16 foot, fitters' shop 25 feet by 24 feet, generator room 183 feet by 60 feet, boiler-house 98 feet by 60 feet, and economiser room 50 feet by 52 feet.
The Generator Room contains six horizontal compound condensing engines by Messrs. J. Musgrave and Sons, Bolton, and Messrs. Hick, Hargreaves and Co., Bolton, each developing 400 i.h.p. at 100 revolutions per minute, with 120 lb. steam pressure, and driving by means of cotton ropes; Elwell-Parker and Parker, Ltd., shunt-wound dynamos, each having an output of 500 volts, 500 amperes. Also one 1,500 h.p. tandem compound engine, by Messrs. Browett, Lindley and Co., running 230 revolutions per minute, and driving direct a Dick-Kerr multipolar shunt-wound dynamo, giving 1,700 amperes at 500 volts.
There are also three positive boosters, two negative boosters, and one battery-charging booster, and the current from all the machines is controlled by switchboards, fitted with automatic cutouts, etc., supplied by the British Westinghouse Co. and Messrs. Thomas Parker, Ltd. There are also two motor-generators for supplying the Waterloo and Crosby trams at the north end of the system. These were built by the British Schuckert Co. The motors are supplied at 500 volts pressure, and the generators deliver current at 1,100 volts, which is transformed down at the substation at Seaforth Sands.
The Condensing Plant is situated in a pit at the south end of the generator room, and consists of surface condensers, with circulating pumps and air-pumps, driven by non-dead-centre Musgrave engines running at 250 revolutions per minute. The circulating water is taken from and returned to the dock.
The Battery Room contains two batteries of E.P.S. (P. 27) cells, each battery consisting of 248 cells, and they work permanently in parallel with the dynamos.
Boilers. — There are seven Lancashire boilers, six being 30 feet by 8 feet, and one 30 feet by 9 feet, working at a pressure of 120 lb. per square inch. Vicars' mechanical stokers are fitted to each boiler. There are two economisers of Green's standard type.
Induced-Draught Plant. — There is a chimney 165 feet high, but in order to economize fuel it was decided some 2 years ago to install an induced-draught plant. This is capable of dealing with the gases from 4,500 lb. of coal per hour, at a temperature of 500° F., when setting up a water-gauge resistance of 2 inches at the fan inlet, and running at a speed of about 510 revolutions per minute. The fan is driven by one of the Lancashire Dynamo Co.'s motors of 30 b.h.p.
Feed Pumps. — There are two of these, each having a capacity of about 6,700 gallons per hour.
Coaling Arrangements. — The coal is brought over the top of the generating station, on what is called the High-Level Railway, and is discharged into hoppers directly over the boilers.
Mersey Electric Railway
Mersey Electric Railway. (For Section of Track, see page 824.)
This Railway, which was formerly worked by steam traction, connects Liverpool with Birkenhead by a tunnel under the Mersey, which is here 1,320 yards, or three-quarters of a mile in width. It begins at the Central Station of the Cheshire Lines in Liverpool, and is constructed almost entirely in tunnel, lined throughout with brick in cement, and laid with a double line of steel rails of bullhead section, weighing 86 lb. per yard, on sleepers spaced 2 feet 31- inches centre to centre. Under the river the tunnel is in sandstone rock, with a cover of 30 to 35 feet between the river-bed and the top of the tunnel. The lowest level is 145 feet below mean high-water mark, and the gradient on the Liverpool side is 1 in 27 for a short distance.
The tunnel is drained by a heading beneath of 7 feet 4 inches diameter, through which the water runs into two pumping-shafts, one on each side of the river, where it is raised 170 feet. There are three pumping engines on each shaft, one a compound overhanging beam-engine of 200 h.p., with double-acting cylinders of 36 and 55 inches diameter, and 101 feet and 13 feet stroke respectively, working plunger pumps of 40 inches diameter and 15 feet stroke, and two compound horizontal engines, working other double lifting or bucket pumps of 30 inches diameter, in balanced sets from quadrants. One of the horizontal engines has cylinders of 20 and 35 inches diameter and 6 feet stroke; in the other the cylinders are 33 and 60 inches diameter with 10 feet stroke; both are fitted with differential valve-gear.
On each side of the river three hydraulic-lifts are provided for raising passengers from the underground stations to the street-level; the height of lift is 76 1/2 feet in Liverpool, and 87 1/2 feet in Birkenhead. Each lift accommodates 100 passengers; the average speed is 120 feet per minute. The rams are composed of steel tubes 10 inches outside diameter, screwed together in lengths of 11 feet. The average pressure is 70 to 75 lb. per square inch, obtained from water-tanks at the top of lofty towers. The tanks are kept full by electrically-driven pumps, and the same water is used over and over again continuously. The lifts are balanced to the extent of about two-thirds of the weight of their cages and rams.
The track is fitted throughout with insulated feeder and insulated return conductor rails (third and fourth rail system). The positive rail throughout its whole length is provided with guard timbers. Two sections of conductor rail are in use, about three-quarters of the rails being 100 lb. per yard, and the remainder 60 lb. per yard.
The power-house is situated at Shore Road, Birkenhead, and adjoins one of the pumping stations. The buildings are of brick, with steel framing. The coal is brought direct to the power-station by a branch of the Birkenhead Dock Railway, and is tipped direct from the wagon into a crusher, whence it passes by means of an elevator and conveyor to a storage bin of 600 tons capacity, placed at the top of the boiler-house. There are nine Stirling water-tube boilers, each of 17,000 lb. of water per hour capacity, and working at 170 lb. pressure; the boilers are fitted with Roney mechanical stokers. The chimney is of brick, and is 250 feet high, and 13 feet internal diameter. Economisers of the Clay Cross type are used, the scrapers being driven by two motors of 5 h.p. each.
The boilers supply direct into a steam-header on the ring system, composed of 10-inch and 12-inch diameter steel piping. The exhaust main is of riveted sheet steel pipe, of diameters varying from 32 inches to 48 inches. A Harris-Anderson water-softener is employed, capable of softening 3,000 gallons of feed-water, and a purifier of 10,000 gallons is employed for removing the oil from the condensed water.
The main electrical supply is generated by three large sets, each consisting of a Westinghouse vertical cross compound steam-engine, direct-coupled to a Westinghouse double current generator, yielding either direct or alternating current, or both, as required. The horsepower of each engine is 1,650 at normal load. The generators have a rated capacity of 1,250 kw. generating direct current at 650 volts, or three-phase alternate current of 25 periods per second frequency at 94 revolutions per minute, and are designed for 50 per cent. overload. The main switchboard is installed on a gallery extending the full width of the engine-room at one end, and raised about 12 feet above the floor-level. There are 19 main panels in all, fitted with the usual Westinghouse type of instrument, switches, etc. There are 10 main feeders passing from the power-station to various parts of the line. The cables are all of the lead-covered paper insulated B.I.W. type.
The rolling stock of the railway consists of 24 motor-cars, and 37 trailers. Of the former, 12 are first class, and 12 third class. Of the trailer-cars, 16 are of the first-class type, and 21 are third class. The cars are built on the corridor principle, and are 60 feet long. The trucks are of the Baldwin type; each motor-car is equipped with motors, each of 100 h.p., one driving each axle. The controllers are of the Westinghouse electro-pneumatic type, and are arranged for series-parallel control of 4 motors each. Automatic couplings of the Buhoup three-stem type are used on the cars. The Westinghouse quick-acting air-brake is employed throughout on the stock. There are also hand-brakes fitted, which are operated from either end of the cars. The motorman's compartment is lined throughout with asbestos slate.
Liverpool Engineering and Condenser Co.
Liverpool Engineering and Condenser Co
The specialities of this firm consist principally of Quiggin's evaporators, food-water heaters and filters, and fresh-water distilling machinery generally, also Quiggin's " Dripless " type surface- condensers. The evaporating and distilling plants on the Cunard steamers " Lusitania " and " Mauretania " were supplied by this firm, and the distilling machinery for several British cruisers and destroyers are also in progress. The works are small but compact, and ordinarily employ about 200 men.
Liverpool Hydraulic Power Co
There are now about 28 miles of hydraulic mains laid in Liverpool, extending from Harrington Dock at the south to Millers' Bridge, Bootle, at the north, stretching back from the river as far as Monument Place, London Road; further extensions are laid as demand arises. The mains in the streets vary from 7 inches internal diameter to 2 inches. They are laid in circuit as far as possible, controlling valves being provided at short distances apart to allow of a small section being shut off for repairs or extensions.
The works were originally started in 1887 and are now supplying power to about 1,100 machines, including passenger and goods lifts, jigger hoists, presses, motors, pumps, ejectors, and vacuum-cleaning apparatus.
The pumping stations are situated, one in Athol Street, on the west bank of the Leeds and Liverpool Canal, and a second in Grafton Street, on part of the ground formerly occupied by the Mersey Forge Co.
At the older station there are five sets of Ellington's compound condensing engines, each of 200 i.h.p., made by the Hydraulic Engineering Co. of Chester, supplied with steam by five Lancashire boilers, fitted with Vicars' mechanical stokers and two Green's economisers, the gear of these being driven by Brotherhood three cylinder hydraulic engines. The pressure in the mains is regulated by two accumulators with rams 18 inches diameter and 20 feet stroke, loaded to a pressure of 750 lb. per square inch.
The newer station at Grafton Street at present contains two sets of Ellington's triple-expansion compound engines of similar power to those at Athol Street, and three Lancashire boilers with Vicars' stokers, Green's economisers, and Dixon's superheaters. Foundations are prepared for two more engines, and space is provided for four further sets and three more boilers. The two accumulators at Grafton Street are 20 inches diameter and 23 feet stroke.
Liverpool Post Office
LIVERPOOL POST OFFICE - TRUNK TELEPHONE EXCHANGE[1].
In 1896 the Postmaster-General purchased the trunk telephone lines then in existence from the National Telephone Company, and from that date the long-distance telephones of the country have been worked by the Post Office.
New apparatus, in accordance with the latest developments of science, has been required from time to time. The Liverpool switch-room was re-equipped in 1906, with a system which involved the provision of incandescent electric lamps for signalling, at a cost of £8,000. That system soon became obsolete, and the new equipment joist opened has been erected at a cost of £12,000. It comprises a fuse-board (1,169 fuses), trunk and junction intermediate distributing frames, trunk and junction relay racks, time-check cabinets, cable troughings, and forty-two 3-panel trunk and junction switch sections — providing accommodation for 420 trunk circuits — and two supervisors' desks. The forty-two switch sections forming the present installation occupy three sides of a rectangle, the two long sides of which can be extended when the traffic warrants an increase in the number of switch sections, whilst the fourth side is occupied by a small local section for 200 lines together with the record transfer section and a Dey time-register.
The test- and apparatus-room are adjacent to the switch-room and divided from it by the sections and a partition. Owing to the noise caused by the driving mechanism, the time-check apparatus is placed in the linemen's room, which is readily accessible from the switch-room.
The sections are of iron, faced with mahogany, and as there is a clear width of 28 1/2 feet between the sections, the switch-room has no appearance of being crowded. The table in the centre of the room is the record table at which requests for trunk service are received by operators, who make out tickets and place them on the travelling band. They are carried by it to the end of the table, and thence by hand to the switching operators. Each set of cables from the fuse-board, intermediate distributing frame, time checks, relay racks, etc., is accommodated in a separate run. The installation was manufactured and erected by the British Insulated and Helsby Cables, Limited.
For supplying current to the Exchange three sets of accumulators of 12 cells, each 720 amp.-hours, and of the Tudor type, are installed; two of these give negative 24- and positive 24-volt powers, whilst the third remains idle, or is being charged. There are also auxiliary sets of cells K-7 E.P.S., for supplying negative 12- and positive 12-volt powers for the permanent current automatic clearing signals. The cells can either be charged through a charging resistance direct from the Department's electric-light supply, or by means of a D.C. motor and D.C. generator set, fitted next the battery-room. The motor is of the multipolar enclosed ventilated type, with shunt-wound fields and slot-wound armatures, designed for a terminal pressure of 105 volts continuous. The generator is similar to the motor in construction, and is designed for an output of 5 kilowatts at a terminal pressure of 32.5 volts continuous; it is capable of a variation of terminal pressure at this load between 32.5 and 24 volts.
The power switchboard is fitted with the usual automatic circuit- breaker, cut-outs, and switches of the open type, quick break, and the ordinary measuring instruments, ammeter, voltmeter, recording ammeter, etc.
The number of calls dealt with at this Exchange is between 8,000 and 9,000 daily, and the daily traffic with London approximates to 400 calls, and with Manchester to 2,000 calls. The majority of outward trunk calls are connected within ton minutes from the time they reach the switch-room, and most of those for Manchester within five minutes. Forty more trunk lines are in the course of erection.
Liverpool United Gas Light Co.
LIVERPOOL UNITED GAS LIGHT COMPANY
Liverpool United Gas Light Co
The manufacture and supply of gas to Liverpool and its suburbs is in the hands of a Company, which dates back to the year 1818. The capital invested amounts to about £2,000,000, the annual make is fully 4,200 million cubic feet, and the consumers are about 126,000 in number. The district supplied has an area of about 40 square miles and the main pipes laid reach a total length of 893 miles. There are six works, situated in various parts of the district, and although three of them are over 80 years of age, the plant has been altered from time to time as opportunities occurred, and is at present fairly up to date. An invitation had been given to the members of the Institution of Mechanical Engineers to visit the Linacre Gas Works, which is the largest of the Company's stations.
LINACRE WORKS.
These works were opened in 1867, and were built to meet the rapidly increasing demands made upon the Company. They are situated in the Borough of Bootle, on the banks of the Leeds and Liverpool Canal, by which there is a direct connection to the Wigan coalfield. An overhead railway-siding enables coal also to be obtained from Yorkshire and the Midlands by the Midland Railway Co. The area now covered with buildings and plant occupies nearly twenty-five acres of land. The first section, having a daily make of 1 1/2 million cubic feet of gas, was followed in 1872 by another, with a capacity of fully 3 millions; and in 1873 an additional plot of ground was obtained on which plant for 5 million cubic feet per day was subsequently erected. The success of the carburetted water-gas process at Garston led, in 1897, to the erection of a plant at Linacre, which was accommodated in the oldest retort-house and coke-yard. By this alteration an output of 11-million feet was replaced by 41 millions per day; and provision is made for duplicating the plant when the need arises.
Retort-Houses. — In the north section there are three retort- houses forming one building. In one there are fourteen beds of sixes, hand charged and drawn. In the other two are twenty-six beds of sixes, charged and drawn by Arrol-Foulis machines, with the necessary coal-breaking and -handling plant.
In the south section there are two retort-houses. No. 1 House has a bench of inclines — eight beds of eights — with the usual coal-handling plant. Coal is taken from the canal barges by a jib-crane and grab, and delivered to an Ingrey automatic weighing-machine, from which it passes through a breaker to a twin elevator, and thus is conveyed to hoppers in the roof of the retort-house. Some old retort-beds occupy the other half of the building, but will make way for modern plant in the near future. Coal-stores, on each side, run the length of the building.
No. 2 House was formerly fitted with horizontal retorts, operated by four pairs of Arrol-Foulis machines with the necessary coal-breaking and -handling plant, but this installation has been swept away and is being replaced by the latest design of horizontal retorts, operated by Fiddes-Aldridge discharging and recharging machines. One half of the plant has been at work since last December, and the installation will be completed in the course of a few months.
Coal is removed from the canal barges by two locomotive jib-cranes and grabs, and is delivered into an Avery automatic hopper, weigher, and totalizer; from thence it passes through a double coal- breaker with by-pass screens, and is elevated and deposited in a continuous overhead hopper, from which it is automatically taken by the Fiddes-Aldridge machine.
The coke on being pushed out of the retorts is received by skips, and these are conveyed out of the retort-house by a telpherage coke-handling plant. The hot coke is quenched by the skip being dipped in a tank of water, and it is then conveyed to a screening and storage plant or deposited on the stock heap. The whole of the plant is electrically driven, and current is generated by three sets of gas-engine and dynamo installed in a part of the old coal-stores.
Condensers, Brushers, etc. — (North Section.) — There are eight parallel sets of condensers, 31 feet high, each consisting of 44 cast-iron pipes, 12 inches diameter, arranged vertically, with cast- iron connecting boxes at the top and bottom. Two cyclone tar-separators have just been installed to relieve the scrubbers, which have been scarcely able to deal with the tar contained in the foul gas. There are six scrubbers, 8 feet square and 24 feet high, arranged in two parallel sets of three each. There are two " Standard " washer-scrubbers, each having a capacity of three million cubic feet per day.
(South Section.) — There are eight parallel sets of 12-inch vertical east-iron pipe condensers, 30 feet high, each consisting of fifty-six pipes and cast-iron connecting-boxes at the top and bottom. There are three Livesey washers, two of them having a capacity of two million cubic feet per day, and the other of three millions. There are also three " Standard " washer-scrubbers, two of these having a capacity of two millions per day, and the other of three millions; the latter is fitted with " Holmes " brushes and used for the extraction of cyanide from the gas.
Purifiers. — (North Section.) — There are six purifiers, 52 feet by 26 feet, for treating carburetted water-gas; also two boxes 58 feet by 27 feet, and two boxes 43 feet by 34 feet for coal-gas. They are provided with a system of water-sealed valves, and shoots for discharging the boxes on to the floor below. The material used is lime throughout.
(South Section.) — In the main building there are eight purifiers, each 36 feet by 23 feet, which are provided with water-sealed valves and shoots for discharging the material on to the floor below. The boxes are fitted with Spencer's hurdle grids; but these are covered by a deep layer of oxide above them, in order that sufficient time- contact may be ensured. There are also two check-boxes, each 39 feet by 25 feet, in a covered yard. The material used is bog ore.
Exhausting Machinery. — (North Section.) — There are three two-blade exhausters, by Messrs. Bryan Donkin and Co., each with a separate engine and having a capacity of 200,000 cubic feet perhour. These exhausters are placed between the scrubbers and the washer-scrubbers.
(South Section.) — There are three Beale exhausters, by Messrs. W. H. Allen and Co.; two of them have a capacity of 100,000 cubic feet per hour, and the third of 150,000 cubic feet. A separate engine is provided for each exhauster.
Distributing Exhausters. — A portion of the gas manufactured at the Linacre Works is pumped to some of the other town stations for distribution. For this purpose, four pairs of exhausters, each having a capacity of 65,000 cubic feet per hour, are employed, each pair being driven by one engine. The makers of these exhausters are Messrs. Gwynne and Co.
Station Meters. — (North Section.) — Nos. 1 and 2 are each of a capacity of 45,000 cubic feet per hour. Nos. 3 and 4 are of 60,000 cubic feet capacity each. No. 7, for carburetted water-gas, has a capacity of 175,000 cubic feet per hour.
(South Section.) — Nos. 5 and 6 are each of a capacity of 125,000 cubic feet per hour. All of the meters were made by the Gas Meter Co. of Oldham.
Gas-holders. — The particulars of the various gas-holders are embodied in the following Table
No. | Diameter (ft.) | Lifts. | Depth (ft.) | Capacity (cu.ft.) |
1 | 140 | 2 | 60 | 859,000 |
2 | 140 | 2 | 60 | 859,000 |
3 | 152 | 2 | 60 | 1,007,000 |
4 | 140 | 2 | 60 | 859,000 |
5 | 163 | 2 | 60 | 1,176,0005 |
6 | 163 | 3 | 90 | 1,739,000 |
7 | 178 | 2 | 60 | 1,420,000 |
8 | 178 | 2 | 60 | 1,413,000 |
Governors. — Five governors with by-passes are accommodated in a building that adjoins the north entrance-gate, and one was subsequently erected at the south-east corner of the gas-holder yard.
Carburetted Water-Gas. — This plant was supplied and erected by Messrs. Humphreys and Glasgow, in 1897. There are four sets of a capacity of one million feet and two of half-a-million cubic feet per day. Three boilers (Babcock and Wilcox) raise an ample supply of steam for all purposes. They are being fired with gas tar by the Kermode Liquid Fuel System. The machinery comprises blowers, exhausters, pumps, etc.; and these are capable of also dealing with an additional installation of producers. Coke is raised to the firing floor by means of a hydraulic hoist. The scrubbing and condensing plant is situated outside the building, and two settling-tanks deal with the foul water. The gas is purified with oxide of iron and lime, and after passing through a station meter is uniformly mixed with the coal-gas. Oil is received by rail, road, and canal, and is stored in a tank of 1,700 tons capacity. At the present prices of coal and oil, the manufacture of carburetted water-gas is of considerable advantage, and at all times the indirect benefits are very great.
Cyanide Process. — The process is that brought out by Messrs. Davies and Neill, and known by that name. The cyanides in the gas are, as far as practicable, extracted by the action of a solution of soda and ferrous carbonate in a "Standard" washer. The resultant liquor is passed through a still, so that any ammonia in it may be driven off by means of wet steam. This is condensed and run into the liquor wells. The cyanide liquor is passed through a filter-press to separate insoluble matter. The clear solution and washings from the filtering press are concentrated by dry steam in a Kestner evaporator and run into vats to crystallize. The crude crystals (sodium ferro-cyanide or prussiate of soda) are washed with mother-liquor to remove soda and insoluble matter, then re-dissolved in a small quantity of hot water; any insoluble matter is allowed to settle, and the clear liquor run into crystallizing vats where the prussiate of soda slowly forms saleable crystals on pieces of rope that are suspended in the liquor.
The plant is accommodated in a two-storey building, and is capable of dealing with gas from 500 tons of coal per day. The mixture for use in the washer is prepared in special vessels, and the precipitated ferrous carbonate is separated from the sodium sulphate solution by filter-presses, and then mixed with soda and water. Steam is raised by a Cochrane boiler situated outside the building, or is taken from adjoining boilers. The process has been in operation since April 1905, when an arrangement was made for the patentees to work it and to pay for each ton of coal used in the manufacture of the gas treated for cyanide; but since November 1906 the plant has been the property of the gas company and under its control. The financial results have been very satisfactory; and no inconvenience or nuisance has been caused by the operations.
Mersey Docks and Harbour Board Estate.
MERSEY DOCKS AND HARBOUR BOARD ESTATE. BRIEF DESCRIPTION OF CERTAIN DOCK WORKS.[2]
Mersey Docks and Harbour Board
Brocklebank Graving Dock. — This dock was opened in January, 1906, and is one of the most recent additions to the list of Liverpool graving docks. It has a length of 804 feet and a width of 96 feet. The depth of water on sill is never less than 30 feet, the water in the group of docks through which it is approached being permanently maintained at that height by pumping water from the river to make good the leakage and lockage. On high spring-tides the depth on the sill is 44 feet. This graving dock has several features of interest, inasmuch as it was, before conversion, a wet dock with vertical side walls; these were under-pinned, and altar-courses provided projecting 2 feet from the face of the walls. A new entrance, of a bell-mouth shape, was constructed, so as to facilitate the docking of large vessels. The gates are of unusual size, namely, 135 feet wide from hollow quoin to hollow quoin. They are constructed of steel, and provided with buoyancy chambers, with the double object of reducing the weight on the rollers and of facilitating handling when repairs are necessary.
Two 48-inch centrifugal pumps are provided for drying the dock, and one 14-inch pump of the same type double lift, running in series, for dealing with leakage water. The pumps were supplied and fixed by Messrs. Tangyes, Birmingham. The main pumps are driven by gas-engines of 500 b.h.p. each, made and fixed by Messrs. Crossley Brothers, Manchester. The pumps can, when necessary, dry the dock in 3 hours When there is a depth of 34 feet of seater on the chamber floor to commence with. When not required for pumping out the graving dock, the pumps are, on most tides, used to assist in pumping water from the river into the adjoining wet docks, which, as previously mentioned, are worked on the impounded system. Powerful electric lamps are provided to facilitate docking at night-time, also portable incandescent electric lights for use in chamber of dock.
Canada Graving Dock. — The Canada Graving Dock, opened in 1899, is the largest graving dock in the Port, being 925 feet 6 inches in length, 124 feet wide at the top and 94 feet at the bottom of chamber. The entrance is 94 feet wide, and has a depth of water on sill varying from 30 to 44 feet, the wet docks through which it is approached being impounded as in the case of the Brocklebank Graving Dock. The pumping plant is on a scale commensurate with the size of the dock, and consists of three sets of main pumps each driven by vertical direct-acting steam-engines. The steam is supplied by six Babcock and Wilcox boilers. The pumps, three in number, each 51 inches diameter, are of the "Invincible" pattern, and were supplied and fixed by Messrs. J. and H. Gwynne, of London. They are capable of emptying the dock of 34 feet of water in 11 hour. The ordinary drainage is provided for by a pump of the same type, 14 inches diameter. To deal with heavy lifts a 40-ton hydraulic crane is provided. This can travel the whole length of the dock, and lift a maximum load from a point beyond the centre of dock. Powerful electric lamps are provided to facilitate docking at night-time, also portable incandescent electric lights for use in chamber of dock.
Canada Branch Dock No. 3, Coaling Hoist. — This coal-hoist, which is of recent construction, was primarily designed with a view to affording increased facilities for the delivery of bunker coal into large steamers. It has a capacity of 300 tons of coal per hour. The hoist is designed to coal vessels up to 88 feet beam at a maximum height of 40 feet above coping-level. It is movable, and is worked by hydraulic power at a pressure of about 750 lb. per square inch supplied from the Canada Hydraulic-Power Station. The lifting and tipping is accomplished by rams fitted with a multiplying gear, wire-ropes being used throughout. Wagons are run on and off the cradle of the hoist by means of a double traversing turn-table, fitted with small hauling capstans. The maximum load which this hoist can deal with is 30 tons gross. The hoist is fitted with an anti-breakage crane to prevent excessive breakage of the coal at the commencement of the operation of loading.
Canada Hydraulic-Power Station. — This station is situated on the west side of the Canada Lock, and, in conjunction with the station at the Langton Graving Docks, supplies the necessary hydraulic power to all the machinery in the northern portion of the Dock Estate. The pumping machinery consists of three sets of triple-expansion engines, marine type, with cylinders 15 inches, 22 inches, and 36 inches diameter, with a stroke of 2 feet driving rain-pumps. Two accumulators, weighted so as to give the requisite 750 lb. pressure per square inch, are provided, the stroke of each being 16 feet and the rams 17 inches diameter.
Huskisson Pumping Station. — The northern group of docks, from Hornby to Sandon inclusive, are worked on the " impounded " system, that is, the water is not allowed to fall lower than the level of high water of a low spring tide. The half-tide docks, which are run down to the level of the tide of the day, serve as locks for vessels to pass in and out at high water. This arrangement allows of comparatively shallow docks being used over neap tides by deep draughted vessels. The pumps are provided for the purpose of soaking good the water lost through lockage and leakage, for which purpose water is pumped from the river into the docks. The pumps at this station are four in number, three of 51 inches and one of 54 inches diameter, all of the "Invincible" centrifugal type, supplied and fixed by Messrs. J. and H. Gwynne. Each pump is driven by a direct-acting vertical engine having cylinders 22.5 inches and 42 inches diameter, 30 inches stroke in the case of 51-inch pumps, the corresponding figures for the 54-inch pump being 22, 40, and 30. Steam is supplied by three marine-type boilers 14 feet 6 inches diameter and 10 feet 6 inches long. The working pressure is 100 lb. per square inch. The pumps at the Brocklebank Graving Dock, when not required for drying the dock, are used in conjunction with the pumps in the Huskisson Station for impounding purposes.
Sandon River Entrances, and the group of Modern Docks adjoining them. — The Sandon River Entrances were finished in 1900 and were part of a programme of remodelling of this portion of the Dock Estate. The entrances, together with the half-tide dock, were designed to afford a means of communication between the river and the docks south and north of them, and to admit the largest vessels coming to the port. The entrances are 100 feet, 80 feet, and 40 feet wide respectively, each provided with two pairs of gates, to form locks for the use of smaller craft between tides. The sills of the 100-ft. and 80-ft. entrances are 20 feet 6 inches, and the 40-ft. entrance 16 feet below Old Dock sill datum, and have a depth of water in the two wide entrances varying from 30 feet at high water of low neap-tides to 41 feet at high water of equinoctial spring-tides. The gates are constructed of greenheart throughout, and are worked by cross chains attached to hydraulic rams.
The Canada, Huskisson, and Sandon Docks, which, with others, are served by these entrances, are of the latest construction, and are capable of accommodating the largest liners afloat. These docks have up-to-date modern sheds of the single and double-storey types, folly equipped in all respects for the reception and sorting of goods. The double-storey sheds have movable hydraulic cranes of 30 cwt. capacity placed on their roofs, and on the roadside of the sipper floors hand-lowering jiggers, and in some cases hydraulic cranes of 1 ton power are fitted to permit of the quick despatch of goods into carts or wagons from the upper floors. Railway sidings are laid along the roadside of the sheds at suitable places, and are connected with the various railway goods stations. The total water area of the Canada, Huskisson, and Sandon Docks with their branches is nearly 108 acres, and their total length of quay is over 5 miles.
Tobacco Warehouses, Stanley Dock. — The tobacco brought to this port was, previous to the year 1901, stored at various warehouses on the Dock Estate. The trade, however, became so great that it was necessary to increase the accommodation and to concentrate it in one position. That of the Stanley Dock, where there were already two large six-floor warehouses, each 627 feet long and 90 feet wide, then largely used for tobacco storage, was decided upon. A new warehouse on the southern portion of the Stanley Dock, 726 feet long, 165 feet wide, and having fourteen floors, was constructed and opened in 1901. This warehouse has a total floor-area of 36 acres, and is capable of storing about 60,000 hogsheads of tobacco, the total storage capacity of new and old warehouses being 100,000 hogsheads. In the older warehouses, which were designed for general produce, the hogsheads have to be stored in many cases three tiers high, and there is, consequently, considerable difficulty and expense in storing and unstoring. The new warehouse has been designed to store one tier high only, so avoiding the disadvantages above-named.
The new warehouse is fully equipped with modern appliances and is lighted throughout electrically. To provide against fire an elaborate system of appliances is installed. Outside staircases are provided on the dock side, and adjoining these, vertical stand-pipes with fire-service valves and nozzles for hose attachment at each floor, are fitted.
Landing Stage, Floating Roadway, and Riverside Passenger Station. — This stage, which comprises the Prince's, Ferry Goods, and George's stages, has an aggregate length of 2,478 feet, and a width generally of 80 feet. It is placed about 100 feet from and parallel to the river wall, and attached thereto by eight bridges and six booms. To prevent undue lengthwise movement from the flow and ebb of the tide, heavy crosswise mooring chains are provided. The pontoons supporting the stage are placed side by side at right angles to the stream, and on them rest five longitudinal box girders, which in turn support a series of cross girders or deck- beams carrying a double planking of greenheart.
The Prince's Stage, 1,368 feet long, is appropriated to the use of coasters and the large Atlantic liners which embark and disembark passengers and snails thereat.
The Ferry Goods Stage has a length of 305 feet, and, as its name implies, is used for ordinary ferry goods traffic between Liverpool and Cheshire.
The George's Stage, 805 feet in length, is used exclusively for ferry passenger traffic. Access for traffic to the several stages is provided by eight bridges and a floating roadway, all of which are used by foot passengers; five of the bridges are also available for vehicular traffic. The floating roadway, which has a length of 550 feet and a width of 35 feet, is designed to provide an easy incline for vehicles at all states of the tide. It is carried on groups or nests of pontoons, and is so constructed that the incline is never greater than 1 in 21.
Immediately at the back of the Prince's Stage is the Customs Depot for examining baggage, and on the pierhead adjoining is the Riverside passenger railway station, where special trains arrive and depart with the passengers of the great liners and their luggage. The luggage is transferred, as well as mails for London and other parts of the country, from stage to Customs Depot, by means of mechanical conveyers worked by gas-engines.
Herculaneum Dock Coaling-Cranes and Hoist. — These appliances are on the east side of the Herculaneum Dock and Branch Dock, and consist of two large movable cranes, capable of lifting a weight in one case of 30 tons, and in the other of 25 tons gross, inclusive of wagon and cradle; and a stationary coal-hoist, for delivering coal into flats or other small craft, which is capable of dealing with wagons of 23 tons gross. All these appliances are worked by hydraulic power. The two cranes deal with both bunker and export coal. In operation, wagons are run on to a cradle suspended from the crane, both wagon and cradle are lifted by the crane, and when in position over the vessel's hatch the contents of the wagon is tipped endwise in the ordinary way. The cranes are of such dimensions as to allow of the coaling of vessels up to 60 feet beam, and will raise the wagons so as to clear a height of 25 1/4 feet above quay-level in the case of a vessel of that beam. The hoist is of the platform type, that is, wagons are run singly on to a platform which, together with the wagon, is raised to the required height by hydraulic cylinders and wire-rope gearing, when it is tipped into a shoot for delivery into the vessel's hold.
Hydraulic and Electric Roof-Cranes, King's and Queen's Docks. — The south end docks, though designed with the idea of accommodating a slightly smaller class of shipping than the north end docks, are nevertheless equipped in the most modern manner. In particular the sheds at the King's and Queen's docks are among the finest on the Dock Estate, and the best facilities in the way of cranes and transporters are provided on the roofs of the double storey sheds for the handling of cargoes between ship and shed. The cranes are of three types all of 30 cwt. capacity, made to travel along the shed roofs, namely, the ordinary hydraulic and electric roof- cranes of the jib type fitted with luffing and sluing gear, and electric transporters with carriers. The electric cranes are of the same general form and power as the hydraulic roof-cranes. The electric transporters project horizontally out from and at right angles to the shed on which the carriers work. When not in use the projecting arm, or runway, is hoisted up to a perpendicular position over the shed clear of all shipping. The power for working the electric cranes and transporters is taken from the Liverpool Corporation supply mains.
Woodside Lairage. — The Woodside Lairage is situated on the Cheshire side of the river adjoining the Woodside Ferry of the Birkenhead Corporation, and forms part of the Birkenhead Foreign Animals Wharf. Cattle, etc., are landed at either Wallasey or Woodside landing stages, and are driven through runways to either of the lairages as required. The capacity of the combined lairage is: cattle 6,172, sheep 16,000.
Generally, the killing is done at Woodside, where there are spacious slaughter-houses, meat-stores, and chill-rooms. There is also a large meat market specially fitted for the display of meat. Extensive accommodation of a similar class is provided at Wallasey.
The slaughtering capacity of the two lairages is Woodside 2,100 beasts in 24 hours, and Wallasey 1,300. The chill-rooms and meat- stores can accommodate 2,250 and 1,300 carcasses respectively. The chill-rooms at Woodside have a capacity of 2,080 carcasses in all, and those at Wallasey 1,300 carcasses. The refrigerating apparatus is designed to lower the temperature of the beef to a little above freezing-point, so that it may be transferred in good condition by rail to other parts of the country. The refrigerating apparatus at Woodside is on the ammonia-absorption principle in three units of 50 tons ice-making capacity each; that at Wallasey is on the ammonia-compression Linde system. Both lairages are connected by sidings with the main lines of five large railway systems.
Sand pump Dredger "Leviathan." — The "Leviathan," which was built by Messrs. Cammell Laird and Co., specially for the purpose of obtaining increased depth in the sea-channels of the Mersey, is a twin-screw vessel having a net hopper capacity of 180,000 cubic feet, and capable of filling herself with 10,000 tons of clean Mersey sand in 50 minutes, from a maximum depth of 70 feet. Her principal dimensions are .—length, 465 feet 9 inches between perpendiculars; breadth, 69 feet moulded; and depth, 30 feet 7 inches moulded. The propelling machinery is of the ordinary triple-expansion inverted marine type, with cylinders 221 inches, 37 inches, and 61 inches diameter, and a stroke of 45 inches, constructed by Messrs. D. Rowan and Co., Glasgow, who also supplied the boilers, four in number, 16 feet diameter and 11 feet 9 inches long, working under a pressure of 180 lb. per square inch, with natural draught.
The pumping machinery and pumps, built by Messrs. Gwynne, of London, consists of four centrifugal pumps with suction pipes 42 inches diameter, driven by four independent inverted triple- expansion engines, with cylinders 15 inches, 25 inches, 40 inches diameter, and 18 inches stroke, working at 180 lb. pressure. The hopper space is divided into twelve separate hoppers, six on each side of the central line bulkhead. The discharge of the hoppers is effected by valves invented by Mr. A. G. Lyster, each of which consists of a large tapered circular cylinder, raised from its seating by a hydraulic ram, which receives its supply from the compressor in the pump-room. With these valves perfect control of the ship can always be maintained—a very important point when dealing with large quantities of sand.
The Sand pump Dredger "Coronation." — This vessel has a length of 345 feet, a beam of 53 feet, and is generally of the same type but smaller than the " Leviathan." She has a capacity of 3,500 tons, and is capable of loading herself from a depth of 60 feet in fifty minutes. The vessel was built by Messrs. Vickers, Sons and Maxim in 1904, and is fitted with twin screws and propelling engines of the triple-expansion inverted type. The pumps are centrifugal, and are driven direct by triple-expansion engines.
Bucket-Ladder Dredger "Vulcan." — The "Vulcan" is a twin- screw self-propelling centre-ladder bucket-dredger,186 feet long and 41 feet wide, specially constructed for dredging reek or other hard material. It can work in a depth of 55 feet, and can lift and deposit in attendant hoppers at the rate of 1,000 tons of hard clay per hour. The vessel is specially designed to cut her own flotation into a bank of material. It was constructed in 1904 by Messrs. Fleming and Ferguson.
"Miles K. Burton." — This vessel was built by Messrs. William Simons and Co., Renfrew, in 1897, and is the largest of the Board's grab dredgers, having a length of 230 feet and a beam of 35 feet. She is a self-propelling self-contained hopper of 1,200 tons capacity, constructed to dredge in 47 feet. Her propelling engines are of the usual inverted typo, with cylinder 18 inches, 28 inches, and 47 inches diameter, and stroke 27 inches. For working the grabs, five hydraulic cranes are provided each having a lifting power of 112 cwt., inclusive of the grab. The pressure-water is supplied by a pair of compound hydraulic engines and compressed-air accumulator. The hydraulic installation and cranes were supplied by Messrs. Armstrong, Whitworth and Co.
The dredgers above described are representative types of a large number of appliances employed by the Board for the maintenance of the docks and sea channels, and for the construction of new docks and waterways.
Mersey Engine Works
MERSEY ENGINE WORKS CO., LIVERPOOL.
Mersey Engine Works Co
These works are situated near the Brunswick Station of the Overhead Railway, and are specially laid out for dealing with repairs to steamers, all classes of work being undertaken for engine or bull repair. The works are driven by electricity, which is generated by means of a gas-engine and gas-producer.
National Telephone Co
NATIONAL TELEPHONE CO. LIVERPOOL TELEPHONE SYSTEM.
National Telephone Co
The Liverpool Telephone area is an extensive district comprising about 100 square miles and covering a large portion of S.W. Lancashire and the Wirral district of Cheshire. Besides Liverpool and Birkenhead, it includes Bootle, Wavertree, Walton, Garston, Gateaere, Formby, Crosby, Hoylake, Huyton, Ellesmere Port, and other localities.
To serve this busy area, in which some 27,000 telephones are in use, 27 exchanges are employed; and in addition four large new exchanges on the central battery system will shortly be opened. In the central battery system the speaking and calling current at the subscriber's instrument, as well as at the exchange, is supplied from one common battery situated at the exchange.
The "Royal" exchange, situated between Great George Street and Rathbone Street, is one of the most recent of the existing exchanges. It serves an area principally in the south and south-west districts, which is to a large extent residential, although a number of business subscribers in the southern part of the town are also served from this exchange. The premises were specially built for the purpose, and can, when fully equipped, accommodate about 10,000 subscribers' lines. At present there are upwards of 4,300 working. Although the magneto instrument is still retained at the subscribers' end, the "visual" signal system is in use at the exchange, and the subscriber automatically gives the "clear," causing a tiny lamp at the switchboard to glow when he has finished his conversation.
The apparatus room, where the testing is done, is planned on a large scale, and the method of distributing the lines so that the operating load is equalized to a largo extent is of considerable interest. It will be understood that the frequency of calling by subscribers varies enormously, and it is necessary to make arrangements whereby each operator has connected to the part of the switchboard to which she attends her proper proportion of busy and quiet lines.
The power-room on the basement contains the apparatus for supplying the necessary energy for both ringing and speaking. This apparatus consists of a set of accumulators from which the current for the apparatus is supplied. A dynamo for charging the accumulators is run by a 12-h.p. gas-engine (Crossley type), and, as a stand-by, a motor generator of 15-h.p., run direct from the Corporation main, is used. In addition there are ringing generators, one worked direct from the accumulators and the other from the Corporation main.
The operators' quarters, consisting of a dining, sitting, and rest rooms, are situated on the first floor, together with the kitchen and other offices. The number of calls originated in the exchange averages about 64,000 per day of twelve hours, allowing about fifteen calls per subscriber; besides this about 45,000 incoming calls are dealt with.
One of the largest of the new exchanges under construction is that situated at the junction of Thomas Street and South John Street and next to Eldon Chambers, which will be known as " Bank " exchange. As in the case of the " Royal " exchange, the building is specially constructed and adapted to the purpose. The switchboard will have an immediate capacity for serving 2,500 subscribers' lines; the part of the building at present approaching completion will accommodate a switchboard for 4,500 subscribers' lines, and the building is designed so that it will later be extended to accommodate two exchanges each of 10,000 lines capacity.
The basement will contain thes toros, a heating chamber, switch- chamber, and mechanics' and foremen's rooms. On the ground floor will be suites of offices for engineer, electrician, faultsmen, and instrument inspectors.
On the first floor is the apparatus room, which will contain the distributing frame, relay and register racks, repeating-coil rack and fuse-panels and the power plant. The latter will consist of two 'motor generators each having an output of 1,000 amperes at thirty volts for charging the battery of eleven accumulators, which have a present capacity of 3,700 ampere-hours with an ultimate of 8,100 ampere-hours, and there will also be two machines of 300 watts capacity for generating the ringing current.
The exchange itself, or switchroom, will occupy the second floor, and will at first consist of thirteen subscribers' sections with thirty-six operators' positions and four incoming junction sections with twelve operators' positions, making a present capacity for 2,500 subscribers' lines and 324 incoming junctions. Down the centre of the room desks will be provided for the exchange manager, clerk-in-charge, and monitors.
The whole of the third floor will be devoted to the personal needs of the operators, with the exception of two rooms set apart for an operating school for the training of young operators. The arrangement which now obtains in the large telephone centres provides for the systematic training of learners by experienced teachers, who put them through their paces at a dummy switchboard and by. oral and written examinations, and turn them out ready to take their places at the exchange. The other rooms on this floor are the kitchen, a large dining-room, where meals can be obtained at a very low rate, a rest room, and a comfortably furnished sitting-room.
Messrs David Rollo and Sons
MESSRS. DAVID ROLLO AND SONS, BOILER WORKS AND FOUNDRY, SANDHILLS.
David Rollo and Sons
These works are conveniently situated near to Sandhills Railway Station, at the corner of Derby Road and Sandhills Lane, and occupy an area of about 12,000 square yards. The forge and smiths' shop contains eight steam-hammers ranging from 5 to 50 cwt. In another part of the works there is a forge for the heavier class of shafting, rudder and stern frames. The firm has done much to develop the making of forgings under the drop-hammer, and most of this work is made to Admiralty requirements.
In the brass foundry are ranges of furnaces with large crucibles, and in the iron foundry is a 40-ton crane. For melting the various alloys a reverberatory air-furnace is employed, with a capacity of 10 tons.
Occupying an extensive range on the other side of the yard are the boiler shops, where boilers up to 18 feet in diameter by 22 feet in length are constructed. This department is well equipped with hydraulic riveting-machines. An adjoining building comprises the boiler repairing-shop, with sets of rolls, machines, flanging fires, etc. In addition to producing high-pressure boilers, and triple- expansion engines, the firm makes specialities of their heavy forgings and stampings, metal bearings of special alloys, propellers, tanks, ventilators, and iron foundry work. The number of men employed at these works and the Fulton Engine Works is about 1,500.
FULTON ENGINE WORKS, LIVERPOOL.
These works, belonging to Messrs. David Rollo and Sons, are employed in the construction of marine engines and boilers, and in the repairing of engines, boilers, and ships.
The machine, fitting, finishing and erecting shops are situated in Blackstone and Fulton Streets, and the boiler and pattern shops, coppersmiths' and whitesmiths' shops, iron and brass foundry, forge and smithy, having 12 steam-hammers, are at Sandhills. The works are lighted throughout by electricity. Among the special appliances are one 140-ton hydraulic riveting machine and another of 40 tons; a machine with five drilling heads for drilling boiler shells and ends in place; a hydraulic machine for flanging furnace fronts, and another for drilling them; a flanging hammer, and 12 drop hammers for hot stamped work.
Walker Engineering Laboratories
WALKER ENGINEERING LABORATORIES, THE UNIVERSITY OF LIVERPOOL.
Walker Engineering Laboratories
The Walker Engineering Laboratories were built about 20 years ago, by the generosity of the late Sir Andrew Barclay Walker. Extensive new laboratories are about to be erected.
In the building is a large, well-lighted and ventilated main laboratory, containing the following plant:-A Stirling water-tube boiler with forced draught, air-heater, and live-steam feed-beater; independently fired two-stage superheater, designed to raise the temperature of the steam to 750° F., and arranged so that besides superheating the steam before admission to the high-pressure cylinder, the steam can also be superheated again before admission to the intermediate cylinder; a triple-expansion marine engine of 150 b.h.p.; a Bateau turbine of 60 b.h.p., directly coupled to a direct-current generator, the field-magnet casing of which is mounted on ball- bearings and used as a brake for the measurement of the brake horsepower; a 15 b.h.p. De Laval steam-turbine driving a high-lift centrifugal pump, which delivers its water to a Pelton wheel. This water is measured in three different ways, namely, by a Venturi meter, by a rectangular weir, and by a V notch; a De La Vergne refrigerating plant, by L. Sterne and Co., capacity 1 ton of ice in 24 hours; one 24 b.h.p. National gas-engine with tube and magneto ignition, and means of varying the compression pressures; one 8 b.h.p. Premier gas-engine. Three producers, one "National " type, one "Mersey" type, and one experimental producer for use with bituminous fuel; a 7-b.h.p. Gardner paraffin oil-engine; two two-stage intercooled air-compressors; one Alley and MacLellan, having a capacity of 200 cubic feet of free air per minute, and delivery pressure up to 220 lb. per square inch; and one Worthington with a capacity of 35 cubic feet of free air per minute, and a delivery pressure up to 250 lb. per square inch.
The laboratory also contains a 100-ton Wicksteed testing-machine fitted with alternative centres, by which it can be converted into a 20-ton machine. Other apparatus includes content-testing machines, cross-breaking machine, and impact testing-machine.
The smaller experiments of the heat-engine course are carried out in the experimental laboratory on the first floor. This laboratory contains a Sirocco fan testing-set by Messrs. Davidson and Co., Belfast, model boilers, fuel calorimeters, gas analysis, and other small apparatus. A departmental library is provided on this floor for the use of students.
The third floor contains the drawing hall, which is well lighted both by natural and artificial means. The chief applied mechanics laboratory is housed in a separate building in the quadrangle. The work done includes determination of efficiencies of various forms of lifting tackle and hoisting gear, deflection of beams, torsion of shafts, friction of belts and ropes on pulleys, and vibration of springs and structures. The hydraulic equipment consists of weirs, notches, orifices, and experiments relating to the flow of water in channels and pipes, centrifugal pumps, hydraulic ram, etc.
There are at present four principal departments in the Faculty of Engineering—Mechanical, Civil, and Electrical Engineering, and Naval Architecture, each under a separate professor.
George Holt Physics Laboratory. — This laboratory was opened by the late Lord Kelvin on 12 November 1904. It covers an area of 9,600 square feet, and has an average height of 55 feet. The external walls, which are very substantial, are built in best common brick with broad courses of red brick and dressings of Storeton stone. The basement floors are asphalt on a bed of concrete resting on the continuous rock which is the foundation of the whole building. All the upper floors are fire-proof; they consist of a bed of concrete which encases a lattice-work of steel girders and supports a layer of coke breeze, upon which tongued and grooved pitch-pine boards are stuck down with bitumen and nailed. The resulting surface is both noiseless and steady, and the whole building is made very rigid by the girders employed.
In the basement there is a large workshop, fully fitted with machine-tools, store-rooms, a room containing a liquid-air plant, a furnace room, an accumulator room, a room for the custody and comparison of standards, and a number of research rooms, in which extra steadiness, complete darkness, or constancy of temperature can be respectively secured.
On the ground floor, close to the entrance-hall and cloak-rooms, are the doors of the large lecture theatre, a smaller lecture room, and a large laboratory for elementary students. This floor also contains the preparation room, the apparatus room, and a sitting-room, office, and private laboratory for the professor. The first floor is set apart for the teaching of senior students. It contains two large students' laboratories, four smaller rooms, suitable for optical and acoustical experiments, a students' workshop, a library, and two private rooms for demonstrators.
The second floor consists almost entirely of research rooms of various sizes. Of these, some are designed for special purposes, such as spectroscopy, but the majority are planned so as to be adaptable to as great a variety of needs as possible. A photographic dark room is provided on each floor; that in connection with the preparation room is adapted for the making of lantern slides and enlargements. There is also a small observatory on the roof, containing a four-inch equatorial telescope.
An electrically-driven lift, working in the centre of a tower, is available for the conveyance of heavy apparatus from floor to floor. It can also be used to give access for experimental purposes to all points of two vertical walls which extend to the full height of the tower, about 75 feet. In another part of the laboratory, access over a horizontal distance, about 90 feet, nearly equal to the whole length of the building, is secured.
The rooms are lighted by electricity, heated by low-pressure hot water, and ventilated by an exhaust fan in the roof. They are adequately supplied with gas, with sinks to which hot and cold water are led, with electric power from the Corporation mains, and with wires from a switchboard in the basement to which the accumulators are connected. All wiring is run in wood-casing on the surface of the walls; all pipes are fully exposed, and wherever a floor or wall is pierced, an opening is left through which further permanent or temporary connections can be made as required. The apparatus and preparation rooms have galleries round them, so that their whole wall-space is rendered available for cupboards and drawers. Special devices have been adopted for the ready darkening of the lecture theatre, and for the provision of rigid points of attachment above the whole length of the lecture table. The counter-shafting of the workshop is supported so as to be entirely independent of the rest of the building, and thus silence and freedom from vibration are secured.
The general scheme of arrangement of the laboratories is conducive to simplicity and economy of administration, and allows teaching and research to flourish side by side without mutual interference.
Laboratories of Applied Electricity. — These laboratories were opened in July 1905, by Sir Joseph Swan. They contain a lecture theatre, class rooms, a small departmental library, and numerous laboratories and test-rooms. The most important laboratory is that used for testing dynamos and motors of all kinds; it is a large, well- lighted room about 60 feet square, containing among other machinery a small Westinghouse gas-engine coupled to a dynamo (which is used for lighting the laboratory), and the under-truck and complete electrical equipment for a tramcar fitted with a dynamometer for measuring the draw-bar pull. One of the most interesting machines is a self-exciting alternator, the first of its kind that was built in this country. Besides the ordinary dynamos and motors, many of which are fitted with special testing appliances, there is a good deal of special testing plant which has been made in the laboratory.
Adjoining the dynamo-room a well-fitted workshop gives the necessary facilities for the repair of machinery and for making small pieces of apparatus required by research students, and in addition there are photometric laboratories, a high-tension test-room with a 20,000-volt transformer and a high-tension static machine, a standard room and a range of special laboratories for research students. There is also a small museum of materials used in the manufacture of electric cables and other electrical apparatus, and on the upper floor a room used for electrical drawing. The laboratory is provided with a number of ammeters, voltmeters, wattmeters, and other appliances for experimental work, resistances (including two oseillographs), a largo battery of storage cells being used to supply the current necessary for the various tests.
White Star Works
WHITE STAR WORKS, BOOTLE.
White Star Line
The works are situated in Strand Road, Bootle, near Liverpool, and are used exclusively for the alteration and repair of vessels of the White Star Line. Originally started in 1873 in Neptune Street, Liverpool, the works were removed to their present site in 1886, in order to be near the vessels, and to provide for additional space caused by development of the line.
The building is of brick, and occupies a space of about 440 square yards. In the basement is the men's dining-room, tool stores, bond and victualling stores. On the ground floor are the general offices, the superintendent engineer's, and victualling superintendents' offices, the brass foundry, blacksmiths' shops, general, victualling and plumbers' stores, boiler-house, fitting shop, and paint store.
On the first floor is the drawing office, opticians' room, joiners' shop, fitting shop, copper shop, upholsterers' shop, and a laundry, which is capable of dealing with 3,000 pieces of linen per day, and comprises a sorting-room, washhouse, drying-room, calender-room, linen-repair, and store-rooms.
The second floor contains pattern-makers' stores, brass shop, sheet-metalworkers' shop, japanning shop, brazing shop, silversmiths' shop, upholsterers' store, sail-makers' loft, and accommodation for the janitor.
Steam is supplied by two Lancashire boilers; each has a grate surface of 23 square feet, and they are fitted with Crosthwaite fire-bars, and supply steam to the laundry, main engine, and two sets of direct- coupled electric light engines, and they are also used for heating the building. The main driving-engine is by Pollock and Macnab, and is of the horizontal double-acting type, with a cylinder, 16-inch bore and 3-inch stroke, giving about 50 i.h.p. at 60 revolutions.
Among the most interesting tools in the lower fitting shop is a large lathe by Davies and Primrose, with 24-inch centres, with an available length of 39 feet; a 7-foot 6-inch radial drilling-machine, also a 2-foot vertical slotter, both by Pollock and Macnab; horizontal planing-machine, 11 feet stroke, by Oldham and Richards, which was originally driven by a rack, and has now been converted into a screw-drive. There is also an 8-foot face-plate lathe. In the upper fitting shop is a 3-inch turret-lathe, by Alfred Herbert and Co.
In the blacksmiths' shop are two steam-hammers, one 5 1/2 cwt. and the other 12 1/2 cwt., both by Davies and Primrose. In the laundry the principal machines are two Bradford's Decoudun calenders, four rotary washing-machines, and three hydro-extractors.
In addition to the above works, there is a boiler-shop at Bankhall, Liverpool. This shop is entirely electrically-driven by motors off the Corporation supply. There are also workshops at Canada Dock, adjacent to the ships' berths. The hands employed at the White Star Works number about 300, at the Dock about 900, and at Bankhall boiler-shop about 30.
Messrs Cammell Laird and Co
MESSRS. CAMMELL LAIRD AND CO., SHIPBUILDING AND ENGINEERING WORKS, BIRKENHEAD.
Cammell, Laird and Co
The Shipbuilding and Engineering Works of this Company at Birkenhead comprise the yard formerly worked by Messrs. Laird Brothers and the large extensions at Tranmere made during the past few years. The works cover an area of about 100 acres with a river frontage of over 3,000 feet, and are suited for all classes of shipbuilding, marine engineering, and repairs. The whole of the site of the Tranmere extension has been reclaimed from the foreshore of the river, the excavation from the docks having been utilized to fill up the rest of the land to the required levels.
Passing first through the old works where vessels of up to 450 feet in length can be built, there may be seen three destroyers now building for the British Admiralty. The platers' sheds, smithy, and engine shops are conveniently arranged for dealing with the type of work turned out. In the old yard are five graving docks, and on passing into the extension two others will be seen. This series of graving docks is the most complete of any in private hands, and together with the disposition of the workshops offers the greatest possible facilities for executing repairs with cheapness and despatch.
The leading dimensions of the docks are as follows
- | No. 1 | No. 2 | No. 3 | No. 4 | No. 5 | No. 6 | No. 7 |
Feet | Feet | Feet | Feet | Feet | Feet | Feet | |
Length | 310 | 360 | 448 1/2 | 440 | 423 | 708 | 860 |
Width at entrance | 38 | 43 | 75 | 83 1/4 | 80 | 80 | 92 |
Draught of water | 13 1/2 | 13 1/2 | 21 1/2 | 21 3/4 | 17 1/2 | 31 | 34 |
Most of the docks are closed by floating caissons, and all except the two largest empty by tidal action. These latter are pumped out by two 36-inch centrifugal pumps drawing from a common sump between the docks. The larger of the two can be dried in about three hours.
Next to the two large graving docks is the fitting-out basin, 131 acres in area and with about 3,500 feet of quay space. It is served by 150-ton and 40-ton cranes, the latter of which travels along the quay and also serves the larger of the two graving docks. Both cranes are worked electrically. A depth of water of over 30 feet can be maintained in the basin, and the entrance is 92 feet in width. The entrance gates are opened and closed by electric power.
Along the west side of the basin is the new boiler shop, a building 500 feet by 130 feet, the main bay being 50 feet in height up to the crane rails. This bay is served ,by two 70-ton electric cranes, the smaller being arranged for 10-ton cranes. The boiler work is at present being carried out in the boiler shop at the West Float, but will be transferred to the now shop as circumstances may require.
Along the south side of the basin and adjoining the 150-ton crane are the main machinery shops with an extreme length of 1,075 feet and extreme width of 162 feet, the floor space being 130,800 square feet, and attached are buildings 270 feet by 43 feet and 315 feet by 43 feet, intended for smithy and coppersmiths' shops respectively. The main bay is served by two 70-ton electric cranes, and the side bays by smaller travellers. The large machines in the centre bay are mostly direct motor-driven, and the smaller machines are mostly driven in groups from line shafting.
Passing on to the shipbuilding department, it will be seen that there are six slips capable of building vessels from 700 feet in length and upwards. In fact, the extreme south slip can accommodate vessels of over 1,000 feet in length.
The shipbuilders' machine shop is immediately at the head of the slips, and consists of three bays each 120 feet span with a total covered area of 145,000 square feet. The machinery is of the latest and most powerful description. Behind the machine shops is a yard for storing plates, which is served by an overhead travelling-crane, and is in direct communication with the railway systems in the yard. There is also a spacious mould-loft 280 feet by 70 feet with stores underneath, and a ship-fitters' shop and smithy each 210 feet by 70 feet. The wood-working department, consisting of sawmills and joiners' shop 200 feet by 110 feet and 300 feet by 100 feet respectively, is in a convenient position for vessels on the slips or in the docks.
The power for the whole works is obtained from the power-station close to the joiners' shop. The source of power is three Mond gas-producers of a capacity equivalent to 2,000 h.p. each, which supply gas for driving electric generators and hydraulic and pneumatic pumps. Gas is also supplied from these producers to the plate and angle furnaces in the shipbuilding department. The electric generators are driven by Premier gas-engines, the largest unit in use being 450 i.h.p., the current produced being continuous at 440 volts. The hydraulic pumps are driven by Premier gas-engines and the pneumatic plant by Westinghouse vertical gas-engines. The yard is in direct communication with the main railway systems of the country, and has the additional advantage of being in communication by water with the chief coal and steel producing districts.
The number of men at present employed is about 4,000, but with the works at their normal capacity employment would be found for fully double the number.
Messrs Grayson, Graving Docks
MESSRS. GRAYSON, GRAVING DOCK WORKS, BIRKENHEAD.
H. and C. Grayson
These works were opened in 1904, and are under the management of Messrs. H. and C. Grayson, Ltd., together with the Canada Engine Works and Garston Graving Dock and Shipbuilding Co., the head office being at 21 Water Street, Liverpool. These works are situated in Beaufort Road, directly opposite the Mersey Dock and Harbour Board's Graving Docks West Float, Birkenhead. They are within three minutes' walk of Birkenhead Docks Station, on the Wirral Railway, by which route it is possible to reach Liverpool (James Street or Central Stations) in fifteen minutes. There is also a frequent service of electric cars from Woodside Ferry and Hamilton Square ( Mersey Railway) to the works. At the sides of the works entrance in Beaufort Road are situated the general and time offices; above these, and extending across the top of the entrance, are the manager's, drawing, and accountant's offices.
Immediately behind the offices and entrance, are the fitting and machine shops, which are equipped with eight lathes of the most efficient and latest types, of various sizes. There are also planing, boring, and universal milling machines, and two drilling machines. In the centre of the shop is a large surface and marking-off table; three jib-cranes, fitted with chain blocks capable of lifting heavy weights, are fitted up in suitable positions for handling jobs in and out of the various machines as required. The machinery in this shop is driven by two motors placed overhead in line with the shafting on the beams.
In the fitting and machine shops are situated, to the left hand side, the plumbers' and coppersmiths' benches, with the necessary fires, and screwing machines for iron piping. At the end, to the coppersmiths' benches, the water service is led and by which any pipes or castings can be subjected to any required hydraulic test.
At the top end of the machine shop is situated the power-house, where all current for driving the machinery and lighting the works is generated. The plant here consists of a Crossley engine and multiple dynamo, and a Crossley engine and dynamo, also a motor generator reducing the current from the town mains to that of the works. The gas for driving the engines is produced at the back of the power-house by means of a Hutchins and Wilkie gas-producer.
The remainder of the works building, from the power-house to the top end of the building, is occupied by the plating, boiler-making, and blacksmiths' shops. Here the machinery is of a very efficient type, and capable of dealing with the largest and heaviest of vessels' shell-plates, frames, beams, and also boiler plates. It consists of large rolls driven by 2 motors, 1 planing machine with motor, 2 shearing and punching presses, each driven by a motor, 1 double- headed countersinking machine, with motor, and 1 radial drilling- machine. There is also a large furnace suitable for heating plates and frames for flanging, bending, etc.; at the top end of the works, and immediately facing this, are the necessary large levelling blocks. At the sides of this shop are the blacksmiths' and ironworkers' forges, the blast for which is supplied by a fan driven by a motor. Conveniently situated alongside of the blacksmiths' fires is a largo power-hammer driven by compressed air, the air-compressor being driven by a motor in a house close behind the power-house. Connecting pipes are also laid the full length of the shop from the compressor for the use of the pneumatic-hammers and drilling machines.
Adjoining the works, to the back and side, is a large storeyard, where the iron and plate racks and riggers' stores are situated. At the back- of the yard, overlooking the railway, is a large general stores of the works. Running right through the stores, yard, and works, are metals on which travels a large crane.
In the West Float Graving Docks opposite the works, is placed a portable boiler with carriage driving two air-compressors. Pipes are laid along the side of the graving docks, and pneumatic-hammers and drilling-machines can be used on vessels undergoing shell, boiler, or machinery repairs, in the dry dock.
Messrs Lever Brothers
MESSRS. LEVER BROTHERS' SUNLIGHT SOAP WORKS, PORT SUNLIGHT, CHESHIRE.
Lever Brothers
The works of Messrs. Lever Brothers, and the village of Port Sunlight, with which they are inseparably connected, are built on a tributary of the Mersey known as Bromborough Pool, between three and four miles further up the river than Birkenhead. It is only 21 years since the first sod was cut at Port Sunlight, but there is now in the works buildings a total floor space of 1,920,000 square feet devoted to the manufacture of soap and subsidiary products. The total land and water area of the works is 216 acres, and the village covers an additional 132 acres, on which stand some 720 cottages, a Church, two Day Schools, a Technical Institute, a Cottage Hospital, a spacious Girls' Restaurant (Hulme Hall), a Mon's Dining Hall, a Bowling Club, a Library and Museum, a fine Concert and Assembly Hall, known as the Auditorium, a Gymnasium, a Swimming Bath, the Collegium (with Lecture Hall), Lawn Tennis Courts, Football Ground, and other institutions.
The soap-producing capacity of the works when transferred from Warrington, and on the completion of the buildings first erected in Port Sunlight, was 800 tons weekly. It is now over 3,000 tons per week. Employment is provided for some 4,000 people in the Port Sunlight works and offices, and this number is greatly increased if the branches, the agents' staffs at home and abroad, and the works and offices of the associated companies in the colonies and in foreign countries are included.
At the Port Sunlight works alone upwards of sixty trades and occupations are represented. The main industry of soap-making is carried on in three soaperies, and a fourth is in course of construction. The soap is boiled in more than 100 pans, each with a capacity of 60 tons. From the pans the soap is run off through wooden spouts into cooling frames below, and in due time, when it has solidified, is cut into slabs and bars and removed to the stamping machines, whence the tablets are carried on moving platforms to the packing tables where they are wrapped up and packed into card boxes and wooden cases for transit. The present power-station is not fully capable of dealing with the load due to the extension of the business, and there is a new power-station under construction, which when completed will add considerably to the available electrical energy in the works.
Prominent among the subsidiary industries are the glycerine recovery and refining works, the wood-box and card-box making, and the printing sections. New and enlarged printing works, of about four acres in area, were recently opened, and are fitted with nearly every kind of letterpress printing plant, including the latest machinery for colour printing. A capacious dock and wharf (on the latter electric transporters are a conspicuous feature) enable one to realize the significance of the name "Port" Sunlight; but besides the waterway to and from Port Sunlight, by which barges bring in raw materials, oil, tallow, oil-bearing seeds, etc., and take away the manufactured soap, there are rail communications with the main line, and the company's own locomotives are conspicuous in the grounds adjacent to the works.
Port Sunlight has also its own oil mills and refinery. Great importance is attached to the work of the chemical laboratories. Here all the ingredients used in the manufacture of the soap are tested; samples taken during the process of manufacture are analysed; and finally, the finished soap is subjected to a further close examination, to ensure the maintenance of the highest standard of purity.
In various divisions of the works are provided rest-rooms, surgeries, bath-rooms, and rooms for drying garments and boots in wet weather. An ambulance corps is ready to give first aid in case of accident until the surgeons arrive. Every case of accident is the subject of inquiry by personal accident inquiry committees, and the minimizing of accidents is further effected by the encouragement of suggestions for their prevention. Boxes are placed at various convenient spots throughout the works for receiving not only those suggestions, but any others relating to improvements in working, or the well-being of the workers, and prizes are awarded for these suggestions according to their value. Ideas worth patenting aro patented in the name of the worker at the firm's expense, the patentee receiving royalties from all users other than Lever Brothers.
"Prosperity-sharing" is the name given to the system under which the employees of the company have had their position as workers from time to time greatly improved, until at length, in the present year, all employees over 25 years of age, and of more than 5 years' faithful service, have become eligible as " partners " under a scheme by which they will have allotted to them yearly, partnership certificates for amounts calculated on a scale of earnings.
These certificates are not negotiable either by way of sale or loan, and are only valid as long as the employee is is active service; but on the employee's retirement they may be exchanged for preferential certificates bearing interest in accordance with the terms of the Trust. These certificates pass to the widows of co-partner employees. Prosperity-sharing began in the building of the model houses (with baths and gardens) of Port Sunlight, let at rents which, except for one per cent. taken for a depreciation fund, are entirely expended on upkeep of the houses, and the various village institutions already named. The eight-hours' day was voluntarily granted many years ago without decrease of pay; for women, the hours are 45 per week. Educational excursions to distant places, sometimes to the Continent, are from time to time given at the expense of the firm.
In 1905 an Employees' Benefit Fund was founded, providing old- ago pensions for all who have been in the service of the company for 20 years and upwards, and making some provision for widows and orphans. A Holiday Club, established a few years ago, enables any worker to enjoy a week's holiday in the summer without loss of wages. And lastly, by the Partnership Scheme already referred to, every eligible employee of more than 5 years' standing will now have a yearly increasing share in the prosperity of the firm when the dividends on the ordinary shares exceed 5 per cent.
Messrs W. Vernon and Sons
MESSRS. W. VERNON AND SONS' FLOUR MILLS, BIRKENHEAD.
W. Vernon and Sons
This is the older of the two sister-mills of the above well-known firm of Liverpool and London. It stands on the quay of the Great Float and was erected in 1899, the other of the pair being erected on the Victoria Dock, London, in 1906. In every essential respect they are practically identical, the machinery in each case being by Messrs. Henry Simon, of Manchester.
The mill at Birkenhead adjoins the grain warehouses of the Mersey Docks and Harbour Board. It has a quay frontage of 400 feet to the dock alongside, with a depth of 35 feet of water affording ample facilities for unloading vessels of the heaviest draught. The mill is driven by a triple-expansion engine of marine type, developing 1,200 h.p., by Messrs. Victor Coates and Co., Belfast, supplied from three large Lancashire boilers working at a pressure of 200 lb. These are fitted with Bennis' automatic stokers, by which means two boilers supply the necessary steam, while the third may remain idle for cleaning, etc. Power is taken from the main driving-wheel by thirty-six ropes, each of the eight lines of shafting being driven by a separate set of ropes.
A portion of the dock warehouse, rented from the Dock Board, contains the silos of the mill. The original flooring having been removed, a series of 162 bins were constructed of ferro-concrete on the Hennebique system, the whole being joined to the old brick shell and made into one solid structure for carrying 8,000 tons of wheat. An elevator, driven by an electric motor, unloads the wheat from the ship or barge into the silos (the wheat being automatically weighed in transit), this electric motor receiving its electricity from a dynamo driven from the mill engine.
Subsequently, the wheat is drawn as required by conveyer-bands under the roadway to the cleaning plant of the mill. Here it goes through numerous separating, scouring, and washing machines, which arc supplied with water from an artesian well on the premises, 400 feet deep, at the rate of 10,000 gallons per hour. The wheat is then put into bins ready for grinding, which is done in two mills, each with a capacity of 50 sacks per hour; these two mills are practically in one building, though separated by a central wall that runs through the roof for the purpose of limiting risk of fire. The process of making wheat into flour is effected on chilled-iron rollers, some fluted and some plain, the fluted being 60 inches by 10 inches in diameter, and the smooth 40 inches by 10 inches, these being the largest sizes of rollers made for the purpose.
The wheat having passed through the rollers is carried to the dressing machines, then to the purifying machines, by which all impurities are eliminated, the bran is separated, and the flour graded into various brands, the heaviest and purest being the well-known white flour, "Millenium".
The elaborate operations of cleaning, grinding, and grading comprise no fewer than thirty-two distinct processes, which are conducted continuously and automatically. Finally, the finished product is sent to the large warehouse that abuts on the quay, where it is sacked-off and stored ready for delivery to barges or ships, on one side of the mill, or to trucks upon railway sidings on the other, the handling being facilitated by means of a system of sack-bands and chutes.
Messrs John Wilson and Co
MESSRS. JOHN H. WILSON AND CO., SEACOMBE, BIRKENHEAD.
John H. Wilson and Co
This firm was established in 1864, and originally occupied the old Bankhall Engine Works, Sandhills, Liverpool. The continually increasing demand for their steam-cranes, excavators, winches, windlasses, capstans, concrete mixers, etc., necessitated the building of more extensive shops, and new works were therefore built in 1900 at Dock Road, Birkenhead, upon a site occupying seven acres.
These works have been specially designed to suit the particular requirements of their manufactures, and consist of the following departments: crane erecting and turning shop, winch-fitting and turning shop, smithy, boiler shop, brass foundry, finished stores, general stores, paint shop, and joiners' shop. They contain a full range of modern lathes, boring mills, drilling machines, slotting machines, feathering machines, punching presses, rolls, steam- hammers, electric drilling-machines, hydraulic riveting-plant.
The shops are driven by means of five gas-engines, the gas for which is obtained from the company's own gas-producer plant.
The iron foundry is still carried on at Commercial Road, Liverpool, turning out on an average 50 tons of castings per week. The offices, which comprise drawing office, time office, general office, secretary's office, waiting room, board room, director's office, and cost office, are all spacious and airy compartments built on the most modern lines. The works employ between 500 and 600 hands.
Hydraulic Engineering Co's Works
HYDRAULIC ENGINEERING CO.'S WORKS, CHESTER.
Hydraulic Engineering Co
The original business was started upwards of a century ago, and in 1805 was known as The Flookersbrook Foundry, under the style of Cole, Whittle and Co. until 1832, when Mr. John Johnson became sole partner.
In 1844 the business passed to his sons Edward and Bryan Johnson, the latter at that time serving an apprenticeship at the works of Messrs. Nasmyth, Gaskell and Co. of Patricroft.
Mr. Edward Johnson retired in 1861, and the business was continued by Mr. Bryan Johnson alone. It was during the partnership of the two brothers that the engineering side of the business was developed, and largely took the place of the purely founder's work.
In 1869 Mr. E. B. Ellington (now one of the Vice-Presidents of the Institution) joined Mr. Bryan Johnson in partnership, and the business was continued under the style of Johnson and Ellington until 1874, when it was made a limited company, and acquired its present title of The Hydraulic Engineering Co., Limited. Soon after Mr. Ellington joined the firm he turned his attention to the designing and manufacture of hydraulic machinery, which has ever since remained the leading speciality of the company. The works, which have recently been largely extended, now cover an area of between two and three acres. The main portion lies between Charles Street and Egerton Street, with long frontages to both. There is also an extensive yard at the top of Charles Street with frontage to the Shropshire Union Canal.
The main entrance to the works and offices is on the east side of Charles Street. This block comprises the general offices, drawing office, stores, turning and fitting shop, erecting and machine shops, smithy, brass foundry, pattern shop, iron foundry, etc., and a lofty covered steel gantry. On the opposite side of Charles Street is the plating shop.
The turning and fitting shop, with a roof in three spans, is 120 feet by 85 feet with galleries on each side. On these galleries are the smaller lathes, screwing machines, and other machine-tools used in the finishing of brass, steel, and ironwork. The centre bay of the shop is devoted to the larger machine-tools, and is served by a 17-ton electrically-driven traveller running the whole length of the shop, and having a span of 41 feet with a height of lift of about 18 feet above ground-floor level. The ground-floor space under the landing on one side is devoted to machine-tools, and on the other side to fitting. In this shop may be seen an application, by Bateman's Machine Tool Co. of Leeds, of their "Planodrive" to an existing 15 feet by 51 feet horizontal planing-machine, by means of which the cutting speed has been increased from 27 feet per minute to 50 feet per minute, and the return speed from 32 feet per minute to 100 feet per minute, and this without setting up any excessive shocks in the machine.
Leading out of the turning and fitting shop are the erecting and machine shops all communicating. The main erecting shop is a new and lofty building added in 1904, measuring about 92 feet by 49 feet 6 inches. This is served by a 17-ton electrically-driven traveller with a span of 461- feet, the height of rails above floor-level being 32 feet. This shop contains the tool room, which is 43 feet by 15 feet. The old erecting shop, which is parallel to and stands between the new erecting shop and new machine shop, into both of which it is now thrown open, is 98 feet long by 29 feet wide. It is served by a 15-ton rope-driven traveller having a span of 261 feet, the height from floor to rail-level being 21 feet. Both erecting shops have large sliding-doors giving access to Egerton Street, enabling heavy machinery to be loaded up and despatched from the works without passing back through any of the other shops.
Leading out of the old erecting shop and on one side of it is a smaller shop 55 feet by 30 feet containing machine-tools, and used also for erecting purposes and hydraulic testing. This shop is served by a 5-ton electrically-driven traveller. Adjoining the old erecting shop a now machine shop has quite recently been added and brought into use. This shop measures about 70 feet by 53 feet and is served by a 10-ton electrically-driven traveller. Among the new machines in this shop may be mentioned a fine vertical planer by Hulse and Co., a powerful high-speed radial arm drilling-machine, and a keyway milling-machine, both by J. Archdale and Co., a pipe flange facing-machine by Richards and Co., and a hexagon turret lathe by Alfred Herbert of Coventry. All are electrically driven, the vertical planer and high-speed driller each by its own motor.
The iron foundry, recently enlarged and remodelled, is 176 feet by 55 feet. The portion now devoted to heavy castings is served by three powerful hydraulic jib-cranes (two of 10 tons. and one of 8 tons capacity), and the extension, used for lighter work, by a 10-ton electrically-driven traveller. Beyond the extension of the foundry and under cover of a separate roof are the sand mills and sifter driven by an electric motor, also the sand bins and a brass ash washing-machine. Entrance gates into Egerton Street provide means for bringing in materials for use in the foundry as well as for the removal of refuse materials. The brass foundry, which adjoins the dressing shop, is about 42 feet by 19 feet. There are four crucible furnaces and two drying stoves. The smiths' shop has a floor area of about 4,200 square feet; there are ten fixed hearths and two steam-hammers.
The pattern shop, an irregular-shaped building, has a floor space of about 2,100 square feet, and a gallery giving an additional 800 square feet. Here may be seen an interesting machine, namely, a mechanical wood-worker by Wadkin and Co., of Leicester. The driving of the machinery in this shop is by electric motor.
Hydraulic power at 800 lb. pressure per square inch is supplied to the works by a steam-driven pumping plant consisting of a pair of horizontal direct-acting pumping engines working in conjunction with an accumulator. This supplies power for working the foundry cranes, a Brotherhood capstan in the yard, punching and shearing machines in the plating shop, intensifiers used for testing purposes, the lift serving the cupola charging stage, and two lifts giving access to the landings in the turning and fitting shop. The system is also employed for testing the hydraulic engines and capstans manufactured in the works, all of which are run under pressure before leaving the works.
Two Lancashire boilers supply steam to the horizontal engine which drives one side of the turning and fitting shop, the hydraulic pumping-engines and the steam-hammers in the smithy. The exhaust steam from the shop engine is used for warming the shops in winter. A water-tube vertical boiler supplies high-pressure steam for testing purposes. Electric current for both lighting and power is at present supplied by the Chester Corporation.
Among the improvements recently made in the works may be mentioned a new gantry with overhead electric traveller, taking the place of an old wooden gantry and hand-power traveller. The structure is of steel, about 170 feet long by 42 feet wide, with a corrugated iron roof over its entire length. The electric traveller has a lifting capacity of 15 tons, and the height from ground to rail- level is 30 feet.
The plating shop, which stands on the west side of Charles Street, is mainly devoted to the making of structural work in connection with cranes and other machinery necessitating platers' and riveters' work. Among the tools and appliances in this shop there are hydraulic punching and shearing machines, portable hydraulic riveter with hydraulic pumps and a differential accumulator, also a large triple ram hydraulic accumulator used for the purpose of increasing the 800-lb, pressure supply to 1,000 lb. or 1,500 lb. per square inch when required for special purposes.
The company's leading specialities in design and manufacture are hydraulic power generating plant for public power supplies as well as for docks and railways, and the hydraulic appliances usually worked off these plants, including coal hoists, fixed and movable cranes, hydraulic engines, capstans, machinery for working swing and bascule bridges, dock gates and sluices, wagon hoists and other lifts, etc., hydraulic machine-tools, such as punching and shearing machines, straightening and bending machines, etc., presses for various special purposes, injector fire-hydrants and hydraulically- driven pumps for water-supply and sewage. Considerable quantities of the smaller gun-mountings and other similar material have been made at the works. The number of employees is about 400.
Garston Graving Dock and Shipbuilding Co
GARSTON GRAVING DOCK AND SHIPBUILDING CO., GARSTON.
Garston Graving Dock and Shipbuilding Co
These works are situated on the east bank of the Mersey at the southern boundary of the City of Liverpool; they are within easy reach by rail from the City itself per London and North Western Railway Co., to Church Road Station, Garston, distance about half a mile, and fifty yards further is the electric car terminus, and a further quarter of a mile brings one in reach of the Cheshire Lines Garston Station. The property was acquired by the firm of Messrs. H. and C. Grayson, by whom it is controlled and managed; the dry dock is called after the family name, " Grayson's Dry Dock," which is 400 ft. long by 85 feet wide, fitted with centre line, side blocks and grid, steam-winch, steam-crane, and large derrick capable of lifting 15 tons, and electric winch for heavier lifts. The dock is fitted with two electrically-driven centrifugal pumps, one 8 inches and one 12 inches diameter, the entrance being closed by means of a caisson; an electric capstan is also placed at the entrance to expedite the docking of vessels.
The approach to the works is at the top end, or river end, of King Street, and immediately at the entrance is the timekeeper's and pay office. On the ground floor are the general office, secretary's office, works manager's office, kitchen and dining room. Passing a little further on the right we come to the general stores, and opposite to this building are the plumbers' shop and paint and oil stores, and on passing the scrap bins we come to the large covered-in scrieve board, adjacent to this being the plate and angle furnaces together with the levelling and bending blocks. To the left is the Power-House, having one air-compressor and air-receiver complete for driving the pneumatic plant, the power of which is carried to the building slips and Graving Dock by piping laid under ground; this building also contains a combined plant consisting of one Browett and Lindley 2-crank compound engine, capable of giving 175 b.h.p. at a speed of 400 revolutions per minute with a Mather and Platt multipolar dynamo for an output of 118 kw. at 250 volts, a spare armature also being kept in readiness. The switchboard is arranged that any section of the yard can be entirely cut off from the other section; an electrical stores is also situated in this building.
On passing out by the furnaces we come to the large Lancashire boiler, feed-pump, and tank, and then to the ironworkers' shed, which consists of the usual shipbuilding plant, namely, rolls, punching and shearing machines, planing machine, countersinking machines, beam bender and radial drilling- machine. The smiths' shop at the end of this shed is equipped with eight fires complete with fan-driven blast, pneumatic hammer and smiths' tools capable of dealing with ship and engine work forgings; abutting this shed is the saw shed, consisting of one direct-driven 10 h.p. motor circular-saw bench complete, with rise and fall table, rollers, and swivelling motion. The ironworkers' shed is well situated for carrying out work with economy, it being placed between the Graving Dock and the building slips, which are fitted with derricks.
The Company have turned out a large number of steamers, hopper barges, barges, launches, tugs, training ship, bell beacon, gas-light vessels, cable tanks, pontoons, funnels and masts, the yard on the south side of the Graving Dock being well suited for the last four items mentioned. At the head of the dock is a gear stores as a convenience for the Graving Dock; a steam-winch is also situated here for the general working of the docks and railway wagons, the railway system being connected to the works. After leaving the dry dock and passing the wagon weighbridge we come to the joiners' and patternmakers' shop, fitted with electrically-driven circular-saw and mortising machine, benches, lathe, pattern and timber stores.
Close by is an Artesian well to which is connected steam- and electrically-driven pumps for pumping water into a tank with a capacity for 130 tons; this tank is connected to a line of pipes on the dry dock quay, and is capable of filling tanks and boilers at the rate of 100 tons per hour, and the water is also utilized for washing down the dry dock. After passing the steam-boiler for this pump on the left we come to the engineers' shop, which is fitted out with lathes, planing and slotting machines, drilling machines, all electrically driven, and gear stores. Abutting this building is a store shed which can also be used for making wood spars, and above this are the mould loft and drawing offices. The yard, shops, and dry dock are well lighted with the electric light.
The works adjoin the new wet dock of the London and North Western Railway Company, called the "Stalbridge Dock," formally opened by Lord Stalbridge in February this year, and the shipbuilding company have a privilege in having access direct from the works to the quay of the wet dock, which enables them to carry out work on vessels in the wet dock with economy; and as this new dock has been equipped on modern principles and up-to-date requirements for discharging and loading, a great increase in trade is expected in the future. The number of men employed is about 300.
L.N.W.R. Garston Docks and Estate
LONDON AND NORTH WESTERN RAILWAY: GARSTON DOCKS AND ESTATE.
London and North Western Railway
The Garston Docks with their adjacent warehouses and storage grounds, coal reception lines, and general marshalling sidings, all the property of the London and North Western Railway Company, are situated on the Upper Mersey, about four miles south of the Liverpool Docks, and on the same side of the river. The growing importance of Garston as a general and coal-shipping centre is largely attributable to its geographical position, since it is in close proximity to the manufacturing districts of Lancashire, Yorkshire, and the Midlands, as well as the exceptionally short haul from the South Lancashire and North Staffordshire Coalfields.
The resources of the existing docks being severely taxed, the London and North Western Railway Company, in 1902, obtained powers for the construction of a third dock, now completed, which has increased the length of quays or berthing accommodation by seventy per cent., whilst the construction of additional sidings and timber and mineral storage grounds to an even greater ratio has been accomplished. Being a railway port, goods are naturally transferred direct from ship to railway wagon, or vice versa, thus reducing handling and consequent expense. At the present time vessels up to 5,000 tons carrying capacity can be dealt with at Garston, but Garden Docks (L. and N. W. Railway). when the new "Stalbridge Dock " river entrance and channel are completed, it will be accessible to vessels of 10,000 to 12,000 tons.
The approach to the Stalbridge Dock from the River Mersey will be through a new cut or channel (leading from Garston Deeps) about 800 yards long and about 100 yards wide, the excavation of which, now well advanced, involves the removal of some 153,000 cubic yards of red sandstone rock and a large quantity of sand and silt. On one side of this cut or channel, five timber piers are in process of construction connected by gangways to act as a fair lead for vessels entering the new lock. This entrance lock is 276 feet long by 65 feet wide, and there will be sufficient water to permit vessels of suitable dimensions entering and leaving the dock at from two to three hours before and after high water; the depth of water on the sills at high water ordinary spring-tides will be 33 feet, and at ordinary neap-tides 26 feet.
At first the rock was removed by means of a powerful bucket- dredger only, but as the work advanced the rock was found to increase in hardness, and to accelerate the work, it soon became apparent that systematic drilling and blasting would have to be resorted to. About four-fifths of the total quantity of rock is being dealt with in this way. With the aid of this blasting, the dredger is removing an average quantity of 4,200 tons of solid rock per week, which is conveyed to the deposit site, 23 nautical miles away, in hopper-barges towed by steam-tugs.
A feature in the construction of the works has been the temporary dams, behind which 700 feet of river wall, and a wall 200 feet across the corner of the old dock adjoining the entrance lock, have been built. All these dams were of a single skin flitch type.
Owing to the new Stalbridge Dock entrance and channel being excavated at a depth of 16 feet lower than the old river wall, it was necessary to remove and rebuild a portion of the latter for a length of 240 feet, and this was accomplished behind a dam. When the water had been pumped out, excavations were made for the now wall which was then built between the two flitches. The method adopted in the construction of this dam dispensed with the necessity for employing divers to place a series of long horizontal struts from the face of the data to the old dock walls.
The Stalbridge Dock itself is 14 1/2 acres in area, or equal to the combined area of the Old and North Dock, with a mean length and width of 1,130 feet and 600 feet respectively, the depth from coping level being 45 feet. A communication passage exists between the North and Old Dock, and a further communication has been constructed between the Stalbridge Dock and Old Dock, 65 feet in width, and with sills placed at the same level as the bottom of the existing North Dock entrance. Of the excavations for the new dock and quays, amounting to 1,500,000 cubic yards, three-fourths were in the red sandstone rock. This rock,after crushing, was used throughout for the cement concrete backing of quay and entrance walls, into which large rough sandstone blocks were introduced as displacers. All the walls, however, have a facing of richer concrete composed of crushed granite 12 inches thick for durability, whilst a considerable portion of the entrance lock and passage walls are faced with masonry of Cornish granite; this granite has also been used for the hollow and square quoins, sill stones, sluice jambs, and culvert outlets; granite has also been used for the pointing sills and roller paths, and also for the coping.
The dock gates, of which there are five pairs, namely, three at the entrance lock, and two at the communication passage, are constructed of greenheart timber of considerable strength. These gates, with the exception of the river and storm gates, are actuated by direct-acting hydraulic rams, the connecting-rods being attached at about 8 feet below coping level; this arrangement avoids the employment of chains, which are always objectionable in working timber gates. In the construction of these gates some 29,000 cubic feet of greenheart have been used, and each leaf of the entrance lock gates weighs complete about 110 tons. The paddles controlling the flow of water through the sluicing and levelling culverts are constructed of greenheart timber, the main working paddles being lifted by hydraulic power; the latter can at any time be isolated for effecting repairs, by lowering stop paddles worked by hand-power, and also by means of the latter the water discharged for sluicing purposes can be concentrated at any particular point desired. The railway traffic is carried over the communication passage by means of a sliding drawbridge worked by hydraulic power.
As the excavation for the dock was principally in rock, the latter wherever sound has been used to form the lower portion of the quay walls, thereby effecting both light and economical construction. For half the length of the quay walls, the stratum dips towards the dock at a somewhat steep inclination, and at intervals the rock has been dovetailed out to the bottom of the reels beneath the continuous walls; these dovetails, when filled in with cement concrete and bonded into the walls above them, form counterforts to the latter, and interlock the rock in such a way as to prevent the possibility of slips taking place under the walls. Where defective seams of rock occurred in the face, they were cut out and the spaces filled in with blue brickwork, in cement.
The accommodation at Garston Docks and general equipment consists of:—
Dock Accommodation | ||||
Width of Entrance | Depth of water | on Sill. | Water area | Berthing space |
feet. | feet. | acres. | feet. | |
Spring. | Neap. | |||
North Dock 55 feet | 28 | 18 | 8 | 2,400 |
Old Dock 50 feet . | 25 | 15 | 6 | 2,160 |
Stalbridge Dock 65 feet, with a lock 276 feet long | 33 | 16 | 14 1/2 | 3,170 |
Hydraulic Power-House. — The power consists of two separate plants: The old plant, originally opened in September 1875 comprises:--
Eight Cornish boilers, 30 feet by 5 feet 9 inches, working pressure 60 lb. per square inch, supplying steam to five engines, namely, three horizontal Armstrong class, one compound tandem Hathorn-Davey, and one Crewe class.
The new plant consists of: Three Galloway Lancashire boilers 30 feet by 8 feet, working pressure 175 lb., fitted with Erith forced draught. These boilers supply steam to three Crewe horizontal hydraulic engines. The hydraulic pumping-station supplies seater at 750 lb. pressure into a 7-inch hydraulic main running completely round the Stalbridge Dock, and also into small mains round the Old and North Docks, and these mains supply pressure to the coal tips, cranes, dock gates, etc.
Coaling and other Appliances. — To deal with the large and increasing export coal traffic, four large movable hydraulic coal-hoists each of 30 tons capacity, fitted with anti-breakage appliances and end doors on shoots, mechanically controlled, have been erected at the Stalbridge Dock. These shoots are capable of tipping coal into vessels at any height from 5 to 45 feet above quay-level, the platforms being adapted for any size of end-door wagon up to a length of 21 feet 6 inches over the buffers. The tables are lifted by direct-acting side rams, which can be worked independently to economize water. Each tip is movable and can be traversed to any required position by means of hydraulic power supplied through a flexible pipe. Arrangements have been made which will permit of two or three hoists so placed as to be capable of working simultaneously into one vessel.
A complete system of hydraulic capstans is provided for running the wagons on and off the hoist table, while weighbridges for weighing both full and empty wagons are laid down adjoining each hoist. There are also two similar hoists at the North Dock, but these have a range of travel from 5 to 35 feet above quay-level. The North Dock has in addition four balance coal-drops with a capacity of 161 tons each, while three similar structures are available in the Old Dock.
The hydraulic cranes around the Stalbridge Dock are of the movable gap pedestal type, each having two powers. Out of a total of eighteen there are sixteen designed to lift 50 and 23 cwt., while the remaining two have a capacity of 80 to 35 cwt. There are in the Old and North Docks thirty-one hydraulic cranes of various patterns with capacities ranging from 30 to 50 cwt. Hydraulic power is supplied to sixty-eight capstans (this number is being increased), the majority of which are of the Brotherhood turnover type, and also to seven sets of dock gates. There are two 7-ton ship's- capstans fixed on the Stalbridge Dock pier-head, and also six 5-ton ship's-capstans. Sheer-legs worked by steam-power and capable of dealing with 40 tons are also installed at the North Dock.
Dredging Plant. — The old dredging plant consists of a small central-ladder dredger, a double-ladder dredger, and four steam-hoppers, capacity of the latter being 300 tons each. To this has been added a modern grab-dredger of 1,000 tons capacity. The latter vessel is fitted with triple-expansion engines and two boilers, and is capable of steaming at a speed of 10 knots. It can dredge to a depth of 40 feet, and under favourable circumstances is able to load itself in two hours.
Electric Lighting. — The electric power-house adjoins the hydraulic power-house, and is equipped with the following machinery Three Belliss-Morcom high-speed compound steam- engines, each 180 b.h.p., coupled direct to a Lancashire Dynamo Co.'s compound dynamo, capable of generating direct current at 500 volts and 250 amperes; two Lancashire Dynamo Co.'s balancers for the three-wire system for incandescent lighting; and one main switchboard for the switch gear, etc.
The lighting of the quays, coal-tips, sidings and storage berths will be effected by about 300 arc lamps (open type) each of 1,000 candle-power. Tho warehouses, sheds, and offices, also the passenger stations at Dock Road and Church Road will be lighted with 1,200 incandescent lamps. Special arrangements have been made for lighting the timber storing berths, so that work can go on at these points both day and night. The ships' berths at the three docks are to be equipped with portable 6-light cargo fittings, plugs being provided on the quays as necessary. The lines leading from Garston to Spoke Junction, as also the adjacent sidings, are lighted by 70 arc lamps, each of 1,000 candle-power. All the main cables to the distributing centres, and the feeders for are and incandescent lighting, are of bare copper carried overhead on poles.
Warehouse and Shed Accommodation. — Extensive warehouse and shed accommodation is provided, including a Customs transit shed.
Mineral Storage Berths. — A very large business in minerals is conducted through the port, namely, sulphur, copper, manganese, iron and other ores. The Company have provided " floored " berths of a special character, and accommodation now exists on these berths for upwards of 100,000 tons of mineral cargo.
Timber Storage Berths. — There are about 48 acres of storage ground specially levelled and provided with sidings at convenient distances from each other, so as to admit of cargoes being laid down, sorted, piled or selected as may be necessary. Special accommodation for heavy logs has been provided, and a travelling crane capable of piling logs to a height of 30 feet is available for stocking purposes.
Tonnage. — During 1907 the imports amounted to 666,011 tons, and the exports (including coal) 2,738,131, making a total of 3,404,142 tons. The vessels clearing during same period were 3,980 steamers, 480 sailing vessels, and 4,110 lighters.
The principal commodities dealt with are deals, battens and boards, staves, sleepers, mining timber and props, and other classes of timber, Esparto grass, nitrate of soda, resin and turps, iron ore, sulphur ore, manganese ore, and phosphate.
There are three regular weekly sailings of steamers conveying general cargoes between Garston and French ports, namely, Rouen, Nantes, and Bordeaux.
Railways. — The London and North Western Railway Company, as owners, control the entire working of the docks, which are, of course, directly connected with their main lino system, and through the latter with the systems of all the railway companies in the country. There are some 70 miles of sidings at the port, of which 8 miles are actually on or alongside the quays, and therefore available for direct working of cargoes from shipside to trucks or vice versa. The Railway Company have two passenger stations on the estate (namely, at Dock Road and Church Road), and these are about five minutes' walk from the docks. In connection with the necessary manipulation of traffic, and to maintain the custom of the port, it may be mentioned that no less than 22 wagon-weighing machines of 30 tons capacity are available for the weighing of cargo. The practice of weighing all cargoes has obtained from the earliest days, and is of great benefit to the traders generally.
Messrs Francis Morton and Co
MESSRS. FRANCIS MORTON AND CO., HAMILTON IRON WORKS, GARSTON.
Francis Morton and Co
These works are situated on the River Mersey at Garston, and cover 10 acres. They comprise a number of lofty and well-lighted buildings, specially laid out for the manufacture of all kinds of constructional steelwork, with large private dock free from dues, and railway-siding accommodation.
For upwards of seventy years the firm has been engaged in the manufacture of steel roofing, bridgework, fencing, steel telegraph- poles, dust-bins, castings, galvanized work, etc., and the company has shipped many thousands of tons of bridgework and constructional steelwork for H.M. Government and Colonial Offices, and also for the various large foreign railways. They have carried out several large swing-bridges, warehouses, wharf-sheds, etc., for the Mersey Docks and Harbour Board at Liverpool and Birkenhead, and are amongst the largest producers of this class of work in this country. The number of men employed is about 650.
Lancashire and Yorkshire Railway, Loco Works
LANCASHIRE AND YORKSHIRE RAILWAY LOCOMOTIVE WORKS, HORWICH. (for map see p.885)
Horwich Works
These works, of which the building was commenced in 1886, were erected for the purpose of repairing and renewing the locomotive stock and of carrying out the mechanical, electrical, and hydraulic engineering work of the railway. They are situated between Chorley New Road, Horwich, and Red Moss, and are about one mile distant in an easterly direction from Blackrod Station, upon the main line between Manchester and Fleetwood. A fork line has been made giving direct access to and from Manchester without passing through Blackrod Station.
The land enclosed for the works comprises 116 acres. The covered area of the workshops is 22 acres. They comprise offices, general stores, boiler shop, boiler-shop smithy, forge, steel foundry, iron and chain foundries, fettling shop, bolt shop and smithy, spring smithy, signals and points and crossings shops, fitting and machine shops, boiler and economiser houses, tin- and copper-smiths' shops, brass foundry, motor and telegraph shops, millwrights', joiners', and pattern-makers' shops (with gallery for storing patterns), erecting and repairing shops, engine shed, paint shop, testing shop, and chain smithy.
For the carriage of material from the stores and of work to the several shops, 7; miles of tramway lines have been laid throughout the works, haulage being performed by small locomotives, the cylinders of which are 5 inches diameter by 6 inches stroke, and the wheels 16 inches diameter. The frames are 7 feet 4 inches over all, and the extreme width of engine is 3 feet. They work at a pressure of 200 lb. per square inch, and their tractive force is about 1,400 lb.; their weight when full and in working order is 3.57 tons.
Offices. — These are 323 feet long by 58 feet wide, and are placed at the north-west end of the works, and include a laboratory, which is fitted up with the requirements for the analysis of all materials. The offices are fitted with electric light, both incandescent and are lamps, and each department of the works is in telephonic communication with the offices.
General Stores. — These are 198 feet long by 111 feet wide, having a gallery built round the four sides. This building is fitted with the necessary weighing-machines and hydraulic cranes for receiving and storing heavy materials.
The Telegraph Shop is 81 feet long by 22 feet wide, fitted with special tools for making and repairing telegraph and block instruments; also automatic screw-making machine, etc.
Boiler Shop. — This shop is 439 feet long by 111 feet wide, and is fitted with a pair of hydraulic pumps and accumulator, two large fixed hydraulic-riveters for boiler work, each having a hydraulic overhead-crane for lifting boilers when riveting; three portable hydraulic-riveters on swing cranes, bolted to walls and columns; and overhead electrically-driven travelling-cranes, in addition to the ordinary machine-tools. Special quadruple multiple stay-tapping machines and stay-heading machines aro provided. Pneumatic caulking and riveting is also in extensive use, the furnaces for heating rivets being fired by liquid fuel sprayed on by compressed air. Right-angle plate-edge planing machines and multiple-drilling machines of different types are in operation. The boiler-shop smithy is 120 feet long by 111 feet wide, fitted with the usual fires. There are also hydraulic flanging-presses for flanging fire-box backs, tube plates, throat plates, ash-pans, tank splasher-plates, etc.
Forge. - This is 452 feet long by 111 feet wide, and contains Siemens regenerative furnaces for reheating, the doors of which are pneumatically raised; a 14-inch merchant mill and a 81-inch guide mill, together with tyre mill and a 30-inch cogging mill with electrically-driven live-rolls; a 35-ton duplex hammer, and one 8-ton and two 5-ton hammers; 18 gas-producers of Wilson type supply gas to all the forge furnaces. Scrap for billets is cut up on the high level by powerful shearing-machines, and is passed from these by a hopper to a long barrel, which acts as a scrap cleaner and a conveyer to the scrap benches.
Steel Foundry. — This is 150 feet long by 135 feet wide, and is fitted with Siemens-Martin regenerative melting furnaces, having high-level tramway for carrying ladle, and narrow-gauge tramway beneath for mould trolleys, also core-drying furnaces, moulding machines, etc. The whole of the furnaces in this foundry are heated by gas made from 8 Wilson's gas-producers. The "Tropenas " process for making steel castings is also in operation.
Iron Foundry. — This is 212 feet long by 111 feet wide. Hydraulic power is used for working the cranes, in addition to which there are overhead (electrically-driven) travelling-cranes, which can be used in both steel and iron foundries. The natural formation of land, which necessitates the rail-level at the rear sad of the foundries being considerably higher than the floors of the foundries, permits of coke and iron being unloaded and wheeled direct to the charge holes of the cupolas or the melting furnaces. Similarly, the gas- producers for the furnaces are charged direct at the top, whilst the ashes from the producers are drawn out at the bottom into the tram wagons running on the lower level.
The Chair and Plate Foundry is 124 feet long by 128 feet wide, and is similarly fitted with two cupolas charged from the high level. Hydraulic charging arrangements are used in connection with these cupolas. A staging is provided for fettling the chairs, which are then placed on an endless chain, which conveys them to the railway wagons for despatch.
Carriage- and Wagon-wheel Shop. — This is 200 feet long by 47 feet wide, and is fitted with lathes for boring and turning carriage and wagon wheels. A hydraulic press is used for pressing the tyres on the wheels, and a press for forcing the wheels on the axles. There is also a special multiple-drill for drilling holes in the retaining rings, wood blocks, and steel wheels, at one setting. Pneumatic tools have been applied to the dressing of steel castings. This shop is entirely electrically driven with motors of 20 and 30 h.p.
The Smithy Bolt Shop is 60 feet long by 111 feet wide, and contains various rivet, bolt, and nut-malting machines, four drop stamps, three Rollo of 12 cwt., one steam of 5 cwt., a large Ajax forging-machine, and several Bradley hammers. The furnaces are heated in some cases with liquid fuel, and in others with coke.
Smithy. — This is 212 feet long by 111 feet wide. It is provided with 11 double and 27 single hearths, also steam-hammers, and is fitted with Roots' blower for the blast. There are 8 drop stamps, three of 20 cwt., one of 30 cwt.; these are steam stamps, the remaining four 12 cwt. being of Rollo pattern.
Spring Smithy. — This is 153 feet long by 47 feet wide, fitted with three gas-heated spring-furnaces, hydraulic spring buckle press, also buckle-stripping machine, and steam-hammer. Special self-contained plant for making spring plates, comprising electrically-driven punching, nibbing, and shearing machines, is installed.
The Signal Shop is 128 feet long by 111 foot wide, and is used for fitting up all locking frames and general signal work, a rack-saw being provided for signal posts, boring machine, and other special tools.
Points and Crossings Shop. — This is 72 feet long by 111 feet wide, and is provided with special machinery for dealing with the manufacture of points and crossings, and includes angular planing-machines, duplex slotting-machine, and special machine for milling and drilling locking-frame standards at one setting.
The Fitting Shop is 508 feet long by 111 feet wide, and is fitted up with a largo number of milling and other machines for dealing with locomotive work, including several automatic machines and turret lathes for turning copper fire-box stays, bolts, pins, etc.; also drilling and slotting machines. These machines are driven by wall engines bolted at the end of the shop, giving motion by means of bevel gearing to four ranges of shafting running longitudinally. Four 5-ton high-speed electrically-driven jib travelling-cranes control the machines on each side.
Boiler House (High and Low Level). — Each contains a battery of Lancashire boilers; some are fitted with underfeed mechanical stokers and Green's economisers, and others with forced-draught grates for burning inferior fuel.
The Central Power-Station is 32 feet long by 47 feet wide, and is equipped with two 300-kw. Belliss and Morecom high-speed engines and dynamos, also four sets of 60 kw. coupled to generate current at 250 volts. Practically the whole of the works are supplied for power and lighting purposes by this plant. In connection with the power-station there is a barometric condenser of the Mirrlees Watson type, which deals with the steam from several other engines of large capacity, thus forming a central condensing plant.
Brass Foundry. - This is 164 feet long by 47 feet wide, and is fitted with gas-furnaces for melting heavy work. The crucible furnaces are coke-fired, having special core drying stoves heated with waste gases from the crucible furnaces.
Coppersmiths' Shop. — This is 89 feet long by 47 feet wide, and is equipped with the necessary appliances for dealing with all tin and copper work used on the railway, and contains furnaces for brazing tube:ends, etc.
The Motor Shop is 153 feet long by 47 feet wide, and is used for making and repairing motors and their accessories.
The Tinsmiths' Shop is 92 feet long by 47 feet wide, and is arranged with tin-making plant for dealing with railway requirements.
Joiners' and Pattern-makers' Shop. — This is 164 feet long by 111 feet wide, and is equipped with modern machinery for sawing, boring, and mortising, etc. It is electrically driven, the motors being 10 and 40 h.p. A gallery is carried round the shop for storing patterns. A sprinkler arrangement is also fitted in case of fire.
Shop. - This is 143 feet long by 111 feet wide. In this shop all the hydraulic and general repairing work for the line is carried out; there are three overhead travelling-cranes, electrically operated, and this shop is driven electrically, the motors being three 10 h.p. and one 20 h.p., and other special machinery for the work required.
Heavy Machine Shop. — This is 360 feet long by 48 feet wide, fitted with frame-plate straightening, slotting, and radial arm drilling-machines; also crank-pin boring, keyway milling, and slotting- machines; also special plant for the manufacture of built-up crank-axles; crank, straight axle and large wheel lathes. Many of the machines in this shop are specially constructed for the purposes required, and all machines are individually driven by 3-phase alternating current motors. Two 10-ton 3-motor electrically-driven overhead travelling-cranes control the machines on each side.
Erecting Shop. — This is 1,520 feet long by 118 feet wide. This shop has been arranged for the repairs of existing, and the building of new, engines and tenders, and is provided with twenty 30-ton electrically-driven overhead travelling-cranes, portable hydraulic riveters, flexible shaft drilling-machines driven by motors, and the necessary tools for repairs. Access for engines to the centre portion of this long shop is obtained by two electrically-driven traversers. Wheel lathes, in some cases electrically driven, are provided in various positions for conveniently dealing with wheels taken from engines under repairs.
Paint Shop. — This is 234 feet long by 111 feet wide. Unlike all the other shops, this has a weaving-shed type of roof, therefore obtaining a light free from sun glare. It is fitted with the necessary grinding and mixing machines, which are electrically driven, and provided with heating arrangement for the thorough drying of the paint quickly.
Test Shop and Chain Smithy. — The test shop is 111 feet long by 27 feet wide, and the Chain Smithy 95 feet long by 28 feet wide.
These shops are fitted with a 100-ton hydraulic testing-machine; also oil, spring, and 100-ton hydraulic chain-testing machines—all chains being tested before being sent out for use. There is also a steam- hammer, and the necessary machines for finishing test specimens.
Gas Works. — These are situated on the south-west boundary of the works, and at a much lower level. They are of sufficient capacity to light all the workshops and premises at Horwich and Blackrod, although at present a greater part of the workshops are electrically lighted.
Dining Rooms have been erected near the public entrance to the works for the accommodation of the men who live at a distance. Accommodation is provided for 1,100 men, whose meals are cooked or heated by attendants in charge of the rooms.
WEAVER NAVIGATION AND ANDERTON CANAL-BOAT LIFT.
Weaver Navigation and Anderton Boat Lift
The River Weaver was at one time a somewhat brackish and very tortuous stream running through the centre of Cheshire. Rising in the Peckforton hills in the south-west corner of the county, it takes a south-easterly course as far as Audlem, and bending sharply round to the north, passes through Nantwich, Winsford, and Northwich, and thence due north-west to Weston Point, near Runcorn, where it previously had direct access to the Mersey, but now is artificially connected to the estuary by means of the Manchester Ship Canal. The chief tributary is the River Dane, which, rising in the Derbyshire hills near Axe Edge, joins the river at Northwich. No part of the Dane is at present navigable, although parliamentary powers were long since obtained but never put into force. The area of the Weaver watershed, including the Dane, is 544 square miles, or nearly one-half the area of the county.
Of the history of the river before its canalization about 1730, there are few points of interest. There is ample evidence of the use by the Romans of the brine springs on its banks, especially at Northwich, and there is little doubt that small vessels took advantage of the flow of the tide to navigate the lower reaches. In King's "Vale Royal," published in 1656, the river is mentioned as having five bridges, and, from the descriptions given in that book, must have passed through what was then most charming scenery, which, however, has now been obliterated in places by the salt and chemical works erected on the banks.
Long before any attempt was made to canalize the river, salt was carried down on the backs of men and horses to the vessels mentioned above as navigating at tide time; but in 1721 an Act was obtained, and, although nothing was done until about 1730, the river was then impounded by means of timber locks from Winsford to Pickerens-o'th-boat, a hamlet about six-and-a-half miles from the Mersey. This enabled vessels of from sixty to seventy tons burden to navigate at spring tide; and about 1763, by means of a lock placed lower down at Frodsham, the navigation was open at all tides for these vessels. The navigable depth of the river was then 4 feet 6 inches.
In 1807 an Act was obtained to make the Weston Canal, so as to avoid the shoals and dangers of the tortuous navigation from Frodsham Lock to the Mersey, and by this means not only was access obtained to the deep water of the Mersey, but also a connection with the Bridgewater Canal system. At Weston Point a basin, now known as the "Old Basin," was built to afford shelter and allow vessels to congregate and wait for the tide.
In 1830 the locks had been improved, and the navigable depth increased to 6 feet 3 inches, and there were nine locks 88 feet long and 18 feet wide, while the vessels carried from 80 to 100 tons. From 1860 to 1870 the locks were made double, new locks, 100 feet by 22 feet, being built alongside the existing locks, and the depth of navigation increased gradually to 9 feet, as that vessels carrying from 250 to 300 tons were able to navigate.
About this time trade was so good and improving, and the introduction of steam on the river had so increased the desire for rapid transit, that it was determined to increase the facilities further, and to make the locks of very much larger dimensions, so that either coasting vessels could themselves use the river or the steamers towing trains of barges could be locked through at one locking.
The construction of the river in its present form was therefore commenced, and although it is not even yet complete, it is so far available that very considerable saving, both in time and money, has been effected for the benefit of the tollpayers, and now not only can vessels with fixed masts navigate to about 2 miles above Northwich, or 17 miles from the entrance to the Mersey, but trains of vessels carrying upwards of 1,000 tons can be navigated and passed through the locks at one locking.
The number of locks has also been reduced from nine in 1830 to four now, while the navigable depth is 10 feet 6 inches for the whole 20 miles. The new locks are 220 feet by 42 feet, and are built so as to allow the river to be dredged down to 16 feet.
Auxiliary Works. — So far the description given above is confined to the river itself; there are, however, most important auxiliary works at Weston Point and Anderton for the accommodation of the inland trade. The original object in making the river navigable was to accommodate the salt trade of Winsford and Northwich, but it appears soon to have been found out, after the construction of the Trent and Mersey Canal, that it was commercially beneficial to tranship other goods in addition to salt, at Anderton, where the two navigations approach each other within a few yards. So important does the interchange of traffic appear to have been, that in 1807 a clause was inserted in an Act of Parliament, prohibiting such interchange except as to salt and kindred goods. This continued until 1825, when it was repealed as being " highly prejudicial to the public," and from that time until 1875 a considerable interchange, chiefly export trade, took place by means of inclined planes and cranes.
Anderton Lift. — The hydraulic lift at Anderton was opened in 1875, and since then there has been a continuous flow of traffic in bulk. This lift consisted of two tanks or caissons, supported on hydraulic rams in equilibrium. One tank was always up and the other down. When in use the boat and cargo float into one of the tanks either above or below, or when convenient, both contain boats. The gates closing the ends of the tanks were then shut, and the machine set in motion by withdrawing a small amount of water from the lower tank. The extra weight of the descending tank then caused them to change places, the ascending boat being transferred through 50 feet to the canal and the descending boat to the river. A small hydraulic-pump made up the losses by friction and other mechanical causes, but five-sixths of the transfer was performed by the slight difference in weight of water in the tanks. These tanks will accommodate "dukers," [3] and no possible straining can occur to the boat as it is kept afloat all the time.
The weight of each tank, including water and ironwork, is 250 tons, which, of course, never changes, as the boat displaces its own weight of water. After working for nearly thirty years it was found that considerable repairs were required, and more especially to the main rams, upon which the whole weight of 250 tons was balanced. In order to repair or renew these, a very considerable length of stoppage would have been necessary, and it was most important not to in any way interrupt the flow of traffic between the River and the Pottery district.
After considerable discussion, it was eventually decided to adopt the plan suggested by the engineer to the trustees (Mr. J. A. Saner) of suspending the caissons by means of wire-ropes on to an overhead arrangement of wheels and pulleys, with counterweights at the other end of the ropes, somewhat similar to the method of carrying an ordinary window-sash. A clear idea of the principle may be given by assuming that a large number of window-sashes are fastened securely together, each one having its own pulleys and counterweights. The essential difference, however, between the window-frame and the arrangement at the lift is, that instead of forcing the windows en bloc up or down, the power is applied direct to the pulleys through suitable gearing, so that they are all made to revolve together, and thus raise or lower the mass. By adopting these means, the repairs and alterations were carried out with three stoppages of about a fortnight each, and the re-opening took place on 29th July 1908. This did away entirely with the necessity for hydraulic power, as an electric motor was more convenient for operating the pulleys, and has the great advantage that all parts of the machinery are above ground and easily accessible. The alteration has also resulted in quickening the time of transit, and reducing the cost of power.
Weston Docks. — In connection with this inland export and import traffic are the docks at Weston Point. These were commenced in about 1860, and have been since extended so that with the lower portion of Weston Canal they form a considerable area for the accommodation of vessels bringing flints, China-stone, bone ash, and other pottery materials, and are well fitted up with hydraulic and steam-cranes, floating derricks and other appliances for handling traffic. At Anderton there are also electric cranes, and at both places, which form the exits and entrances for the inland through trade of the river, are extensive sheds, warehouses, and wharves, so that rapid despatch can be given. The size of the dock entrances and depth of water enable vessels up to 1,200 tons burden to be dealt with. Although the construction of the Manchester Ship Canal has cut off direct access to the Mersey, the rights of the Weaver have been very fully preserved by Parliament in order that no interference may take place.
Subsidence of Land, and Northwich Bridges. — An interesting feature is the subsidence of lands through which the river passes. These subsidences are caused by the removal of the salt rock from below, and take place all over large areas both at Northwich and Winsford, where lakes, locally known as Flashes, have been formed. These subsidences have given very considerable trouble, owing to the lowering of the banks and formerly of works such as locks and bridges. The permanent works have, however, now all been placed on sound ground except the two new swing bridges at Northwich, which were specially designed by the engineer to meet the difficulty. The bridges, which consist of bowstring lattice girders for carrying the roadway, and weigh some 300 tons each, are balanced with their centre of gravity over the centre of a large circular pontoon or buoy, which floats and carries about five-sixths of the whole weight, the remaining one-sixth resting on a ring of live-rollers supported by screw-piles. When the bridge is turned, the whole pontoon turns with it, so that friction is reduced to a minimum. Should any subsidence take place, the weight to be handled is comparatively small, and for ordinary unevenness the piles are provided with screw-heads by which the roller path can be adjusted. The whole is operated by electricity, and can be opened and closed in less than four minutes, including the application of the gates for the safety of the public. These bridges were the first opening bridges to which electricity was applied as a motive power in the kingdom.
Trade. — In the early days of the Navigation the trade was very small in comparison with what it is now. The earliest record is 1732, when the total traffic was about 14,525 tons of salt: and the amount gradually increased, until with the introduction of steam brine-pumps and deep mining, it rapidly advanced, and in 1881 it had reached the grand total of 1,466,917 tons of goods, salt, and merchandise carried down the river. Since then the tonnage of salt has declined, and although there has been a very large increase in chemicals and inland pottery, grain, and other goods, the total figure for 1908 only amounted to 1,058,700 tons.
Control of the River. — By the original Act of 1721, three gentlemen were appointed Undertakers to carry out the work of the Weaver Navigation, and eighty-six Commissioners, drawn from the leading families of the county and individually named, were appointed to settle any disputes between the Undertakers and the landowners and others interested. In 1754 the second Act was obtained, and this abolished the Undertakers and appointed 105 trustees instead of the commissioners, but drawn from the same source and with the same qualifications. These trustees, having complete powers and full control, were self-elective, and continued in office, with slight modification, until 1895, when they were relieved of their duties by Parliament, and a fresh arrangement made. The present Trust consists of thirty-eight members, partly representing the "old" trustees, partly the County Council of Cheshire, while fourteen are elected triennially by the tollpayers, and one from each town of Northwich and Winsford; as vacancies occur among the representatives of the " old " trustees, who are elected for life, the County Council has the power of appointment.
British Insulated and Helsby Cables
BRITISH INSULATED AND HELSBY CABLES. WORKS PRESCOT, HELSBY, AND LIVERPOOL.
British Insulated and Helsby Cables
The Prescot Works are situated on the London and North Western Railway, 8 miles from Liverpool, and occupy an area of 23 acres. Prescot is an old coaching town and is mentioned in the Doomsday Book. The works of the British Insulated and Helsby Cables, Limited (then The British Insulated Wire Co.), were erected in 1891, and were primarily engaged in the manufacture of paper- insulated lead-covered cables. Later, as electricity became more popular and of greater commercial importance, the works were enlarged and the variety of manufactures increased until to-day the works are the largest of their description in this country, the company being the only firm of cable manufacturers rolling and drawing their own copper wire. The Prescot works are devoted to the manufacture of paper-insulated cables for lighting, power, and telephones, high conductivity copper wire and strip, trolley wire, aluminium wire, strip and sheet, tramway fittings, electric welders, paper pinions, distribution and feeder pillars and boxes, meters, and numerous other items.
In 1902 The British Insulated Wire Co. amalgamated with the Telegraph Manufacturing Co., of Helsby and Liverpool. The Helsby Works manufacture india-rubber covered cables, insulating tapes, rubber and ebonite accessories, motor-car tyres, golf balls, and general telegraph and telephone overhead equipment. The Liverpool Works manufacture complete telegraph and telephone exchange equipments, switchboards, etc., and have carried out the complete installation of many large telephone exchanges for the Home and Colonial Governments, National Telephone Co. and private works.
PRESCOT WORKS.
The offices at Prescot face the railway. To the right of the entrance are the offices of the general manager, works manager, contract department, estimating department, and the board room. To the left are the chief engineer's, secretary's, and general offices. The whole of the offices and various parts of the works are connected by telephone through a private telephone exchange.
Wire Mill: Smelting - In this department are two furnaces capable of dealing with 100 tons of copper per week. The copper is cast into bars weighing from 140 to 360 lb., the larger sizes being used for drawing long lengths of trolley wire. It may be of interest to note that the bars are cast with a point at both ends. This is not only to facilitate easy entrance to the rolls, but to prevent a hollow forming in the end of the wire during the subsequent stages of rolling.
Rolling. — After being cast the bars are heated to a red heat and passed through a series of rolls which reduce the bars from 3 1/2 to 4 inches square down to 7/8 inch round for trolley wire and 1/4 inch ordinary wire. In this department copper is also rolled for manufacturing bus-bars and other copper fittings.
Pickling. — After being rolled the copper has a thick layer of black oxide, which is removed by pickling.
Drawing. — After annealing and pickling, the copper is ready for drawing. In the drawing mill there is plant suitable for drawing copper bars from 3 inches in diameter down to wire 1 mil in diameter; during the drawing the wire becomes Lard and has to be annealed. This is carried out in a Bates and Peard water-sealed annealing furnace, which has the great advantage of preserving the brightness of the wire. No difference can be detected in its appearance after it has passed through the furnace. The present plant in the wire mill is capable of drawing 200 tons of copper per week. A special shop has been started to cope with the demand for phosphor-bronze wires. In another portion of the wire mill is situated the tinning shop; in this department the copper wire is tinned before being manufactured into rubber cables, etc. Adjoining the wire mill is the aluminium shop, which is devoted to rolling aluminium sheet and rod, and is being rapidly enlarged, the present plant being for too small to meet the demand for this metal.
Mechanics' Department. — This department manufactures a good deal of the machinery required in the works, including hydraulic pumps used in connection with the lead presses. A specially interesting manufacture is the well-known "Prescot Paper Pinion," which is now rapidly replacing raw-hide. This department also manufactures the Bates and Peard furnaces for the annealing of nonferrous metals.
Stranding Room — The copper or aluminium wire, after being drawn to the required size, is taken to the stranding shop; here it is made up into strands of various sizes.
Insulating. — The strand is next passed through a covering machine; this machine has bobbins of paper ribbon revolving round the strand as it passes forward. Each of the paper ribbons forms one complete spiral layer of insulation, the number of layers depending upon the pressure at which the finished cable will have to work. Having been insulated the cable is taken to the drying ovens, of which there are six having a total capacity of 214 drums.
Oil-Tanks. — The insulated strand is then thoroughly impregnated with hot oil in a vacuum chamber, which ensures every layer of paper being properly treated; from the vacuous tank the cable is placed in one of the baths of hot oil, which are situated behind each lead press. The end of the cable is taken from the drum (which can revolve in the oil) and is passed through the lead press; the lead covering is squirted on at a comparatively low temperature by hydraulic pressure of 1 to 4 tons per square inch. Notice may hero be called to the paper pinions at work on the hydraulic pumps. In the lead-covering department is also manufactured extruded lead strip for window-glazing purposes. After being covered with lead the cable is taken to the testing department, where it is immersed, whilst still warns, in a water-tank. After remaining in the water-tanks for a minimum of twenty-four hours, the cable is pressure-tested to three or more times its working pressure; the insulation resistance, capacity, and conductivity are then measured. When the cable has passed all these tests, it is taken to the export department and battened up ready for dispatch.
Telephone Cable Department. — In this department are manufactured telephone and telegraph cables, of which a large amount is supplied annually to the General Post Office and National Telephone Co., besides many foreign customers. The paper used for insulating telephone and telegraph cables is not impregnated with oil, and in order to extract every trace of moisture from the paper, the insulated cables are heated electrically in special vacuum drying-ovens, of which there are at present five having a total capacity of 12 drums. The lead-covering process for these cables is similar to that for light and power cables described above.
Power-Station. — The power-station supplies current to the various motors and lights in the works. The total capacity of plant installed is 1,500 kw., the systems being 2,000 volts single phase and 500-volt continuous current. The company also supplies current to Prescot and the surrounding districts, for public and private lighting, and also to the Lancashire Light Railways Co.
Electrical Fittings Department. — This is a very important department of the works, manufacturing all descriptions of joint and distribution boxes, switches, feeder pillars, meters, welders, and tramway fittings. The department consists of a large machine shop, fitted with all the latest labour-saving machinery, test-room, stores, and a large brass foundry. Notable amongst the output of this department are the electric-welding machines for various purposes. Notice may also be called to the tramway fittings turned out, especially to the " non-fouling " type.
The number of men employed at the Prescot works is about 2,000.
Messrs Dick, Kerr and Co
MESSRS. DICK, KERR AND CO., PRESTON.
Dick, Kerr and Co
Works. — The site of the works comprises about twelve acres of land on the River Ribble, at Preston, a location admirably suited for serving both the home and foreign markets, being contiguous with two great railway systems and the Port of Liverpool. Transport facilities are thus available to ensure prompt delivery either in this country or abroad. The buildings are all one-storey structures, except the offices, of steel and brick construction, the former serving only to support the cranes and roof, and are abundantly lighted from the roof and sides. The lay-out permits extensions being conveniently carried out without entailing serious constructional modifications. The works are made up of a foundry building, containing the pattern-shop, iron and brass foundries, various shops for the construction of electrical machinery and apparatus, and a roomy power-house which furnishes electrical energy for operating the cranes and tools and for lighting the works.
Foundry. — This is 465 feet long by 120 feet wide, and is equipped with ties 30-ton cupolas and two 15-ton electric cranes. The frames of the largest generators built at the works are cast here, as well as the bed-plates, bearings, etc. All tools and machines, such as sand-sifters, cleaners, and chipping tools, are electrically driven. The cupolas are fed directly from the railway, and 600 tons of pig metal, with enough coke to reduce it, can be stored. An extensive pattern-shop, with large store adjoining, also form part of the foundry building, and modern wood-making tools, driven by electric motors, are everywhere in evidence.
Machine Shop. — The two main bays making up this shop are each 900 feet long by 60 feet wide, the dividing-line between them being a double row of lattice-work stanchions centrally supporting the roof and also carrying the main driving-shaft. This latter is one of the features of the works. To procure the most efficient method of driving, large motors of 50 h.p. each were decided upon. These were each built upon hollow shafts, through which the main shaft could pass to the next length, and fitted with clutches allowing of any motor being stopped independently of the others.
The work of preparing the raw materials previous to assembly proceeds from the north end of the machine shop, where the receiving and store department is. This forms the distributing centre for all the different departments, which are supplied with a minimum of delay by the overhead electric travelling-cranes. In its passage down the bays the raw material gradually assumes the finished shape, when it is ultimately handled in building up the complete machine. The machine shop is suitably apportioned into departments for dealing with the various component parts of dynamos, motors, controllers, and snitch-gear.
Of these the most interesting is the heavy machine-tool department, where field frames, armature spiders, large shafts, and commutators and stator carcasses are dealt with on more or less large lathes, boring mills, planers, slotting and drilling machines, etc. Among these heavy tools there is a 24-ft. boring mill, and a planer to take a casting of the same length, also a boring and milling machine with a 24-ft. table.
Numerous portable tools are also employed on large castings, which, for obvious reasons, can be less readily handled than the tools which were lightness itself in comparison. Both the generator and motor departments have their own testing beds, which are equipped with every known facility for ascertaining the characteristics of the different types of machines dealt with. In addition to the large machine shop, other bays are devoted to insulation, winding, etc.
Power-House. — This is a substantial building contiguous with the machine shop, though originally it was separate from it. The intervening space has, however, been roofed in, and now forms a shop for the winding and transformer departments. The power plant at present comprises two units each of 300 kw. capacity, driven direct by cross compound Corliss engines of 400 h.p. output, and one 750 kw. unit coupled to a 1,000 h.p. vertical engine. Energy is furnished on the d.c. system at 500 volts. A large battery is held in reserve. Alternating currents of high tension are obtained by motor generator sets, and transformers which give any desired voltage and periodicity.
Salt Union Works
SALT UNION WORKS, WINSFORD.
Salt Union Works, Winsford
On these works some 500,000 tons of different kinds of salt are produced annually. The supply of brine, however, is practically unlimited, and a great deal more could be made if required. By far the greater portion of the salt is still made in open pans varying from 30 feet long by 20 feet wide to 100 feet long by 28 feet to 30 feet wide, with a depth of 2 feet. Cheap slack is burnt in large furnaces immediately underneath the pan at the front, and the hot gases are conducted in flues underneath the pan, whence they pass in some cases direct to the chimney and in other cases through iron floes in a stove room fur drying the well-known handed squares before passing to the chimney. The crystals produced depend entirely on the way the pan is fired — the harder the firing the smaller the crystals and vice versa. Some of the large crystal pans do not boil at all but simmer at a temperature of about 170 F. These produce a curious crystal known as the hopper crystal, which floats about on the top of the brine in the shape of a hollow pyramid.
Various methods of producing special crystals are employed, locally known as " poisoning," and various ingredients are mixed with the brine. The salt is drawn daily or at longer intervals, as the ease may be, and either wheeled away in bulk, after having been left for some hours on the hurdles between the pans to dry, or ladled into wooden moulds, in which the squares seen on hawkers' carts are set. After having been a few hours in the mould they are knocked out and put in the stove to dry. This briefly is the only method of manufacturing salt, which has been in vogue in England and elsewhere until recent years, when the vacuum process was introduced in America, an example of which will be seen at Winsford. This is simply the ordinary multiple-effect evaporator (in this case triple) such as is used for the evaporation of sugar, with this difference, that whereas in sugar the juice is merely concentrated in the triple-effect evaporator, and then boiled to grain in a vacuum pan, salt is thrown out immediately evaporation begins in the multiple-effect evaporator; the brine enters completely saturated with salt, as pumped from the shafts and contains some 26 per cent. of salt. This plant, which will be seen at the works, produces about 80,000 tons a year, most of which goes to Calcutta.
At Northwich the Marston Salt Mine will be visited; the workings are about 300 feet below the ground-level and are of considerable extent. They are in a solid bed of rock salt, which is worked out by compressed-air rock-cutters and hand-labour, large square pillars being left at suitable intervals to support the roof. The salt as worked is of a reddish colour, but occasionally small pure white pockets of salt crystals are encountered.
See Also
Sources of Information
- ↑ Some of the particulars for this Notice were extracted from Mr. J. S Brown's Paper in the Post Office Electrical Engineers' Journal, April 1909, and are published by courtesy of the Board of Editors of that Journal.
- ↑ Mr. Anthony G. Lyster, Engineer-in-Chief, made, at the Dinner on 27th July 1909, an interesting statement as to the history and progress of the Harbour and-Docks (see page 806).
- ↑ * "Duker " is the local name of vessels using the Duke of Bridgewater Canal; they carry about 40 tons.